SANDHELDEN Turns to Binder Jetting and ExOne for its Sustainable, Sand Projects
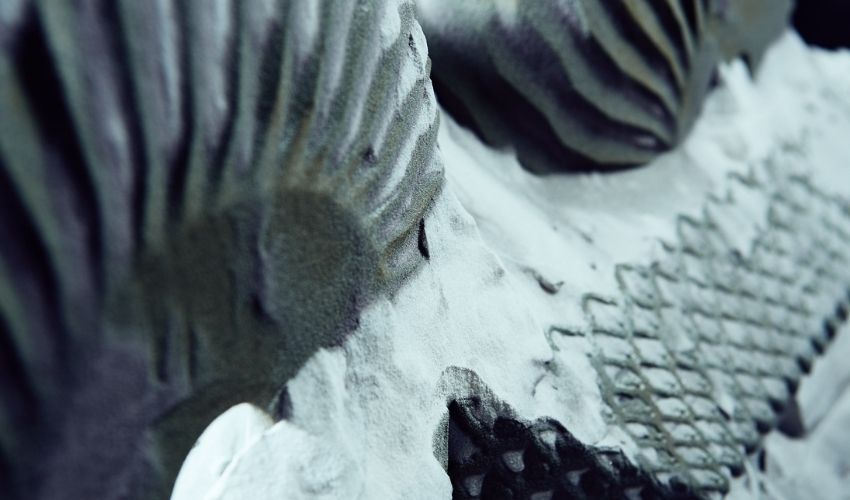
Sand binder jetting is increasing in popularity when it comes to end-use parts. This is due to a variety of factors. For one, binder jetting is one of the fastest additive manufacturing technologies and sand binder jetting, in particular, is even faster than its metal counterpart, as it involves significantly less post-processing. Additionally, using sand as a building material is more environmentally-friendly and cost-effective than many traditional options. For these reasons, among others, SANDHELDEN, a global leader in the production of 3D printed design elements made of sand, has turned to the leader in sand binder jetting, ExOne, to create its products.
SANDHELDEN is known for its sustainable bathroom products, including sinks and bathtubs, created using sand 3D printing. Since 2016, the company has been working with the sand binder jetting experts at the 1,800 m² ExOne Adoption Center in Gersthofen, in the heart of Germany. Though ExOne sand 3D printing is perhaps best known for metal casting molds and cores or other tooling purposes, this partnership has allowed both companies to advance the strengths of the technology.
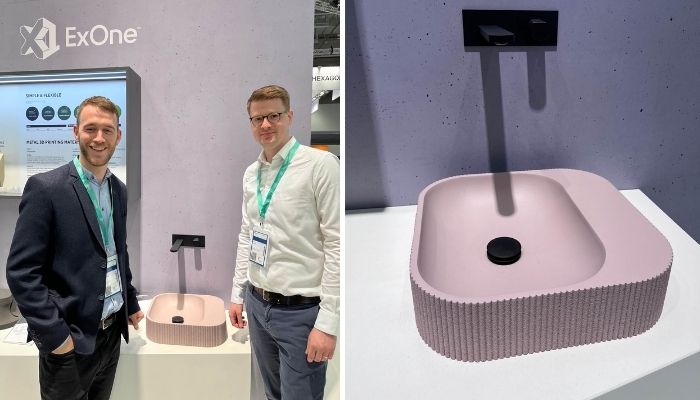
SANDHELDEN showed their creations at ExOne’s booth at Formnext (photo credits: SANDHELDEN)
SANDHELDEN Uses the S-Max 3D Printer from ExOne for its Sand Binder Jetting Needs
But how are durable, waterproof sinks and bathtubs made from sand? As with any 3D printing process, it starts with a CAD model, a 3D image that serves as the basis for the printed molds. This is transferred to one of the 3D printers at the ExOne adoption center.
The S-Max 3D printer from ExOne is preferred as it allows for a number of benefits for SANDHELDEN, including efficient and flexible batch production, high productivity, and a customizable platform. All of which are crucial in the creation of SANDHELDEN’s sand products. Additionally, the S-Max 3D printer is equipped with both a double job box and a Jobmatic, which allows for automatic post-processing. The binder jet 3D printing process begins with the base plate of the job box, where a recoater applies a thin, even layer of sand before the printhead distributes the binder precisely onto the points which will be joined together to create the printed part. In binder jetting, the binder, furan in this case, surrounds each individual layer of sand. The plate is lowered so that the steps can be repeated until the mold has been created layer by layer. UpPon completetion, the job box automatically moves out of the printer.
The large job box of the S-Max system allows for the simultaneous production of various products – of the same series or of multiple designs all at once. For example, up to 48 molds of the Basin “S-01“- SIMBIOSIS Collection” product can be printed in a single printing procedure on an S-Max. After 3D printing, the SANDHELDEN designs are infiltrated with resins and then further coated to create unique shapes that are waterproof and durable enough to withstand the daily use of bathroom environments.
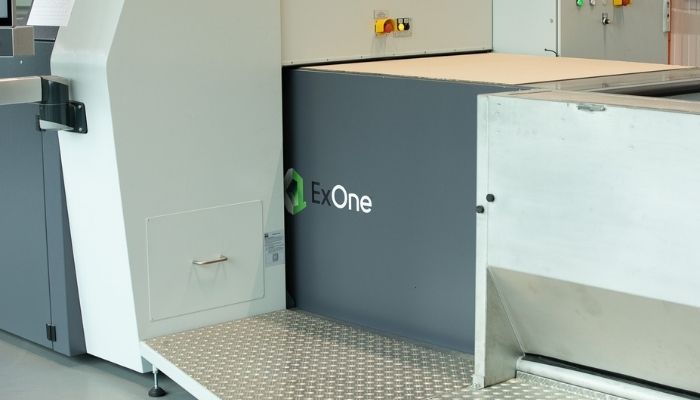
ExOne’s S-Max 3D printer is used to create SANDHELDEN’s projects (photo credits: ExOne)
Sand binder jetting is the perfect production method for these pieces for a variety of reasons. First, SANDHELDEN is able to take advantage of the flexibility of the technology in terms of materiality, size, and geometrical freedom. They specifically note that ExOne’s technology helps them create geometrically complex shapes that are not possible with conventional production processes. Additionally, binder jetting allows them to operate more sustainably, a key benefit for the environmentally –conscious company. This is not just through reducing waste by only building material that is needed, but also because the company is able to use silica sand as the base for the binder jetting process. This natural material can be exclusively sourced from regional suppliers in Germany and reused for future builds if it was not bound into a design during the initial production process.
“We’re familiar with traditional foundry applications for our sand 3D printers, but are excited to see the new opportunities companies are discovering with the technology,” commented Eric Bader, Managing Director at ExOne. “We’ve partnered with SANDHELDEN from the beginning to enable this innovative use of the binder jetting for consumer products and we’re proud to see their business prospering on the values of unique product offerings, quality, and sustainability.” You can learn more about ExOne’s sand binder jetting solutions HERE.
What do you think of SANDHELDEN’s use of ExOne’s binder jetting machines to create their innovative sinks? Let us know in a comment below or on our Linkedin, Facebook, and Twitter pages! Don’t forget to sign up for our free weekly Newsletter here, the latest 3D printing news straight to your inbox! You can also find all our videos on our YouTube channel.
*Cover Photo Credits: SANDHELDEN