Tethon 3D: A Behind-the-Scenes Look at Resin Development
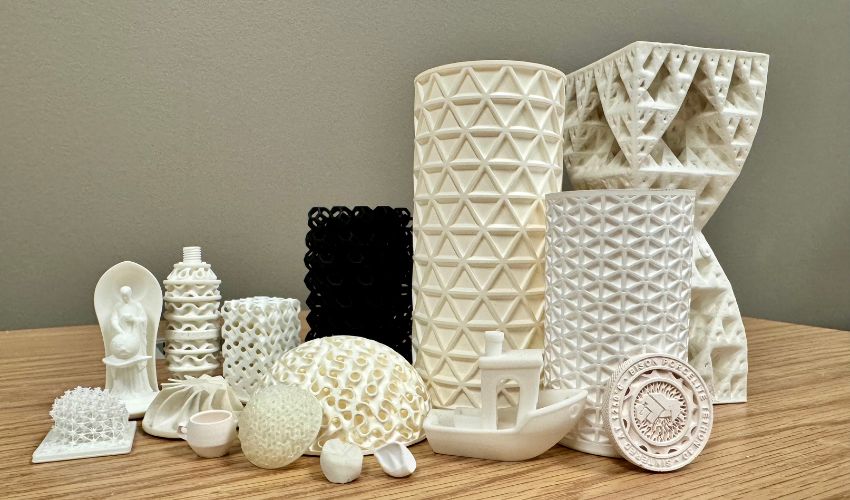
When you purchase resin for vat photopolymerization, do you ever think about where that resin came from? Even if there’s a brand name on the label that coincides with the printer you are using, there is a chance that the resin was actually developed by a different manufacturer—perhaps a company like Tethon 3D. Tethon 3D is a ceramic additive manufacturing company that develops composite resins and hardware, with a focus on material development. The Nebraska-based business is named Tethon for the Native American Omaha tribe word for white buffalo. In Omaha Native culture, the white buffalo symbolizes strength, rarity and earthly connection. Tethon 3D, with its recognizable white buffalo logo, seeks to produce ceramic 3D printing technology with the same qualities.
Stepping into the Tethon 3D offices, you see printers from several well-known brands like Stratasys, Formlabs and Nano Dimension, as well as Tethon 3D’s proprietary printer, the Bison 1000. Why all the printers? The lab at Tethon 3D makes custom resins to be resold by such brands like Stratasys and Fortify, as well as custom materials for research labs and government and military projects. While rooted in Omaha, the company has clients and partners across the US, Asia and Europe. Since its founding in 2014, it has provided over 1,700 customers in over 40 countries with solutions for ceramic additive manufacturing.
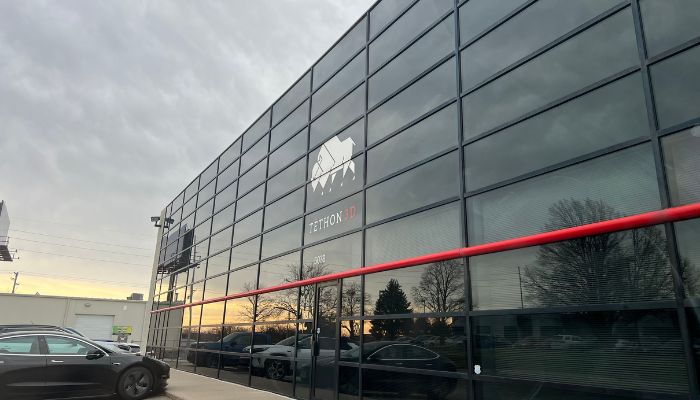
Tethon 3D’s office in Omaha, Nebraska (Photo Credits Julia Steiner)
Tethon 3D was founded by husband and wife Karen and Jim Linder, who both have medical backgrounds. One night, the two attended a lecture from a Bowling Green State University (BGSU) professor who was researching ceramic 3D printing. Their initial thought was that 3D printed ceramics could have useful medical applications. As it turned out, the professor had been looking for an avenue to commercialize his research while still being able to teach. Karen and Jim had previously founded other companies and had funded over thirty startup companies with their angel investment company Linseed Capital. So, they negotiated with BGSU to acquire the invention’s intellectual property and founded Tethon 3D as a materials company.
