Titanium vs Aluminum: Which Metal Should You Choose for 3D Printing?
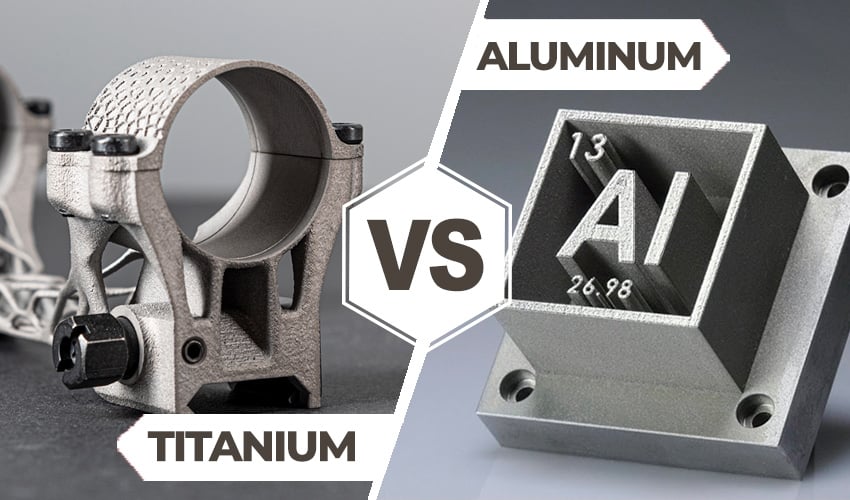
Metal is currently one of the most sought-after materials in additive manufacturing processes. Not surprisingly, its excellent properties make it the ideal choice for the most demanding applications in terms of performance and strength. In this article, we will focus on two of the main metals used in 3D printing: titanium and aluminum. These are mainly used for processes such as laser powder bed fusion (L-PBF) or directed energy deposition (DED). They are mainly available for 3D printers in powder form, especially in industrial environments. We will compare their similarities and differences, in order to better understand their properties and applications, and the advantages they offer in this manufacturing process.
Production and Characteristics of Titanium vs Aluminum
Titanium
Titanium is a material that does not occur in nature as an element and must instead be extracted from minerals such as rutile (TiO2) or ilmenite (FeTiO3). The extraction of pure titanium is a complex process that involves several steps. The most widely used method for the production of pure titanium is the Kroll method, developed by the American chemist William J. Kroll in 1940. This method involves the reduction of titanium dioxide (TiO2) with chlorine gas (Cl2) to produce titanium tetrachloride (TiCl4), which is then reduced with magnesium (Mg). Although the Kroll method is effective in producing pure titanium, it is an expensive process that requires a large amount of energy. In addition, the high reactivity of titanium makes it difficult to obtain as a pure metal, so much so that a sample with a purity of 99.9% is considered commercially pure titanium. Therefore, it is normally used in combination with other elements to form an alloy.
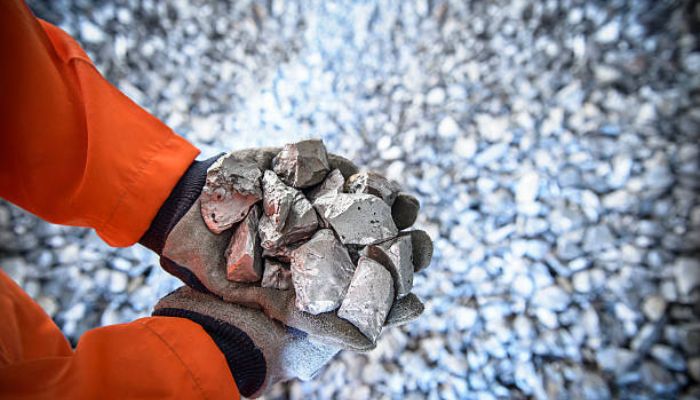
Photo Credits : Getty Images
Titanium has many properties that make it very versatile and useful in a number of sectors. As previously explained, it is often used in alloy form, but pure extracted titanium is used in certain applications, such as in the medical industry, due to its high biocompatibility. Its main characteristics are high mechanical strength, low density, excellent corrosion resistance and high rigidity.
