What Technical Ceramics Are Compatible With Additive Manufacturing?
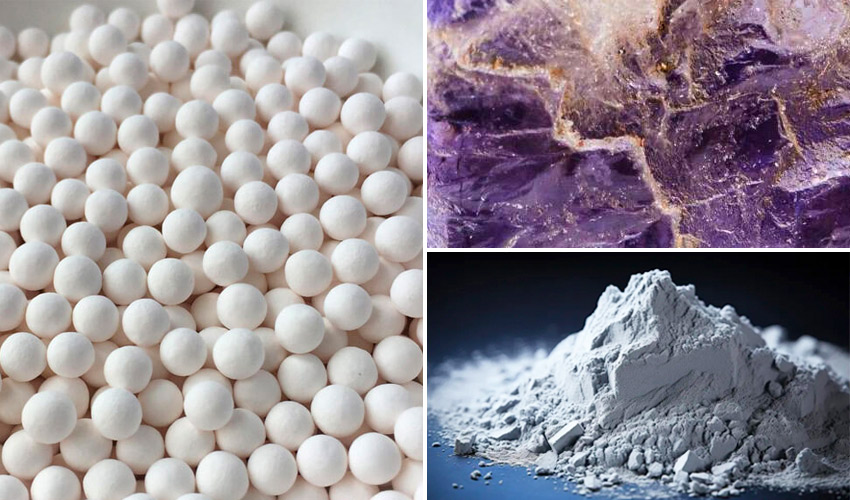
Though the first thing that comes to mind for many when you mention ceramics is pottery or porcelain, technical ceramics are actually some of the strongest and toughest materials on Earth. Broken into two categories, oxides and non-oxides, the main difference between them is that an oxide contains at least one oxygen atom along with another element, giving it different properties. Notably, non-oxide ceramics often have better electrical conductivity and a higher degree of hardness while oxide ceramics are easier to melt and sinter, making it easier to use in manufacturing. And it should come as no surprise that it is possible to use these technical ceramics in additive manufacturing in several forms including filaments, powder and resin. In the following listing, we take a closer look at which technical ceramics are compatible with 3D printing, excluding other commonly used ceramic materials like clay, as the materials in conjunction with 3D technologies are increasingly used for applications in everything from aerospace and defense to automotive and even the biomedical field.
Oxide Ceramics
Alumina
Alumina, which is one of the technical ceramics compatible with additive manufacturing, is suitable for a wide range of applications. With a melting temperature above 2000°C, it is highly resistant to high temperatures and thermal shock. Alumina is also often chosen for its remarkable hardness, placing it just behind diamond as the hardest natural material. It is also appreciated for its resistance to corrosion, high temperatures, electrical insulation, thermal conduction and biocompatibility. It is used in major applications such as electronics (insulators), biomedical prostheses, cutting tools and aerospace.
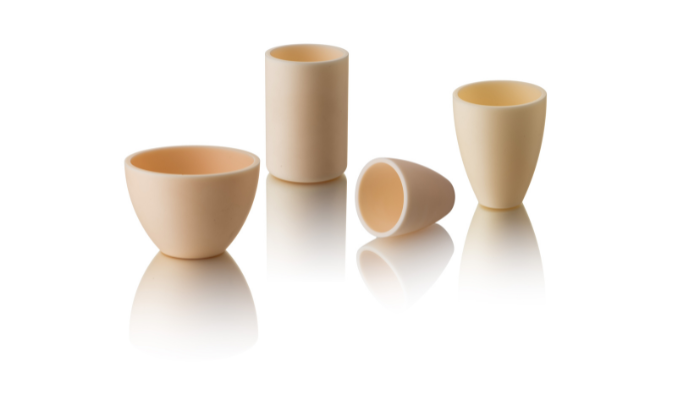
Photo Credits: Umicore
Zirconia
Zirconium oxide, also known as zirconia, boasts outstanding mechanical properties at both low and high temperatures. With its relatively low thermal conductivity at room temperature, this material displays remarkable qualities when exposed to extreme conditions. At temperatures in excess of 1000°C, zirconia becomes an excellent electrical conductor. Its high hardness, wear resistance, chemical inertness and ability to resist attack by metals make it a material of choice for a wide range of applications, including jewelry, biomedical devices, biomedical implants (especially dental implants) and electronic equipment.
