What Are the Soluble Support Materials Available for 3D Printing?
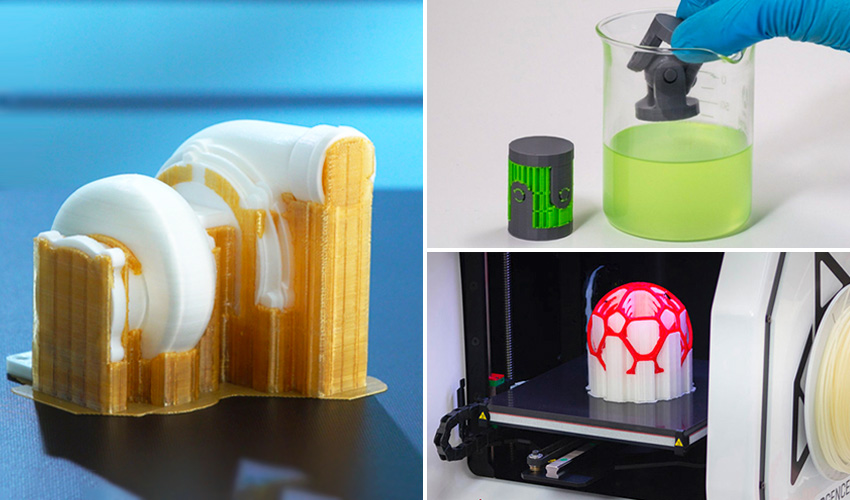
Support removal can be an annoying part of post-processing in 3D printing. However, it does not have to be. If you have a dual-extruder 3D FDM 3D printer, or any other process that allows multi-material printing, you can take advantage of soluble support materials. As their name suggests, soluble support is a material that can be used as for support structures in 3D printing and is soluble, whether in water, a chemical agent or organic agents. But what materials are out there? Find out in our list of some of the most common soluble support materials for FDM 3D printing (though many companies offer their own versions as well), separated by the medium in which they dissolve.
Water-Soluble Materials
PVA
Polyvinyl Alcohol (PVA), along with HIPS, is one of the most popular soluble support materials for intricate structures in FDM 3D printing. As would be expected, PVA’s most notable benefit lies in its water solubility, allowing for effortless removal of these supports and eliminating the necessity for harsh chemicals or time-consuming post-processing. Furthermore, PVA’s water solubility not only streamlines the printing process but also enhances design flexibility, enabling the production of more complex geometries in parts. Its compatibility with various filaments, such as PLA and Nylon, broadens its use, allowing for more visually appealing models and durable prototypes. This material operates within a temperature range of 45-60 °C, rendering a heated bed optional and eliminating the need for an enclosure. Additionally, the printing temperature for PVA falls in the range of 185-200 °C, and no special hotend is required, further emphasizing its user-friendly printing process. Despite challenges like PVA’s moisture sensitivity which calls for proper storage, PVA’s positive features, including transparency, biodegradability, non-toxicity, and ease of dissolving, establish it as a highly beneficial material for molds, decorative objects, and elaborate designs.
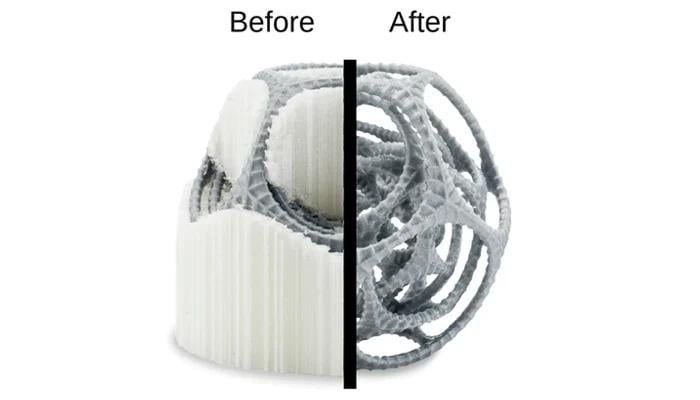
Photo Credits: UltiMaker
BVOH
Another water-soluble material used for support structures in FDM 3D printing is BVOH (Butenediol vinyl alcohol copolymer). It is particularly advantageous in cases where traditional substrates may be difficult to remove or fail to deliver the desired result. In fact, BVOH makes it very easy to remove substrates. Once you’ve printed a 3D object, all you have to do is immerse it in hot water for the support to dissolve completely, 100%. BVOH is practical for printing prototypes, such as small models and those with hard-to-reach spaces for removing supports. The material is also suitable for fine details, jewelry, decorations and complex structures. It imposes no limitations on object shapes during design. What’s more, BVOH is environmentally friendly and can often be disposed of down the drain. It can be printed on a variety of materials, including PLA, ABS, PETG, ASA and elastomeric filaments. To preserve its quality, it is advisable to protect it from humidity, light and UV rays by storing it in a dry place or using it quickly.
