The Coolest Metal Applications at Formnext 2024
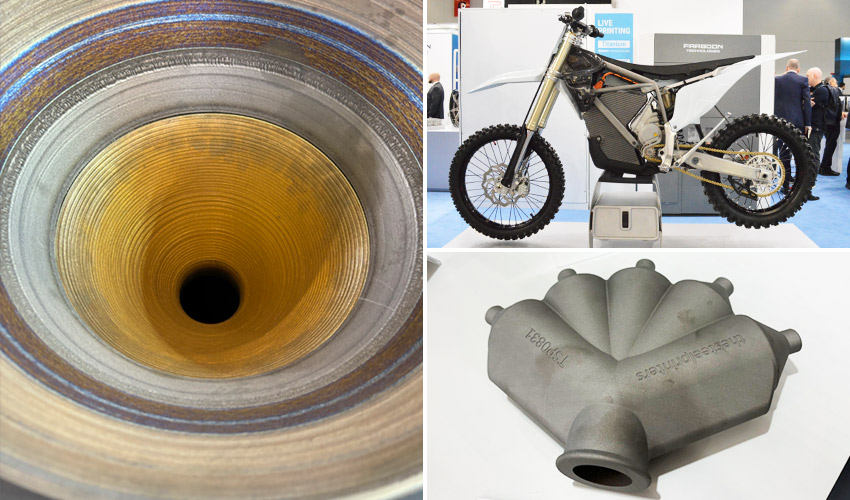
It goes without saying that at Formnext attendees will see incredible solutions, whether for 3D printing, software or materials. But what should also not be ignored are the amazing applications that different companies are bringing to their booths. At Formnext 2024 especially there have been some incredible metal applications that we have seen around the show in different sectors including aerospace, automotive, dentistry and many more. That’s why we decided to take a look at some of the coolest examples that we saw this year, put below in no particular order.
InssTek’s Multi-Material Nozzle
The first application that has blown us away at Formnext is undoubtedly the multi-material rocket nozzle present at InssTek’s booth. The 3-ton rocket nozzle (measuring 301 x 201 x 567 mm and made in 600 hours) and extension (432x 270 x 169mm and made in 64 hours) were created using Directed Energy Deposition 3D printing in partnership with the Korea Aerospace Research Institute (KARI). The multi-material factor comes from the fact that each part was manufactured using the optimal material, a unique feature possible with InssTek’s DMT technology. For example, in the nozzle itself, the inner part is made of Al-Bronze with a cooling channel at 1mm intervals while the outer part is made of Inconel 625. Meanwhile, the extension was made using C-103, one of the most exciting materials currently being used in the space industry.
The resulting unified, high-performance unit is remarkable because combining these different metals enables the use of the strength of each one, allowing for the creation of intricate structures and functionalities that can enhance the efficiency and reliability of rocket engine components. According to InssTek, this breakthrough is the result of rigorous testing, including successful combustion trials. For example, to ensure the reliability of the multi-materials, each part was produced after verification through material research using the MX-Lab, including tests on tensile strength and thermal conductivity. The hope is that the success of these parts will help open the way for tailored solutions that meet the complex demands of modern aerospace. An incredible feat from the Korean space sector that hopefully will pave the way for even more breakthroughs in the use of additive manufacturing for rocket propulsion. You can learn more about InssTek’s solutions HERE or find out more about the application at InssTek’s booth D98 in hall 12.0 at Formnext.
