Scawo3D Enables Freedom in Architecture With Inkjet Concrete Printing
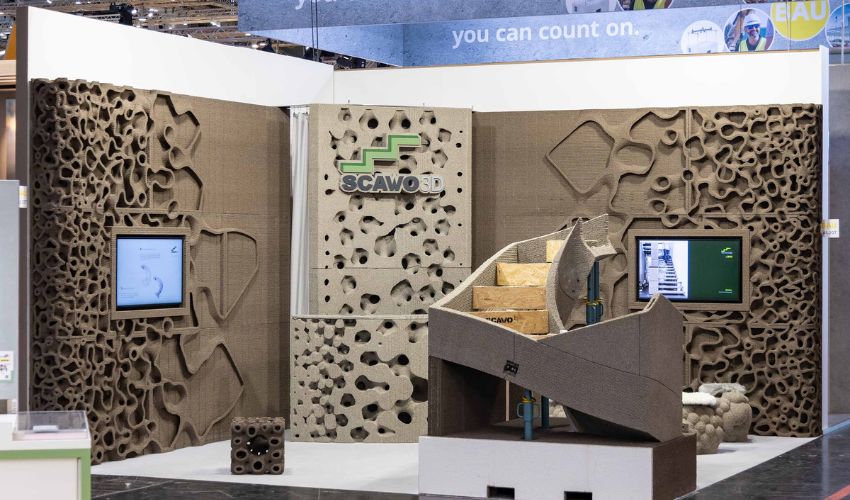
Anyone involved in 3D printing is unlikely to have missed the trend towards 3D printed houses. Innovative companies are continuously driving the establishment of 3D printing in the sector. Extrusion printing is often used in current projects, with huge printing robots creating modern buildings layer by layer. Scawo3D, however, takes a different approach. With its Selective Paste Intrusion technology, the company based in Sarntal in South Tyrol, Italy has found a way to produce concrete components using a powder bed process. The company produces an isotropic concrete with high strengths that is also weatherproof. With this technology, there are no limits to the imagination and even complex geometries can be realized at manageable production costs. We spoke to Philip Schneider from Scawo3D to find out more about the company’s innovative approach.
3DN: Could you briefly introduce yourself and tell us about your role at Scawo3D?
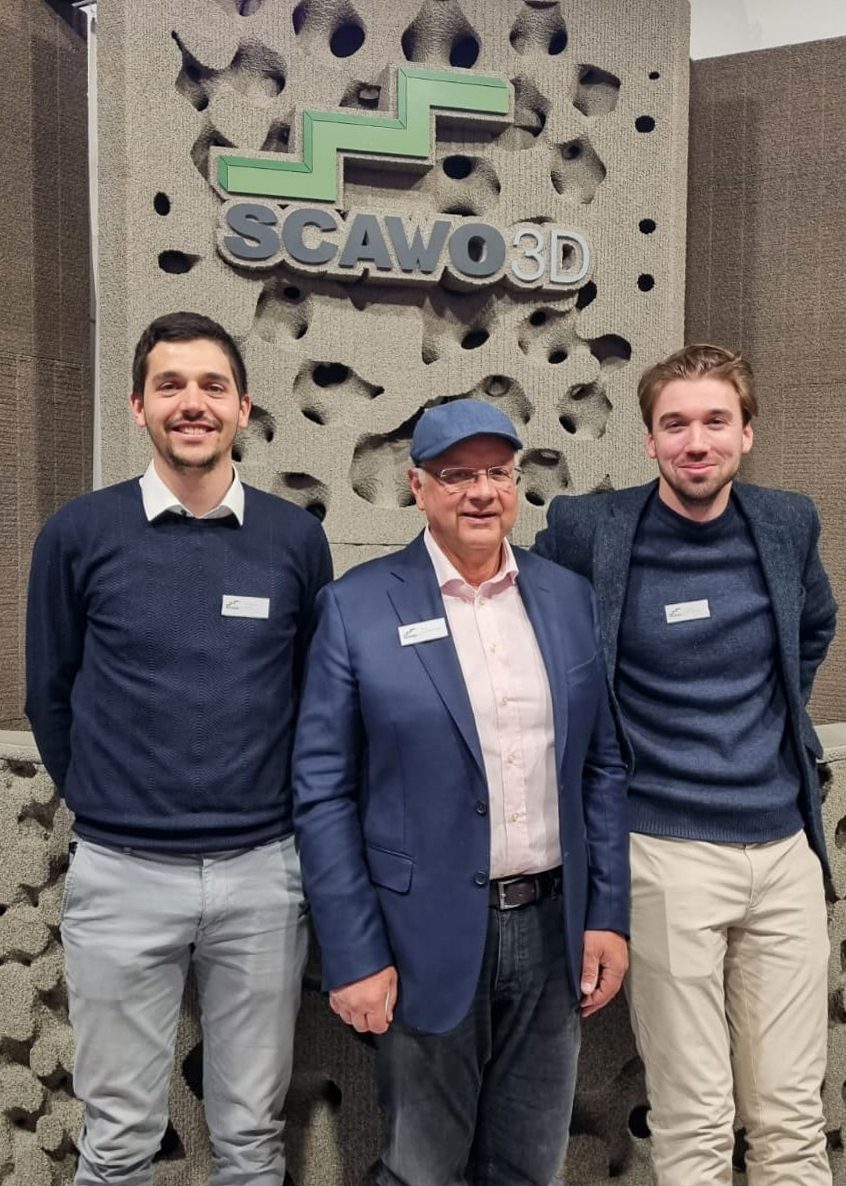
Scawo3D team (from left to right): Andreas Spiess (machine programming), Kurt Wohlgemuth (company owner, inventor) and Philip Schneider (architecture & computational design) (photo credits: Scawo3D)
Hi, I’m Philip Schneider, I studied architecture with a focus on computational design and digital fabrication at the Technical University of Munich. I came to concrete 3D printing and Scawo3D at the beginning of 2022 through the design of a 3D printed pedestrian bridge during my studies, which was finally realized together with Scawo3D.
Scawo3D is the inventor of the world’s first print head for cement paste for a new process for concrete 3D printing called Selective Paste Intrusion (SPI for short). We are the developer and sole manufacturer of this print head as well as a service provider in concrete 3D printing. We are constantly developing and optimizing the process in order to provide our customers with the best possible machines and to make our service more accessible in terms of price.
