#Startup3D: Diabatix on Using Generative Design for Cooling in 3D Printing
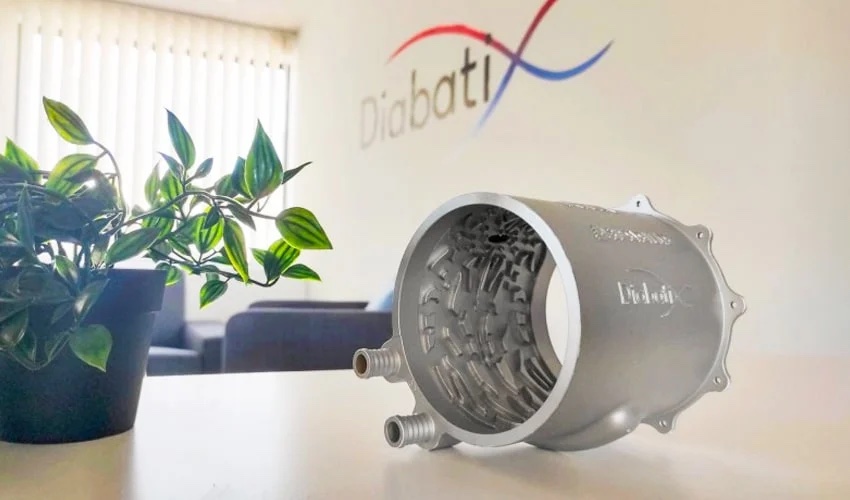
In the most demanding industries, such as aerospace or automotive, the creation of parts requires exhaustive quality control to ensure they are suitable for their intended purpose. One of these aspects to be taken into account is the cooling of the parts. In order to obtain higher quality, certain manufacturers need to create cooling channels that prevent components from overheating. The same is true when using 3D printing as a production method, especially when working with metallic materials. That’s why Belgian startup Diabatix has developed the ColdStream platform that allows you to use its generative design systems for increased cooling of parts, even those that have been 3D printed. We spoke with its team to learn more about the young company and its role in the additive manufacturing industry.
3DN: Could you introduce yourself and your connection to 3D printing?
I am Lieven Vervecken, the founder and CEO of Diabatix. I have two master’s degrees in engineering and a PhD in fluid mechanics from the University of Leuven (Belgium), so I think it’s fair to say I have a strong technical background. Immediately after completing my PhD in 2015, I founded Diabatix. During the first few years of Diabatix my main focus was on technology and software development but as the company grew, my role evolved towards business development and the management of the company. Today, I have a Head of R&D and a Head of Product & Operations in my management team that take full care of the technical aspect of the company.
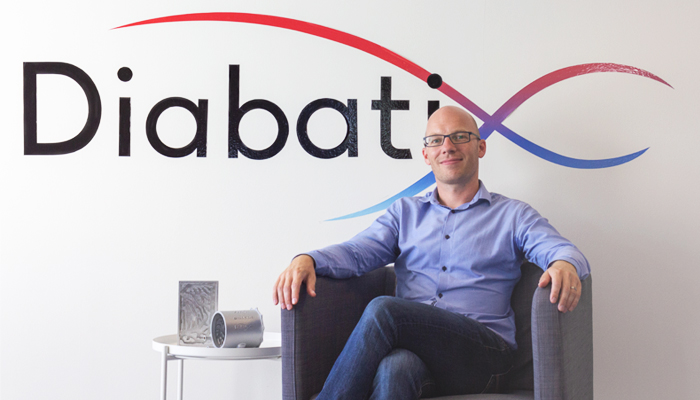
Lieven Vervecken, CEO and founder of Diabatix
My first contact with 3D printing was during the summer holidays of my first year at university in 2005. I had the opportunity to work as a student at Materialise for a few weeks. I was the ‘assistant’ of the R&D engineer who was responsible for the development of their Mammoth 3D printers. You can’t be any closer to the development of these machines. The nice thing was, I actually did this student job for 5 years in a row. As a result, the moment the Diabatix started, I was very well aware of the capabilities of 3D printing and the value we could bring if we would adopt our technology to this manufacturing process.
3DN: What is Diabtix? How did the idea to create the company come about?
Diabatix is a Belgian technology company with a clear focus on helping companies with the design of the cooling of their products. Initially, we started as an engineering consultancy firm to learn about the exact challenges and the needs in the industry within this scope. The opportunity we identified was in the initial phase of the cooling design process. It was striking to us that the approach to get to a cooling design for the product that was being developed, was fundamentally no different from the design process of 50 years ago. It was strongly relying on a trial-and-error cycle with a big loss in both design time and thermal performance. So we took on the challenge to develop ‘generative design’ for thermal components and offer an effective alternative that offers both speed and performance.
