The Top Topology Optimization Software Solutions for 3D Printing
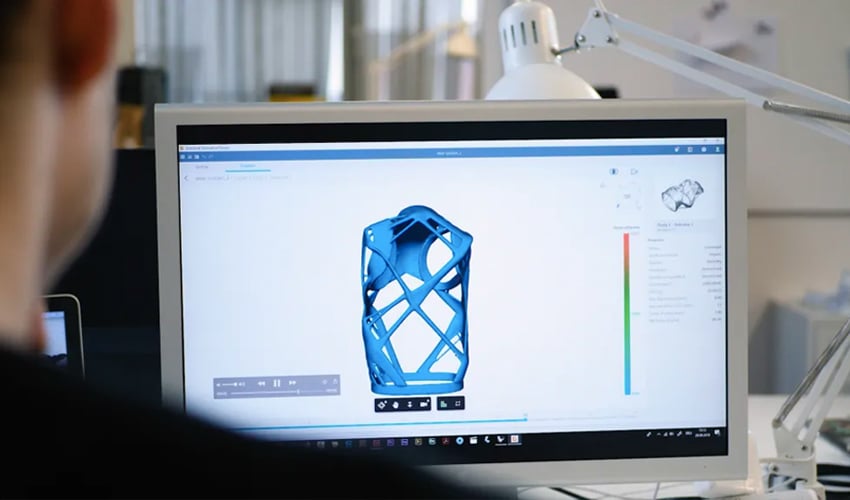
Topology optimization is a process that aims to achieve reduce a part to its most minimal possible geometry. To do this, an initial concept of a part is optimized using computer-based calculations so that less material is required for its production without any loss of performance. The material savings also lead to lower costs. The advantages of topology optimization can be felt in numerous industries, which is in turn increasing the demand for specialized software. According to a report by Market Research Intellect, the market for structural topology optimization software is expected to reach USD 21.02 billion by 2031, growing at an annual CAGR of 11.09% between 2024 and 2031. Given this trend, it is clear that more and more topology optimization solutions are being developed. But what is the current status quo? Let’s take a look at topology optimization software solutions that are suitable for additive manufacturing.
3DXpert
3DXpert is an all-in-one software originally owned by 3D Systems, and which passed under the Oqton brand in 2022. 3D Systems purchased Oqton in 2021 and it is now an independent software subsidiary. 3DXpert is a comprehensive, integrated additive manufacturing 3D software that optimizes the entire workflow from design to printing. The software is designed to avoid costly errors by unifying all AM processes in one software environment, including DfAM, print preparation, simulation, and inspection. In addition, 3DXpert provides a dedicated set of design tools needed for lightweight, texturing and printability changes. These include: topology optimization, meshing, texturing, implicit modeling, and others. The software is ideal for industrial projects in a variety of industries and is particularly known for bringing automation and speed to processes.
Ameba Topology Optimization Software From XIE Technologies
Ameba, the software from XIE Technologies, was created as an advanced topology optimization tool that is easy and intuitive to use. Based on Bi-directional Evolutionary Structural Optimization (BESO) technology developed by Prof. Yi-Min (Mike) Xie, Ameba integrates Rhino-Grasshopper for modeling and post-processing of models. With Ameba, finite models can be analyzed in a very short time and their topology can be optimized using cloud computing. The software also has numerous computational libraries and open-source files with which data can be manipulated in both preprocessing and post-processing. Finally, Ameba has a high extension capability and easily integrates with external software, making it a versatile tool for advanced design.
Altair Engineering and its Range of Software for Topology Optimization
Altair Engineering is a company dedicated to the development of software and cloud solutions. Its software offerings include several 3D modeling solutions, some specifically designed for additive manufacturing. Altair® HyperWorks®, for example, is a complete design and simulation platform that integrates topology optimization through an analysis of the structural integrity of designs, durability, dynamics, weight, strength and material efficiency. Within this platform there are specific topology optimization tools such as OptiStruct. This offers various structural optimization methods and a whole range of functions useful in traditional manufacturing processes, with composite materials and additive manufacturing. Moreover, the company has developed Altair Inspire, a suite of programs that accelerate simulation-based design. One tool that stands out is Altair® Inspire™ Print3D, which offers specific functions to reduce the use of materials in specific processes such as Powder Bed Fusion and Binder Jetting. In addition, there are tools for mold manufacturing, metal and polymer extrusion, among others.
