Technical Ceramics in Additive Manufacturing
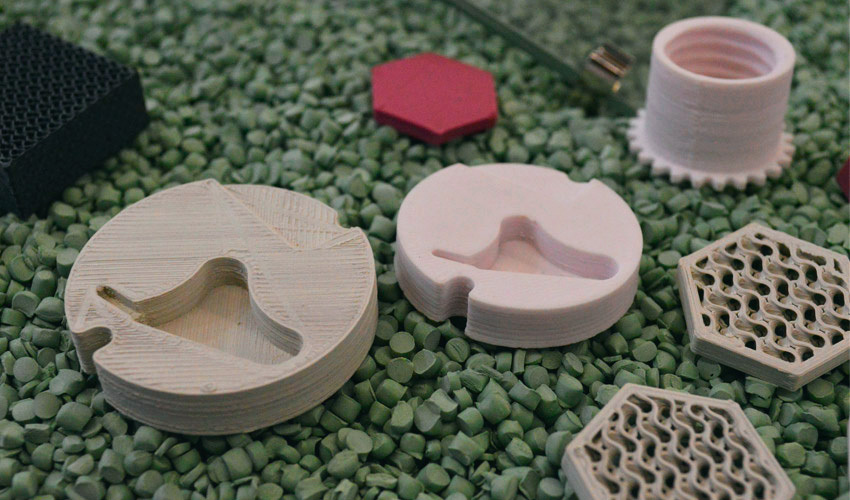
Technical ceramics, as opposed to artisanal or artistic ceramics, are materials that have been used for centuries in many industrial sectors. They are renowned for their temperature resistance, hardness and mechanical properties. In the additive manufacturing sector, ceramics are less popular than polymers or metals and remain a niche market, although 3D technologies are a particularly interesting fit for the materials. Indeed, due to their characteristics, technical ceramics are difficult materials to shape and additive manufacturing represents a relevant alternative in the creation of complex geometries. Currently compatible with photopolymerization, powder bed and extrusion processes, ceramics offer multiple advantages to manufacturers, laboratories and research centers. Among them, the Research Center of the Belgian Ceramic Industry (CRIBC), which has relied on several 3D printing processes, including that of the French manufacturer Pollen AM.
For the past twenty years, CRIBC has invested in additive manufacturing to be able to manufacture parts with complex geometries. Indeed, technical ceramics are fragile and refractory materials and therefore intrinsically difficult to shape. When it comes to creating complex geometries using conventional processes, lead times are extended and the cost of a part is strongly impacted. The promise of additive manufacturing lies precisely in overcoming this pitfall: to offer complex geometries while preserving the properties of ceramics, whatever the material used.
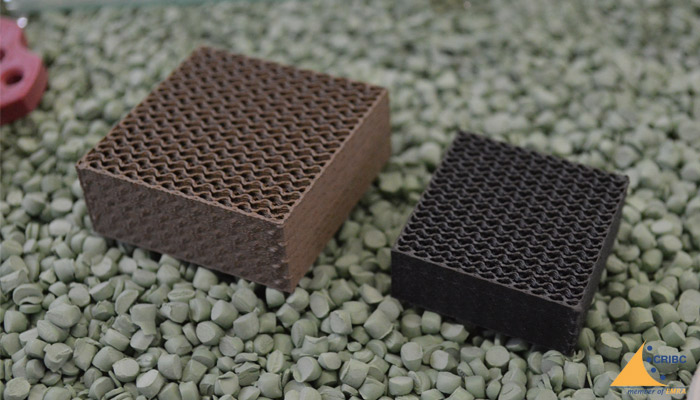
Ceramics are difficult materials to shape. Thanks to additive manufacturing, complex geometries can be imagined (photo credits: 3Dnatives)
Technical Ceramics on the Market
There is currently a very diverse range of technical ceramics that can meet various markets and needs. The family most used in additive manufacturing is undoubtedly oxidized ceramics which, as their name indicates, are composed of metal oxide such as alumina or zirconia. They are used in the medical sector for to make bone implants as well as in the field of watchmaking. Next come the non-oxidized ceramics with nitride materials that combine good mechanical performance and temperature resistance, and carbides that are excessively hard and often used for their tribological resistance. Silicon carbide, for example, is three times harder than steel.
