Syqe Medical, a 3D printed medical cannabis inhaler
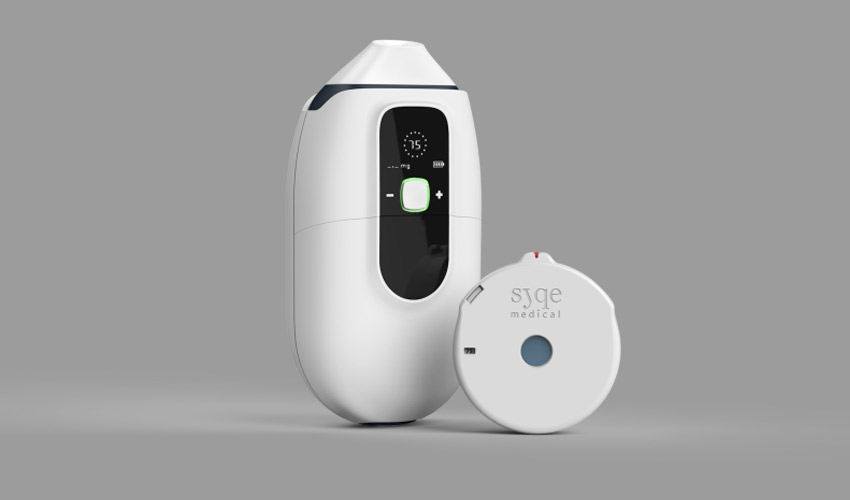
Syqe Medical is a young Israeli company that has developed a 3D printed cannabis inhaler to offer a tailor-made pharmaceutical treatment. This tool transforms the plant in order to meet the pharmaceutical requirements of the market and thus offer patients the dose they need to treat themselves. Thanks to a system of pre-loaded cartridges, the inhaler offers a selective dosage with an accuracy of 100 micrograms according to the needs of the user. The different parts of this medical solution were printed in 3D, allowing the startup to accelerate the product design phase and its launch on the market. We met Itay Kurgan, product manager at Syqe Medical to learn more about this pharmaceutical device and understand the impact of additive manufacturing on this sector.
3DN: Can you introduce yourself and your link to 3D printing?
My name is Itay Kurgan, I am a product manager at Syqe Medical. I have professional experience in industrial design and have been working with 3D printers since 2010, when I was a student at HIT. (Holon Institute of Technology).

3D printing allows to accelerate the manufacturing of the final product
When 3D printers were first introduced to us in a CAD course, we were told that CAD software was not used to design but to execute our designs and that 3D printers were not manufacturing tools, but prototyping tools at most. I was quite intrigued and always found excuses to try to use these printers in my projects over the next three years.
Towards the end of my studies, I was offered a position at Syqe Medical as an industrial designer. I took this opportunity to present Stratasys 3D printers, which was then a company of 5 employees with very limited funding. Syqe Medical made good use of these printers and very quickly, my final project was our first cannabis inhaler, a significant part of which was printed in 3D. Today, I am in charge of accelerating Syqe’s research and development processes, a mission that I could not accomplish without 3D printers.
3DN: How did the idea of creating Syqe Medical come about?
Perry Davidson, founder of Syqe Medical, sought to solve one of the biggest challenges in the industry: transforming a plant into an inhaled pharmaceutical product, with the safety and precision expected from these products.
He explains: “I founded Syqe because I was frustrated to see that a pharmaceutical company was not able to transform cannabis into a traditional treatment that could help as many patients as possible. So we decided to take up the challenge ourselves. “Syqe Inhaler is the first platform for the administration of whole herbal drugs that meets pharmaceutical standards.
