Shark Intestines Inspire 3D Printed Pipes
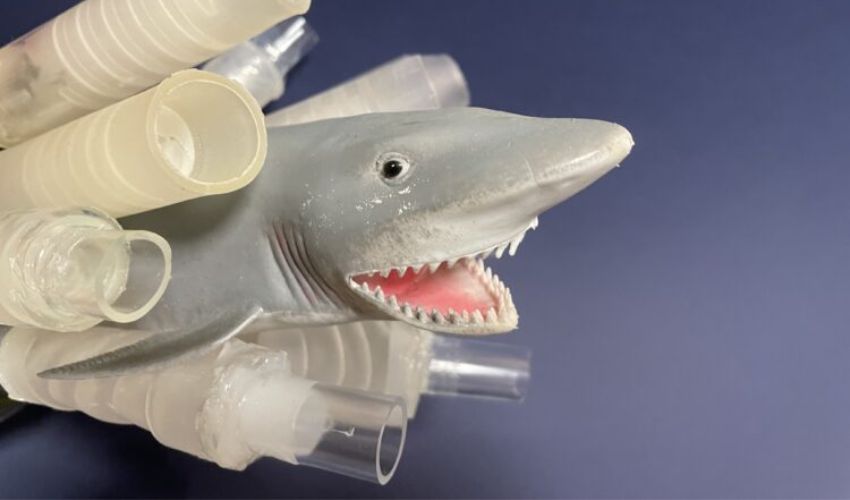
Sometimes, the answers to design questions are not hidden in plain sight, but rather, in shark intestines. Such was the case in a study conducted by researchers at the University of Washington. The team was on a mission to understand whether pipes designed like shark and ray intestines would promote asymmetric flow, meaning, the one-way flow of liquids. Their interest in the question was prompted by a 2021 publication that supposed “shark intestines may operate as Tesla valves,” and the University of Washington team wanted to test the claim. The National Science Foundation, the Washington Research Foundation, and the Fulbright Foundation funded this research.
Ido Levin, lead author of the study, explained his interest in the subject. “Flow asymmetry in a pipe with no moving flaps has tremendous technological potential, but the mechanism was puzzling,” he said. “It was not clear which parts of the shark’s intestinal structure contributed to the asymmetry and which served only to increase the surface area for nutrient uptake.”
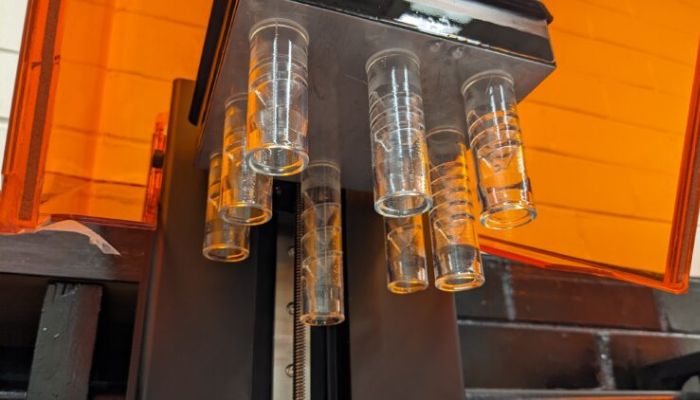
These are eight of the research team’s pipes with various interior helices (photo credits: Ido Levin/University of Washington)
Many pipes, including human intestines, have liquid flow controlled by moving flaps. However, these flaps can fail and cause backflow. By contrast, shark and ray intestines contain helical structures that loop around a cylindrical hole, promoting flow down the digestive tract. The researchers at the University of Washington wanted to see if they could create pipes modeled after this structure and realized their designs did indeed promote the desired flow asymmetry. “The first measurement of flow asymmetry was a ‘Eureka’ moment,” Levin said. “Until that instant, we didn’t know if our idealized structures could reproduce the flow effects seen in sharks.”
How was this achievement accomplished?
While the University of Washington’s press release did not mention the specific type of 3D printing their researchers used, their photos and descriptions suggest VAT photopolymerization. To make the pipes, the team 3D printed “biomimetic” pipes with rigid materials, which they used to test which physical parameters of the interior helices yielded the largest flow asymmetries. The parameters they varied included the pitch, the hole radius, the tilt angle, and the number of turns within the pipe.
By fine-tuning the geometrical elements of their design, they eventually succeeded in getting their prototypes’ flow asymmetry to exceed that of the Tesla Valve, which was famously designed to be a one-way fluidic device with no moving parts. Once this was established with the rigid material, the Washington University team tried printing the pipes with the softest printable polymers on the market. This way, their pipes more closely mimic intestines, which are highly “deformable.” The result was astounding, and the printed tubes with soft material performed at least seven times better compared to all previously measured Tesla valves.
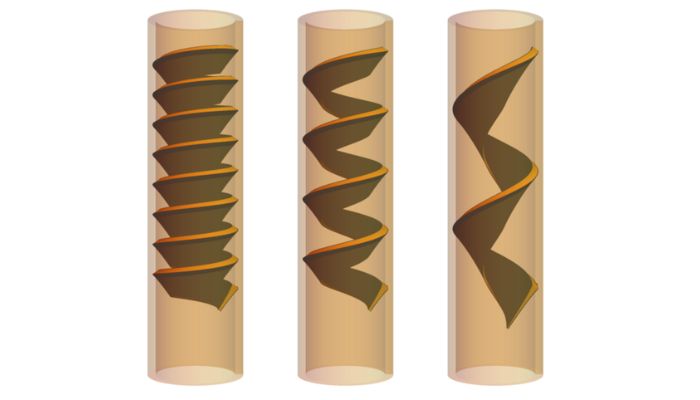
The various types of helical structures in the pipes’ interiors (photo credits: Ido Levin)
Yet, there is still potential for the models to advance. “Actual intestines are still about 100 times softer than our soft material, so there is plenty of room for improvement,” said Naroa Sadaba, one of the researchers on the team. Sarah Keller, another researcher, explained that their team had to thank sharks, for one, for allowing them to discover the helical design’s potential. “Biomimicry is a powerful way of discovering new designs,” Keller said. “We never would have thought of the structures ourselves.”
The type of piping designs the University of Washington team developed have a diverse range of applications. “Chemists were already motivated to develop polymers that are simultaneously soft, strong and printable,” said Alshakim Nelson, an expert in developing new types of polymers. “The potential use of these polymers to control flow in applications ranging from engineering to medicine strengthens that motivation.” To learn more about the study, read the University of Washington’s press release here.
What do you think of the use of biomimicry for additive manufacturing designs? Let us know in a comment below or on our LinkedIn, Facebook, and Twitter pages! Don’t forget to sign up for our free weekly newsletter here for the latest 3D printing news straight to your inbox! You can also find all our videos on our YouTube channel.
*Cover Photo Credit: Sarah L. Keller/University of Washington