What Are the Top 4D Printing Projects?
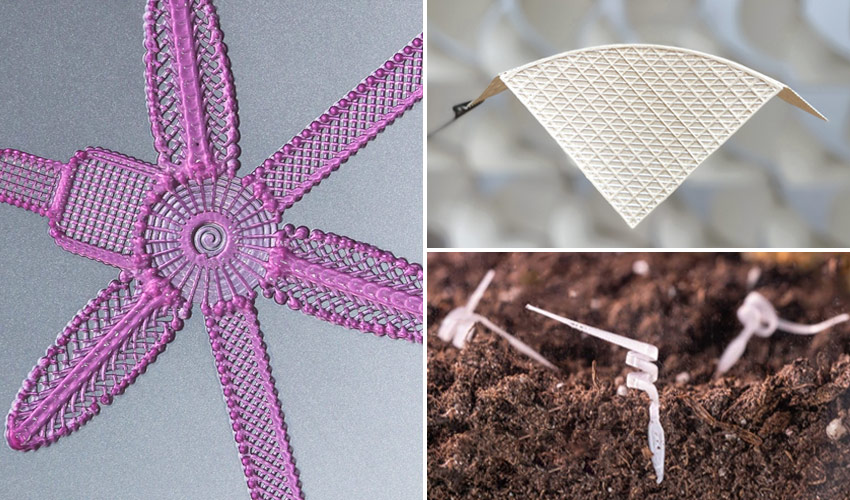
Have you heard of 4D printing? Building off conventional 3D printing, 4D printing incorporates another dimension: time. This means that the final object does not stay static, rather it is able to change shape, color or size after receiving an external stimulus. Introduced in 2013, the origins of 4D printing trace back to Sklyar Tibbs from MIT’s Self-Assembly Lab, who is still one of those most active in projects today, even if the field has come a long way. But what projects are available? We took a closer look at different successful examples of 4D printing that can be found in the sector, including applications and materials, in our latest listing.
Mizzou Engineering Develops Implant Made From Smart Material
As part of a study published earlier this year, a team of researchers from Mizzou Engineering has succeeded in developing a medical implant using 4D printing. The implant can be fully personalized and also promotes soft tissue regeneration thanks to its material composition. According to the scientists, the decisive factor for a personalized treatment option was the 4D printing of the implant. 4D printing combines 3D printing technology and smart materials that can adapt their functions in certain contexts. In this case, a bioresorbable shape memory elastomer was used. This made it possible to address the patient’s complaints and identify an optimal treatment: “We designed an in vitro model of the patient and implanted it intravascularly inside a 3D printed heart of the patient to show a proof of concept of how the material would be used for that issue,” says Alireza Mahjoubnia, PhD student in mechanical engineering. “The material can change behavior based on physiological conditions. We program its shape to go through a catheter and after it gets inside the left atrial appendage, it can recover its shape to go back to its original shape, showing shape memory behavior.”
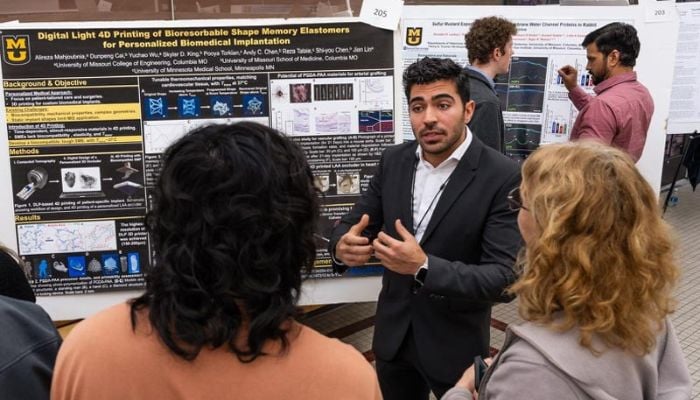
Photo Credits: University of Missouri
4D Printing for Bone Regeneration
Another example of 4D printing in the medical field, a group of researchers in China has studied the possibility of creating smart 4D biopiezoelectric scaffolds for bone regeneration. Piezoelectricity in human bones is a key factor in bone regeneration. Therefore, biopiezoelectric materials have gained considerable attention in the repair of damaged bone. However, traditional manufacturing strategies still encounter limitations in creating customized scaffolds, hindering their clinical applications. Researchers therefore investigated the uses of 3D and 4D printing for the fabrication of biopiezoelectric scaffolds into more complexly shaped structures. Specifically, 4D scaffolds can provide time-dependent programmable tissue in response to external stimuli for bone regeneration. These intelligent implants that change shape, properties, and functionality in bone tissue engineering and could thus be used as next-generation implants.