Initially, they focused on binder jetting powders, binder and 3D print services, but now, UV resins and hardware are their primary products. CEO Trent Allen explained that in around 2016, when Autodesk’s Ember and Formlabs were growing in popularity, the Tethon 3D team realized that the resin market had fewer barriers to entry, so they expanded to ceramic resins. The company specializes in mixing and compounding raw materials to create proprietary resins. Tethon does not produce raw materials, but they have relationships with suppliers who provide high-performance ceramics like alumina and zirconia, focusing on strength and production readiness.
Genesis: A Base Resin
Tethon 3D’s flagship products include the line of Genesis resins, which are base resins that serve as a starting point for researchers looking to create custom materials. These resins can be mixed with powders, including metals and pigments, to meet specific needs. The resulting custom printable resin can be used for final-part production as well as research, so once someone achieves the formula they desire, they could continue to use it to produce parts.
Tethon 3D providing materials designed for experimentation feels true to the nature of the 3D printing community, where research and development teams account for a large part of the technology’s user base. “It is really rewarding to see people take the research to the next level,” Allen said, referring to Genesis. These resins have a variety of possible applications, including automotive, aerospace, dentistry, biotech and jewelry.
Bison 1000
While materials are currently Tethon 3D’s focus, the team also created a proprietary 3D printer through the South Korean brand Carima because they recognized a gap in the market. Around 2020, the time of the printer’s release, there were no desktop ceramic 3D printers on the market, and many of the DLP printers available were made for plastics, not ceramics. Previously, Autodesk’s Ember 3D printer, which was released in 2014 and discontinued in 2017, had been a popular desktop DLP solution, but it was no longer available; it posed a problem that Tethon 3D could solve.
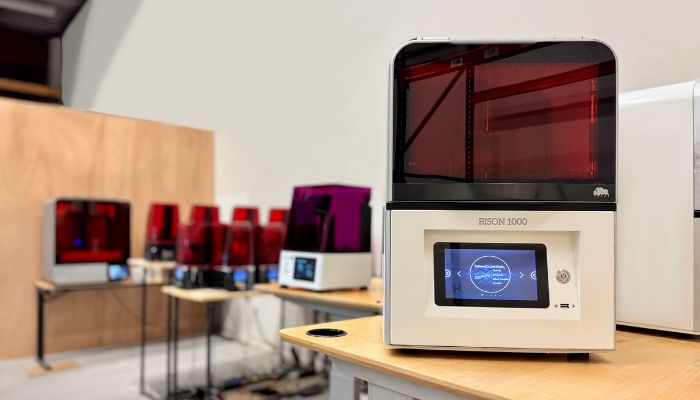
The Bison 1000 3D Printer (Photo Credits: Tethon 3D)
“There were a lot of companies sending us powders to develop materials, and we were limited by machines that were locked down,” Allen said. “So, we really wanted to develop a machine that was the best for material development and our team, and that’s what ended up as the Bison 1000.” The DLP printer has fully adjustable settings (the dosage, exposure times and intensities can be changed), making it ideal for research in government, military and high-level academic labs. Since unveiling the Bison 1000, the company has released three new 3D printer models that are more geared towards ceramic part production.
Tethon 3D Going Forward
In the next few years, one of the areas the company plans to target is dental implants. “Today, people are 3D printing composite crowns, but they’re generally pretty weak,” Allen explained. “They’re used generally for temporary crowns, and we believe our materials will eventually be a good option for permanent crowns.” He added that he believes his company is close to having a material optimized for that application. “All of our dental materials have passed cytotoxicity testing, but we would still need to go through the FDA process. That’s going to be the biggest slowdown.”
However, deciding on areas to focus on is not always easy. One of the challenges of directing the business, Karen Linder explained, is defining their direction. “Ceramics are everywhere,” Karen said. “As a company, it is almost distracting—it is hard to focus sometimes when a lot of different industries need material.” From NASA experiments to Harvard and MIT research labs, Tethon 3D materials have been everywhere. “We’ve had our material on the International Space Station as well as underwater.,” Karen added. “MIT did a really nice research study using our material for a satellite sensor.”
In keeping with the rhythm of the industry, Tethon 3D plans to expand its hardware platforms and develop those that are geared more toward production. As additive manufacturing becomes more widely adopted across industries, the need for custom materials designed for specific applications will rise, and companies like Tethon 3D are answering the call.
What do you think of Tethon 3D’s mission? Let us know in a comment below or on our LinkedIn, Facebook, and Twitter pages! Don’t forget to sign up for our free weekly Newsletter here, the latest 3D printing news straight to your inbox! You can also find all our videos on our YouTube channel.
*Cover Photo: Ceramic 3D printed objects. (Photo credit: Tethon 3D)