In additive manufacturing, manufacturers can use different technological approaches to design their parts, but they are not all compatible with all families of ceramics. CRIBC tested several ceramic 3D printing processes and was able to compare the quality of the parts obtained, their characteristics and performance. Fabrice Petit, Program Manager Manufacturing Processes at CRIBC, explains: “There are many additive technologies for ceramics, but none of them supersedes the others. The choice will be made according to the desired application. Stereolithography, for example, will be ideal for small parts with little opening and low mass. Powder bonding allows the design of large but very porous parts, so its use is rather limited. In my opinion, extrusion processes remain the most interesting, and particularly Pollen AM’s technology because it relies on materials in the form of granules that are found in the injection molding industry. It’s an open machine that reduces the cost of materials and opens up the field of possibilities.”
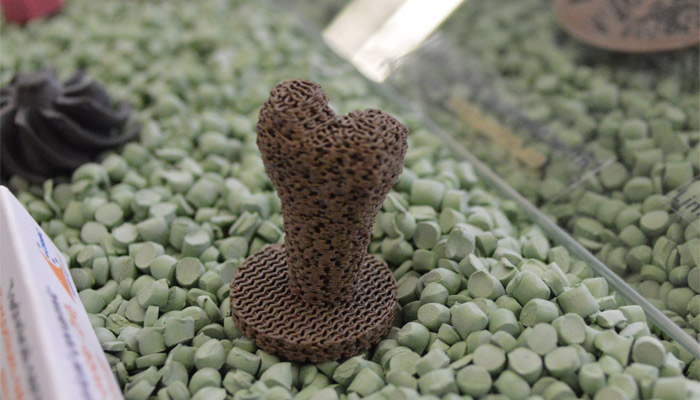
Example of a 3D printed part in zirconia by the CRIBC on a Pollen AM machine (photo credits: 3Dnatives)
The Choice of Pollen AM Technology
CRIBC is working primarily on oxides with Pollen AM technology, although it is beginning to use nitrides to meet temperature requirements. It also has plans to test carbides, including tungsten carbide. The research center is evaluating the technology and characteristics of the parts, whether they are lattice structures, nitride micro-turbines, tungsten carbide cutting tools, etc. And the result is satisfactory: Pollen AM’s extrusion process produces quality parts with very good surface finishes that can be mechanically stressed.
This is often the challenge of ceramic additive manufacturing: it is necessary to pay attention to the porosity of the parts because if it is too high, the mechanical performance will be insufficient. The surface condition is a key point because if it is degraded, it will lead to cracks and therefore a part that will break after stress. In any case, Fabrice Petit expands, “Ceramic additive manufacturing offers, like all 3D technologies, a greater freedom of design. I think this is even more relevant with ceramics because of their characteristics and properties.”
Finally, Pollen AM’s extrusion process has the advantage of being cleaner and more convenient than other ceramic 3D printing technologies. Powder bed processes, for example, present a health risk for the operators, especially for their respiratory tract, but also require a certain installation in the working environment; Pollen AM’s machine can be used in a closed office. Fabrice Petit concludes. “From a practical point of view, PAM technology has serious advantages over other technologies. Add to that the material compatibility, their cost and the quality of the resulting parts, it is an ideal ceramic additive manufacturing technology.” You can find more information about engineered ceramics and PAM technology HERE.
Do you use technical ceramics in additive manufacturing? Let us know in a comment below or on our Linkedin, Facebook, and Twitter pages! Don’t forget to sign up for our free weekly Newsletter here, the latest 3D printing news straight to your inbox! You can also find all our videos on our YouTube channel.