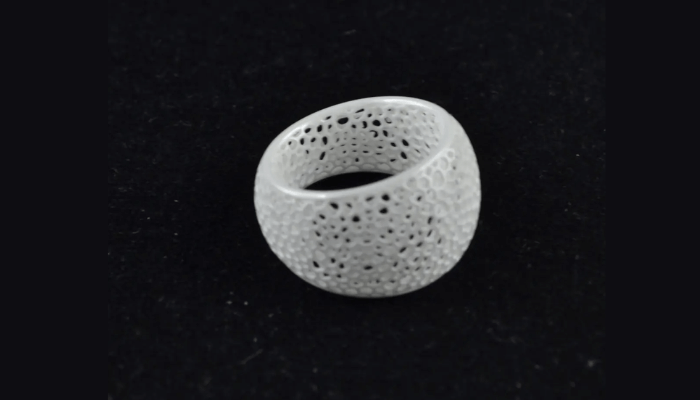
Photo Credits: 3DCeram
Silicore
Another ceramic material used in additive manufacturing is silicore. Designed specifically for foundry cores, silicore’s main component is silicon dioxide. Its porosity is one of its major assets, significantly simplifying the removal of complex structures from castings and facilitating washing. What’s more, this ceramic offers outstanding mechanical strength and robustness in the face of stress. Silicore can be used with virtually all alloys, except for those containing cobalt, and stands out for its stability, even at very high temperatures.
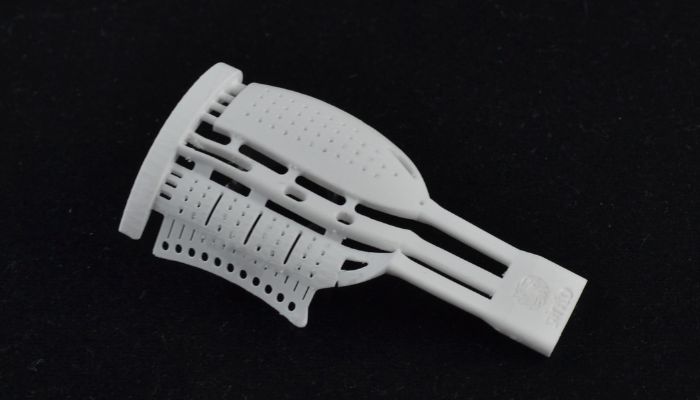
Photo Credits: 3DCeram
Cordierite
Cordierite, also known as iolite, is a magnesium iron aluminum cyclosilicate (meaning silicate minerals which is made up of silicon dioxide). Cordierite technical ceramics are mainly used in the aerospace industry for optical parts, but also in electrical heating technology, including in sectors adopting additive manufacturing. For example, the insulating bodies of electric instantaneous water heaters, the heating conductor supports or the inserts of gas burners are made from cordierite. They have a low coefficient of expansion and are therefore highly resistant to temperature variations. Cordierite is also wear-resistant, has good mechanical strength and low thermal conductivity. A distinction is made between porous and dense cordierite. Compared to the dense version, porous cordierite has lower flexural strength, but higher thermal shock resistance.
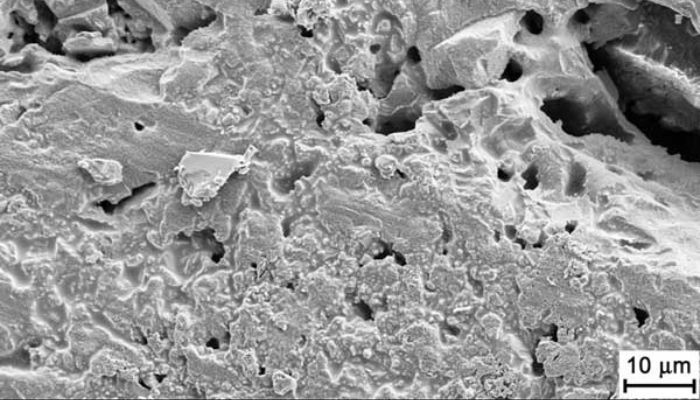
Photo Credits: Keramikverband
Hydroxyapatite
Hydroxyapatite can be considered a bioceramic material. It is a mineral belonging to the apatite family, which is also one of the main components of bone. It is used in 3D printing, and with other technologies, in the biomedical sector for bone reconstruction. Hydroxyapatite is also a bioactive material, i.e. it is capable of forming direct chemical bonds with the bone and soft tissues of living organisms. This makes it particularly interesting because hydroxyapatite implants are absorbable, meaning they do not need to be removed from the body after implantation. Hydroxyapatite 3D printing is mainly used in the production of cranial, spinal and orthopedic implants, among others.
