What Are the Applications for 3D Printing in Space?
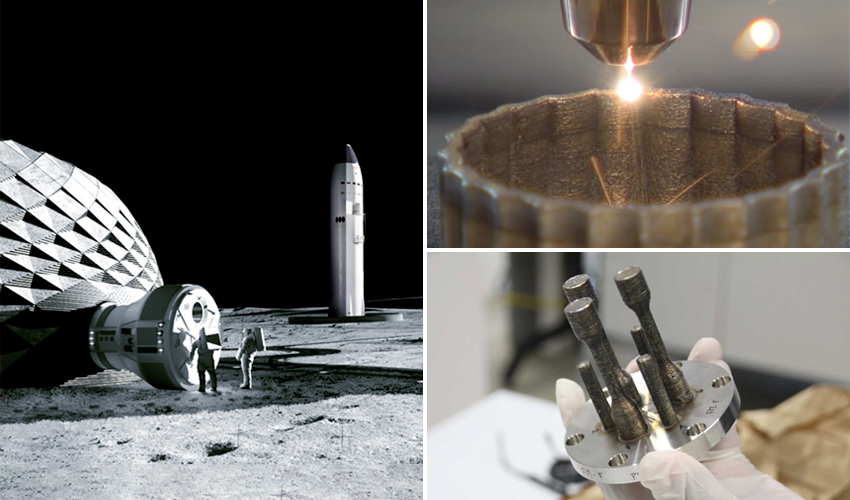
Space is the final frontier of human exploration and additive manufacturing is playing a key role in that expansion. From producing rocket components to printing parts in zero gravity, 3D printing is being chosen in aerospace for its ability to reduce costs, optimize designs and enable manufacturing in extreme environments. Space companies and agencies such as NASA and ESA have already incorporated 3D printed parts into their missions and even futuristic applications are being explored, such as printing food and biological tissues for long-duration missions.
One of the areas where 3D printing has had the greatest impact is rocket development. In these developments, additive manufacturing has been able to shine as it allows for optimizing the performance of even these demanding components. Since we have already devoted an entire article to rockets and spacecraft, let’s take a look at some of the other fascinating applications of 3D printing in space.
In-Space Manufacturing
3D Printing in Zero Gravity: The First Step Towards Space Factories
Efficient 3D printing in space is currently one of the biggest goals of space organizations, as it would enable numerous applications on-site. However, the conditions in space are fundamentally different from those on Earth, with microgravity and vacuum in particular causing difficulties for conventional 3D printers. So, researchers at the University of Glasgow have developed a solution to advance 3D printing in zero gravity. Dr. Gilles Bailet from the University of Glasgow has been working for years on a prototype 3D printer for space that prints devices directly in orbit, such as reflectors, communication antennas or medicine. The printer processes granular material and prints efficiently even under the prevailing conditions. Bailet sees this as the solution to pave the way for space factories. The printer was extensively tested in several test flights in November 2024.
First 3D-Printed Metal Part Aboard The ISS
In early 2024, a metal 3D printer was sent into space to test in-orbit manufacturing. The printer in question was designed by Airbus in collaboration with the European Space Agency (ESA) and was sent to the International Space Station (ISS) aboard the Cygnus NG-20 resupply mission. After months of calibration, they succeeded in 3D printing the first metal part in orbit, marking a milestone in space manufacturing. This was done using the direct energy deposition (DED) process, where a high-power laser melts stainless steel wire at temperatures up to 1,200°C. The result was a 9 x 5 cm array of metal components. This achievement demonstrates the potential of 3D printing to manufacture tools and structures in space, opening the door to on-demand production and optimizing resources in space exploration.
NASA Tests Laser Beam Welding in Space
Laser beam welding, a type of directed energy deposition, is often used for repairs or making parts from scratch. In space, the technology could help build large habitats in low Earth orbit, spacecraft structures for astronaut safety and more. In the fall of 2024, NASA released details of their two-year-long research project on the viability of laser beam welding in space–and announced that their mission was a success. The project was the result of a collaboration between NASA’s Marshall Space Flight Center and Ohio State University. Together, they sought to understand the physical processes of welding on the lunar surface. The team investigated the effects of laser beam welding in a combined vacuum and reduced gravity environment. During test flights, they successfully welded 69 out of 70 welds, collecting data with a network of sensors during the tests. By understanding how laser beam welding could work in such an environment, they hope to increase manufacturing capabilities in space.