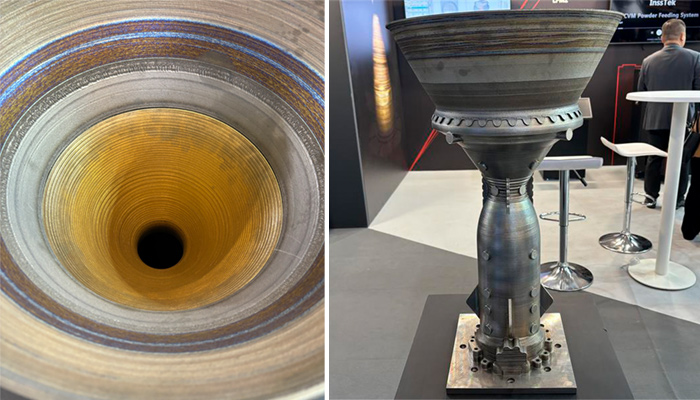
InssTek’s multi-material rocket nozzle showing the inside (left) and outside (right)
Metal 3D Printing a Premium Electric Motorcycle Bike Frame
Another application that we want to highlight at Formnext comes from Farsoon Europe. The company, which is dedicated to the development of 3D printing solutions for metals and polymers, has joined forces with Stark Future. This collaboration aims to enable the development of scalable, high-performance manufacturing solutions for the premium electric motorcycle market. A clear example of this is a complete motorcycle frame created with a titanium alloy on Farsoon’s FS721M-H-8-CAMS 3D printer, an industrial metal solution designed to meet large-format production demands. With a build volume of 720 x 420 x 650 mm and equipped with eight powerful 1000W fiber lasers, the FS721M-H-8-CAMS maximizes productivity while reducing part costs. The system also incorporates Farsoon’s Continuous Additive Manufacturing Solution (CAMS), which utilizes a unique conveyor system and interchangeable cartridge strategy to keep the printing process running continuously, minimizing downtime between builds. If you want to see this metal motorcycle part in person, feel free to visit Farsoon at Formnext, at booth E11 in hall 11.0. You can find more information at Farsoon’s website HERE.
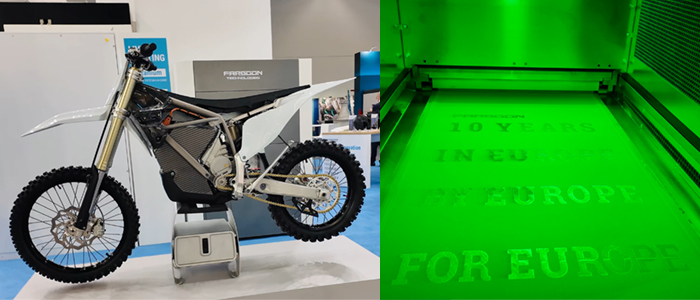
Farsoon’s 3D printed motorcycle frame (left) and its technology (right)
FIDENTIS and Its Multi-Material Metal Dentures
Additive manufacturing applications in dentistry are hardly a new phenomenon. What is a little out of the norm however is metal 3D printing in the sector. This is where FIDENTIS comes in. The startup, which spun out of Fraunhofer IGCV, has developed a multi-material laser powder bed fusion solution which is particularly well-suited to creating dentures. With this technology, there is a laser powder bed as well as a robot which is able to deposit additional materials for simultaneous processing of two or more different alloys. For this particular application, it is made of CoCr with gold fused to the friction surface. The company notes that using this process is 20x faster and 60% cheaper than traditional methods. The metal application has been so well-received that not only can attendees see the dental multi-material dentures at Fraunhofer IGCV’s booth but FIDENTIS is also a finalist in the new Rookie Award at Formnext 2024.
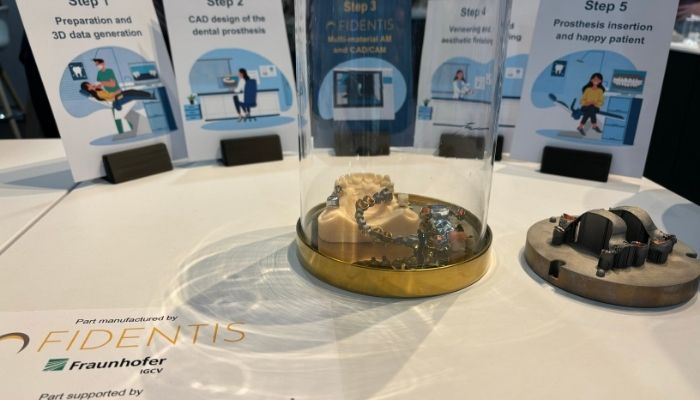
The metal dentures on display at Formnext
In-Ear Monitors for Musicians
In-ear monitors are an integral piece of technology for any musician or singer as they allow them to hear on stage. But did you know that they can not only be made from 3D printing but also from metal? At Bright Laser Technologies’ (BLT) booth, in-ear monitors made using metal AM, more specifically the BLT A160 500W metal 3D printer, are in the spotlight. Done by Earfit, which specializes in high-fidelity acoustic solutions for musicians, the 160 mm x 160 mm x 160 mm, titanium in-ear monitors have been designed to make personalized, high-quality, crystal-clear audio accessible to everything. Additive manufacturing was chosen as a way to create cost-effective, reliable and practical solutions that allow them to go even further than traditional manufacturing. Music to our ears!