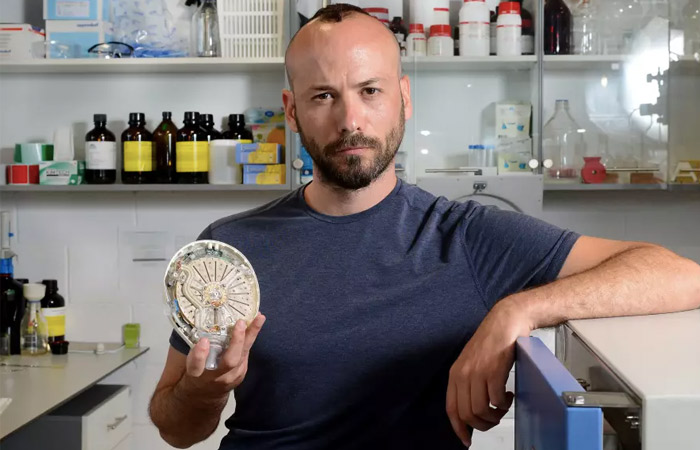
Perry Davidson, founder of Syqe Medical
3DN : How does 3D printing affect the manufacturing process of your inhaler?
At Syqe Medical, 3D printing is an extension of our toolbox, an accelerator of our thinking process and an essential element of our success. We use 3D printing at all stages of the manufacturing process of our products, from design to production. As a multidisciplinary team, each department uses 3D technologies differently. These include the Product and Design team, which proposes new ideas, shapes and functions; the Biology team, which has unique tooling requirements; the R&D team, which requires rapid prototyping, templates and assembly of production facilities; and even our clinical team, which uses functional prototypes printed in 3D of our inhaler and accessories for conducting clinical trials.
Most of our 3D printers are located in our R&D offices to remind our staff that the use of machines is part of the development process. Our employees can use 3D printers without too much restriction, which inevitably influences their thinking. This led them to feel the need to use the printers, even if they had never used CAD software before, pushing them to learn the basics of modeling. Anyone who wants to use a 3D printer is trained with another employee, we do not have a dedicated person.
We use different types of printers, ranging from the FDM desktop machine to more complex systems such as the Stratasys Connex and the new XJET Carmel, with various materials: plastics, rubber imitations, ceramics, metals and even printed circuits.
3DN: What are the main advantages of additive manufacturing?
For us, the many advantages of additive manufacturing are all linked to each other. This begins with a change in the mindset of designers and engineers who were once limited to traditional technologies, their geometries and materials; now they can design and manufacture with many new possibilities. This leads to better design faster. The designs are now adapted to their function and not to the machine that will manufacture them.
Then having 3D printers on site, right next to the users, leads to more and more iterations, which leads to a faster overall process, then bringing greater benefits in terms of cost reduction. Although printers and their media can be expensive, time to market is usually the most expensive and risky factor in developing a new product. Accelerating development and manufacturing processes results in a faster launch date, which means a faster return on investment.
The inhaler is connected to a mobile application to control the dosage of medical cannabis.
3DN: How do you see the future of additive manufacturing in the pharmaceutical sector?
We are witnessing extraordinary developments in the pharmaceutical industry, operating and using 3D printers on a daily basis. Tailor-made drugs are becoming more and more sophisticated and widespread thanks to 3D printers. Another major development in my opinion is organ transplantation; the complexity and ingenuity involved are probably impossible to solve without 3D printers.
3DN: Any last words for our readers?
3D printing is not a substitute for all other production methods and cannot yet be treated as such. You need to know the existing 3D printing capabilities and your manufacturing requirements. Nevertheless, 3D printers are a valuable asset and I strongly recommend using them internally as part of any development process, with an emphasis on free use within the company, without limiting the duration and amount of use or the people who have access to them. Design, prototypes and even clinical trials can benefit considerably from such devices, and the products of the future will come to market faster: they will be better than if they had been manufactured in the traditional way. You can find more information on our official website HERE.
What do you think of the Syqe Medical inhaler? Let us know what you think in a comment below or on our Facebook and Twitter pages! Don’t forget to sign up for our free weekly Newsletter, with all the latest news in 3D printing delivered straight to your inbox!