Thought3D Talks Adhesion and Drying for More Standardized, Quality 3D Printing
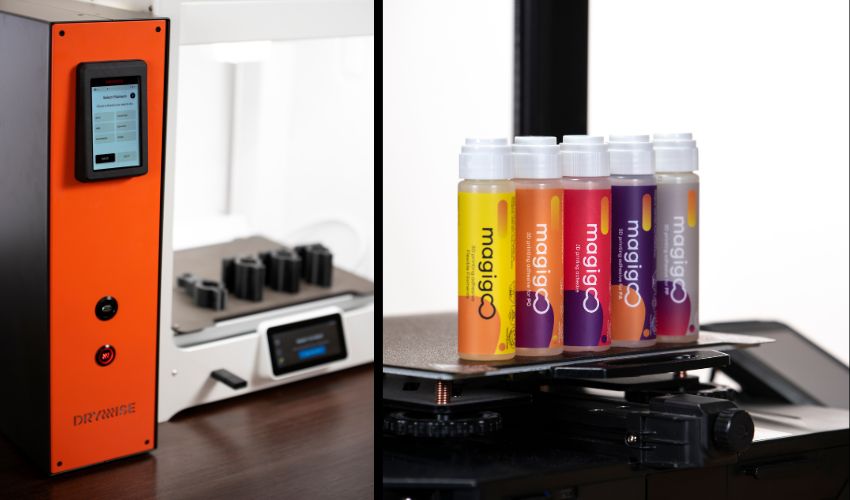
When it comes to 3D printing, getting a successful print is dependent on a number of aspects, especially as use cases become more industrial. Take for example FFF 3D printing. Two of the key factors in determining whether a print will be successful are that it is properly stuck to the build plate during printing (improper sticking is one of the leading causes of build failures) and that the material is effectively dry. Hence the success of Thought3D, the creators of the Magigoo adhesives and their newest product DryWise. We spoke with co-founders, Edward Borg and Andrei-Andy Linnas, to learn more about the company as well as their groundbreaking products.
3DN: Could you introduce yourselves?
E: Hello, I’m Edward Borg, co-founder of Thought3D. My background is in engineering and currently I spearhead the development of DryWise, among other ventures within our company.
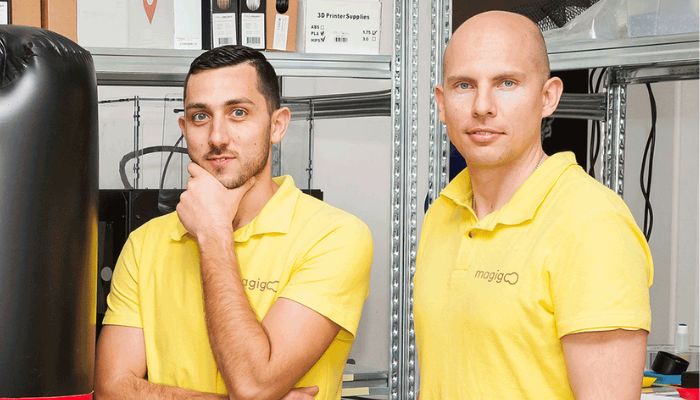
Edward Borg (left) and Andrei-Andy Linnas (right), two of the three co-founders of Thought3D (photo credits: Thought3D)
A: I’m Andrei-Andy Linnas, also a co-founder and the commercial strategist of Thought3D. I oversee our reseller network, client relations, business development and investor relations.
3DN: How did Thought3D come about? What is its mission?
E: Thought3D’s journey began several years back when Dr. Keith M. Azzopardi and I were exploring an idea related to scuba diving, which led us to 3D printing. In those early days, when filament spools were still quite expensive, we were creating our own desktop filament extruder. We were also thinking of new 3D printer technologies, whilst designing and building our own, and offering 3D printing and design services. This experience ultimately led to Magigoo, our first product. It was born out of the challenges we were facing with print adhesion and subsequent difficulty in detaching finished prints from the build plate.
We were determined to find a solution since the market offerings at the time were subpar, providing adhesion without an easy release mechanism. For us, this was a critical flaw. Leveraging our combined expertise—Keith’s chemistry and material science prowess and my technical background—we developed a product that not only adhered but also released when needed. Our prototype, first housed in a Nutella jar, marked the humble beginnings of our innovation, the first iteration of Magigoo.