In the company, I am responsible for architecture and computational design, i.e. I deal with potential applications of the SPI process for the construction industry. As our process makes it possible to realize even the most complex geometry in concrete, there are increased demands on the software used for modeling and planning. It is also my responsibility to ensure that we are equipped with software for modeling complex geometries and that we develop our own solutions for certain applications. For example, we are currently working with the companies Skeno GbR and Timo Harboe ApS on a plugin based on Rhinoceros and Grasshopper for planning complex free-form staircases.
3DN: Why did you decide to implement 3D printing?
Scawo was originally a process patented by us for the production of CNC-milled formwork made of EPS for reinforced concrete stairs. After some time, however, the inadequate fire protection class of EPS prevented it from being used more widely in the construction industry. The company therefore decided to develop a 3D printing process that could be used to produce concrete with the highest fire protection class. From this point on, the project was called Scawo3D.
Over the last decade, the SCA process (short for Selective Cement Activation) was first developed, in which a powder bed of dry mortar is selectively activated. However, only material properties that were insufficient for load-bearing parts could be achieved. Finally, after further development, we arrived at the SPI process, with which we started production in mid-2022. During development, the staircase formwork remained the test object. The idea was that stairs combine both complex geometries and static requirements. Once the staircase worked, we thought, the process could also be used for other objects. Fortunately, we can now say that this train of thought was correct.
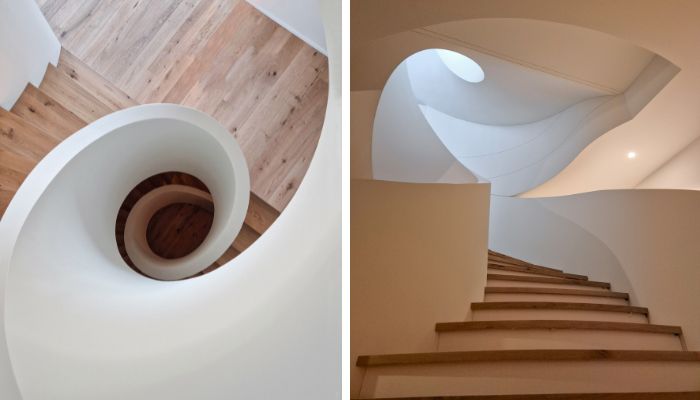
Completed staircase (photo credits: Tschanen/André Wäspi).