Ansys Additive Suite
Ansys Additive Suite is a comprehensive and powerful solution dedicated to metal additive manufacturing, helping to avoid manufacturing failures all while ensuring that the resultant parts conform to design specifications. It provides designers, engineers and analysts with essential information covering the entire workflow, from topology optimization to design validation. Its advanced features include STL file manipulation, structural and thermal analysis, and simulation of additive processes, including powder laser melting (DMLS), DED and metal sintering. In addition, Ansys Discovery, the first simulation-based design tool to combine instant physical simulation and advanced modeling, remains available to support additive manufacturing projects.
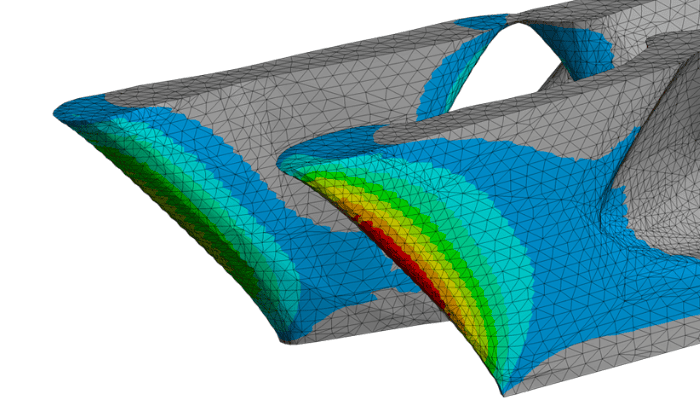
Photo Credits: Ansys
Cognitive Design
The Cognitive Design software was developed by the French company Cognitive Design Systems. It offers a wide range of functionalities and aims to optimize designs, whatever their complexity. Relying on a simulation-based approach, CAD designers can identify the best strategies for reducing the weight of their 3D models and creating novel shapes. The software can, for example, integrate ribs, lattice structures or play with fillings. Users can implement these geometric optimizations semi-automatically, offering greater flexibility and reduced design times. In addition, Cognitive Design can generate models for 3D printing, and identify any manufacturing faults at this stage. It will alert you, for example, to the thickness of the walls, the positioning of the part on the tray, and so on. In short, it’s a solution that goes beyond topology optimization to help streamline the production process.
COMSOL Multiphysics®
COMSOL Multiphysics® is a comprehensive software for topology optimization, used to improve the designs of 3D printed parts. This software uses advanced numerical methods and offers tools for both multiphysics and single-physics modeling, which are fully integrated with each other. It also allows the entire workflow to be managed efficiently and easily with its intuitive interface. The integration of the COMSOL Multiphysics® add-on, called The Optimization Module, also provides additional tools for both parameter estimation and optimization by shape and topology. Some practical examples of The Optimization Module capabilities are available on the website. These include showing the topological optimization of a hook for better material and weight distribution and the design of a coil to maximize magnetic flux density. Finally, the software offers two different user interfaces for shape and parameter optimization.
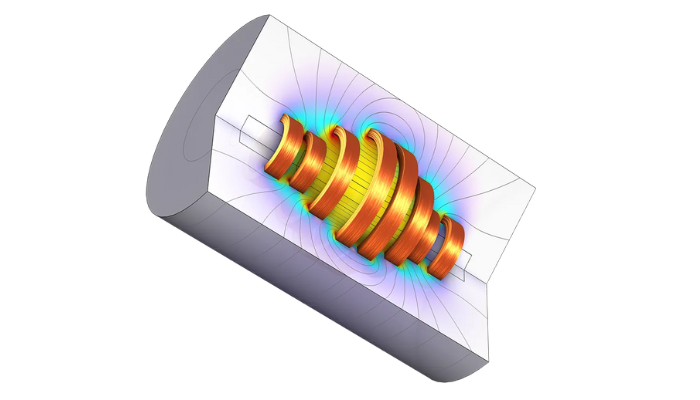
A coil model optimized to obtain a uniform magnetic field on an axis (photo credits: COSMOL Multiphysics®)
Netfabb
Acquired by Autodesk in 2015, Netfabb is a software solution aimed at preparing the production process. Among its main features you can find the conversion and importation of models coming from different CAD applications, the maximization in the number of parts capable of being printed and, as expected, design optimization for additive manufacturing. Because of the great design freedom offered by this technology, Netfabb had to integrate topology optimization into its software solution. In addition to preparing for the printing process, the program allows the reduction of failures during the printing process by predicting how parts might be affected. Netfabb is available in 4 different versions: Standard, Premium, ultimate and Simulation, so its price will vary depending on the version chosen.