Our technical skills were solid, but we lacked the commercial savvy to bring our product to market. That’s when we connected with a university incubator program, where Andy was at the helm. Initially our mentor, Andy’s insight and guidance were invaluable, before he eventually became an integral part of the team.
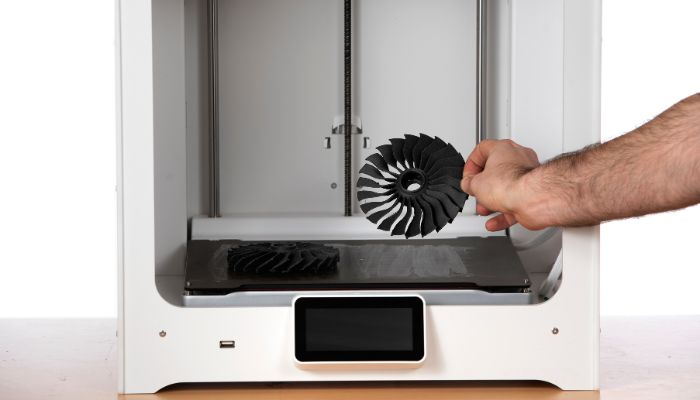
Magigoo is exceptional not just for its sticking ability but also the quick-release of parts after printing (photo credits: Thought3D)
A: From my perspective, at the university, Edward and Keith were juggling multiple projects, a common scenario for early-stage startups. However, the pivotal moment came when Leapfrog, a Dutch manufacturer, visited and showed a keen interest in the makeshift solution in the Nutella jar. It was a clear sign that, in an already saturated printer market, we needed to concentrate our efforts to find an easier way to the market. With Magigoo, we had the opportunity to address a tangible concern for the wider 3D printing community.
E: Though adhesion issues were widespread, the available solutions were either ineffective, overly complex or outright dangerous. Magigoo stood out as a water-soluble, user-friendly, and eco-conscious alternative. We officially launched at TCT3Sixty in Birmingham in 2015, where the response from resellers and distributors was overwhelmingly positive. This feedback was instrumental in refining Magigoo into the product it is today. Building on that success, we later introduced DryWise, our latest innovation in the 3D printing space.
3DN: Could you tell us more about Magigoo?
E: Magigoo was originally developed for glass build plates which are quite uniform across the board. When it came to flex plates, with so many different textures, coatings, binding mechanisms etc., the challenge was greater. However, Magigoo rose to the occasion. Its standout feature is the ease of release—even if a print stubbornly adheres, a splash of water can dissolve the adhesive thus freeing the print.
From the first day we aimed for global distribution, which meant ensuring the product was non-toxic, non-hazardous and non-flammable. And over the years, we’ve refined both the formula and the packaging. Our initial design resembled a marker, but we encountered some hiccups with the original felt tip applicator. To address this, we ended up creating multiple prototypes over time, all with unsatisfactory results. Today, Magigoo resembles a glue stick, a form that has proven most effective for our users.
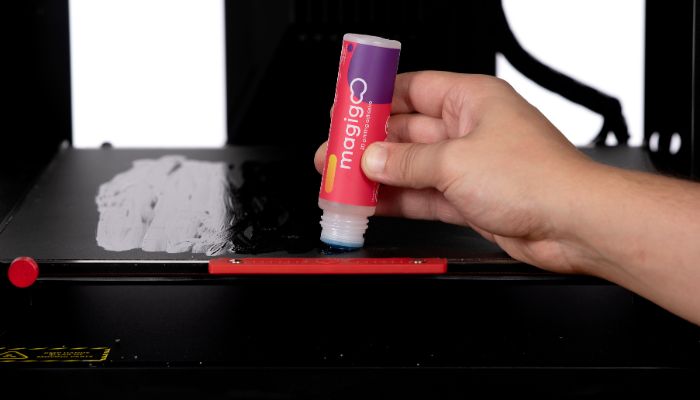
The current iteration of Magigoo resembles a glue stick (photo credits: Thought3D)
A: Delving deeper into the formula’s evolution, a pivotal moment was in 2017 during our visit to China, where we engaged with manufacturers and recognized a shift towards more professional applications. This coincided with Ultimaker’s announcement of the third-party materials program, prompting us to tailor Magigoo formulas for specific materials. Take Magigoo PP. It was developed as our response to a challenge set by a large glue producer, who said that sticking PP is very close to impossible. But we managed to solve what was considered a very tough problem in a record four months.