3DN: Could you explain your SPI process in more detail?
SPI is a new process for 3D concrete printing. It differs from the previously known extrusion 3D printing, which is often used directly on the construction site. Our system is stationary and based on a powder bed. The principle works in the same way as other powder bed processes, such as the SLS process for 3D printing of plastic. The only difference is that our powder bed is filled with aggregate and concrete or mortar is printed.
During the printing process, the powder bed is filled layer by layer. Loose aggregate and cement paste are alternately applied to each layer. The cement paste, consisting of cement, water and superplasticizer, is selectively applied by our print head with several hundred nozzles and binds the aggregate locally. A new layer of loose grain is then applied and the process is repeated until printing is complete. During the entire printing process and curing, the loose grain serves as a formwork for the printed parts. This allows us to print any geometry without restrictions due to overhang angles or cavities.
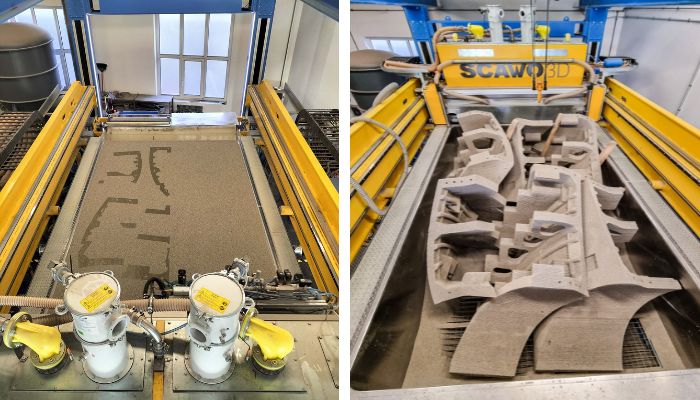
Left: The 4 x 2.5 x 1.5 m pressure bed during the production of the staircase formwork. Right: Formwork elements for a 3.5 m high flight of stairs (photo credits: Scawo3D)
The construction chamber of our large printer has a capacity of 15 cubic meters with dimensions of 4 x 2.5 x 1.5 meters and currently works with a layer height of 3 millimeters. This combination of low layer height and a large number of nozzles enables us to produce concrete components with a very fine resolution of 3 millimeters for construction. Despite the high resolution, we still produce relatively quickly. We can print 15 cubic meters in eight hours. However, further machine optimization will soon reduce this to four hours.
As the resulting material has similar properties to standardized concrete of strength classes C25/30 – C60/75, the technology can be used in a wide range of applications. The high compressive strength enables the use of SPI-printed parts with a load-bearing function, which can also be exposed to the weather in our latitudes. This means that components such as load-bearing walls and vaulted ceilings as well as facades can be made. Of course, objects for indoor and outdoor use, such as garden furniture or sculptures, can also be produced.
3DN: What are the advantages of inkjet concrete printing compared to extrusion?
Probably the biggest difference between the extrusion process and the SPI process is that our process is significantly less complex. On the one hand, this is because we manufacture exclusively in the factory – at least for the time being – and not directly on the construction site. This can be seen as an advantage or a disadvantage. In any case, the advantage is that we work under constant conditions, i.e. we don’t have to adapt the machine or material to different environments with fluctuating temperatures or humidity. The material we print with is therefore simple and contains only cement, water and, apart from a small amount of superplasticizer, no chemicals. This is also made possible because the time from layer to layer is always the same – just a few seconds. The open time of conventional cement is therefore perfectly adequate.
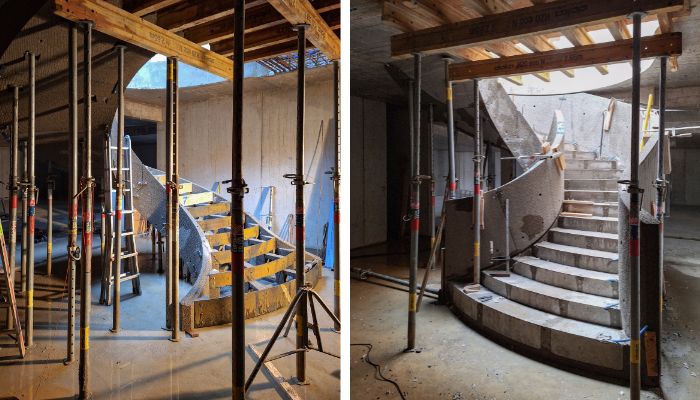
Assembly of the staircase formwork on the construction site (photo credits: Skeno/Scawo3D)
The next advantage results from the consistent time from layer to layer: no matter how complex the geometry to be printed is or how full our build space is – the printing time for a print of 15 cubic meters always remains the same. We can therefore control the price with the capacity utilization of a build chamber. Last but not least, production in the factory has the advantage that the technology is also suitable for building in existing buildings. Here you often come across building sites that are difficult to access. With the SPI process, there is no need for space on the construction site for a large printer gantry; instead, the parts can be dimensioned to suit the construction site. In summary, “inkjet concrete printing” simply gives the designer more freedom.
