Thermwood develops a process for large format vertical 3D printing
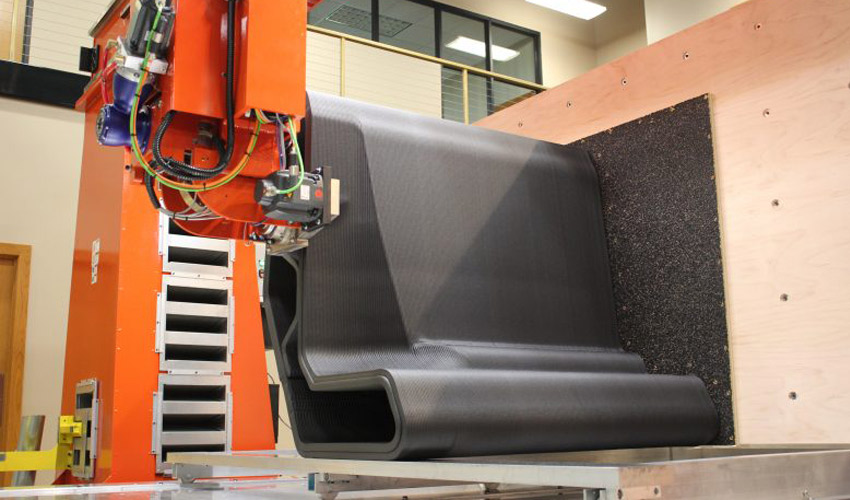
Large-format 3D printer manufacturer Thermwood Corporation has unveiled a new approach to XXL 3D printing: the creation of parts vertically, rather than horizontally like all machines on the market. This development will allow the company to further increase its printing volume while maintaining a certain final strength. Thermwood has in fact designed prototypes in carbon fiber reinforced ABS and PSU/PESU composites.
You may have heard of Thermwood Corporation from its long-standing partnership with Local Motors, an automotive manufacturer that uses additive manufacturing in the design of its vehicles. The American company, which developed the Olli stand-alone minibus, can now rely on a composite solution that combines large volume with increased strength. This time, the manufacturer adapted its LSAM MT machine and patented its Vertical Layer Print (VLP) process, which consists of printing parts vertically. The company claims that this process allows it to produce parts up to 6 meters high in one go.
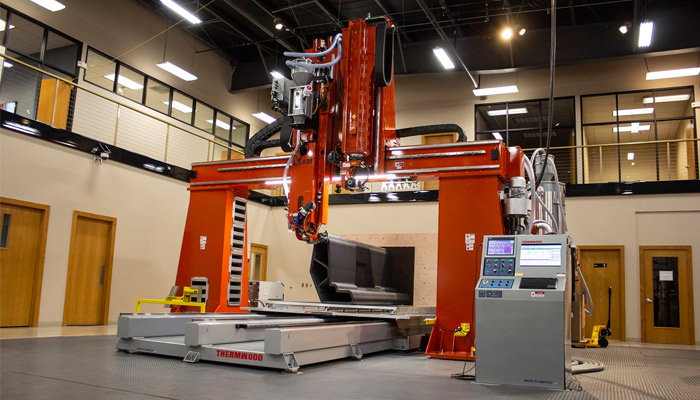
The LSAM MT machine (All image credits: Thermwood Corporation)
LSAM large format machines generally look like giant gantries, with a fixed table on which a mobile arm moves, at the end of which is the extruder. When printing vertically, the platen must be positioned vertically and move according to the desired pattern. The new LSAM MT solution consists of a fixed gantry and a mobile platen, requiring a change of approach to allow vertical printing. More precisely, the part to be created is printed on a support structure, which is fixed at the back and moves on the mobile table.
Thermwood explains: “A second printing platen measuring 1.5 metres by 3 metres, mounted vertically, was added at the back of the main platen. As the piece grows, the movable platen pulls it onto the support structure. This approach allows us to design parts up to 1.5 meters on the Z axis and 3 meters on the X and Y axes.” It’s easy to imagine the range of possibilities, especially since the manufacturer’s machines can provide a cutting function, ideal for quickly machining the desired parts.
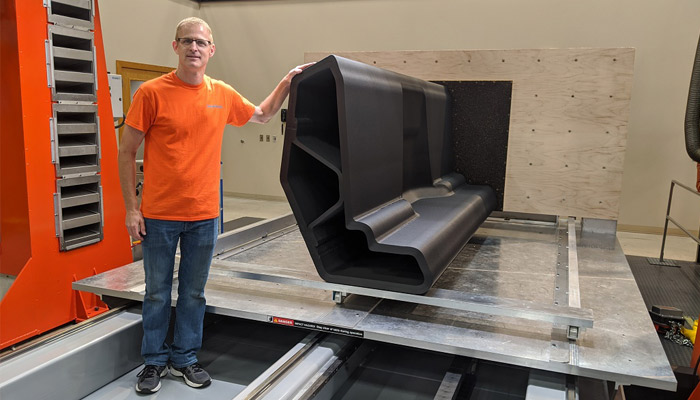
One of the pieces created with the VLP technology
The teams claim that they have carried out tests with rather technical materials, since only composite materials were preferred – ABS and carbon fibre-reinforced PSU/PESU. The part made from the high-temperature PSU/PESU had a total weight of 540 kilos – the maximum weight for the moving platter system – and was completed in 16 hours and 40 minutes. You can find more information on the manufacturer’s website HERE, and also discover the live 3D printing process in the video below:
What do you think about the vertical 3D printing process developed by Thermwood? Let us know in a comment below or on our Facebook and Twitter pages! Sign up for our free weekly Newsletter, all the latest news in 3D printing straight to your inbox!
Giant gantries