The main titanium alloys used in 3D printing are the following:
- Titanium 6Al-4V, grade 5: The most important and most common of the titanium alloys. It is used in additive manufacturing because of its high strength and durability. The alloy is composed of titanium, aluminum and vanadium and can withstand high temperatures and corrosive environments.
- Titanium 6Al-4V, grade 23: Commonly used in medical implants and prostheses thanks to its biocompatibility.
- Titanium Beta 21S: Stronger than conventional titanium alloys, it is also more resistant to oxidation and deformation. It is perfect for orthopedic implants and aerospace engine applications. Beta titanium is prized in orthodontics.
- Cp-Ti (pure titanium), grade 1, 2: This alloy is used in the medical industry for a wide range of applications due to the biocompatibility of titanium with the human body.
- TA15: An alloy made almost entirely of titanium, to which aluminum and zirconium have been added. Components made from this alloy are very strong and resistant to high temperatures, making them ideal for building solid parts in aircraft and engines. They are also very light in relation to their strength.
Aluminum
Aluminum is a metal that offers an excellent compromise between lightness and strength. In addition to being corrosion resistant, it can be welded. It is quite rare to find it in its pure state, so it is used in the form of an alloy, with metals that improve its physical and mechanical properties, such as silicon and magnesium. As for titanium, two consecutive industrial processes make it possible to obtain the material in its pure state. In the first process, called the Bayer process, aluminium oxide is obtained from bauxite ore. The ore is washed and crushed, dissolved in caustic soda and filtered to obtain pure aluminum hydroxide. It is then heated to obtain aluminum oxide powder. In the second process, called the Hall-Heroult process, the electrolytic reduction of aluminum oxide is performed to obtain pure aluminum. Most of the processing plants are built near the mines in order to reduce the cost of transporting the ore.
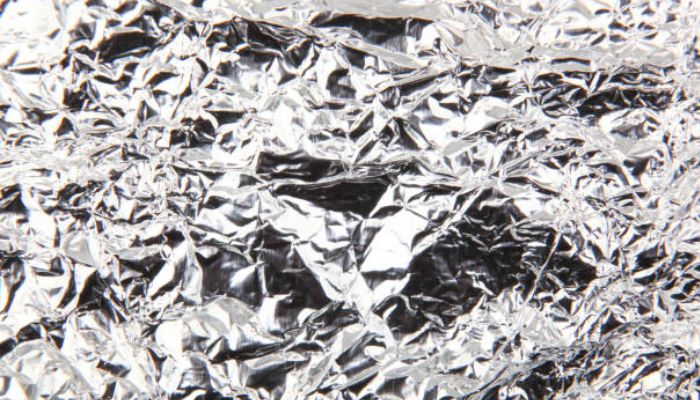
Photo Credits: Getty Images
As mentioned above, aluminum alloys are more common than the pure form and are used in many industrial applications. In addition, they have a very good strength-to-weight ratio and very good fatigue and corrosion resistance. They are also recyclable, thermally and electrically conductive, and have low toxicity.
The main alloys used in aluminum 3D printing are the following:
- AISi10Mg: This is the most common alloy formed by silicon and magnesium. It can be used to manufacture solid and complex parts and is used to create various objects such as housings, engine parts and production tools.
- Al2139: The strongest aluminum alloy, ideal for industries such as automotive due to its light weight, strength and chemical resistance. It has been used by organizations such as the U.S. Air Force, Mercedes-Benz and Airbus. The beauty of this material is that it was specifically designed for additive manufacturing and outperforms many other alloys on the market.
- Al 7000 series: This is a well-known series of powder alloys, with high tensile strength and low temperature resistance.
- Al 6061 & Al 7075: Recently, 3D manufacturers have had very good results using these two alloys. 6061 has lower tensile strength and hardness than 7075. On the other hand, 7075 has better impact resistance and less deformation than 6061 aluminum.
- A201.1: It is part of the 200 series of copper-aluminum alloys, known to be very strong. However, they are difficult to cast. These alloys are recommended for applications where strength to weight ratio is crucial, such as in transportation and aerospace.
What Are the Differences Between the Two?