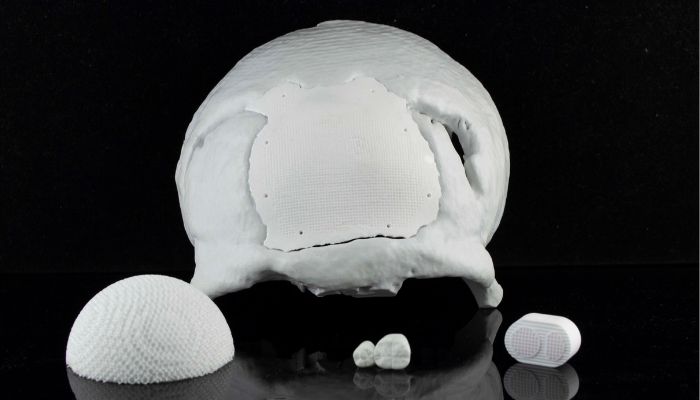
Photo Credits: 3DCeram
Alumina-Reinforced Zirconia
Alumina, also known as aluminum oxide, plays a major role in the composition of clays and enamels. On the other hand, zirconia, often considered diamond’s little sister due to its similar properties, stands out as a particularly resistant gemstone. Thus, the combination of hardened alumina and zirconia creates an exceptional ceramic material, with both industrial and biomedical applications. Alumina-reinforced zirconia is particularly well-suited to the biomedical sector, especially dentistry, thanks to its remarkable hardness and toughness measured on the Mohs scale. Its high biocompatibility as well as thermal shock and wear resistance make it an ideal choice for dental applications such as oral implants, dental parts and other components.
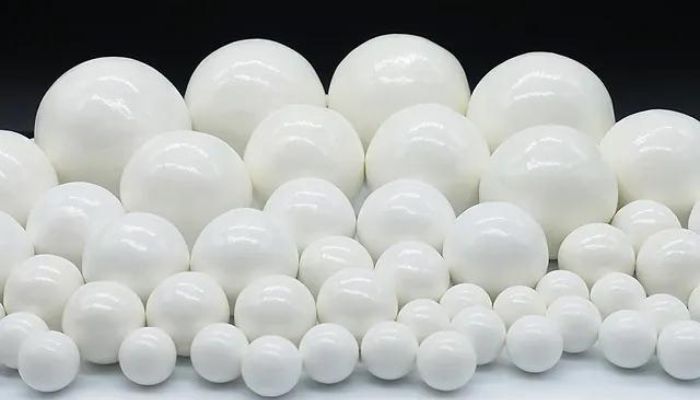
Photo Credits: CHEMCO
Non Oxide Ceramics
Boron Carbide
Boron carbide (B4C) is a material renowned for its hardness; it is one of the hardest materials in the world, after diamond and cubic boron nitride. This ceramic has excellent resistance to wear, compression and heat, low density and low thermal conductivity. It is mainly used for aerospace applications (manufacture of nozzles), nuclear applications or in the production of armor equipment such as bulletproof vests or tanks. In additive manufacturing, it is not the most widely used ceramic, but it can be found as a filament – wherein boron carbide is actually mixed with a polymer – as well as a powder.
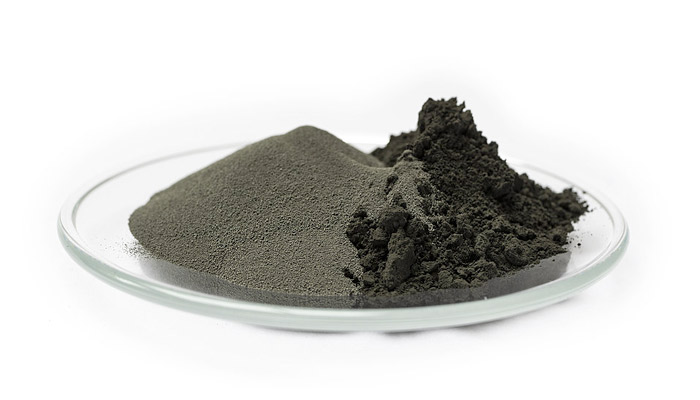
Photo Credits: Fiven
Silicon Nitride
Silicon nitride is one of the most interesting technical ceramics for additive manufacturing. It is a ceramic that can be found naturally in the form of a mineral (nierite, found in certain meteorites). It can also be obtained by heating silicon powder in a nitrogen atmosphere up to 1400°C. In terms of properties, silicon nitride is highly resistant to abrasion, corrosion and cracking. As well as being an ideal material for creating lightweight, dimensionally stable parts, it is a good electrical insulator and has low wettability (a physical property chracterizing the ability of a liquid droplet to maintain or spread on a solid surface) to molten metals. Used in conjunction with additive manufacturing, this technical ceramic enables a wide variety of uses in a multitude of industries. Among its most striking applications are the creation of semiconductors, valve and pump components, and heating pipes.