3DN: What have been the most impressive projects you have completed with 3D printing so far?
I would like to mention two projects here: “Bridge the Gap” was developed in collaboration with the Collaborative Research Center “Additive Manufacturing in Construction” (AMC TRR 277) and the Technical University of Munich. The project was the first to demonstrate how concrete 3D printed in a powder bed can serve as a supporting structure. It is a prototype for a pedestrian bridge with load-bearing spans of 5 x 2.5 meters, which was printed in 21 parts and then joined dry, i.e. without mortar or other compensating material in the joints. Design details for the integrated tension elements were also considered at the planning stage, also without a permanent bond. This configuration meant that the entire bridge could be assembled within one day and assembled and dismantled several times without having to damage or destroy any parts. The project shows how to use a material effectively – concrete has high compressive strength but only low tensile strength – and how to do so in a single-origin material to facilitate recycling or downcycling.
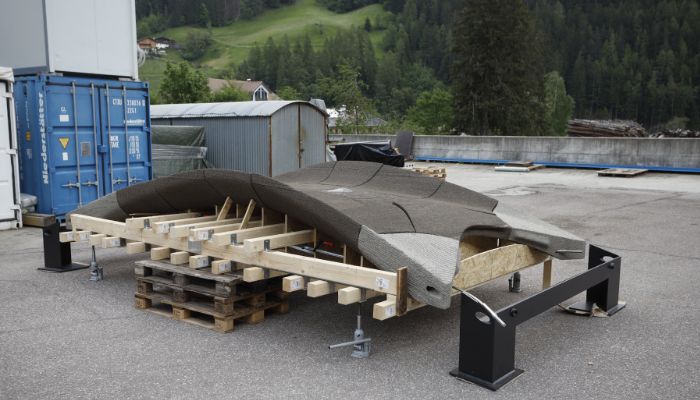
First assembly of the bridge on a specially developed substructure in Sarnthein (photo credits: AMC TRR 277 / Ema Krakovska)
The second project, the H. staircase, is the largest staircase to date that we have made with our 3D-printed formwork: A free-form staircase with an elliptical floor plan and a diameter of more than three meters over two floors. The construction company Tschanen AG from Switzerland contacted us because the alternatives would have exceeded the available budget. Thanks to good cooperation between the planners, the construction company and us as producers, we were also able to prove with this project that the SPI process is suitable for various applications. A particular advantage in this project was the simple transportation of manageable parts – in contrast to the heavy transportation of an entire prefabricated staircase – and the rapid assembly on site within a few days. While Scawo3D was still assembling the first flight of stairs, Tschanen AG was already well prepared for the installation of the second flight and completed it just as quickly. The 3D-printed parts also provide a good base for the subsequent surface treatment: the plasterer was able to apply the plaster directly to the formwork without having to level out any major unevenness.
3DN: What can 3D printing offer architecture? And where are the challenges?
Until now, concrete 3D printing processes were limited in their areas of application. Either not all geometries could be realized or the strength and weather resistance were significantly impaired by the process-related layer structure or the material. We were able to overcome both problems with the SPI process. This results in complete freedom of form during the design process, which not only allows components to be conceived differently aesthetically but also structurally. This means that concrete components can now be statically optimized to a degree that was previously only possible with complex formwork work. For these reasons, I believe that 3D printing has the potential to trigger a revolution in architecture – inspired by construction methods that have been forgotten for some time.