In terms of strength-to-weight ratio, titanium is the ideal choice when high strength and robustness are required, which is why it is used for medical components or even in satellite components. On the other hand, although aluminum is less strong than titanium, it is much lighter and more affordable. In terms of thermal properties, aluminum is perfect for applications that require high thermal conductivity. Titanium, on the other hand, is ideal for applications in high-temperature environments due to its high melting point, such as aerospace engine components. Both aluminum and titanium have excellent corrosion resistance. However, titanium is more biocompatible than aluminum, which is why it is widely used in the medical sector.
Material Form and Compatibility With 3D Printing Technologies
Form
In most cases, titanium and aluminum come in powder form, although they can also be available in wire form, such as the titanium or aluminum filament offered by Virtual Foundry or Nanoe. To 3D print parts with these metals, the alloy powder must first be obtained, which is done using two main techniques: plasma atomization or gas atomization. Plasma (ionized gas) atomization is a process that uses high temperatures, an energy and heat source, an inert medium such as argon, and high velocities to atomize the metal. This process produces high quality, wear-resistant powders. Gas atomization, on the other hand, uses air, argon or helium as the gas to fragment a stream of molten material. This is a very efficient process, widely used to produce fine, spherical metal powders. The technique used to manufacture the metal powder is important, as it obviously influences the final properties of the part.
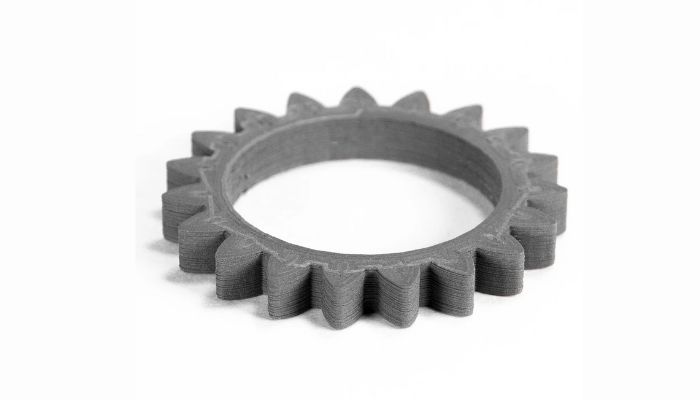
Unsintered 64-5 titanium gear (photo credits: SAPPHIRE3D)
3D Technologies Used
To work with titanium in 3D printing, a large number of processes can be used, including laser powder bed fusion (L-PBF), DED and binder jetting. For processes related to aluminum, there is another one in addition to those already mentioned, Cold Spray.
In L-PBF, the laser beam is used to heat the powdered metal layer by layer to its melting point and build the object. Titanium melts at very high temperatures (1,600°C), so the thermal and mechanical effects of the material will need to be analyzed before 3D printing. The melting temperature of aluminum is much lower (about 630°C), but aluminum has high reflectivity and thermal conductivity. Another interesting aspect of additive manufacturing with aluminum is that it forms a natural oxide layer, which other metals do later on their edges, which means that the presence of this thin layer on aluminum slows down the process.
In regards to DED, it is a very similar process to the previous one, but here the material is melted as it is deposited by the nozzle and can be in powder or wire form for manufacturing. Normally, this technology results in a higher production speed and lower cost per unit volume.
In the case of Binder Jetting, the material is in the form of a powder that is not melted, but rather, in order for the particles to adhere to each other, a binder is sprayed onto the layer at specific locations using a multi jet print head. A sintering step or other solidifying post-processing is also required after printing. When they leave the 3D printer, the parts are very fragile and porous and will need to be heat treated to achieve their final mechanical properties.
In Cold Spray processes, the metal material is also found in powder form, but since in this case it does not have to be melted or fused, cold spraying avoids heat distortion and a protective atmosphere is not required.
