The Complete Guide to Multi Jet Fusion (MJF) 3D Printing
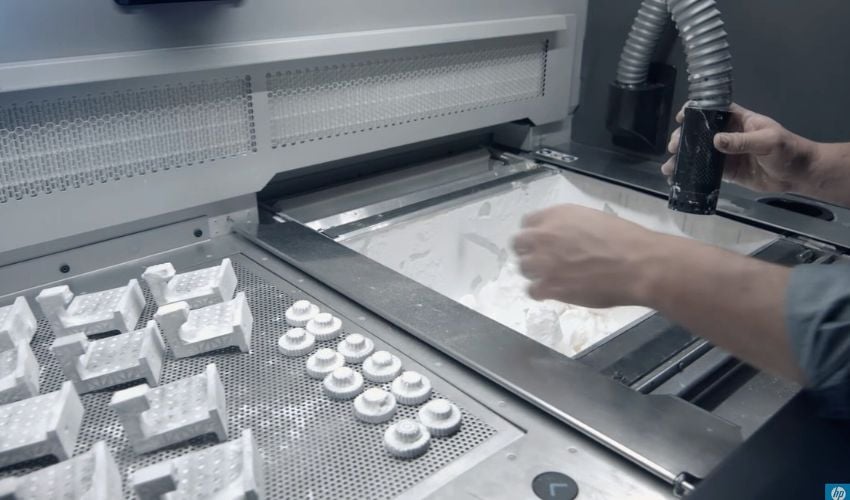
When it comes to additive manufacturing, it is safe to say that it is definitely not one size fits all. Though of course the basis of the technology, developing layer by layer, stays constant, the way of doing this certainly does not. Indeed, currently there are 7 additive manufacturing families that separate the processes: photopolymerization; material extrusion; Material Jetting; Binder Jetting; Powder Bed Fusion; Directed Energy Deposition; and sheet lamination. But sometimes there is one that does not quite fit into any of these. One notable example is Multi Jet Fusion (MJF) from HP.
Technically speaking, MJF belongs to the powder bed fusion family. This is unsurprising considering that the technology involves both a powder bed and fusing agents. But it also shares characteristics with other processes, notably Binder Jetting. We took a closer look at how the technology works, its benefits and limitations and applications.
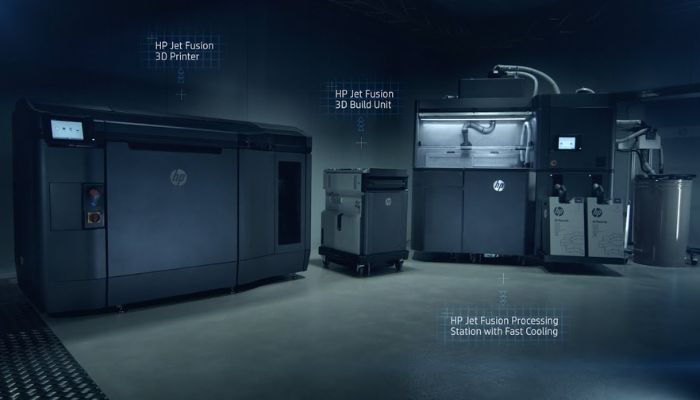
Photo Credits: HP
How Does Multi Jet Fusion Work?
But what exactly is Multi Jet Fusion? Well the technology was created by HP in 2016, building upon the company’s expertise in inkjet printing and is compatible with both rigid and elastomeric polymers. Although relatively a newcomer on the 3D printing market (to compare, stereolithography and fused deposition modeling were both developed in the early 80s and many metal AM processes started to come out in the 90s), it is relatively popular, especially when it comes to creating highly accurate and durable polymer parts.