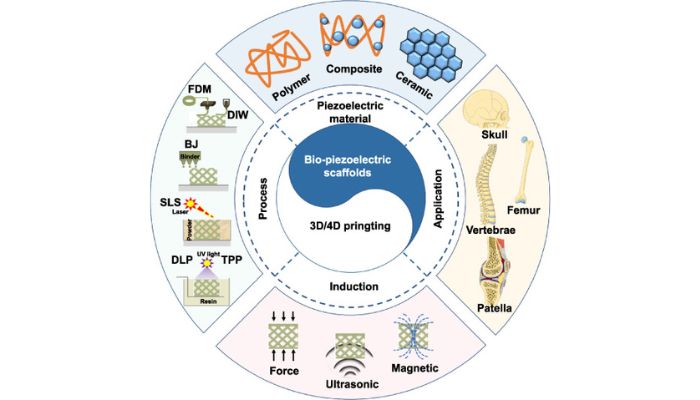
Piezoelectric materials, printing processes, and potential applications for 4D implants. (Credits: Annan Chen et al 2023 Int. J. Extrem. Manuf.)
4D Devices That Mimic Plants
The next application of 4D printing comes to us from a group of researchers at the Wyss Institute and the School of Engineering and Applied Sciences, both institutions of Harvard University. The team has found a way to mimic the dynamic changes of plants and flowers in response to humidity and temperature using 4D-printed hydrogel composites. To achieve this, they developed an ink made of aligned cellulose fibrils derived from wood and configured according to the mathematical model of 4D printing. This ink encodes expansion and stiffness properties allowing the programming of expansion behaviors when the prints are immersed in water. Similarly, different hydrogel materials can be used and cellulose fibrils can be replaced with other fillers, such as conductive ones. Applications with this material include medical devices that adopt programmed shapes upon contact with body fluids; smart textiles; soft electronics; sensors; and electrical actuators.
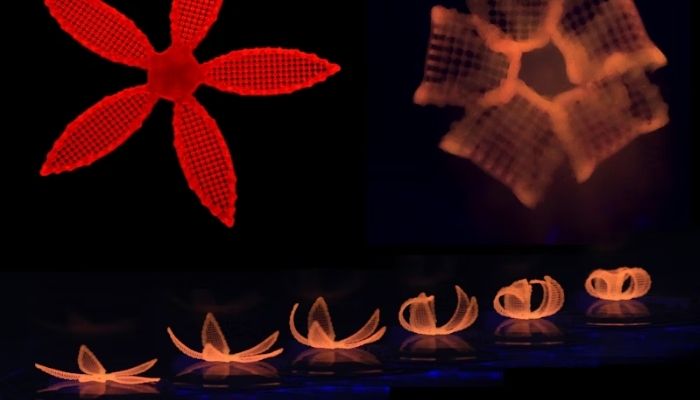
Photo Credits: Wyss Institute
4D Printing for Robotics
Robotics is yet another area where 4D printing could be useful. For example, Researchers Dr. Liwen Zhang and Dr. Ruirui Quiao at the University of Queensland have developed a 4D printing technology that creates liquid metals for robotics that change shape using near-infrared light. The metal polymers, which can perform mechanical tasks using infrared lasers, are currently in the research phase, but offer potential for aerospace and medical applications, for example in the production of artificial muscles. The printing resins are produced using round metal nanoparticles that react to infrared light. This allows them to be controlled and moved. The laboratory’s new manufacturing methods make it possible to create flexible designs that are also strong. Dr. Zhang emphasizes: “4D printing takes traditional 3D printing and adds a new dimension – the dimension of time. The versatility of this technology has been demonstrated by their 4D printed designs that can bend, grasp, lift, and revert to pre-programmed shapes, surpassing their weight limits. Notably, the method eliminates the need for traditional wiring or circuits, providing engineers with the ability to shape smart liquid metals over time.” The technology will also be used for soft robotics and related technologies to mimic natural movements and interactions.
