Sandia Labs Uses 3D Printing for Weapons Systems
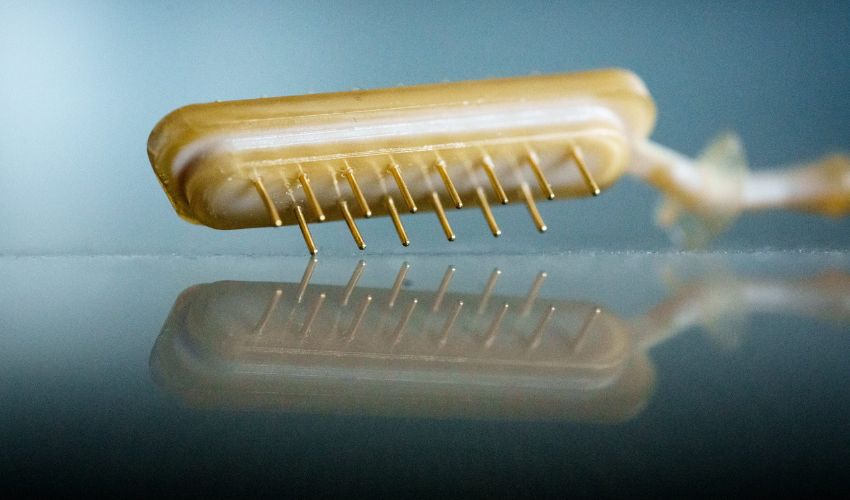
Whether for tanks, propulsion systems, helmets, or on-ship printing, additive manufacturing is slowly but surely gaining a foothold in the defense industry. And new applications are being discovered nearly every month. For example, Sandia National Labs has announced that it is using 3D printing and other technologies to transform how it develops custom electronic connectors for weapons systems.
Sandia National Laboratories is a multimission laboratory operated by Sandia LLC, a wholly owned subsidiary of Honewell International, for the U.S. Department of Energy’s National Nuclear Security Administration. The lab receives funding from numerous sources and is at the forefront of research in areas like nuclear deterrence, global security, energy technologies and more. It also has experience with additive manufacturing. Last March, we told you about its project with Oregon State University to create a 3D printing construction material that could trap carbon dioxide.
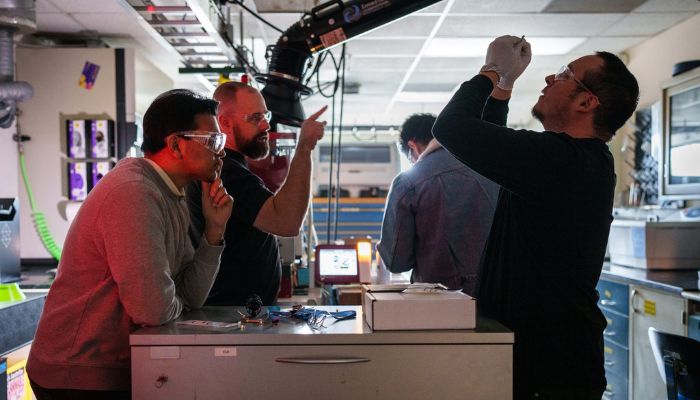
Sandia National Laboratories engineers analyzing PEEK inserts (photo credits: Craig Fritz/Sandia National Laboratories)
This particular project, the Rapid Development Connectors program, is however completely different as it is dedicated to using advanced manufacturing techniques to help develop connectors for weapons systems, notably nuclear weapons. The five-year National Security Administration-funded project seeks to build a team that is capable of fabricating and delivering functional connectors in less than four weeks, in contrast to the current year or longer. All while ensuring that the quality of the resulting components remains superior.
Sandia Labs Makes 3D Printed Electronic Connectors for Weapons Systems
It may no longer be the Cold War, but nuclear deterrence, the often controversial principle that a country can retaliate against a nuclear attack thus preventing any in the first place, continues to be an important part of many governments’ defensive strategies. As such, it is critical to ensure that a country’s nuclear arsenal remains in good condition. With the US holding the second-largest stockpile of nuclear warheads (an estimated 3,748 in September 2023 as compared to Russia’s 5,580), it is a particular challenge in the country. Electrical connectors are a key part of this maintenance as these types of components are critical to maintaining the safety of the nuclear weapons as well as triggering them if necessary.
But where does 3D printing come in? Well, the Rapid Development Connectors program has quickly seen the value of additive manufacturing in a number of ways. One is as a complementary technology.
In a recent press release from Sandia National Laboratories, it is explained that co-locating manufacturing techniques has shown the value of combining 3D printing with injection molding for low-volume production of parts. The benefits of using 3D printing to create more cost-effective molds is well-established. Namely, because 3D printed molds rather than machining them allows for a quicker turnaround as well as the possibility for more design iterations. The lab has also looked into creating hermetic seals made with additively manufactured glass.
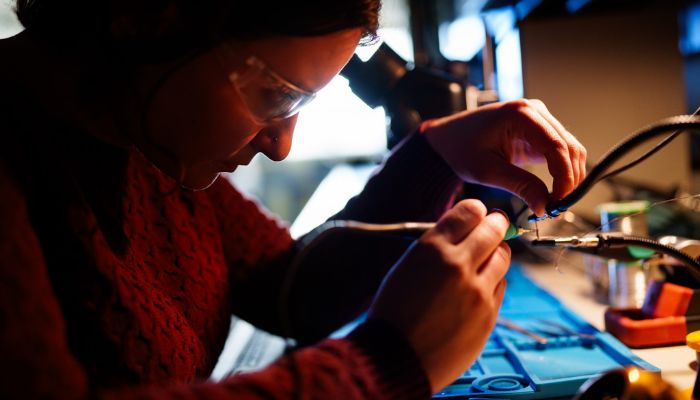
An electrical engineer working on socket contacts as part of Sandia’s Rapid Development Connectors Program (photo credits: Craig Fritz/Sandia National Laboratories)
Those who have benefited from these electronic connectors include those working on W93 weapons, a nuclear warhead expected to replace the W76 and W88 warheads on United States Navy submarines from 2034 on. Leaving it clear that it has been a success. It also seems that there are plans to incorporate the program into the budget for new weapons programs at the end of its current NNSA funding. You can learn more about it in the press release HERE.
What do you think of these 3D printed electronic connectors for weapons systems? Let us know in a comment below or on our LinkedIn, Facebook, and Twitter pages! Don’t forget to sign up for our free weekly newsletter here for the latest 3D printing news straight to your inbox! You can also find all our videos on our YouTube channel.
*Cover: A PEEK part made using a 3D printed molding tool (photo credits: Craig Fritz/Sandia National Laboratories)