Siemens Energy repairs and improves turbine blades with metal 3D printing
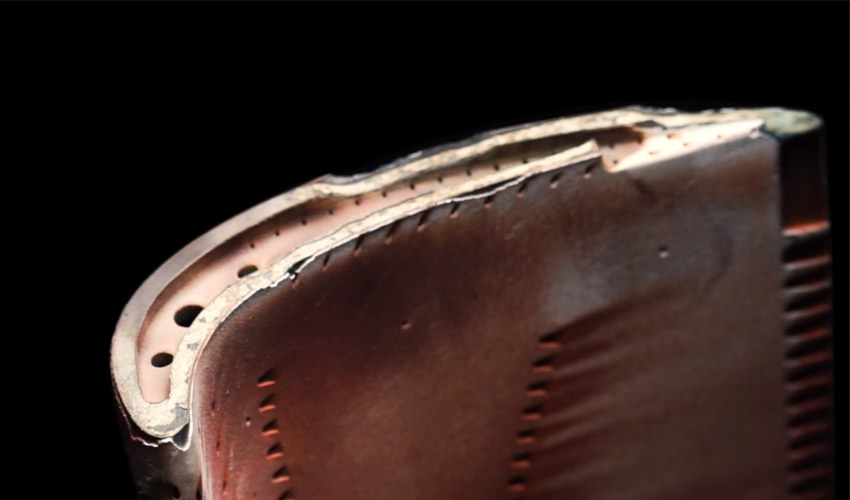
Siemens Energy is one of the German group’s four major divisions and specializes in manufacturing thermal power plants. A recognized market player, it relies on additive manufacturing to develop innovative applications in the energy sector. The company recently developed a new digital repair line to improve the functionality of gas turbine blades. Relying on a hybrid laser powder bed fusion process, Siemens Energy were able to prevent failure by adding cooling structures in critical areas.
Turbines are responsible for converting the kinetic energy of a fluid into mechanical energy. The moving fluid energy forces several blades attached to the turbine to rotate at high speeds, transforming it into mechanical energy. Turbines are therefore subject to heavy constraints, both in terms of temperature or gas displacement speed. Accordingly, the blades have a tendency to weaken, particularly due to potential burn-off at their ends. Siemens Energy explains: “This process leads to a vicious circle: with greater gap formation, the temperature of the blade material increases due to the overflowing hot gas, which in turn leads to even faster material loss and further increases the gap between blade tip and ring segment.” It was therefore necessary to find a solution to reinforce the ends of the gas turbine blades and additive manufacturing proved to be a good option.
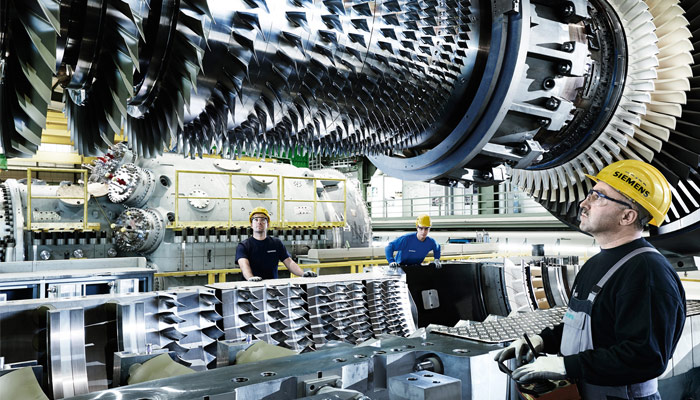
Turbine blades undergo heavy stress (photo credits: Siemens AG)
The team relied on a laser powder bed fusion process. A rather surprising choice when it is well known that Directed Energy Deposition (DED) is the preferred process for repairing parts. This process, called Hybrid L-PBF Repair or HybridTech for short, is a research project led by 9 partners including Siemens, Fraunhofer and BAM. Launched in July 2020, its objective is to implement new technologies to repair and maintain parts.
By applying this HybridTech technology, Siemens Energy claims that it can design internal cooling channels for an already existing blade. However, in order to so, it is first necessary to modify the design of the blades, especially since they can differ significantly from one component to another. This is where this digital CAD-CAM chain comes in. A 3D scan first digitizes the end of the blade, allowing HybridTech technology to tailor the laser (power, shape and displacement) to the shape of the part. The teams also had to deal with a material for the tip of the blade that was very resistant to oxidation.
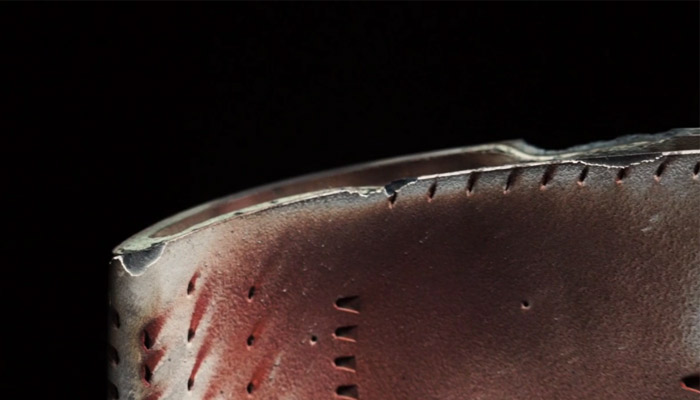
HybridTech technology will repair damaged blades (photo credits: Siemens Energy)
So far, a few blades have reportedly been repaired and a process is underway to establish criteria and standards of repair. This method should be extended to other critical components, thus strongly impacting production processes.You can find the official press release HERE .
* Cover photo credits: Siemens Energy
What do you think of the technology used by Siemens Energy? Let us know in a comment below or on our Facebook and Twitter pages! Sign up for our free weekly Newsletter here, the latest 3D printing news straight to your inbox!