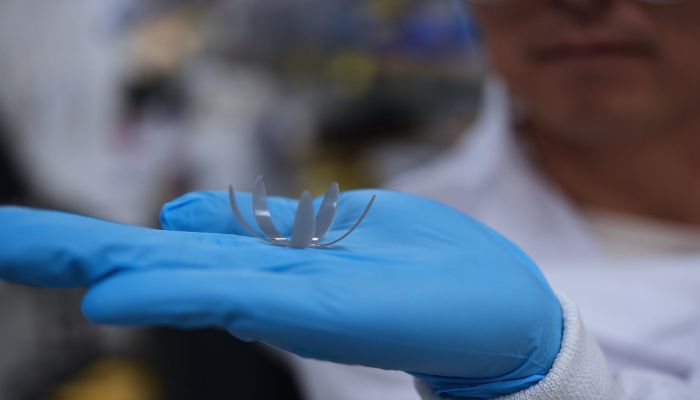
The 4D structure that is set in motion by near-infrared light (photo credits: Australian Institute of Bioengineering and Nanotechnology University of Queensland)
4D Printing for Space Travel
Zortrax, a 3D printer manufacturer, worked for over a year on a 4D printing project funded by the European Space Agency to develop electrical mechanisms using 3D printing to enable bending, twisting and unfolding. Back in 2013, 4D-insertable structures were researched that would move when heated. However, the project presented many difficulties as the process was difficult to control and activated at 40°C. This problem has now been solved by using new materials, software and 3D printers. The materials used were shape memory polymers, which have a glass transition temperature of 75°C, and the electrically conductive filament FIBERFORCE NYLFORCE Conductive, which acts as a heater and triggers the shape memory effect. This process describes the ability of certain materials to return to their original shape after being deformed. The Z-SUITE software and the M300 Dual dual extrusion 3D printer, which uses a bi-material 3D printing process and can print with two print heads simultaneously, were also chosen. The design was made spring-like to generate enough torque to allow the 3D printed chassis to rotate without friction. This advance offers great potential in space travel as it could reduce the weight of antennas or sensors and the process can also be applied to larger mechanisms. The project is currently still in the research phase.
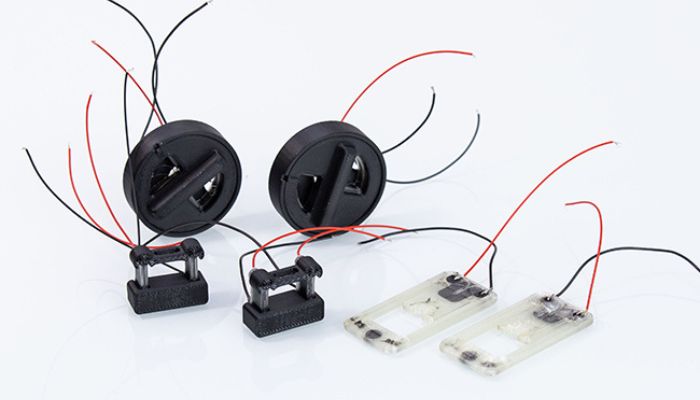
Photo Credits: Zortrax
The I-Seed Robot
Researchers at the Italian Institute of Technology (ITT) have designed the soft robot I-Seed using 4D printing. This plant seed-inspired robot can analyze and monitor soil and air temperature and humidity, and detect the presence of pollutants. Specifically, I-Seed was built by mimicking the operation of a South African geranium and is able to change shape when it absorbs moisture. The researchers printed the robot using the FDM process with biodegradable polycaprolactone-based polymers. To design I-Seed , they mimicked the biomechanical specifications of the African plant so that it would have dimensions and performance as close as possible to a real seed.