MJF could be considered a mix in some ways between powder bed fusion and binder jetting. That is because the technology, as the name suggests, contains both jetting and fusing. It starts of course with a coating of powder which heated up to ensure consistent and accurate temperature control before being covered with the fusing agent and detailing agent in the appropriate areas to develop the layer of the part using inkjet technology. The fusing agent is the material that will be fused whereas the detailing agent helps to provide clear edges on the part for much finer details. Next, energy is applied to the layer in one go, making it significantly faster than laser-based processes which fuse point by point. Powder covered with the fusing agent is subsequently melted while the powder covered with the detailing agent remains loose, defining the exact boundaries of the part. This is repeated layer by layer until the final part is created. It should be noted that what is also different about MJF is that new material and agent layers are placed while the previous layers are still molten, allowing both to fuse completing and improving durability and the finer details in a part.
After the printing, parts made with MJF require post-processing, notably the elimination of the loose powder surrounding the part. This loose powder however eliminates the need for support structures, the same as with SLS and Binder Jetting, meaning that support removal is not required. The part is removed to a separate processing station, part of HP’s MJF solutions, which allows for the loose unfused powder to be vacuumed up, or bead blasted, and reused. There are also many other post-processing steps that are possible to augment the characteristics of the part or to smooth surfaces.
Right now, the technology is proprietary only to HP. The company has two currently available MJF solutions: HP Jet Fusion 4200 and HP Jet Fusion 5200. Moreover, it is only currently compatible with polymers, namely TPU, PP, TPU, PA11, PA12 and PA12 with glass beads.
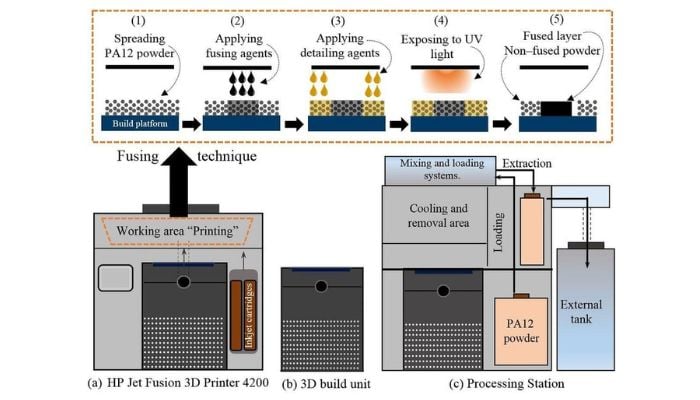
A schematic of the Multi Jet Fusion (MJF) process including the build unit and processing unit (photo credits: Amer Alomarah via ResearchGate)
Benefits and Limitations of MJF
But what exactly are the pros and cons of using MJF? Well, if we look at the downsides first, one of the biggest is that the initial printer investment is expensive. Given that only one company offers Multi Jet Fusion solutions, there are no cheaper options out on the market. The HP Jet Fusion 4200 has a starting price of over $200,000 while the HP Jet Fusion 5200 starts at around $350,000. Over time, the parts certainly become much more cost-effective, but that initial investment cannot be ignored.
Another significant drawback is that the technology is still relatively limited in terms of material choice, though it has expanded greatly since 2016. Right now, HP has seven compatible materials for its machines though they are not all compatible with both solutions. For the HP Jet Fusion 4200, the machine is compatible with Estane® 3D PU M95A, TPA, PA11, PA12 and PA12 Glass Beads. Meanwhile, the HP Jet Fusion 5200 is compatible with the latter three materials as well as PP and BASF Ultrasint® TPU01. The materials vary greatly and allow for a wide variety of applications and characteristics of course, but still compared to many other AM technologies, it is limiting.
Some final drawbacks include the fact that the final product is gray without dying agents and slightly rough (though white parts are also now available), making it likely that users will need additional post-processing steps. This in and of itself can cause small raised text and cosmetic parts to be lost. The technology is also unable to produce some curved, hollow geometries.
