SPEE3D Enables On-Demand Manufacturing in Hard-to-Access Locations With EMU
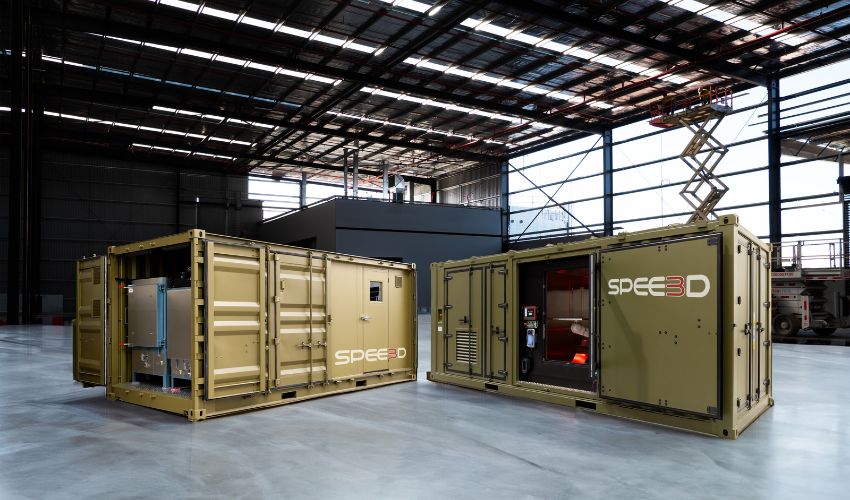
The Covid pandemic and the blocked cargo ship “Ever Given” in the Suez Canal demonstrated what international companies already know: supply chains are extremely unstable, and dependency causes numerous production processes and project work to falter. The effects of unsustainable supply chains are particularly evident in remote locations. Think of the maritime sector or the military, where there is often an immediate need for spare parts, but no remedy is available due to being in a remote area. We now know from numerous application examples that 3D printing can be used for on-demand production on site, although parameters such as speed and quality are often unsatisfactory. SPEE3D responds to this demand with its Expeditionary Manufacturing Unit (EMU), which combines Cold Spray Additive Manufacturing and post-processing, offering a solution to the challenge of production in hard-to-reach locations.
The Australian manufacturer of metal 3D printing solutions has developed a fast, cost-effective and scalable solution for 3D printing of metal parts with its patented Cold Spray Additive Manufacturing (CSAM) technology. SPEE3D’s technology works with a variety of metals – copper, stainless steel, aluminum and various alloys – and these solutions are known for their use in high-performance applications in industry and the defense sector. With the EMU, the company is specifically targeting customers struggling with unstable supply chains by providing a high-performance, high-quality solution for on-site and on-demand manufacturing.
EMU bypasses unstable supply chains with fast on-site production
The EMU consists of two 20-foot containers with twist locks and includes a metal 3D printer, the XSPEE3D, and the SPEE3Dcell post-processing unit. Thus, the unit enables the production of metal parts at remote locations, their post-processing and various quality tests. The XSPEE3D impresses with the rapid production of robust metal parts, while the SPEE3Dcell system provides a furnace for heat treatment, a CNC three-axis milling machine, tools and testing equipment.
The combination of these two units into one system, the EMU, enables complete end-to-end part production without the need to access external facilities. This way, important components can be made available immediately and problems such as long lead times and unstable supply chains are avoided.
A significant advantage of the EMU is the fast printing process, achieved thanks to SPEE3D’s patented CSAM technology. Here, a rocket nozzle accelerates the air and metal powder so that they are combined at three times the speed of sound. The result is particularly dense metal parts with low porosity. The technology has a deposition rate of 100g/min and is significantly faster than alternative casting methods. Other arguments in favor of cold spraying instead of casting are the lower costs and independence from supply chains, i.e. simplified logistics.
The EMU was developed in collaboration with defense forces and meets the requirements for a robust, fast, and user-friendly solution in remote areas. It is extremely safe to operate, eliminating the need for expensive and dangerous lasers or inert gases. The system can be transported on a single platform – such as a truck, ship, or cargo plane – where complete parts can be finished quickly, efficiently and ready for use. For example, SPEE3D reports NAB parts can be printed, heat-treated and post-processed in just 24 hours, highlighting the possibility of rapid spare parts supply or tooling.
Just recently, the EMU was also successfully tested in the European exercise AM Village with the British Army and the US exercise RIMPAC with the US Department of Defense. The EMU impressed with its versatility, robustness, and mobility – parameters that were at the forefront of the EMU’s development, as Byron Kennedy, CEO of SPEE3D, emphasizes:
“The launch of our Expeditionary Manufacturing Unit addresses the current state of the global supply chain, which is fragile and increasingly under pressure,” he explained at the time of EMU’s launch before continuing, “Part of the issue for defense and other heavy industries is getting critical equipment up and running quickly to avoid costly production delays. EMU will enable [defense organizations] to take control, giving them the ability to print and post-process parts very quickly from anywhere.”
A concrete example of this is the printing of a Jaguar J60 manifold made of aluminum bronze alloy. This engine manifold was used in armored vehicles and is no longer traditionally manufactured. With SPEE3D’s EMU capability, this 6.9-kilogram engine manifold could be produced in as little as two hours, and following SPEE3D’s post-processing recommendations with SPEE3Dcell, it is ready to use in just over a day. This shows that the EMU offers a cost-effective alternative to small series production.
Anyone who wants to see the potential of the EMU for themselves will have the opportunity to see the XSPEE3D 3D metal printer in action at Formnext 2024 in Frankfurt. As part of the show, SPEE3D will be running live demonstrations at its stand C.01 in hall 12.0, showcasing the CSAM process. In addition, you will also see numerous application examples at Formnext, including parts made from SPEE3D’s newly launched NAB material for use in the maritime sector. You can find out more about SPEE3D HERE.
What do you think of the EMU from SPEE3D? Let us know in a comment below or on our LinkedIn, Facebook, and Twitter pages! Don’t forget to sign up for our free weekly newsletter here for the latest 3D printing news straight to your inbox! You can also find all our videos on our YouTube channel.
*All Photo Credits: SPEE3D