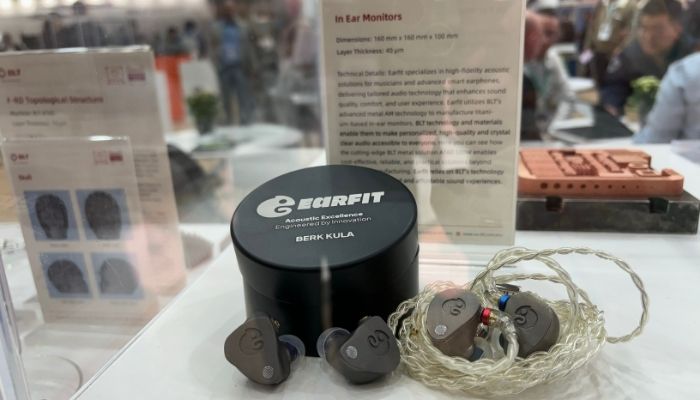
The titanium in-ear monitors at BLT’s booth
Renishaw’s Olympic-Medal Winning Bike
Paris 2024 might be over, but at Formnext you can still see one of the most exciting additive manufacturing applications coming from the event. British manufacturer Renishaw is showing the track bike, developed for British Cycling with Lotus Engineering and Hope Technology, which helped take home eight medals at the Olympics this year. And it is particularly interesting for us because it includes parts that were 3D printed using Renishaw’s RenAM 500Q in titanium. Notably, we are talking about the seat post and the crank, though smaller components such as a seat bridge and dropouts were also made. Focusing on the bike crank, it was made using Ti6Al4v and included an internal lattice structure to maintain the strength of the part while still accommodating the bike’s weight requirements. An incredible show of how 3D printing can be used to improve equipment in cycling.
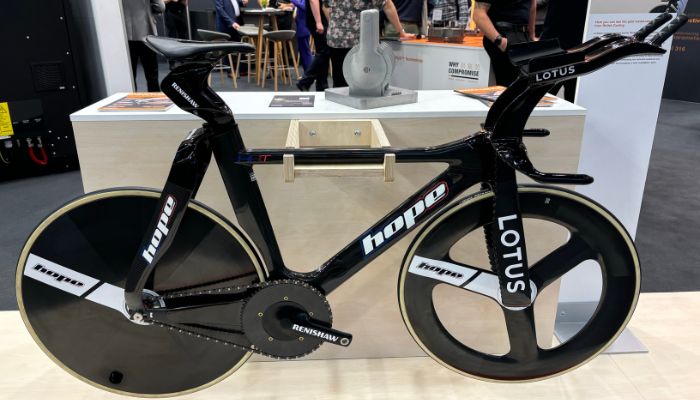
The gold-medal winning bike with the metal bike crank behind it
Finland’s Largest Metal 3D Printed Part at Formnext 2024
With the Nordic nations in the spotlight at Formnext 2023, we saw how AM is growing in the region. And now they are back with a new pavilion in Hall 11.1 at Formnext 2024 and this is where you can find a relatively remarkable application. This pressure vessel is not only Finland’s largest metal 3D print but was tested according to pressure vessel standard EN 13445-3. Remarkably, the 300 kg part was made using WAAM and acid-resistant stainless steel. The part has a diameter of 900 mm and a height of 1600 mm and in testing was able to withstand testing until a pressure of 111 bar, an incredible feat considering it was originally designed for an operating pressure of 10 bar. It is the result of cooperation between ANDRITZ Savonlinna Works Oy and the FAME ecosystem with the non-destructive and destructive tests carried out by LUT University.