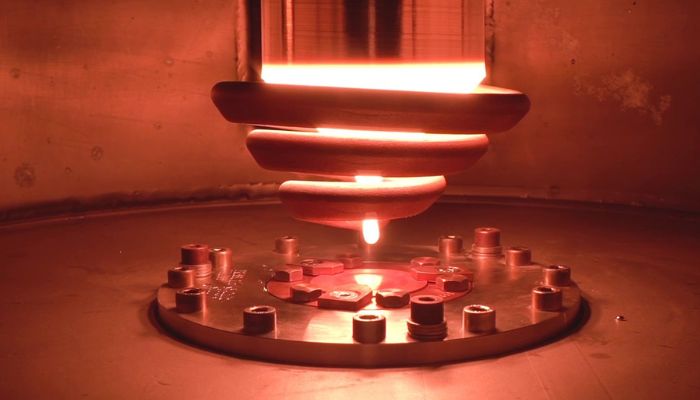
Photo Credits: Sandvik
Post-Processing
In order to achieve an optimal result, it is essential to go through one or more post-processing steps. There are no specific differences in the post-processing of titanium and aluminum, so the following steps apply to both materials. Because titanium and aluminum are often used in mechanically stressed applications, bead blasting and shot peening are very useful. In the first method, small metal or ceramic beads are blasted against the surface of the part to create a controlled deformation of the surface layer of the part. This improves the adhesion of subsequent coatings and reduces the likelihood of cracks and fractures, among other things. Shot peening removes only the top layer of material, which can improve the aesthetic appearance of the part, remove dirt and corrosion and prepare the surface for subsequent coatings.
Another option is to combine metal printing with traditional manufacturing methods. CNC machining is a suitable post-processing process for this purpose, as it ensures tight tolerances and the desired surface finish. With DED technology in particular, 3D printed parts have a very rough surface because the metal is melted directly during the extrusion process. Therefore, CNC machining is always necessary to achieve a smooth and defined surface.
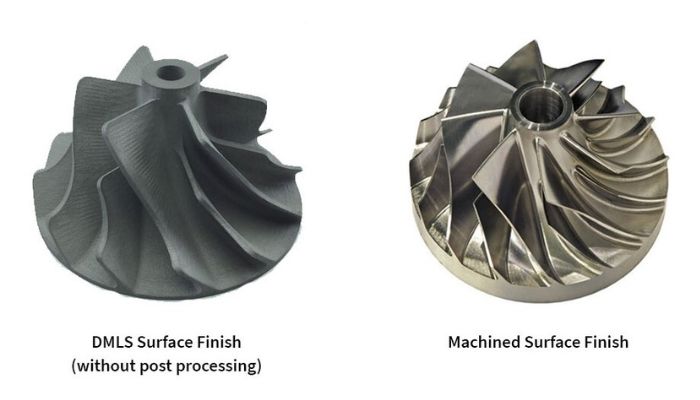
Photo Credits: FacFox
Solution annealing is a heat treatment option that involves heating the printed part to an elevated temperature and cooling it rapidly to change the microstructure, which improves the material’s ductility, or ability to deform under load before breaking. In general, better mechanical properties are obtained with this process, which is mostly used for aluminum parts.
Sintering is also required for aluminum and titanium when they are used in so-called indirect 3D printing processes, such as FDM or powder bonding. After the printing phase, the parts must undergo a debinding process to separate the polymers from the metal binder. The parts are then heated to a certain temperature in a sintering furnace, just below the melting temperature, which will consolidate the final object. This results in parts with very low porosity, as the cavities where the binder was located are closed during the process, resulting in compression.
Applications
The aerospace industry has found great benefit in using additive manufacturing of titanium. It is an ideal material for manufacturing aerospace components, such as jet engines and gas turbines, because it can significantly reduce the weight of highly stressed structures. One example of titanium’s application in additive manufacturing is Boeing’s partnership with Norsk Titanium to manufacture large structural components for the 787 Dreamliner. The technology used in this process is DED, which is reportedly 50 to 100 times faster than powder-based systems and uses 25 to 50 percent less titanium than forging, potentially saving up to $3 million per aircraft.
While titanium is currently being used in space exploration through 3D printing, applications of aluminum in industry have multiplied. For example, Boeing is producing 3D printed parts from aluminum alloys coated with nanoparticles during the cooling phase. This makes it possible to weld an extremely strong aluminum alloy without it cracking when hot. The manufactured parts are much lighter, allowing the aircraft to use fuel efficiently and travel longer distances on the same amount of fuel.