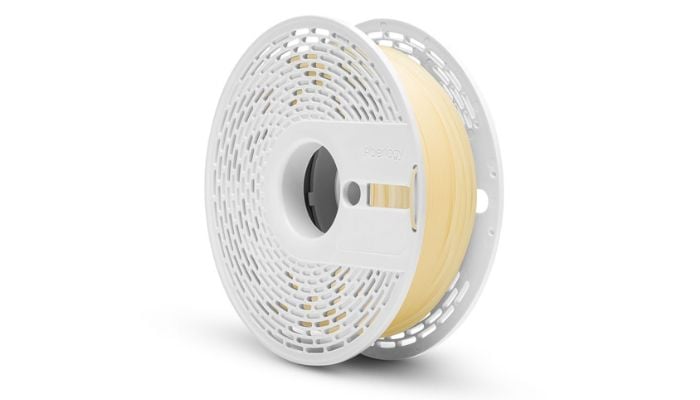
Photo Credits: Fiberlogy
Aquasys 120
Aquasys 120, developed by Infinite Material Solutions, marks a breakthrough in the field of support materials for 3D printing. Its special formulation, which combines a water-soluble polymer with a polysaccharide called trehalose, ensures high thermal stability while preserving optimum flexibility. Aquasys 120’s solubility means it dissolves twice as fast as PVA at room temperature, and up to six times faster in water heated to around 80 degrees. Its versatility is reflected in its compatibility with various materials such as PLA, ABS, CPE, ABS, TPU, PC-ABS, PP and PETG, making it one of the most adaptable soluble support materials available on the 3D printing market. But it’s not the only alternative. Aquasys 180 also sets an unrivalled benchmark as an advanced and highly compatible support material. It is water-soluble and compatible with advanced high-temperature materials such as PEEK, PEKK, PEI and PPSU.
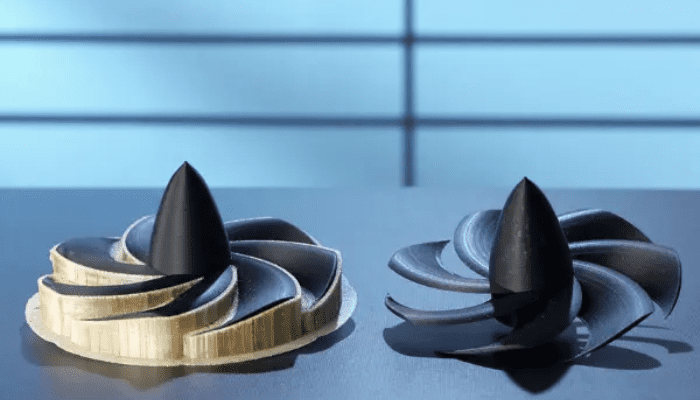
Photo Credits: Infinite Material Solutions
Organic Solvent-Soluble Materials
HIPS, a Thermoplastic Polymer for Support Structures
HIPS or “High Impact Polystyrene” is a thermoplastic polymer that is made from a blend of polystyrene and polybutadiene rubber. It is frequently used as a support material in FDM printing. Its main characteristic is its high solubility, which distinguishes it from other soluble support materials and allows it to dissolve easily in organic solvents. This means that no tools are required to separate the printed part from the support material. A user must simply immerse the part in the solution. In addition to its solubility, HIPS offers other advantages, such as heat resistance and translucency, making the printing process easier by allowing the user to see through the material. However, despite these advantageous properties, it has a number of drawbacks, such as the risk of discoloration, the production of toxic fumes during printing, and poor resistance to low temperatures.
