RMIT Research Team Develops New Method for Designing Implants Using Bioprinting and Injection Molding
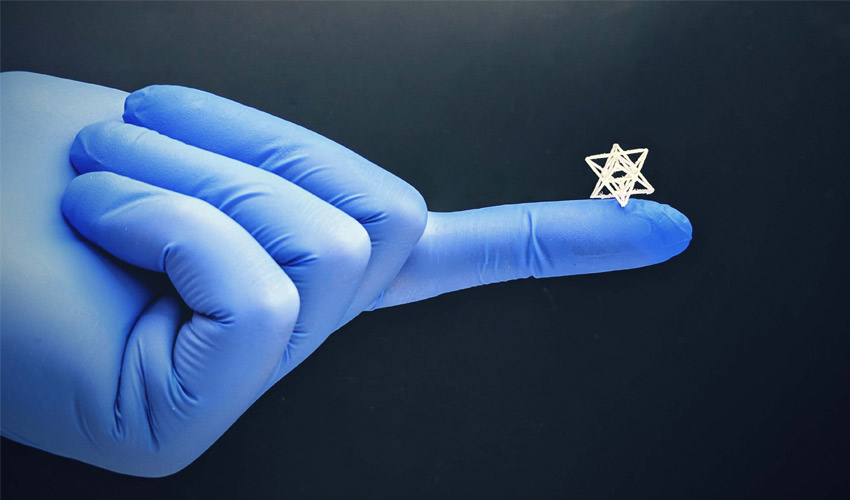
At the Royal Melbourne Institute of Technology (RMIT University), a team of researchers, along with doctors from St Vincent’s Hospital in Melbourne, have developed an innovative method for bioprinting medical implants. Instead of designing scaffolds on which cells will multiply, they 3D printed molds with cavities into which they injected biocompatible materials. Once the mold was dissolved in water, all that would remain would be this bio-scaffold. This technique, dubbed Negative Embodied Sacrificial Template 3D (NEST3D) should be compatible with a wide variety of materials but would especially allow the creation of microscopic structures.
In tissue engineering, the use of bioprinting is becoming more and more common as it can design of devices that promote the reconstruction of bones or muscles. Generally, 3D printed scaffolds are implanted in a patient’s body to encourage cells to reproduce and thus heal injuries which can range in severity. One of the obstacles that exists today is the size of these structures and their complexity: using scaffolds in the micron range remains complicated. Why not adopt a more indirect approach?
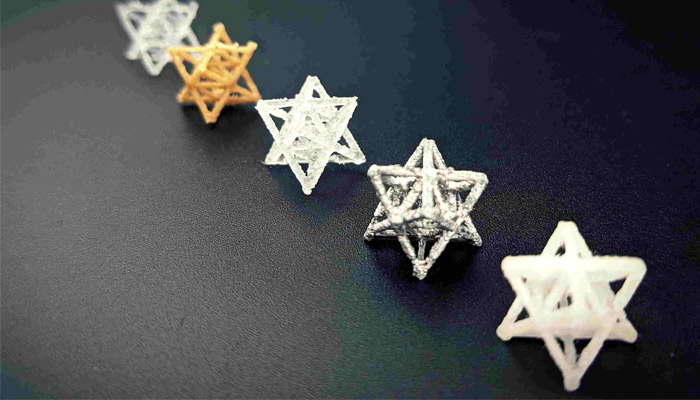
Using their method, researchers can design much more complex and smaller structures (photo credits: RMIT University)
This team of researchers decided to 3D print a mold with complex, intricately-patterned cavities. They were then able to inject biocompatible materials into these holes that form a welcoming scaffold for any cell. The researchers explain that they used a PVA glue to make the mold and injected biocompatible materials into it. Once hardened, the mold is immersed in water, which completely dissolves the glue. All that remains is the intricately shaped scaffold, as small as a fingernail.
Stephanie Doyle is one of the researchers in this study. She adds, “The advantage of our advanced injection moulding technique is its versatility. We can produce dozens of trial bioscaffolds in a range of materials – from biodegradable polymers to hydrogels, silicones and ceramics – without the need for rigorous optimisation or specialist equipment. We’re able to produce 3D structures that can be just 200 microns across, the width of 4 human hairs, and with complexity that rivals that achievable by light-based fabrication techniques.”
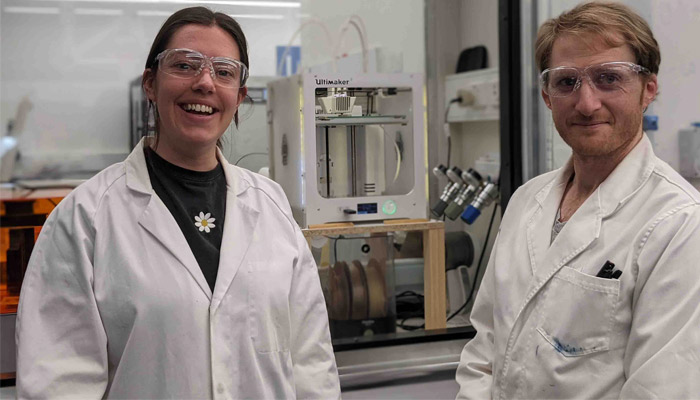
Stephanie Doyle and Dr. Cathal O’Connell in front of the 3D printer (photo credit: RMIT University)
This method could be more cost-effective, easy and scalable because it would be possible to use any FDM 3D printer on the market. In bioprinting, when it comes to designing scaffolds, the size of the machine’s nozzle is crucial: it must be large enough to extrude the ink. This will inevitably affect the final size of the part, limiting the possibilities. However, by 3D printing a mold, much thinner spaces could be attained.
After testing their scaffolds, the researchers say they are safe and non-toxic. They now hope to speed up cell reconstruction by testing different designs and possibilities. In any case, it’s a first step for doctors who could benefit from a more accessible solution. Professor Claudia Di Bella, an orthopedic surgeon at St. Vincent’s Hospital, concludes, “A common problem faced by clinicians is the inability to access technological experimental solutions for the problems they face daily. While a clinician is the best professional to recognize a problem and think about potential solutions, biomedical engineers can turn that idea into reality. Learning how to speak a common language across engineering and medicine is often an initial barrier, but once this is overcome, the possibilities are endless.” Find more information on the university’s website HERE and in the video below:
What do you think of this new research for bioprinting implants? Let us know in a comment below or on our Facebook, Twitter and LinkedIn pages! Sign up for our free weekly Newsletter here, the latest 3D printing news straight to your inbox!