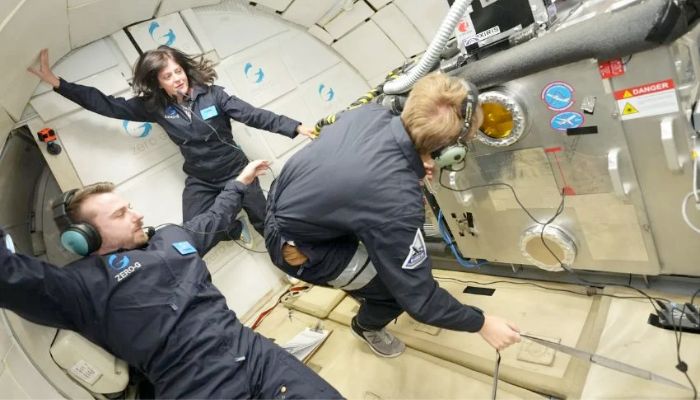
The team monitors laser beam welding in a vacuum chamber during a Boeing 727 parabolic flight. From left, Andrew O’Connor, Marshall materials scientist and NASA technical lead for the project; Louise Littles, Marshall materials scientist; and Aaron Brimmer, OSU graduate student. Photo Credits: Tasha Dixon
Berkeley Researchers Send a 3D Printer Into Space
On June 8, 2024, researchers at the University of California, Berkeley, sent their microgravity 3D printer into space for the first time as part of the Virgin Galactic 07 mission. The SpaceCAL printer spent 140 seconds in suborbital space aboard the VSS Unity spacecraft. In that short time, it independently printed and post-processed a total of four test parts, including space shuttles and figurines, with PEGDA liquid plastic.
While the printer still needs to be fine-tuned, it performed well in microgravity conditions and allowed them to validate the readiness of this 3D printing technology for space travel, according to the researchers. With NASA’s support, Berkeley researchers will continue to test the technology to provide it to astronauts as a means of parts production during longer missions in space.
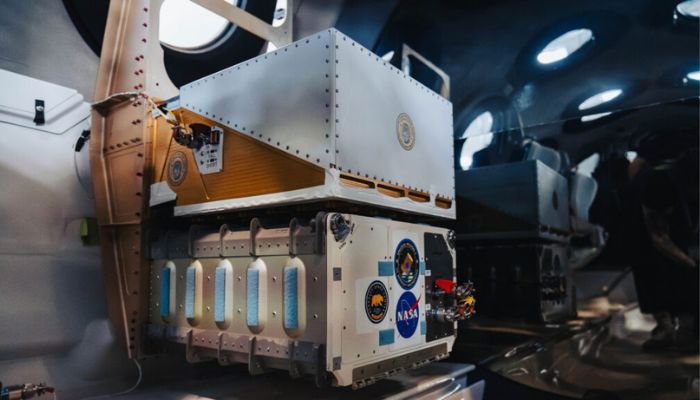
The SpaceCAL 3D printer on board the VSS Unity. (Credit: Virgin Galactic)
European Space Agency (ESA) Uses IMPERIAL 3D Printer
The European Space Agency (ESA) has decided to use the IMPERIAL 3D printer for its space exploration. The solution was developed by OHB System AG, Azimut Space, Athlone Institute of Technology and BEEVERYCREATIVE to create parts larger than the available volume. Thus, thanks to the IMPERIAL 3D printer, structures, tools and spare parts that are essential for the success of extended space missions can be created. The features of this printer are very interesting. First, it is capable of printing in microgravity conditions, that is, in near-zero gravity. A capability that normal printers do not have. It is also equipped with a conveyor-belt-shaped printing plate that, by serving a single axis, enables continuous production and is suitable for creating structures with large volumes. Finally, it can also print nearly zero-gravity high-performance materials such as PEEK, PEKK and PEI due to the presence of a thermoregulated environment that prevents their deformation. The prototype was successfully created on Earth, and the next step will be experimentation in the microgravity environment of the International Space Station (ISS) or ESA’s Space Rider.
