SURGE Aims to Predict Life of Critical Military Parts During Production
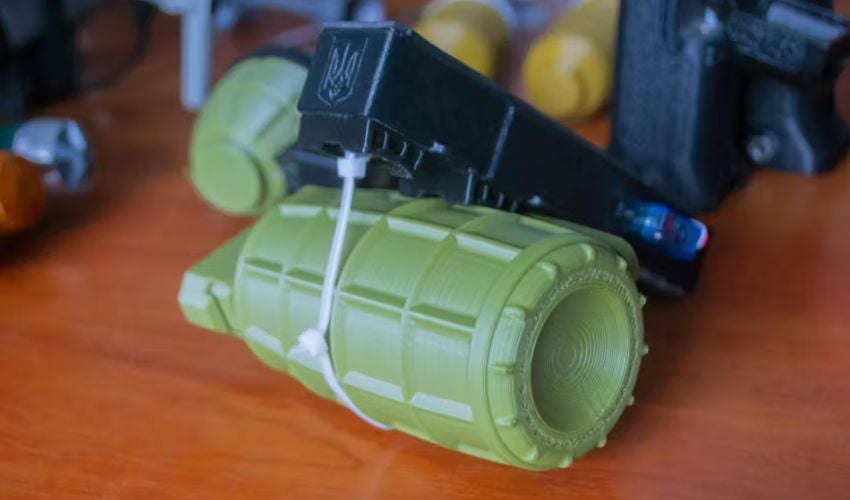
The Defense Advanced Research Projects Agency (DARPA) works to advance technology for United States national security. Created in 1958 in response to the Soviet Union’s 1957 launch of Sputnik, the agency positions itself as the nation’s commitment “to never again face a strategic technical surprise.” Instead of incremental change, they push for transformational breakthroughs. The DARPA program that interests us, of course, brings additive manufacturing into the fold. SURGE, which stands for Structures Uniquely Resolved to Guarantee Endurance, aims to rethink the current machine-focused methodology of part qualification in additive manufacturing. Instead of focusing on perfecting AM machines, they want to predict the structural life of each additively manufactured part, shifting the focus from qualifying the machine to assessing individual parts.
To predict the viability of 3D printed parts, SURGE turned first to the Southwest Research Institute (SwRI), entering into a $6.2 million contract on February 3rd. Just a week later, SURGE entered into an additional contract with HRL Laboratories for $8.9 million. While neither party released details on the contract or the work they will do together, we know they will both work toward SURGE’s general mission: exploring “a new approach where the life of every unique part is predicted at the point of production based directly on data captured during manufacturing.”
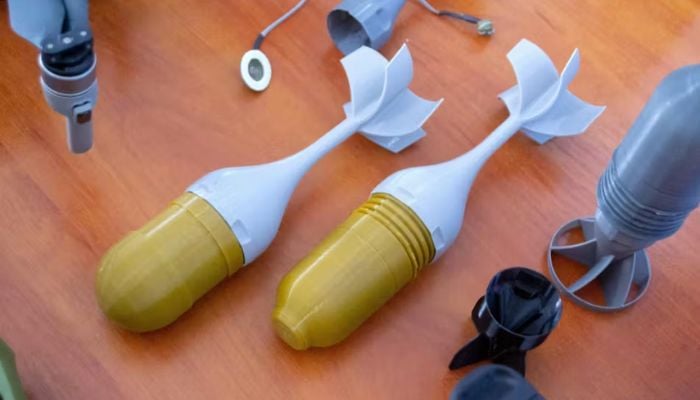
A prototype of 3D printed weaponry, not from DARPA (Image credit: Mari1408 Dreamstime.com)
How will the SURGE team do it? Military Aerospace Electronics reported that the program will combine in-situ sensing technologies, process modeling and microstructure-based fatigue-life methods to quantify the useful life of 3D printed hardware. They will derive predictions from extensive experimental validation. By focusing on the part, and evaluating it while it is being produced, they anticipate saving time and money.
According to SURGE, the current approach to AM involves fine-tuning AM machines to repeatably produce material with known properties. The problem, as SURGE sees it, is that this can take months or years of process optimization and material property testing at a cost that can surpass millions of dollars. By contrast, the program’s new approach will uncover the full potential of AM, permitting any geometry to be produced on any machine, anytime, anywhere. Specifically, they focus on critical structural military parts. By being able to guarantee part life, SURGE will be able to deliver longer-term solutions.
An Ongoing Investment in AM for Defense
The contracts between SURGE, SwRI and HRL Laboratories are just one of many investments the United States’s defense services have made in favor of additive manufacturing. Last week, we reported that the United States Air Force is using 3D printed drag reducers on cargo aircraft, and the week before, Spanish-American company Supernova was awarded a contract to 3D print energetic materials for the Department of Defense.
Why is AM a popular solution? The technology can reduce costs and lead times, and it can make repairs, replacements and unique, customizable parts. For defense applications, it can be especially useful for work in the field, where new parts might be necessary at a moment’s notice. How SURGE could change the game for AM in defense remains to be seen, but you can learn more about the program here.
What do you think of SURGE’s additive manufacturing plan? Let us know in a comment below or on our LinkedIn, Facebook, and Twitter pages! For more on additive manufacturing in aerospace and defense, click HERE. Don’t forget to sign up for our free weekly Newsletter here, the latest 3D printing news straight to your inbox! You can also find all our videos on our YouTube channel.
*Cover Photo: Example of 3D printed weaponry, not from DARPA (Credit: Mari1408 Dreamstime.com)