4D Printed Self-Assembling Objects From MIT
As mentioned previously, 4D printing’s origins can be traced back to Skylar Tibbs and the MIT Self-Assembly Lab. Therefore, it should come as no surprise that the lab continues to be extremely important in the 3D printing space with many different projects, including an older project (from 2013!) but one that is iconic in the sector: 4D printed self-assembling cubes. These are made of hydro-reactive composite polymers with hydrophilic elements and non-active, rigid elements. Due to this, when exposed to water, the chain would be able to morph into a new shape, namely a cube, as seen in the video below. Since then, the lab has continued it works with recent projects including a 4D Knit Dress
4D-Printed, Bistable Structures
4D printing is treated in specialist circles as an “upgrade” to 3D printing, as it incorporates the component of time. For this reason, innovative research is also focusing on testing materials for 4D printing and experimenting with designs for 4D printing. This was also the case at EHT Zurich, where PhD student Tim Chen was involved in a research project on the design of printed, deployable and active systems. He initially focused on exploring the design for these 4D-printed structures, aiming to control his materials so that the parts would react to the environment. He focused on bistable connections within his structures that could cause the structures to change shape. Such desired changes to shapes could prove profitable for various applications, including architecture, soft robotics, aerospace and the automotive industry.
4D Hydrogel Structures for Precise Implantation
Published in the journal Nature Communications, a recent study describes the development of dynamic thermosetting polyurethanes for multimaterial 4D printing, with the goal of creating support structures that can be implanted in a minimally invasive manner. The research team developed structures with a shape memory that is activated by body temperature and that deform when they come into contact with water. The application of these supports works as follows: a 2D pattern is printed that can be temporarily reduced to a one-dimensional shape, facilitating its insertion through a catheter. Once implanted, the body temperature causes the material to recover its original 2D shape. Then, upon hydration, the material expands and transforms into the desired 3D structure due to a swelling mismatch. This combination of shape memory, programmable deformability, and expansion and stiffness properties makes the thermoset polyurethanes that have been developed promising for the creation of filling supports for minimally invasive implants.
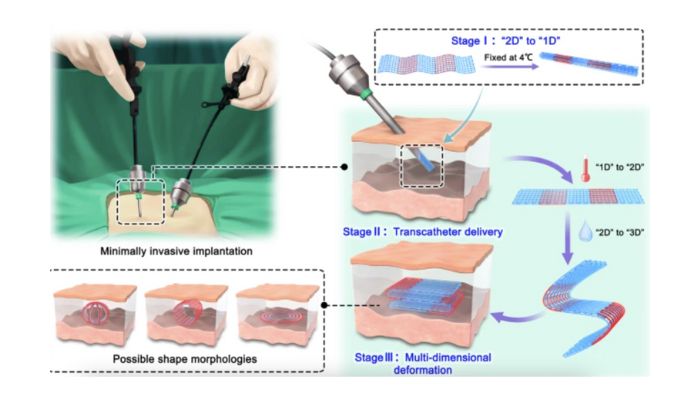
Photo Credits: Nature Communications
4D Printing Shape Memory Resins
This time, we tell you about a research project using shape memory resin. Researchers have developed a material based on photosensitive resin and liquid crystals. The latter enable the future 3D-printed part to change under the effect of temperature. Specifically, they mix 5% by weight of crystals in a tank with toluene, at a temperature of 70°C. The mixture is cooled overnight, allowing the toluene to evaporate. The resulting material is then used with a DLP 3D printer. And the results are impressive! When subjected to higher temperatures, 3D printed parts deform, then return to their original shape when the temperature drops.
