Rodin Cars 3D Prints A Sequential Titanium Gearbox

New Zealand racing car maker Rodin Cars is implementing the use of metal additive manufacturing to produce parts for its new hypercar, the Rodin FZERO. Thanks to the DMP Factory 500 3D printer, the company was able to design its tailor-made sequential gearbox with a hydraulically operated differential. Made of titanium, the component is more compact, light, strong, and durable.
The automotive industry has used additive manufacturing for years. Initially used for prototyping, additive manufacturing is now recognized as a method for producing finished and spare parts, offering more flexibility to manufacturers around the world. More specifically, additive manufacturing makes it possible to produce personalized parts, on-demand and locally, thereby reducing manufacturing times and costs. This is surely what prompted Rodin Cars to invest in a 3D Systems machine. David Dicker, the founder of the New Zealand-based company, says, “3D printing allows us to design and create components otherwise unachievable using traditional methods of manufacturing. With the Rodin FZERO gearbox, we had specific criteria we wanted to meet in terms of weight and durability. Because of the size and quality required for such a large component, it was only possible to print it on 3D Systems’ DMP Factory 500 machine. We couldn’t source another AM supplier who was able to offer a similar solution for our needs — the print quality, volume capacity, testing facilities in Leuven, and continued technological support.”
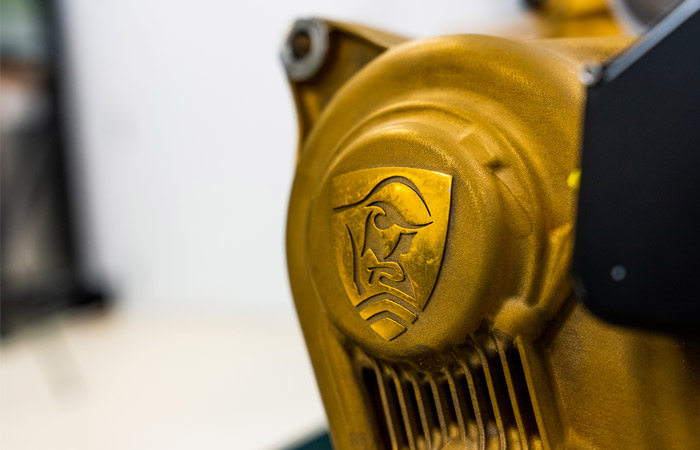
Thanks to additive manufacturing, Rodin Cars has designed a tailor-made gearbox. (Photo Credit: Rodin Cars)
Rodin Cars Creates Compact Gearbox Thanks to 3D Printing
After developing his first racing car in 2019, Rodin Cars wanted to go further in the design of a new vehicle. After 18 months of design work in collaboration with the British engineering company Ricardo, Rodin Cars imagined a titanium gearbox with new gear ratios. Containing internal galleries and thin-walled bearing structures, this gearbox could not be manufactured using traditional methods, at least not so quickly. It would have been cast in magnesium and could not have stood up to the performance demands of motor racing. The manufacturer, therefore, approached 3D Systems in order to bring this innovative project to life.
Rodin Cars invested in an industrial machine, the DMP Factory 500, which offers a generous 3D printing volume of 500 x 500 x 500 mm. 3D printed from titanium, the gearbox is said to weigh 68 kilos and has walls just 2mm thick. Note that the part was printed in only one go, significantly reducing the manufacturing process. Kevin Baughey, segment leader, Transportation & Powersports at 3D Systems, concludes, “As a high-tech, high-performance car constructor, Rodin Cars delivers unparalleled vehicles to their customers. This is a shining example of how additive manufacturing not only enables parts to be produced that couldn’t be created through conventional methods, it is also delivering a lighter, more durable, beautiful vehicle. It’s the blending of the art of design with the science of hyper-performance cars and motorsports.”
What do you think of Rodin Cars’ 3D printed gearbox? Let us know in a comment below or on our Facebook and Twitter pages. Don’t forget to sign up for our free weekly newsletter, with all the latest news in 3D printing delivered straight to your inbox!
Cover Photo Credit: Rodin Cars