3D Printing Electronic Circuits for Spacecraft
A team of NASA engineers successfully tested 3D printed electronic circuits on a suborbital flight from Wallops Flight Facility. The technology allowed sensors to be printed directly onto the internal and external surfaces of spacecraft, optimizing space and functionality. During the experiment, temperature and humidity sensors printed on the cargo door and panels of the SubTEC-9 rocket collected data transmitted to Earth. This innovation facilitates the integration of components in previously unusable areas and improves the accuracy of antennas by printing them on curved surfaces. In addition, they developed circuits with ultra-thin traces, reducing reliance on traditional methods such as metallic wiring. This technology could be applied in future missions to monitor temperatures inside spacecraft or complement AI-designed structures fabricated in orbit.
Supporting Human Life
Redwire’s BioFabrication Facility
Redwire Corporation is an American aerospace manufacturer whose aim is to accelerate the conquest of space by developing solutions that make life in space easier. One way of achieving this goal is through the use of bioprinting in space. Indeed, the company has been working for some time on the creation of printed fabrics in a microgravity environment. At the end of 2023, the company announced that it had successfully 3D printed the first knee meniscus in space, on board the International Space Station. John Vellinger, Executive Vice President of Redwire, adds: “This is a groundbreaking milestone with significant implications for human health. Demonstrating the ability to successfully print complex tissue such as this meniscus is a major leap forward toward the development of a repeatable microgravity manufacturing process for reliable bioprinting at scale.” In any case, it’s a development that shows how additive manufacturing can impact human health in space and make it much more accessible.
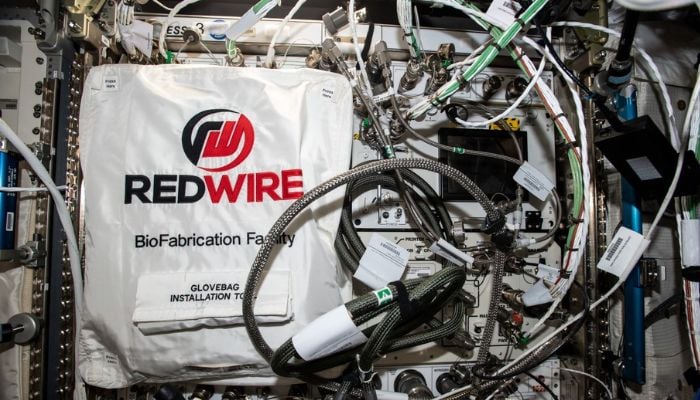
The 3D bio-printer installed on board the ISS (photo credits: Redwire Corporation)
Bioprint FirstAid Helps for Wound Care in Space
The Bioprint FirstAid experiment is another notable example of how bioprinting could be used in Space. In 2022, ESA astronaut Matthias Maurer tested the device, which is hand-operated and is described as a “plaster/bandaid gun,” while on the International Space Station. Bioprint FirstAid works by producing a plaster/band-aid-like covering for skin wounds using bio-ink. When used by Maurer, the ink was made of fluorescent microparticles rather than skin cells, with the goal being that ultimately it would be used to provide personalized wound care for astronauts on the ISS. In 2024, a research paper showed that some success had been had with human skin cells that proliferate in biogels after printing. Apparently, the bioprinter was found to have a low susceptibility to failure, a robust design, no electronics and maintenance-free mechanics. Perfect for future human exploratory missions to the Moon or even Mars!