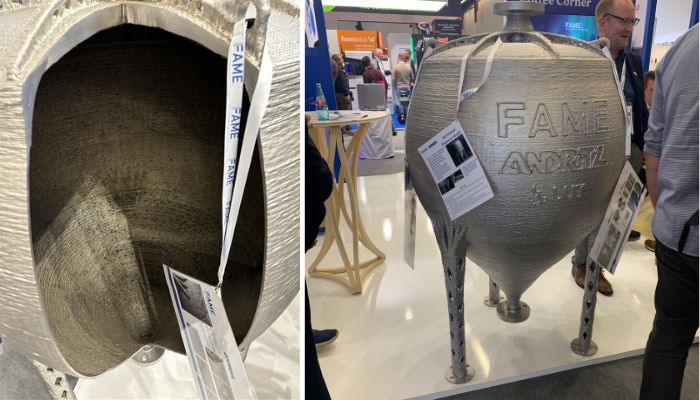
The part showing the inside (left) and outside (right)
Eplus3D and LEAP 71 Show the World’s Largest Metal-Printed Rocket Thruster
When we think of metal AM parts, the first sector that comes to mind is obviously aerospace. And there were quite a few remarkable examples at Formnext this year. Apart from the multi-material nozzle from InssTek, we were also quite impressed with this rocket thruster from Eplus3D and LEAP 71. Claimed to be the world’s largest metal 3D printed rocket thruster by the companies, the 200kN thruster was made in a single piece and stands more than 1.3 meters tall. The thruster, which is powered by cryogenic liquid oxygen and kerosene, is an advancement from the Noyron TKL-5 rocket engine that LEAP 71 successfully hot-fired in June but apparently is 40 times more powerful. It was made using AlSi10Mg, a high-performance aluminum alloy, on an Eplus3D EP-M650-1600 Metal Powder Bed Fusion printer. What is especially intriguing about this is that it was able to integrate the many different parts in a rocket thruster, the combustion chamber, nozzle, cooling channels, manifolds and structural elements into one piece. This is expected to help reduce the time needed for quality assurance, as no longer will each component need to be tested separately.
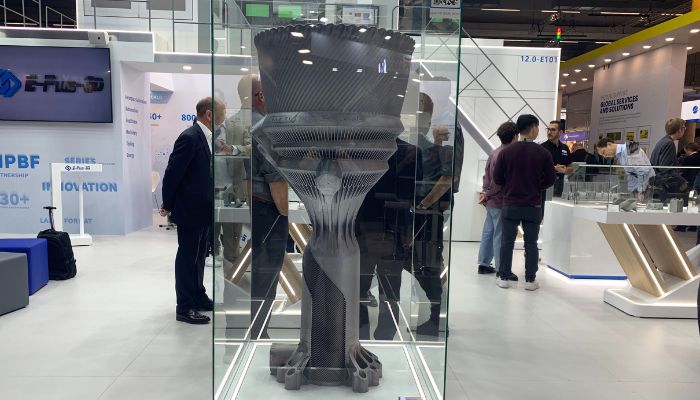
The rocket thruster on display at Formnext 2024, one of the most exciting applications we saw
A Five-Outlet Nozzle for Coke Batteries
For those who may not be well-versed in industry, a coke oven battery is a set of ovens that that process coal into coke. This fuel has a high carbon content and is important in sectors like iron ore smelting as well as fuel in stoves and forges. This piece is a specially developed five-outlet nozzle, made by ArcelorMittal and TheSteelPrinters that was designed to consolidate five single nozzles into one single component in order to decrease the amount of maintenance needed for the part. Not only was it tailor-made and reduced lead time to 3 weeks as compared to 4 months, but the material is of note. AdamIQ3167L was designed by TheSteelPrinters, a 3D metal printing service provider, which was optimized for LPBF and is starting to be commercialized. The resulting part is 8kg and measures 73 x 300 x 228 mm. You can see it at ArcelorMittal’s booth in Hall 11.0.
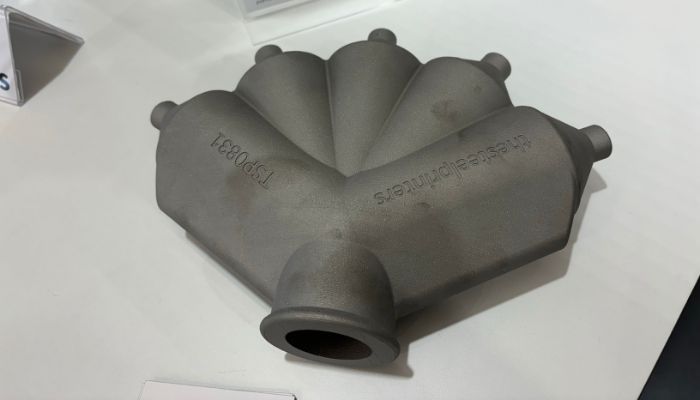
A closer look at the 5-nozzle component
What do you think of these cool metal applications at Formnext 2024? Let us know in a comment below or on our LinkedIn, Facebook, and Twitter pages! Don’t forget to sign up for our free weekly Newsletter here, the latest 3D printing news straight to your inbox! You can also find all our videos on our YouTube channel.
*All Photo Credits: 3Dnatives