Tiffany & Co. Incorporates a 3D Printed Façade on Iconic Store
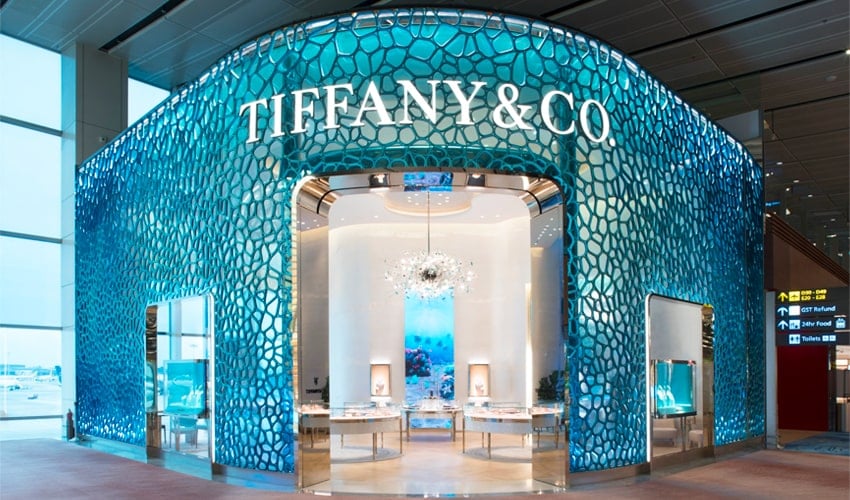
If you plan to travel to Singapore, you can not miss this work of architecture. Located at Singapore’s international airport, in Changi, well-known luxury brand Tiffany & Co. has integrated a one-of-a-kind façade that is as iconic as the brand name itself. Specifically, the store in question is located in the airport’s Piazza Garden, near the Jewel Changi, and the sustainable structure has been designed by architect Moshe Safdie, in collaboration with the firm MVRDV. What is interesting about this creation is the use of additive manufacturing and recycled materials as a production method, highlighting the House’s commitment to sustainability. The 3D printing process of the façade for the Tiffany & Co. store also involved the Dutch company Aectual and several engineers from the Italian company BUROMILAN. Its coral-inspired design and color scheme will certainly as well catch the eye of any traveler strolling through the airport.
It is becoming increasingly common to see design projects that use additive manufacturing to create decorative structures for stores, businesses and commercial premises. Previously, fellow luxury brand Dior turned to WASP to create an eco-friendly pop-up store. Meanwhile, in the Netherlands, Rotterdam-based studio RAP designed a façade for a luxury boutique on the popular shopping street P.C. Hoofstraat. Indeed, these examples show not only the beauty that can come through the use of optimized designs and 3D printing to create impressive exteriors, but also the increasing important of innovation. Whether in terms of architecture or by increasing sustainability, a concern that certainly could be said to be at the forefront of issues in our times.
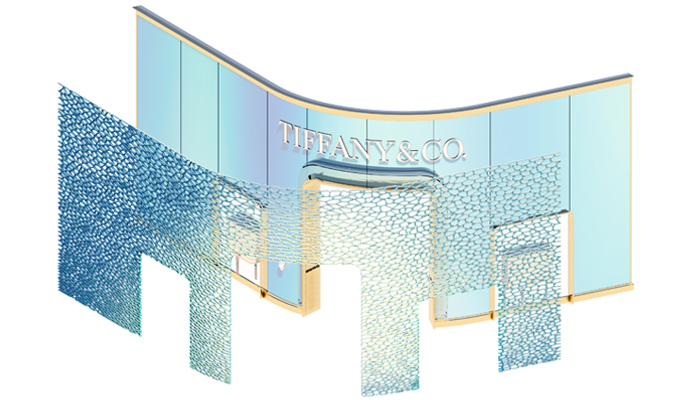
Initial rendering of how the 3D façade would be implemented in the store
3D Printing of the Façade for Tiffany & Co.
During the process of creating the Tiffany store, the MVRDV team highlighted key aspects that highlight the brand’s identity and history, including the incorporation of iconic elements such as the Tiffany Blue®, among others. Using coral reef patterns as a guide, they created an organic screen that covers the store’s façade. This screen includes screen-printed glass with a gradient of colors, ranging from the iconic Tiffany Blue to a deeper blue that evokes the marine environment. The gradient is repeated in multiple elements of the 3D printed design, such as at the store entrances, where the display shows a gradient from light blue on the front to dark blue on the back. In addition, this gradient is reversed at the corners of the façade, with a gradual transition between the two shades, creating a three-dimensional effect.
Innovation was also present in the materials used. The MVRDV team explains, “3D printing experts Aectual developed a process to produce the 50-millimetre-thick screen using recycled plastic, including reclaimed and recycled fishing nets.” This choice of both materials and technology not only reflects inspiration from the oceans, but also contributes to their protection. The need to meet strict fire safety standards in an airport environment was solved by BUROMILAN. Its engineers added a chemical product made from seawater, providing a unique solution. If you want to know more projects of this style or get more information about this 3D printed façade, click here.
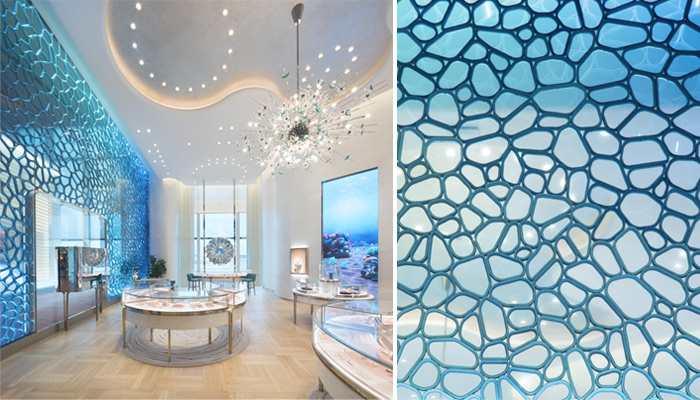
The interior of the Tiffany & Co. store, and next to it a close-up view of the 3D printed façade
What do you think of the 3D printed façade made for Tiffany & Co? Let us know in a comment below or on our LinkedIn, Facebook, and Twitter pages! Don’t forget to sign up for our free weekly Newsletter here, the latest 3D printing news straight to your inbox! You can also find all our videos on our YouTube channel.
*All Photo Credits: Tiffany & Co. / MVRDV