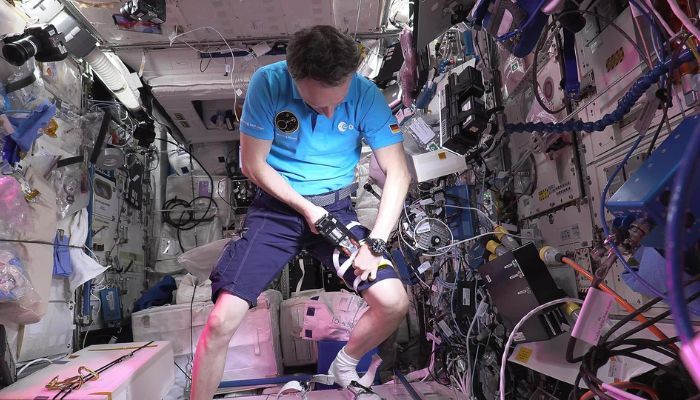
Astronaut Matthias Maurer testing the Bioprint FirstAid experiment (photo credits: ESA/NASA)
Professor Pablo de León Patents 3D Printed Space Suits
Pablo de León, chairman of the Department of Space Studies at the University of North Dakota (UND), has patented an innovative 3D printing technology. This allows astronauts to produce entire spacesuits and independently create replacement parts during long-duration space missions, intending to be ready for future trips to Mars. Professor Pablo de León’s technology would bring numerous benefits to space missions. First, the production of spacesuit components and other essential items could take place on-site in space, limiting dependence on hypothetical supplies from Earth. In addition, the design of space suits or gloves and boots can be customized for each astronaut through data collected from scans of their bodies. Both rigid and flexible filaments can be used with this technology, making it possible to make both rigid components, intended for areas such as the torso, and softer parts, ideal for joints.
The technology also lends itself to the production of other objects, such as pressurized fluid tanks. The filaments used to produce the suits can also be made from elements found in Martian soil or extraterrestrial atmospheric gases, allowing local resources to be exploited in the case of extended planetary missions. The technology thus could be used for NASA’s Artemis program, which consists of a series of missions aimed at returning astronauts to the Moon, with the goal of advancing them to Mars.
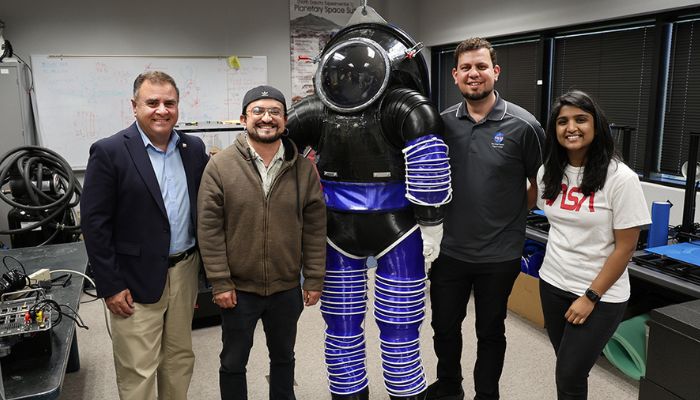
Next to the prototype 3D printed spacesuit, Pablo de León (left) poses with doctoral students David Mateus Jimenez, Jurie Visagie and Pranika Gupta. (Photo credit: Joe Banish/UND Today)
3D Printed Astronaut Meals from Plastic Waste
You have seen 3D printed food—but have you ever heard of 3D printed food made from plastic? To produce food in space, American, Japanese and European space organizations have collaborated with the food industry to find a solution: collecting plastic waste and turning it into edible food. It sounds miraculous, but the company Beehex has made it possible. First, they collect plastic waste, shred it and put it into a bioreactor with a specific modified bacteria. Then, the bacteria eats the plastic and turns it into a biomass that can be 3D printed to form meals. Beehex was founded by Anjan Contractor, an engineer affiliated with NASA, and part of the project’s goals was to feed astronauts. With 3D printed, they have created steaks, chicken and more.
