US Soldier Completes SPEE3D Additive Manufacturing Demonstration for Army Research Lab
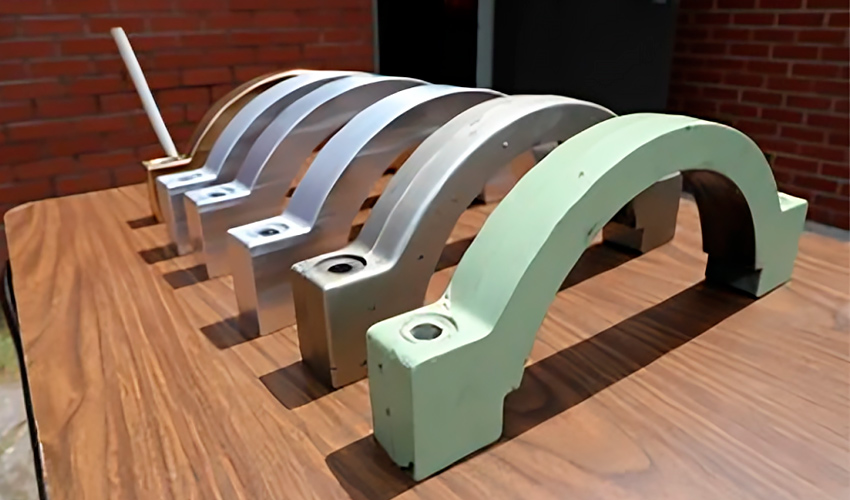
By 2027, the value of additive manufacturing in the defense sector is projected to be $1.7 billion. Why? Employing additive manufacturing technologies is advantageous because it can mean faster production times, cheaper costs, and more customizable outcomes. While 3D printing for the defense industry is often only conducted by experts, the US Army wanted to see if a soldier with no background in AM could be trained to produce a critical part within a short period. This way, parts could be produced on the field or at deployment locations in times of need. To test this idea, they completed an exercise at the University of Tennessee, Knoxville from August 5th to the 16th, and the demonstration was a success.
The collaboration had many players. The US Army Combat Capabilities Development Command (DEVCOM) and the Army Research Laboratory (ARL) were the government leaders. SPEE3D was the AM company lead along with VCR Metal Systems. The University of Tennessee Knoxville was the demonstration host, and the 278th Armored Cavalry Regiment (ACR) was the site host with soldiers.
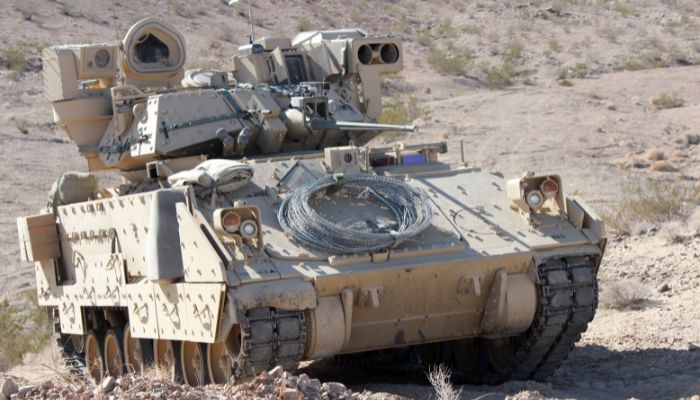
This is a Bradley Fighting Vehicle, similar to the one for which the soldier 3D printed a transmission mount, though not the same vehicle. (Photo Credit: Sgt. Eric Garland, Public domain, via Wikimedia Commons)
For this trial, a soldier with no experience in AM learned to print a Bradley Fighting Vehicle’s transmission mount using the WarpSPEE3D printer. Then, they installed the 3D printed transmission mount into the vehicle and took it on test drives. Upon return, the part showed no degradation, and the mission succeeded. This soldier, with only brief training, could restore the vehicle’s capabilities.
SPEE3D is a leading metal additive manufacturing company. They provided their WarpSPEE3D printer for the demonstration, which uses cold spray additive manufacturing (CSAM) technology. CSAM involves a high-velocity gas jet spraying powder particles onto a substrate. The gas jet accelerates the particles so fast—up to four times the speed of sound—that it allows the metal to bond through mechanical interlocking and metallurgical bonding. This will either coat the surface or, in this case, create a whole part. CSAM is relatively fast, and several types of metals can be used.
Bryon Kennedy, CEO of SPEE3D, said “SPEE3D intends to make additive manufacturing accessible as a quick, cost-effective, and easy way to print crucial metal parts that otherwise would not be available at the point of need. Having a soldier with no previous additive manufacturing experience learn our technology within a week certainly meets that goal.”
If 3D printing can practically be achieved by deployed soldiers or soldiers on the field, that means parts or repairs could potentially be completed the moment they are needed. Michael Nicholas, Materials Engineer at DEVCOM ARL, explained “This demonstration successfully illustrated how cold spray technology can be utilized to positively impact the warfighter in expeditionary scenarios. Expeditionary cold systems provide added repair and manufacturing capabilities which can address supply chain challenges as would be expected in a contested logistics environment. Overall, this advanced manufacturing demonstration was extremely successful due to our amazing partnerships with industry, academia, and future technology users.” For more, find the original press release here.
What do you think of the potential of AM technology in the field of defense? Let us know in a comment below or on our LinkedIn, Facebook, and Twitter pages! Don’t forget to sign up for our free weekly Newsletter here, the latest 3D printing news straight to your inbox! You can also find all our videos on our YouTube channel.