Today Magigoo PP is probably one of the leading adhesives for any PP material, making it really easy to print. We continued this trend with Magigoo PC, Nylon, and other variants, eventually creating the high-temperature versions in partnership with Essentium for materials like PEEK and PEI. Our latest collaboration with BASF tackles metal filament, ensuring no chemical residues remain post-printing and that the initial, delicate parts aren’t damaged during removal.
These diverse formulations reflect our understanding that one size does not fit all. Different materials have unique properties, and we meticulously test various filament brands and types to guarantee compatibility and performance on multiple surfaces. We’re not just creating an adhesive; we’re crafting a comprehensive solution that balances robust adhesion with gentle release, without introducing hazardous chemicals.
E: The quest for a universal, no-adhesive-needed build surface is unrealistic. Even the most ideal surfaces degrade over time, affecting print quality. That’s where Magigoo excels—it’s not just about maintaining adhesion; it’s about ensuring consistency and longevity, even as surfaces like flex plates begin to show wear.
A: Magigoo isn’t merely a failsafe; it’s a bridge for users of varying expertise in 3D printing. While manufacturers focus on enhancing their machines and filaments, Magigoo serves as the integrative element, smoothing the learning curve for novices and bolstering the confidence of seasoned professionals. With a database of over 160 verified materials, our product is rigorously tested to minimize common printing failures. Magigoo is the key to successful prints, preventing issues like warping and ensuring every user can achieve their desired results with ease.
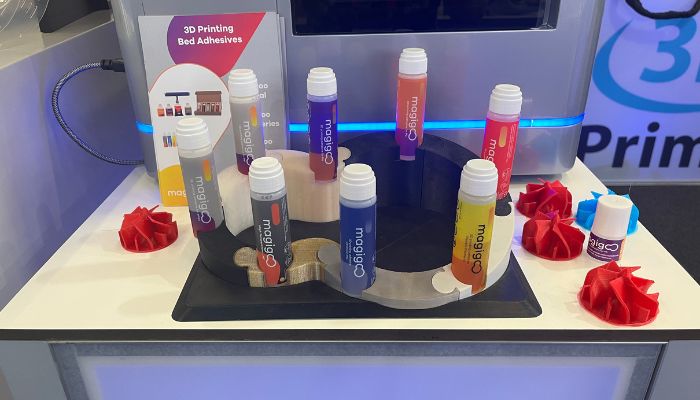
Part of Magigoo’s success is the fact that there are individual formulas to fit different materials, as seen here at Formnext 2023 (photo credits: 3Dnatives)
Our pricing strategy has often been a topic of conversation, with some initial perceptions that a 50ml bottle of Magigoo may appear costly. However, users quickly discover the compact container lasts them much longer than alternative products. Many are surprised to find that a single application can be effective across multiple prints, making the cost per print not only competitive but, in many instances, more economical than budget adhesion alternatives.
When you factor in the extensive testing, support accompanying each bottle and the unparalleled customer service we provide—services that are unmatched by any other product in the market—the value of Magigoo becomes evident. The price reflects not only the high-quality adhesion it ensures but also the peace of mind it offers—acting as a reliable insurance for the success of your prints.
3DN: Tell us more about DryWise, Thought3D’s latest project, what was the driving force in introducing it to market?
E: The vision for DryWise was rooted in our own experiences while perfecting Magigoo PA. We were frequently using nylon for quality control, which necessitated constant drying of the material. This process was not only time-consuming but also wasteful, causing delays in development. The industry’s vague guidelines on drying—often as non-specific as “4 hours at 60°C” or, at times, entirely absent—made it a frustrating game of guesswork.
You might bake the filament, attempt a print and find the material to be still damp. To combat this, we began crafting our own standard operating procedures, paving the way for a more streamlined approach. It wasn’t until Magigoo gained traction that we revisited and refined these concepts into what would become DryWise.
