GE, COBOD and LafargeHolcim create taller wind turbines using concrete 3D printing
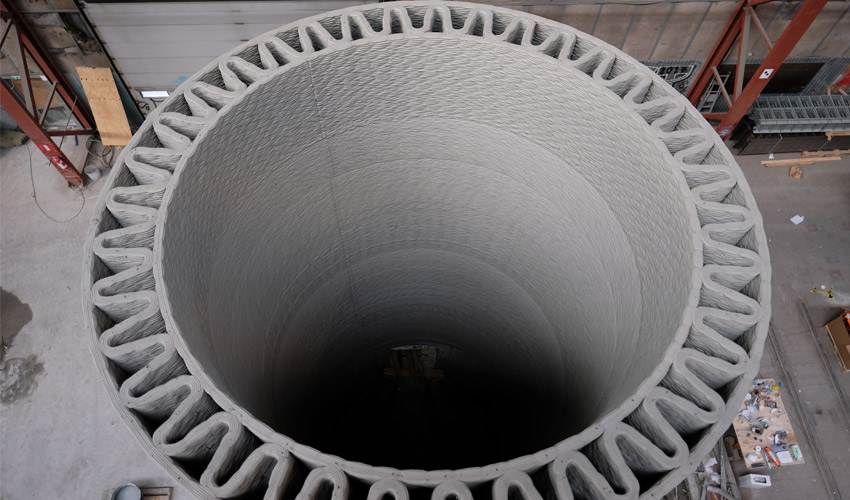
GE, COBOD and LafargeHolcim worked together to develop a 3D printed concrete base to support larger wind turbines, capable of reaching 200 meters in height to capture stronger winds, and therefore offer more efficiency. The goal of the partnership is to boost global renewable energy production while lowering the cost of energy. A fine example of the potential of concrete 3D printing!
Today, the majority of wind turbines are generally no more than 100 metres high, limited by the 4.5 metre base diameter. Indeed, not everything that is wider can be transported by road, and if it can it is quite expensive to do so. This poses a number of constraints for the construction of wind turbines. As you know, additive manufacturing makes it possible to reinvent the supply chain, removing logistical limitations, since local manufacturing is preferred. Thanks to 3D technologies, companies are no longer dependent on transportation constraints, and can produce what they want at any time. The case of wind turbines is no different: concrete 3D printing makes it possible to design the base of the device directly on site, thus offering the possibility of enlarging its diameter and height.
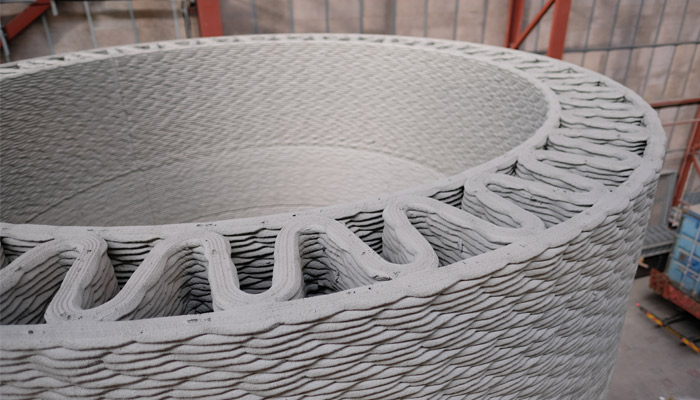
The partners used 3D concrete printing to design taller wind turbines | Credits: GE
But why increase the height of a wind turbine? It is important to know that a 5 MW wind turbine of 80 m height generally produces 15.1 GWh per year. By increasing the height of the same wind turbine to 160 m, it could produce 20.2 GWh per year, an extra 33%. This increase in height can therefore generate more energy, while concrete 3D printing lowers manufacturing costs. Matteo Bellucci, Head of Advanced Manufacturing Technologies for GE Renewable Energy, explains: “3D printing is in GE’s DNA and we believe that additive large format manufacturing will revolutionise the wind industry. Concrete 3D printing has progressed significantly over the last five years and we believe it is moving closer to a real application in the industrial world. We are committed to taking full advantage of this technology both for the design flexibility it allows and for the logistical simplification it offers on such massive components“.
It is for these reasons that GE, LafargeHolcim and COBOD printed a first prototype last October in Copenhagen. GE Renewable Energy contributed its expertise in the design, manufacture and marketing of the turbines, COBOD masters the robotics and printing part, and LafargeHolcim is involved in the production of custom concrete. The three partners explain that they want to print concrete bases from 10 to 80 metres high in order to add the 200-metre steel wind turbine.
Edelio Bermejo, R&D Director at LafargeHolcim, concludes: “3D printing on concrete is a very promising technology for us, as its incredible design flexibility expands the range of construction possibilities. As a user and promoter of clean energy, we are delighted to put our expertise in materials and design to work on this revolutionary project, which will enable large wind turbine towers to be built at lower cost and accelerate access to renewable energy. “The full press release can be found HERE.
What do you think of this collaboration to promote renewable energies? Let us know in a comment below or on our Facebook and Twitter pages! Sign up for our free weekly Newsletter, all the latest news in 3D printing straight to your inbox!