Scientists Double the Solidity of 3D Printed Aluminum
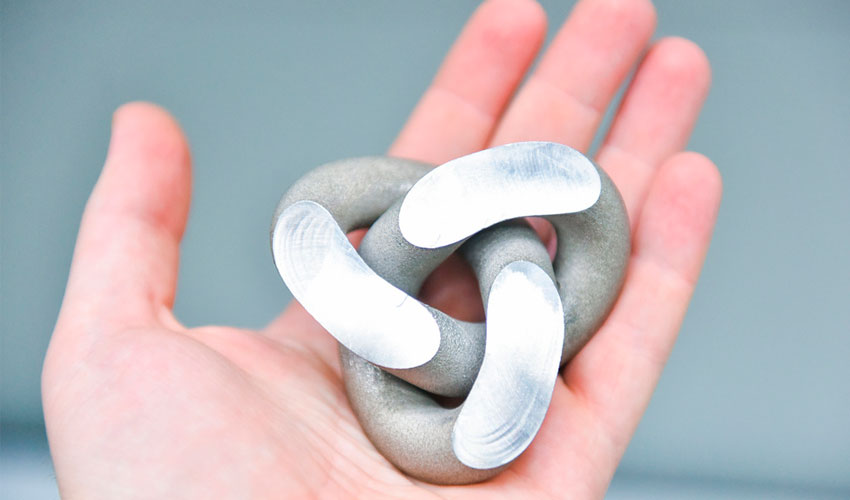
In Russia, scientists from the National University of Science and Technology (NUST MISIS) presented their research on a method of producing ultra-high purity alumina (UHPA) capable of doubling the strength of printed aluminum composites In 3D. We would have components similar to the strength of those made of titanium alloy. A material highly prized in the aerospace industry for its weight to strength ratio.
We know that the automotive, aerospace and medical industries are looking for savings in weight, manufacturing time but also cost savings. All reasons that explain their interest in additive metal manufacturing, particularly with titanium, aluminum and steel. Aluminum is a light material that can be easily molded, two essential requirements for a metal to be 3D printed. However, it is not strong and resistant enough. Thus making the use of titanium with a strength six times higher is preferred. Russian researchers have therefore wanted to increase this strength and propose a new method of powder production.
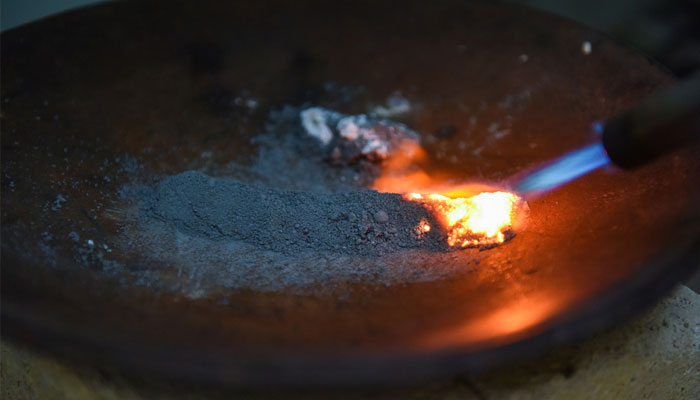
Aluminum is burned in the powder purification stage (photo credits: NUST MISIS)
A purer aluminum powder
The team explains that it uses aluminum granules with a purity of 99.7%. By oxidation, alkaline and acid treatment and thermal calcination at 1450 ° C, the granules are converted into aluminum hydroxide. At each stage of the process, the researchers check the impurities of the oxide, especially those of iron and potassium, which have proven to be the most problematic. With these data, the team then modifies the chemical treatments, washing and calcination, giving a UHPA with a purity of 99.99% and 99.999%.
Although the optimum powder processing conditions remain to be determined, the NUST MISIS team explains that it is already using this material to develop 3D printed prototypes using selective laser sintering. She would have obtained parts with a third of the resistance of titanium. Professor Alexander Gromov explains, “We have developed a technology to strengthen the aluminum-matrix composites obtained by 3D printing, and we have obtained innovative precursor-modifiers by burning aluminum powders. Combustion products — nitrides and aluminum oxides — are specifically prepared for sintering branched surfaces with transition nanolayers formed between the particles. It is the special properties and structure of the surface that allows the particles to be firmly attached to the aluminum matrix and, as a result, [doubles] the strength of the obtained composites“
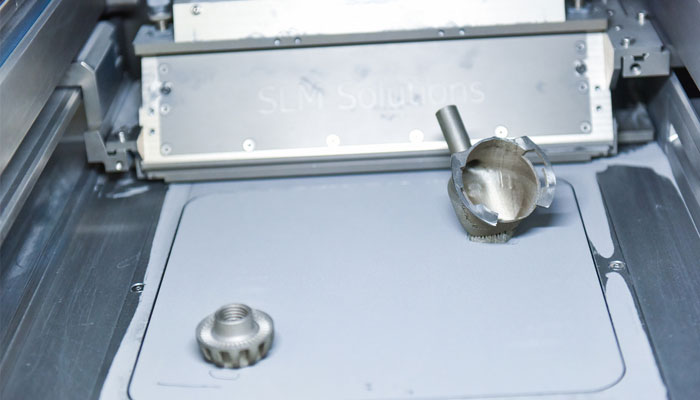
Some pieces printed with UHPA powder (photo credits: NUST MISIS)
One of the main advantages of this UHPA powder production method is its low cost, which makes it possible to maintain a high profitability during the application of the material. You can find all the research work HERE.
What do you think of this 3D printed aluminum? Let us know what you think in a comment below or on our Facebook and Twitter pages! Don’t forget to sign up for our free weekly Newsletter, with all the latest news in 3D printing delivered straight to your inbox!