The interplay of material properties and freedom of form allows solid construction to be rethought and optimized, for example, towards less complex, yet still thermally insulating and load-bearing components made from a single material. Geometrically, these parts can certainly be more complex than before, but with fewer structural layers. As a result, buildings can be constructed that are more sustainable and will require less maintenance in the future due to their increased durability. The statics of vaulted ceilings could also be exploited to the full using computer-aided methods, thereby significantly reducing the amount of material used in building ceilings, which incidentally make up the largest proportion of material in a building. One could start by enhancing the sometimes somewhat dull German cityscape here and there with ornamental façades or art on buildings.
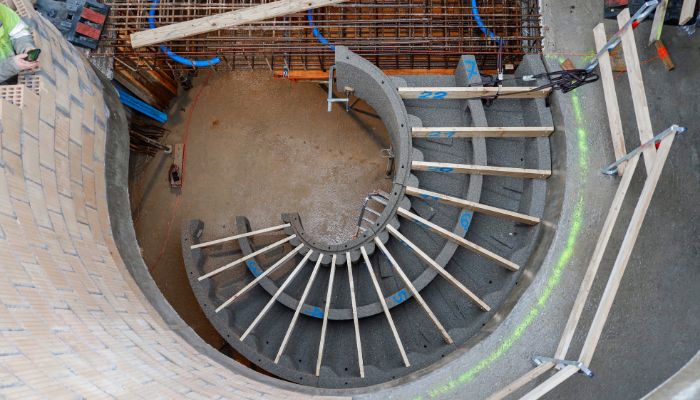
Assembly of the staircase formwork on the construction site: Fully installed first flight of stairs without balustrades (photo credits: Skeno/Scawo3D)
The biggest challenge, on the other hand, is to put this relatively new process into practice on a larger scale. We have been receiving requests for and accepting design or art objects and manageable constructions such as stairs for some time now. However, we see more potential in the SPI process. Although hydraulic binders were already known to the Romans, it took until the 19th century and industrialization for cement to become more widely accepted. What I am trying to say is that we are at the beginning and it takes time.
Additive manufacturing in construction has gotten a good start. There is a shortage of skilled workers, while more living space needs to be created quickly, and this is finally giving more attention to the urgently needed discussion about sustainability. In principle, the conditions are in place for a new technology that can be used to build differently and faster. The downside is that the industry, especially in Germany, is still structured by standards that are not very transparent and are based on a body of knowledge that does not necessarily do justice to today’s requirements, but also to today’s possibilities in architecture.
Through projects and research results, the Technical University of Munich showed where and how additive manufacturing can be used most effectively in the construction industry. So a lot is happening in research. And it is also slowly becoming apparent that some of these findings are being transferred into practice, for example through initiatives such as “Building Type E” in Germany. By relaxing the standards, planners and building owners should be given more freedom to build more simply, more resource-efficiently and, in the best case, more cost-effectively.
Nevertheless, we are waiting for customers outside the research sector who show the courage and, initially, the financial willingness to embrace a new technology such as the SPI process. We have demonstrated and will continue to demonstrate that large-scale construction in the form of load-bearing components is possible. You can find out more about Scawo3D on our website.
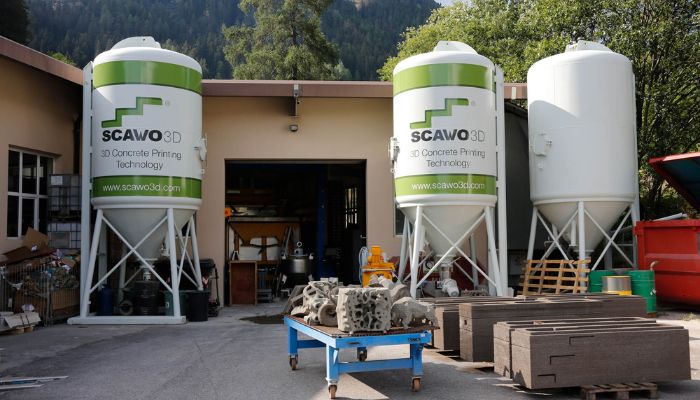
Production of Scawo3D in Sarnthein, South Tyrol (photo credits: Scawo3D)
What do you think of Scawo3D? Let us know in a comment below or on our LinkedIn, Facebook, and Twitter pages! Don’t forget to sign up for our free weekly Newsletter here, the latest 3D printing news straight to your inbox! You can also find all our videos on our YouTube channel.
*Cover Photo: Scawo3D trade fair stand at BAU 2025 in Munich (photo credits: Skeno/Scawo3D)