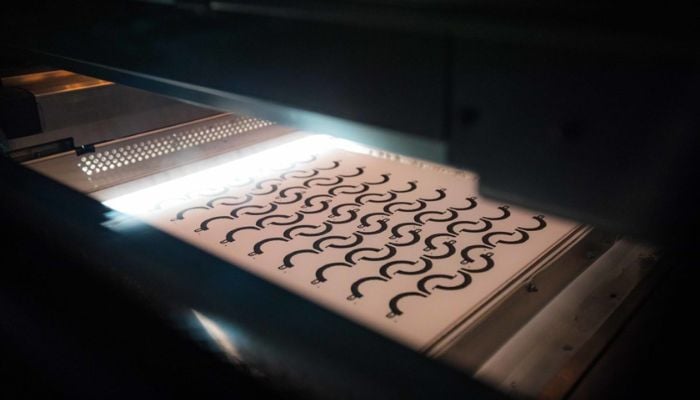
Parts being created by MJF (photo credits: Hubs)
It also has a number of significant benefits however. Similar to binder jetting, HP Multi Jet Fusion has a fast printing speed and production cycle thanks to its use of inkjet technology as well as the ability to print many parts at once. It is capable of producing parts at speed without negatively affecting quality, making it popular for everything from prototyping to end-use parts.
Isotropy in the final parts is one of the major advantages of Multi Jet Fusion. Defined as the property of being identical, or having the same physical properties, in all directions, isotropy is not necessary for all 3D printed parts but is critical for those needing to be able to carry loads or force in all directions. For this reason, MJF is understandably popular among users who need parts with consistent isotropic mechanical properties.
Additionally, despite some limits, there is generally great design freedom with MJF thanks to the fact that supports are not necessary. It also has a high rate of powder recycling, especially compared to other powder bed fusion processes, up to 80 to 85% depending on material. It is also highly accurate. HP MJF’s voxel by voxel production in particular allows for very fine details for parts.There is also a high-quality surface finish, especially after additional post-processing.
Applications of the Technology
Given the numerous benefits of Multi Jet Fusion 3D printing, it stands to reason that it has a number of applications in sectors. And that is certainly the case. Even with material limitations, MJF is being used in sectors as vast as industry, medical, automotive and consumer goods, among others.
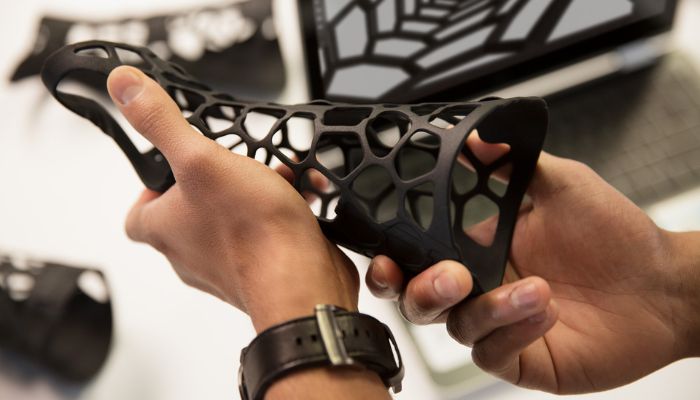
MJF can be used in a variety of sectors including medical, as this orthotic shows (photo credits: Invent Medical)
And MJF is still growing. HP is continuously bettering the technology, introducing new materials and improving processes for an even more streamlined, effective production process. For now, it remains one of the most popular processes and is likely to remain so at least for the near future. Furthermore, HP recently unveiled its own metal 3D printing process, HP Metal Jet, as the company moves into even more applications. You can learn more about it on HP’s website HERE.
What do you think of Multi Jet Fusion? Do you use it? Let us know in a comment below or on our Linkedin, Facebook, and Twitter pages! Don’t forget to sign up for our free weekly Newsletter here, the latest 3D printing news straight to your inbox! You can also find all our videos on our YouTube channel.
*Cover Photo Credits: HP