After two years of development, we delivered our first proof-of-concept and we switched to a project-based engineering business model during which we used our software only in-house to serve our customers. In 2021, we judged our software as sufficiently mature and we released it as an online platform called ColdStream.
3DN: What is ColdStream?
It is our main product. ColdStream is a cloud-native engineering platform that supports the entire cooling design process, from thermal analysis to thermal design. In particular, the ability to apply generative design to thermal and flow problems is what makes ColdStream unique. Usage of the platform does not require installation of any additional software, nor does it require any special hardware. The platform relies on state-of-the-art simulation methods which are regularly updated. ColdStream offers access to several libraries and a wide range of features that allow for convenient case and project management. We always strive to ensure the most optimal user experience. The platform is live since 2021 and it is used by customers all over the world, literally from Tokyo (Japan) to Silicon Valley (USA).
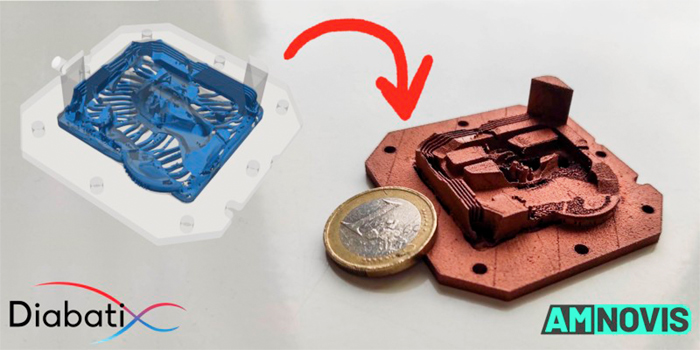
Photo Credits: Diabatix
3DN: What are the benefits of this platform for additive manufacturing? Are there limitations?
What’s special about our generative design technology is that you have freedom in the choice of manufacturing techniques. In other words, prior to starting a design run, the user selects the manufacturing technique of his preference and the software will automatically design within the boundaries of the chosen technique. For instance, a die-casted design will automatically be two-dimensional, a sheet-metal formed design will respect curvature constraints and so on. Of course, also designing for additive manufacturing is perfectly possible. Overhang angles, minimal and maximal features sizes, printing orientation, among others, are then taken into account. What I particularly like about designing for 3D printing is that ColdStream is capable of making full use of the additional design freedom. This directly results in a much higher thermal performance compared to any of the other techniques.
We recently completed a case study on replacing a commercially available CPU cooling by a copper 3D printed heatsink that clearly demonstrates the added value of combining the generative design method with 3D printing. We simply purchased an off-the-shelf available cooling and as an input to ColdStream, we imposed the nominal operating conditions of the product, we defined the volume of the initial heatsink as design volume and we set the preferred 3D printing parameters. An initial guess for what the design should look like is not needed so the user input is literally minimal. With an outstanding 55% lower thermal resistance for the same pressure drop compared to the commercial product, it seems fair to state that the value was proven.
3DN: How do you see the future of generative design in 3D printing?
Very bright! Over the past few years, I observed an exciting evolution in the field of additive manufacturing. Initially, the main drivers to adopt 3D printing were the reduction of assembly complexity and fast prototype production. But with the emergence of generative design tools a new driver was added, i.e. a functional driver. Basically, you can now design components for a dedicated function through generative design and, because of the capabilities of these design methods, they most often outperform human-based designs by a large margin. So due to generative design, there is now the possibility to design for what is manufacturable. Because of the flexibility of 3D printing, this is well beyond what is imaginable.
Obviously, I am happy that Diabatix is taking up a pioneering role in the development of generative design tools for additive manufacturing in the context of thermal management. We have seen many use cases where an effective thermal design can shift the economical balance from traditional manufacturing to 3D printing. This will only accelerate now that copper, an excellent material for thermal management, is becoming a mainstream 3D printing material.
3DN: Any last words for our readers?
Thanks for reading! If you want to know more, don’t hesitate to visit our website HERE. It contains a bunch of resources related to additive and you have the possibility to try out our ColdStream platform yourself. Of course, you are always free to connect with me via LinkedIn to reach out to me directly.
What do you think of Diabatix and its generative design platform?Let us know in a comment below or on our LinkedIn, Facebook, and Twitter pages! Don’t forget to sign up for our free weekly Newsletter here, the latest 3D printing news straight to your inbox! You can also find all our videos on our YouTube channel.
*Cover Photo Credits: Diabatix