Self-Monitoring Plastics? Glasgow Researchers 3D Print Auxetic Materials
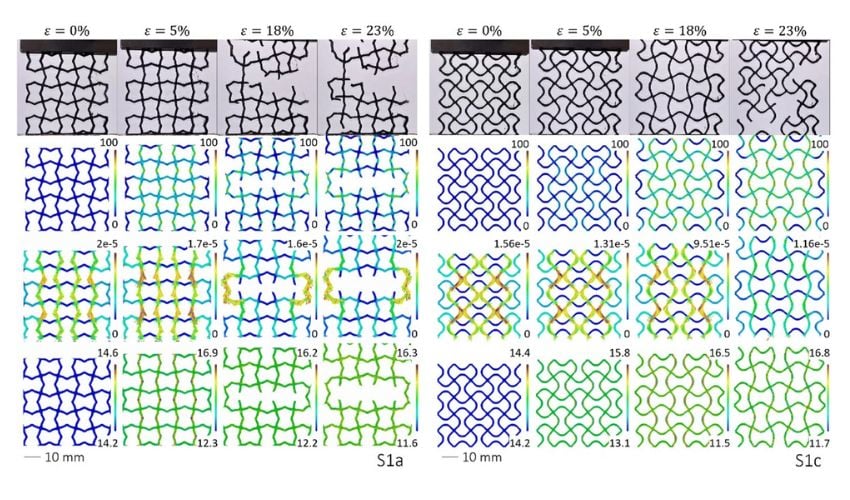
Picture yourself stretching a material, say, a rubber band. The more you stretch it, the thinner it becomes. A group of researchers from the University of Glasgow designed a material that does the opposite: plastics that grow wider when pulled. These are classified as auxetic materials, and the researchers achieved this unique behaviour by carefully engineering and 3D printing internal geometries. But how exactly are these plastics made, and what are their applications?
Late this June, the team reported a breakthrough in developing and designing novel auxetic structures using high-performance engineering plastics. The research, published in Materials Horizons, demonstrates how additive manufacturing can create self-monitoring materials with programmable properties like strength, stretchability and strain sensitivity. In general, auxetic materials have extraordinary mechanical characteristics, like enhanced energy absorption and improved damage tolerance, so the plastics developed by the Glasgow team have potential for many applications.
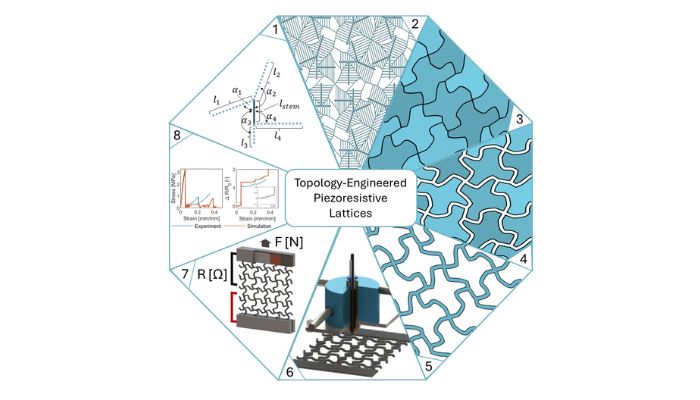
Illustration of the Glasgow study (Photo Credit: Johannes Schneider et al./Materials Horizons)
The researchers used an FDM Apium P220 3D printer from Apium Additive Technologies GmbH, with PEEK, to create these structures. PEEK is a strong, semi-crystalline thermoplastic that is not only heat and wear resistant but also capable of substituting some metals due to its strength-to-weight ratio. Furthermore, the material is lightweight and biocompatible, already widely used for engineering and biomedical purposes. Using PEEK allowed the researchers to precisely control both mechanical and electrical behaviour.
“We’ve shown that it’s possible to design PEEK lattices that are not only auxetic but also capable of sensing strain and damage without the need for embedded electronics,” said Professor Shanmugam Kumar, corresponding author of the study and a materials and additive manufacturing expert at the University of Glasgow’s James Watt School of Engineering.
The Fabrication Process
What makes the material self-sensing is a phenomenon called piezoresistivity. This phenomenon allows the materials to “sense” how they are being stretched, compressed or impacted. The researchers achieved this by creating a family of 2D lattices from four types of PEEK-based feedstock, including three that were infused with carbon nanotubes. These nanotubes give the plastic electrical conductivity, permitting it to act like a sensor. When the lattices are deformed under mechanical strain, their internal electrical resistance changes measurably.