nTop Software
Based in New York, nTop is a company dedicated to developing topological optimization solutions for solving complex engineering problems in additive manufacturing. Its nTop software provides access to a suite of features to transform the way product development is designed, refined and scaled. In addition to the base option, the company offers two variants to expand modeling capabilities. nTop Automate, for example, allows you to run design workflows at scale, all in a programmatic environment. For its part, nTop Core allows connecting applications with implicit files, avoiding conversions to B-rep or STL meshes. This results in a seamless process that yields higher fidelity designs and better performing parts. It is undoubtedly a cost-effective option for the demanding 3D industry, which is constantly looking to lighten parts while reducing production costs.
OpenPisco
OpenPicso is a modular open-source topology optimization software whose structural design process supports grids, unstructured meshes and body-adapted meshes. In addition, the software offers a user-friendly GUI, a command line application and a Python library. The focus is on modularity, extensibility and interoperability. Furthermore, the user can integrate routines such as optimization algorithms or network processing without changing the source code. The topology optimization method is based on an implicit modeling engine. OpenPisco is currently being developed by IRT SystemX and Safran Tech, the Safran Research & Technology Center.
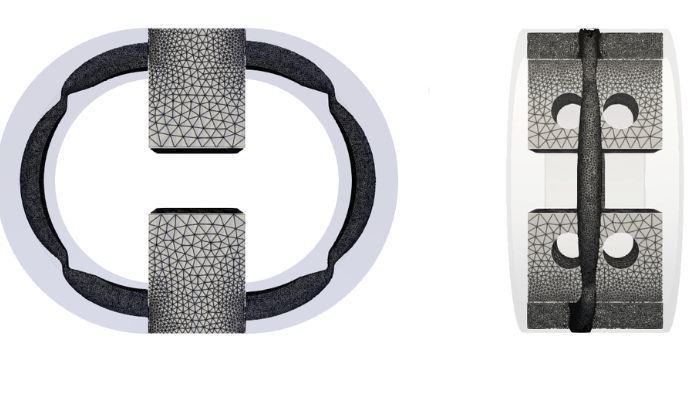
Photo Credits: OpenPisco
Siemens NX
Siemens has developed an integrated software solution called NX. It allows any user to benefit from all the advantages of additive manufacturing by simplifying the modeling steps. In concrete terms, its tool will allow users to design for 3D printing, prepare their part, visualize it, multiply iterations, etc. Among the functionalities offered, topology optimization is obviously part of what Siemens calls Convergent Modeling. It has developed a solution to allow traditional geometry to converge with mesh models in the same model. The user no longer needs to go through another file format and export it if he wants to optimize his part: everything is done on the same platform. NX is not a topology optimization software per se: it is an all-in-one solution that offers this function for additive manufacturing.
TopOpt, Topology Optimization Software for Grasshopper
TopOpt is a tool integrated into Grasshopper, Rhinoceros 3D’s visual programming environment, designed to explore new topological optimization methods in the fields of architecture and structural engineering. Currently in its alpha phase, TopOpt offers a variety of optimization strategies, including a 2D approach derived from an interactive mobile application, a method focusing on continuous structures optimized for tension and compression, and a bi-material model for composite structures. Future software development will incorporate advanced features such as 3D optimization and further interactive visualization. Compatible with Grasshopper for Rhino 4 and 5, TopOpt represents a major step forward for designers wishing to integrate high-performance optimization solutions into their projects.