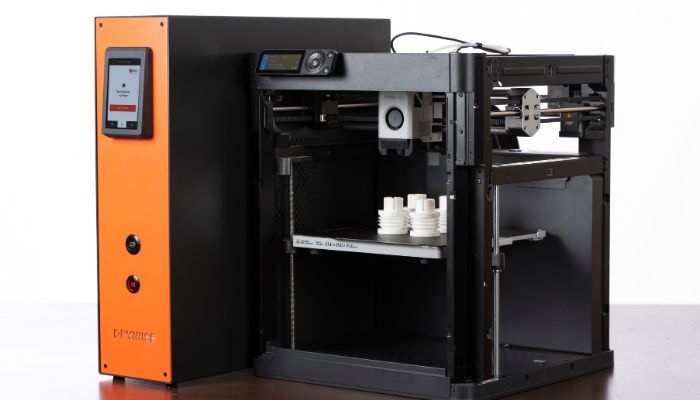
Thought3D’s latest product, Drywise, helps take the guesswork out of drying filaments (photo credits: Thought3D)
Understanding DryWise, however, requires an appreciation of the critical role drying plays in 3D printing. Anyone coming from the world of injection molding appreciates the importance of drying the material. In the 3D printing world however, it is often overlooked until problems arise and then it becomes a significant hurdle.
A: Observing the industry, we see this push towards industrial applications where the stakes, and margins, are higher. However, for the industry to evolve and for FFF to transition from a prototyping tool to a reliable instrument, consistency and repeatability are essential—not just in the machinery but in the entire process.
Yet, we recognized a gap: the industry’s narrow focus on individual solutions often overlooked the broader process. This oversight is particularly problematic for large industrial companies. They operate across diverse climates and with varying levels of operator expertise, leading to inconsistencies in material dryness and print quality despite stringent manufacturer quality control processes.
DryWise is our answer to this challenge. It’s designed to bridge the gap in the value chain, ensuring that the materials the end-user experiences are at the highest quality level, regardless of prior handling or environmental conditions. In practical terms, DryWise serves as a quality assurance tool, providing a level of reliability that is indispensable for true industrial applications. It’s not merely a product, it’s a commitment to repeatability and reliable excellence in the 3D printing processes.
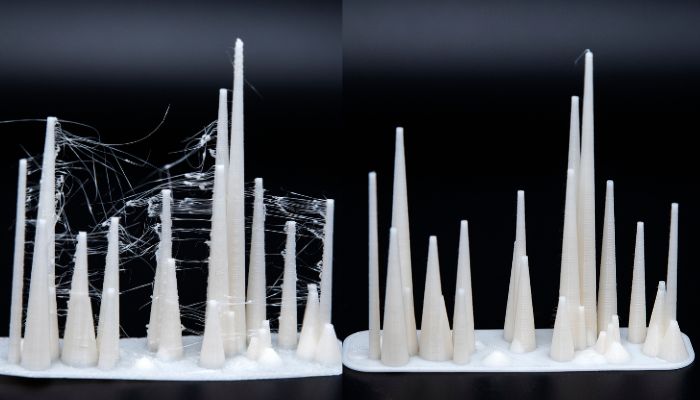
Wet filament printed without Drywise and with Drywise, clearly showing the effect of drying on the print quality (photo credits: Thought3D)
Investing in DryWise is a savvy decision when considering the full spectrum of its benefits. Beyond just drying, it offers comprehensive quality assurance that translates into significant time and energy savings, minimizes material waste and enhances print quality. Additionally, it reduces the necessity for separate material storage solutions. To sum it up, DryWise has the power to elevate the performance of low-priced printers, enabling them to produce results that rival those of their high-end counterparts.
3DN: Any last words for our readers?
A: We have always distributed our products through resellers, so we are one step removed from clients. We want to hear the stories from end-users (successes or failures) about the products. This will help us adapt and continue to improve.
E: Building on that, we have already proved how successful and efficient we are at solving challenges. We look forward to hearing of any specific issues requiring results. You can get in touch with us or learn more about Magigoo on our website HERE or about Drywise HERE. There you can also download resources like your very own free Magigoo manual, with key 3d printing takeaways and learnings or download the whitepapers regarding the effect of moisture on 3D printing.
What do you think of Thought3D? Have you already used Magigoo or DryWise? Let us know in a comment below or on our LinkedIn, Facebook, and Twitter pages! Don’t forget to sign up for our free weekly Newsletter here, the latest 3D printing news straight to your inbox! You can also find all our videos on our YouTube channel.
*Cover Photo Credits: Thought3D