PVB
As a printing support material, PVB comes in handy for complex objects or those requiring internal supports. Soluble in solvent, it enables easy removal of post-printing supports. PVB’s chemical solubility, particularly with agents such as isopropyl alcohol (IPA), offers advantages in terms of bonding and smoothing during post-treatment of printed parts. What’s more, its extensive compatibility with a variety of materials such as PETG and nylon offers flexibility in its use.
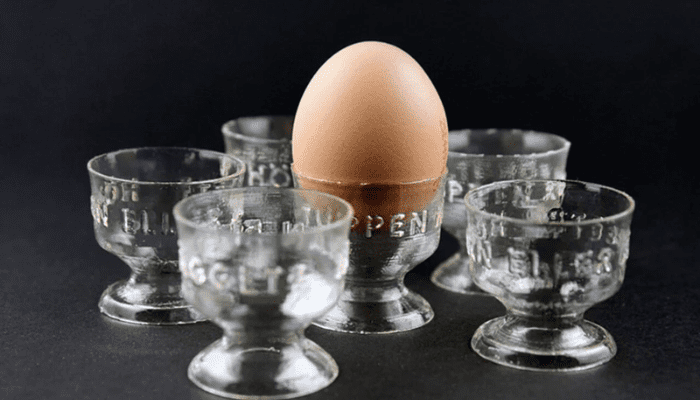
Photo Credits: Polymaker
ATP-Based Polymers
ATP-based polymers (acrylate terpolymers) are ideally suited to 3D printing support structures, as they are soluble in alkaline solutions. Unlike other materials, they do not simply dissolve on contact with water, but require that the liquid have an alkaline pH, making them less sensitive to humid environments than PVA, for example. Although they are more resistant to ambient humidity, it is essential to store the filament spool away from direct sunlight, in a cool place. ATP-based support materials are compatible with materials such as ABS and ASA, although specific compatibility depends on the manufacturer. Generally, the manufacturer provides detailed information on compatible materials and instructions on printing parameters. After printing, support structures can be dissolved in an alkaline liquid by adding an activator to the water, often supplied with the filament. An example of an ATP-based support material is Zortrax’s Z-Support ATP, which also offers the activator.
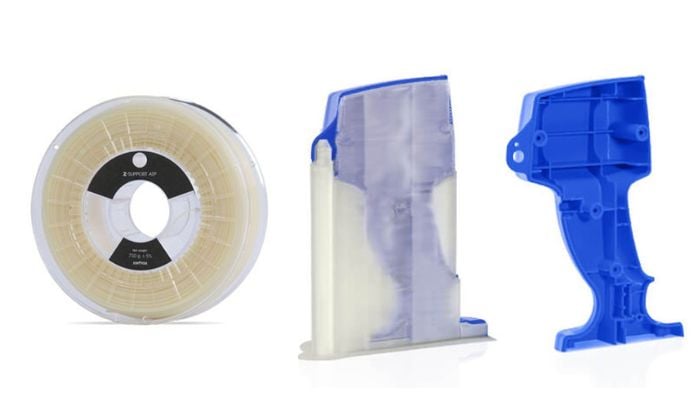
Photo Credits: Zortrax
What do you think of these soluble support materials for 3D printing? Do you prefer one over the other? Let us know in a comment below or on our LinkedIn, Facebook, and Twitter pages! Don’t forget to sign up for our free weekly Newsletter here, the latest 3D printing news straight to your inbox! You can also find all our videos on our YouTube channel.
There is also Massivit 3D’s Dimengel WB which is a proprietary photo polymer material designed for the Massivit 10000 additive manufacturing system. Based on Cast In Motion technology, this advanced water-breakable material enables the creation of tooling with complex geometries and custom manufacturing without extensive support structures. It is a wash-away material that can be removed by immersing into a bath of plain water or peeled after exposure to a water fog system, or by any other mechanical means.
It has been a game changer in the world of mould production for composite materials as it has reduced the traditional 19 steps to 4 meaning moulds are created in days instead of weeks.
Slicers such as Simplify3D, and possibly others as well, allow two stage support structures too. This means there’s a ‘dense’ support configuration, and a regular support configuration. This allows the area that actually interfaces with the part (the dense supports) be of this material (extruders can be different between dense and regular supports), while the bulk of the support material can be of a cheaper material. As long as the 4 or so interfacing layers are soluble, it’s just as good as if all the supports are soluble (unless of course it’s an almost totally enclosed volume). Anyway, this is a technique to have your cake and eat it too in many circumstances.