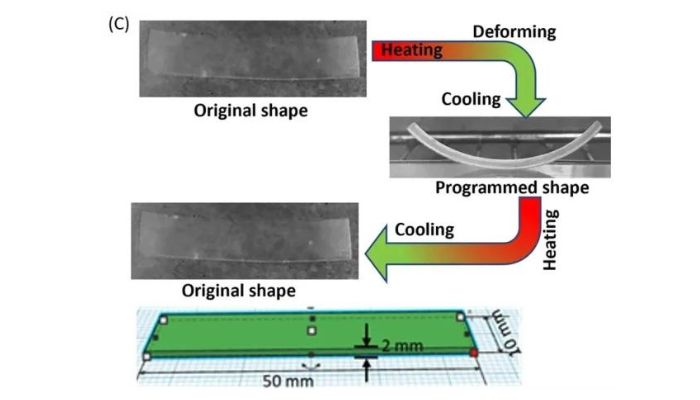
Photo Credits: Nature
Magnetoactive Polymer Actuators
A team of scientists at CEA-Iramis in France has developed actuators in magnetoactive polymers by 4D printing of smart materials. First, they conducted experiments and simulations to analyze how magnetite nanoparticles self-assemble into wire-like structures within photosensitive resins. The mechanical properties of the photopolymers can be adjusted by varying the resin composition, and the magnetic response can be modified by adjusting the nanoparticle loading in the printed layer. The scientists then adapted a DLP 3D printer to apply a magnetic field with varying intensity and direction during the fabrication of each layer. In this way, they were able to make a series of objects with programmed behavior, such as actuators that rotated or bent on command. They also combined magnetic wheels with non-magnetic elements to create linear actuators or active grippers.
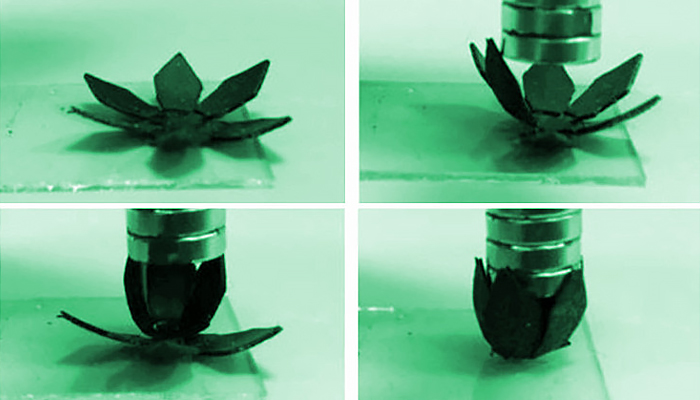
Photo Credits: CEA-Iramis
A 4D Printing Process for Hygromorphic Structures
Hygromorphic behavior is defined by Harvard as “responding to changes in environmental humidty by changing geometry.” As a result, hygromorphic smart structures are in high demand due to their wide-ranging applications including weather-responsive archiectural skins to adaptive wearables. And now it could be possible to use 4D printing to make these structures. More specifically, in a recent research article, researchers show how fused filament fabrication incorporating biobased cellulose-filled filaments with varying stiffness and hygroresponsiveness combined with mesoscale structuring in printed elements can help achieve humidity-responsive actuation. Using a standard dual-extruder FFF 3D printer, it was possible to make parts that responded to ambient relative humidity showing that it could fold in on itself. An interest process to create 4D-printed, humidity-responsive structures.
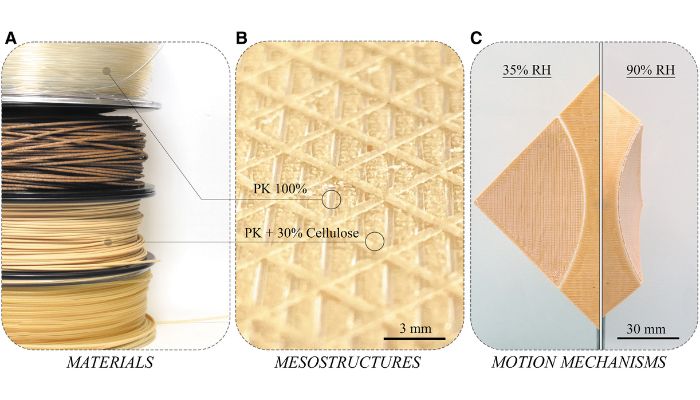
A graph showing the materials used, design of the mesostructures and the results of the hygromorphic structures (photo credits: Tahouani et al.)
What do you think of these 4D printing projects? Let us know in a comment below or on our LinkedIn, Facebook, and Twitter pages! Don’t forget to sign up for our free weekly newsletter here for the latest 3D printing news straight to your inbox! You can also find all our videos on our YouTube channel.