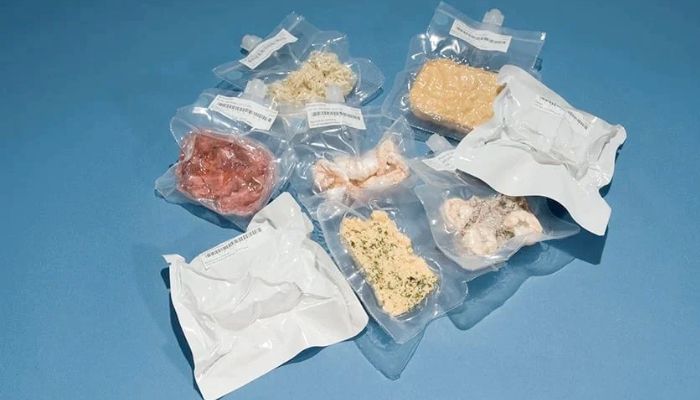
Photo credit: NASA
Space Construction
ICON and NASA Boost 3D Construction on the Moon and Mars
NASA has awarded a $57.2 million contract to Austin-based ICON to develop construction technologies for future missions to the Moon and Mars. As part of the Moon to Mars Planetary Autonomous Construction Technologies (MMPACT) project, ICON will work with NASA’s Marshall Space Flight Center to develop the Olympus construction system. This project aims to use local materials in the fabrication of infrastructure such as landing pads, habitats and roads on the lunar surface. This contract, which runs through 2028, expands on ICON’s previous work under the Small Business Innovation Research (SBIR) program and builds on its expertise in 3D printing applied to space exploration, including the construction of Mars Dune Alpha, a simulated Martian habitat for the CHAPEA analog mission. With these innovations, NASA seeks to advance technologies essential to the sustainable exploration of new sites.
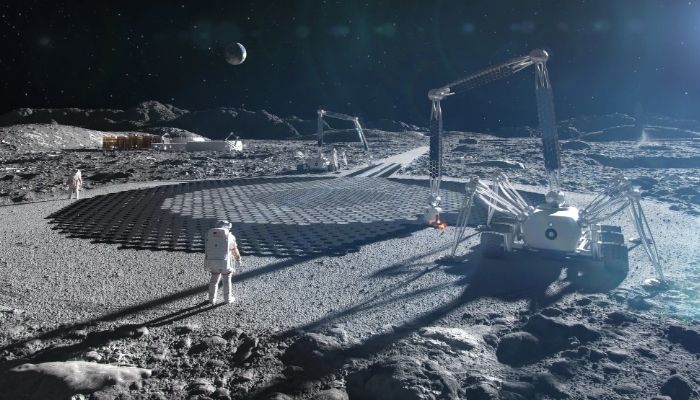
Photo credit: ICON/BIG-Bjarke Ingels Group
Space Copy Shoots to Have a 3D Printer on the Moon
Space Copy is one of several companies with the mission of 3D printing on the Moon, Mars and beyond! The company’s general aim is to develop solutions to practical problems faced when producing infrastructure in extreme environments on Earth and in space where standardized and traditional manufacturing is costly and high-risk. The startup, launched in 2022, wants to deploy autonomous printing solutions for remote construction, as well as integrate custom additive manufacturing techniques for on-demand fabrication of supplies and infrastructure. Furthermore, the company is developing printers to print lunar soil simulant material. Founder Madison Feehan said her goal was to have a printer on the Moon by 2031.
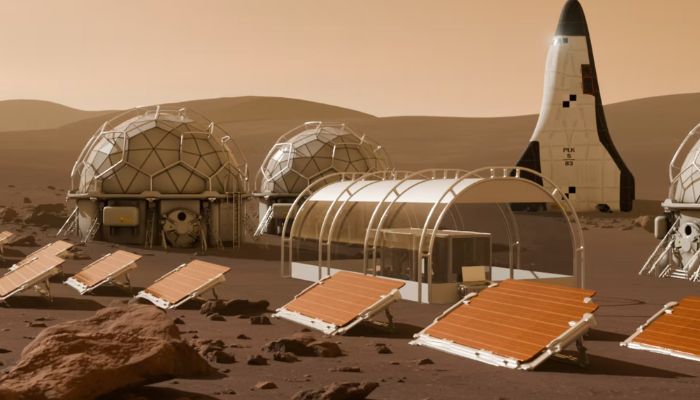
Photo credit: Space Copy
What do you think of these 3D printing applications in space? Let us know in a comment below or on our Facebook and Twitter pages! Don’t forget to sign up for our free weekly Newsletter, with all the latest news in 3D printing delivered straight to your inbox!
I am trying to cite the author for: What are the applications for 3D printing in space? But I can’t find the author. Could you send me the authors full name and credentials.