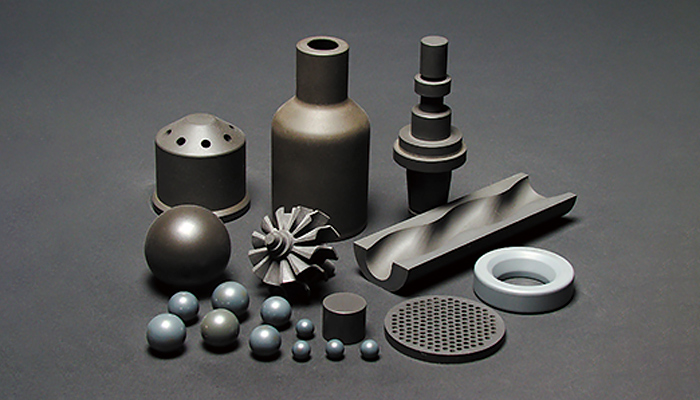
Photo Credits: UBE Corporation
Aluminum Nitride
Aluminum nitride (AlN) is a chemical combination of aluminum and nitrogen. Its properties include high thermal conductivity, efficient electrical insulation and appreciable mechanical strength. These characteristics make it a preferred choice in the electronics industry, particularly in microelectronics. Aluminum nitride is frequently used in semiconductor construction, and as a heat sink in LED technology. An additional advantage is its resistance to plasma, and it is safe to use during processing.
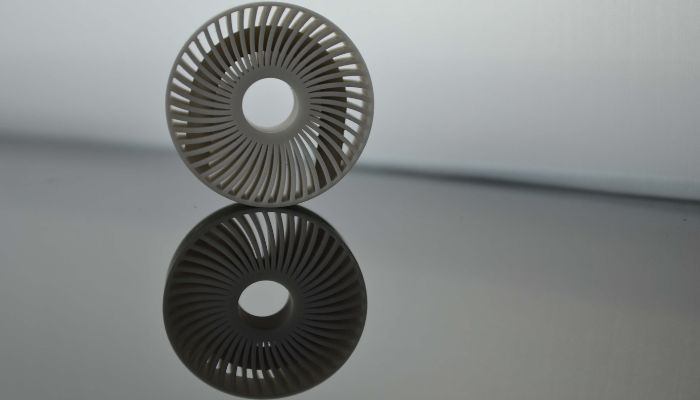
Photo Credits: 3DCeram
Silicon Carbide
Silicon carbide, also known as carborundum, is an extremely resistant chemical compound. Although its composition is similar to that of diamond, which might seem unlikely given the size differences between carbon (C) and silicon (Si) in this compound, there is a diverse range of silicon carbide derivatives. Some are sintered or recrystallized, yet they share common properties that make them remarkable technical ceramics, including for additive manufacturing. These ceramics are distinguished by their excellent resistance to thermal shock and wear, despite their high thermal conductivity. Combined with their exceptional corrosion resistance, high hardness and high-temperature mechanical properties, silicon carbide is an ideal composite for the automotive and energy industries. Key applications include the manufacture of parts for heating systems, electric vehicles and electric vehicle charging stations including with additive manufacturing.
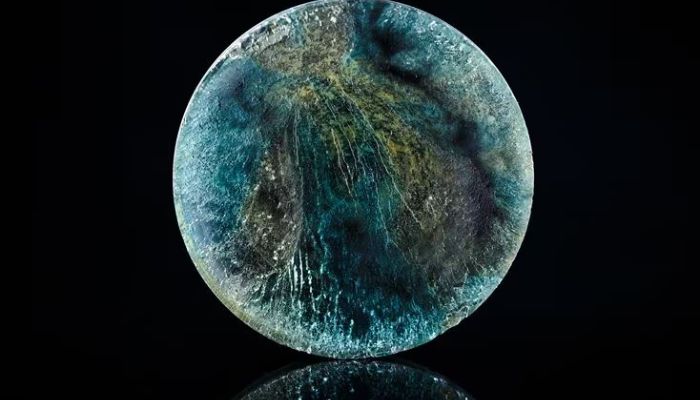
Photo Credits: Arrow.com
What do you think of the different technical ceramics which can be used in additive manufacturing? Let us know in a comment below or on our Linkedin, Facebook, and Twitter pages! Don’t forget to sign up for our free weekly Newsletter here, the latest 3D printing news straight to your inbox! You can also find all our videos on our YouTube channel.