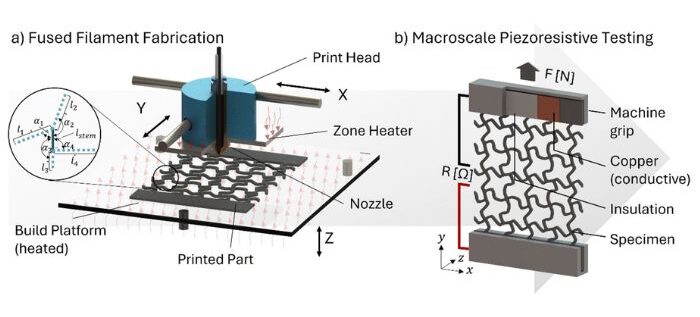
Illustration of the printing process (Photo Credit: Johannes Schneider et al./Materials Horizons)
The Glasgow team created the designs based on repeating units shaped like a double-ended ‘Y’, creating a branch-stem-branch layout. This framework enabled them to make a wider range of designs and to fine-tune the mechanical properties of each structure by changing parameters like thickness, angle and spacing. The team ended up compiling a catalogue of materials with various levels of auxeticity, stiffness, strength and sensitivity to strain and/or damage.
To accompany the newly developed materials, the researchers created a computational model to predict how these materials behave under different loading conditions. This tool accurately captures how the lattices’ electrical resistance changes in response to mechanical stress, allowing them to optimise material behaviour in simulation before 3D printing a physical sample. “By combining design, fabrication, and predictive modelling, we can now create materials that behave exactly as needed for a given application, whether that’s absorbing impact, sensing damage, or deforming in controlled ways,” Kumar said. “That means we can move towards a ‘design for failure’ philosophy where materials are not only strong and lightweight, but also intelligent, able to monitor their own integrity over time.”
Diverse Applications
The current study builds upon a previous study the team did with PLA infused with carbon black, where they created a library of 56 different auxetic lattice structures. For that previous research, which was published last year, the team created lattices that could stretch dramatically, sense tiny strains or withstand high loads. Similar to the PEEK lattices, the PLA structures could conduct electricity and respond to mechanical deformation through changes in piezoresistivity. “The PLA-based designs are ideal for temporary applications like smart scaffolds in low-load biomedical implants, or disposable sensors embedded in sports gear,” Kumar added. “The PEEK-based materials, on the other hand, open the door to permanent, load-bearing smart components in much more demanding environments.”
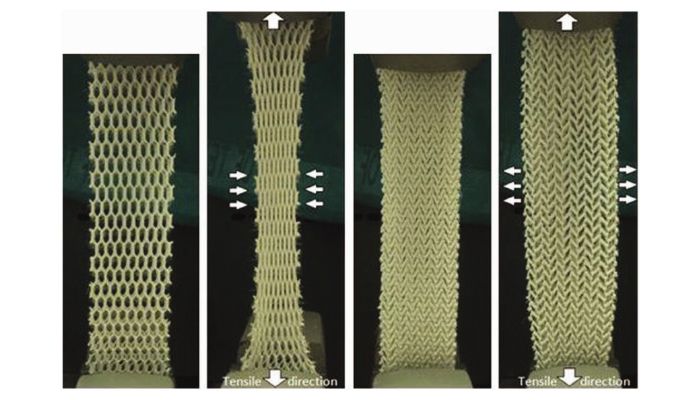
A comparison between conventional and auxetic spacer fabrics, from a different study. (Photo Credits: Wang Z, Hu H.)
What kind of applications are possible with the PEEK materials? Kumar listed several possibilities, including smart orthopaedic implants, aerospace skins and wearable technologies. It could also be used for impact-resistant vehicle structures and structural health monitoring. Kumar concluded, “We’re essentially giving designers a toolkit for building the next generation of multifunctional materials, ones that are as intelligent as they are strong.” To learn more, read the study HERE.
What do you think of the 3D printed auxetic materials? Let us know in a comment below or on our LinkedIn or Facebook pages! Plus, don’t forget to sign up for our free weekly Newsletter to get the latest 3D printing news straight to your inbox. You can also find all our videos on our YouTube channel.
*Cover Photo Credits: Johannes Schneider et al./Materials Horizons