Sensors for Future NASA Missions To Be Manufactured With Additive Technology
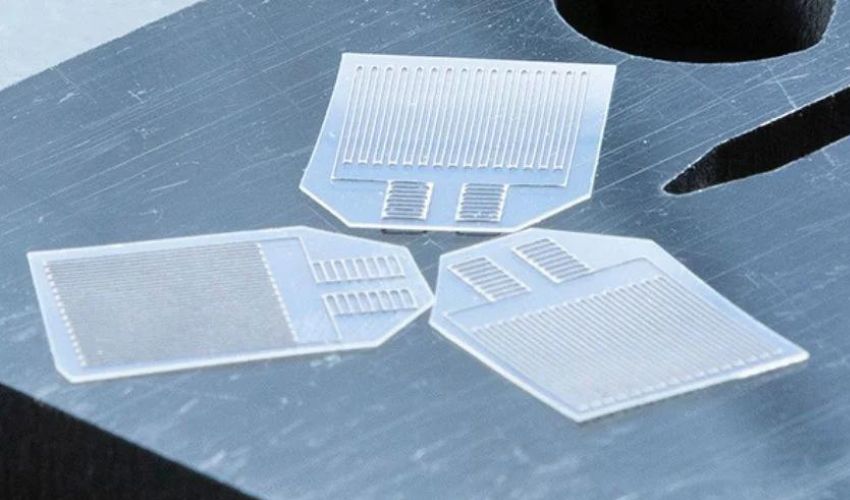
The aerospace sector stands out as a prime beneficiary of additive manufacturing‘s advantages. Through 3D printing, intricate, lightweight components can now be designed and produced with unprecedented speed and efficiency, revolutionizing not only aerospace but various other industries as well. A groundbreaking moment in space exploration and additive manufacturing occurred when a team from the FAMU-FSU College of Engineering, a collaborative institution between Florida A&M University and Florida State University, successfully developed 3D printed sensors for NASA. This achievement represents a notable stride in leveraging 3D printing technology to craft high-performance components, promising remarkable advancements in both space exploration and manufacturing capabilities.
The research team, consisting of engineering students and experienced engineers, was led by Professor Subramanian Ramakrishnan of the Department of Chemical and Biomedical Engineering. With the expertise of the multidisciplinary team and the decision to use innovative technologies such as additive technologies, they were able to produce state-of-the-art sensors that mechanically outperform conventional sensors used in the aerospace industry. This breakthrough is the result of the NASA-driven project Additive Manufacturing of Electronics for NASA Applications, on which work will continue for another year. The universities received $300,000 for research and development of the sensors, which will be supported by NASA engineers.
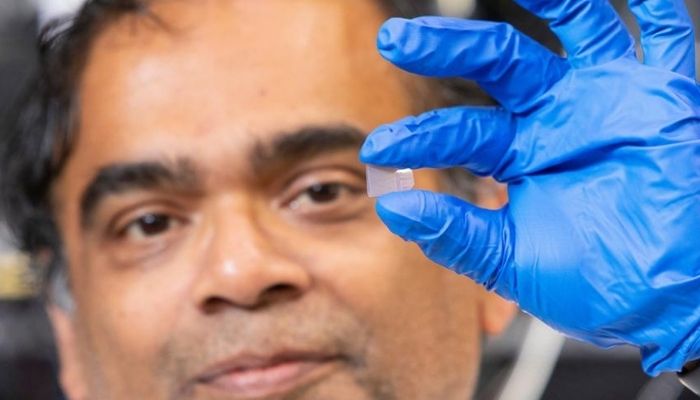
Professor Subramanian Ramakrishnan, project leader (Photo Credit: FAMU-FSU College of Engineering).
Sensors play a pivotal role in aerospace endeavors, translating physical phenomena into electrical signals for computer processing. This critical function enables engineers to comprehend the behavior of spacecraft systems amid the rigors of space. Among the array of sensor types with specific functions, strain gauges stand out. These sensors are instrumental in measuring the deformation of objects, offering invaluable insights into structural integrity. During aerospace missions, these devices assume a paramount role, diligently monitoring systems in real-time. Their vigilance is essential in averting any deformations that might jeopardize spacecraft safety and operational efficiency.
3D Printing Driving Aerospace Innovation
To produce the strain gauges, which are a flexible, insulating stamping, 3D printing was used in combination with a laser baking method that involves heating the ink to improve its properties without melting it. The sensors were printed with silver ink and with the help of a printer from the manufacturer nScrypt, which is ideal for printing on curved surfaces. The combination of both techniques resulted in a product with optimal mechanical and electrical properties. The sensors are more accurate and have shown better performance when measuring the deformation of objects. On the next stage in the development of the sensors Professor Ramakrishnan stated, “We are also experimenting with novel ink formations and process parameters that will result in new design rules and better methods for fast additive manufacturing of next-generation sensors at NASA.”
The project shows how space technology is redefining its boundaries. The two-year grant, awarded through NASA’s Science Mission Directorate (SMD) Bridge Program, seeks to advance diversity, equity, inclusion, and accessibility in NASA’s workforce and the U.S. science and engineering community. “Students will spend fall and spring semesters at the college and work with NASA scientists at one of the centers,” Ramakrishnan said. “They will have access throughout the year for mentorship opportunities and networking. The students will be learning while making a product to launch future rocket missions.”
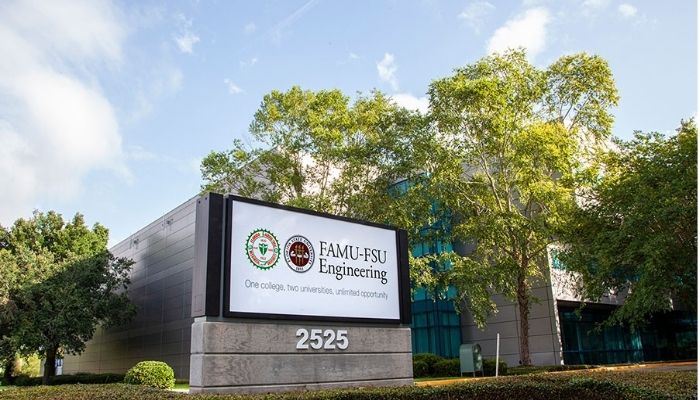
(Photo Credits: Florida State University)
The program emphasizes mentoring students and expanding their hands-on training to shape NASA’s scientists of tomorrow, as well as easing students’ transition to graduate school or STEM careers. Beth Paquette, an aerospace engineer at NASA’s Goddard Space Flight Center in Greenbelt, Maryland, and Curtis Hill, principal investigator at NASA’s Marshall Space Flight Center in Huntsville, Alabama, have also collaborated on the project and are among the experts who will work with the students.
What do you think of 3D printed sensors for NASA? Let us know in a comment below or on our LinkedIn, Facebook, and Twitter pages! Don’t forget to sign up for our free weekly newsletter here for the latest 3D printing news straight to your inbox! You can also find all our videos on our YouTube channel.
*Cover Photo Credits: FAMU-FSU College of Engineering