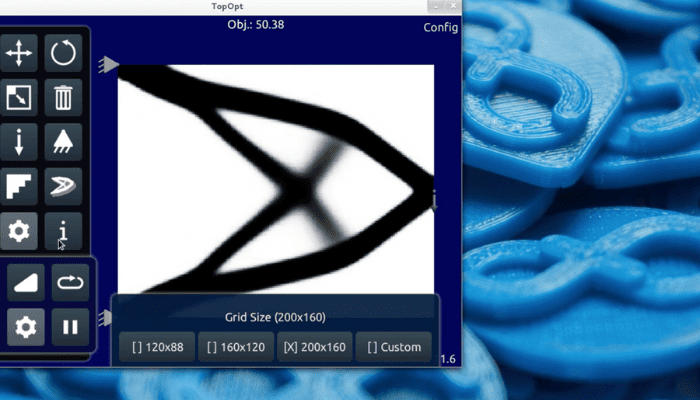
Photo Credits: TopOpt
Tosca
Tosca is an optimization suite from Dassault Systèmes. It is a powerful structural and flow optimization solution based on FEA and CFD simulations. The company offers two product solutions in this regard: Tosca Structure and Tosca Fluid. Tosca Structure can be used for optimization in the design of lightweight, rigid and durable parts. Thanks to topology optimization, the development process as well as time-to-market can be reduced. This is an advantage that automotive manufacturers, among others, know how to use. The current version of Tosca comes with Python 3.7.1 and has been improved to include automatic creation of stop conditions. The second product, Tosca Fluid, is used for design and non-parametric fluid flow topology for components and systems.
Topology Optimization Software in Z88
In 1985, Prof. Dr.-Ing. Frank Rieg developed the first version of the finite element software Z88 in FORTRAN at the University of Bayreuth. Today, the further development includes several variants, including Z88OS as an open-source calculation kernel for the basic understanding of FEA, the user-friendly GUI version Z88Aurora®, which also processes CAD data, and Z88Arion® for topology optimization. In addition, the mobile apps Z88Tina and Z88Mobile enable quick visualization of simulation results. The entire Z88 family remains free of charge and is primarily used for engineering education at universities and technical colleges. The Z88Arion® offers a user-friendly interface with powerful calculation cores and is divided into the preprocessor, solver and postprocessor areas to enable quick familiarization and efficient calculations.
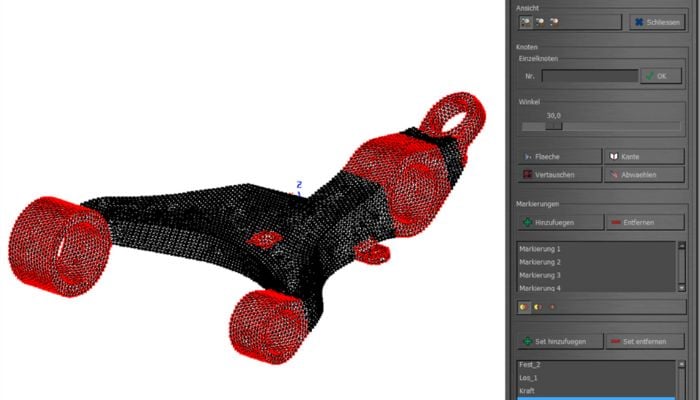
Z88Arion® picking and set management (photo credits: Z88)
What do you think of our list of topology optimization software solutions? Did we miss any? Let us know in a comment below or on our Facebook and Twitter pages. Don’t forget to sign up for our free weekly newsletter, with all the latest news in 3D printing delivered straight to your inbox!
and TOffeeAM, http://www.toffeeam.co.uk 🙂
https://www.youtube.com/watch?v=BWUIEE0yMwI
CATIA on 3DEXPERIENCE also has topology optimization and CAD reconstruction tools.
Fusion 360 with its generative design. It appears your first screen shot is Fusion 360 but only Netfabb is included in your list. GD in Fusion supports manufacturing methods such as additive, costing, buckling, modal analysis and so on. I think with its ability there, in the SubD manipulation and the inclusion of Additive MFG support in the manufacturing workspace it seems to fit in this category.