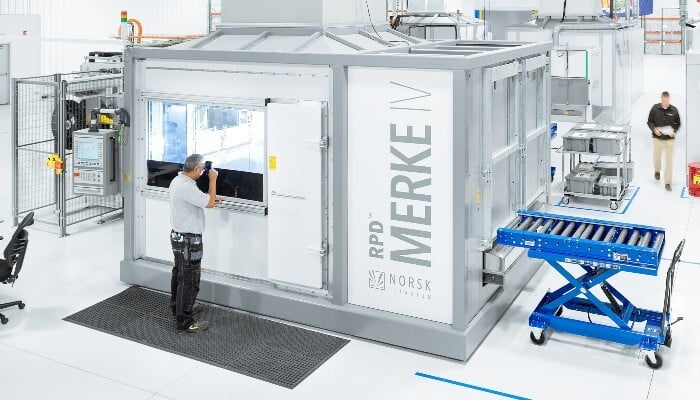
This machine makes parts for the Boeing 787 (photo credits: Norsk Titanium)
Although the high price of titanium in the automotive sector may be an obstacle to its widespread use, we may see an increase in its use in this sector, particularly in the luxury segment. Currently, 3D printing is used to create parts where the weight/performance ratio is crucial. For example, Bugatti printed the brake caliper for its titanium brake system using SLM technology in just 45 hours. The result is claimed to be 40 percent lighter than a conventionally milled aluminum brake caliper. Despite its light weight, the titanium part also ensures its elasticity and temperature resistance.
Aluminum, on the other hand, is even more common in the automotive industry. Porsche used 3D printing to create high-performance aluminum pistons for its flagship 911 model, the GT2 RS. Using this technology, the 700-hp twin-turbo engine can gain up to 30 hp of power and improve its efficiency. In addition, in 2020, Porsche produced an all-aluminum 3D printed housing for an electric transmission, which passed all of the company’s quality and load tests.
Finally, titanium is a very attractive material in the medical industry because of its high strength and corrosion resistance, as well as its biocompatibility, which makes it ideal for orthopedic and dental implants. 3D printing allows for the creation of porous structures that mimic the texture of bone, which contributes to rapid healing and growth of bone and tissue. TrabTech in Turkey makes trabecular implants, such as a hip, using titanium. Aluminum is less common in the medical industry than titanium, but it can be used for orthopedic and dental applications.
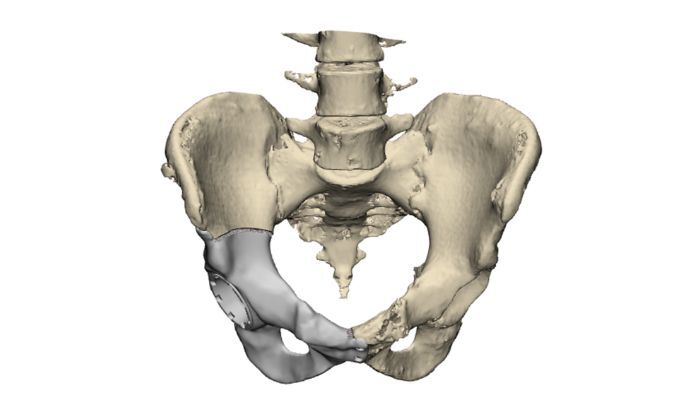
TrabTech manufactures trabecular titanium implants (photo credits: TrabTech)
Price & Manufacturers
A major drawback of titanium is its high price. According to Wohlers 2021, Ti-6AI-4V titanium alloy powder or pure grade 2 titanium costs about 363 USD per kilogram, placing it in one of the highest price segments. Aluminum, on the other hand, is significantly cheaper, with AISi7 aluminum alloy available for $94/kg powder and AISi10Mg for $98/kg.
On the manufacturing side, we have Heraeus Additive Manufacturing, a German company specializing in precious metal processing that produces various types of titanium, such as 6Al-4V, grade 5 and grade 23. GKN, on the other hand, offers pure titanium and Beta 21S titanium. On the aluminum side, Uniformity Labs and Equispheres produce AISi10Mg aluminum alloy, while APWorks produces 7000 series aluminum alloy powder.
Do you use more titanium or aluminum in additive manufacturing? Let us know in a comment below or on our LinkedIn, Facebook, and Twitter pages! Don’t forget to sign up for our free weekly Newsletter here, the latest 3D printing news straight to your inbox! You can also find all our videos on our YouTube channel.
Thanks for suggesting suitable corrugated iron.
I’m constantly searching on the internet for posts that will help me. Too much is clearly to learn about this. I believe you created good quality items in Functions also. Keep working, congrats!