Rilsan® Polyamide 11 is used to manufacture a turbine in direct contact with drinking water
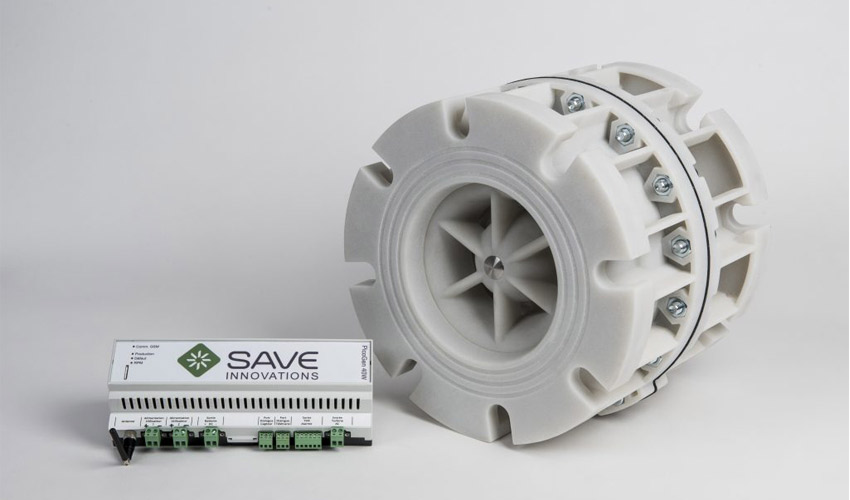
When it comes to product development, additive manufacturing has an important role to play, allowing for quicker iterations, leading to shorter production times. Many design offices have equipped themselves with 3D printing solutions to accelerate innovation and bring to the market differentiated products faster. This is the case of Novall, a French company specialising in the design of industrial products: 3 years ago it opened an entity dedicated to additive manufacturing, and today uses this technology to design and produce small series adapted to the needs of its customers. The company thus offers tailor-made solutions that would be too expensive to produce using injection molding for example. The entity works with a powder sintering process and Arkema’s Rilsan® Polyamide 11, a 100% bio-source material based on castor oil. The unique chemical and mechanical properties of this material allow Novall to design ACS (French Certificate of Sanitary Compliance) certified components that are in direct contact with drinking water, such as hydrogenators or filtration solutions.
Novall first invested in an additive manufacturing machine a few years ago as an alternative to outsourcing, in order to produce more quickly and locally. Novall is working with Save Innovations, a company that provides electrical power to equipment used to modernize drinking water networks. In France, the network has a lifespan of about 50 years, with a leakage rate of 20%: its modernization is therefore an important issue. This is why it decided to design Picogen, a patented pico-turbine consisting of a turbine and regulator that optimizes electricity production. Therefore, Picogen enables the production of the electricity needed to supply the equipment used to modernize drinking water networks. The solution was installed in 2018 on the Eau de Paris’ network.
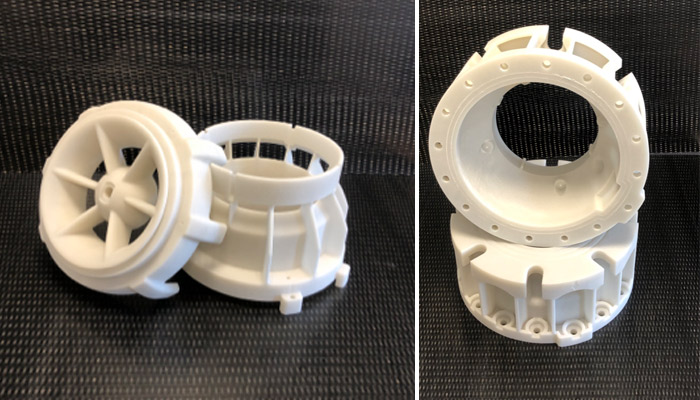
Picogen is a patented pico-turbine consisting of a turbine and regulator that optimizes electricity production
The use of Rilsan® PA11 in turbine design
After carrying out some tests on different 3D printing processes, the company opted for selective laser sintering, and in terms of materials, PA11 for its mechanical and chemical properties. The material has very low water absorption properties, as well as excellent mechanical and resistance properties: it is ductile and shows a great impact resistance. It is also compatible with direct contact with drinking water while PA12 for example requires a special coating and revaluation. Ronald Bosch, CEO of Novall, explained: “We were hesitating between PA12 and PA11, but in various tests we found that PA11 performs better in water.” A material that proved to be ideal for the series production of a connected pico-turbine.
The turbine body was 3D printed by Novall, using glass-bead filled Rilsan® Polyamide 11. The part measures 350 x 400 mm, weighs 8 kilos and has been ACS certified (Attestation de Conformité Sanitaire in French) so that it can be used in direct contact with drinking water. ACS, issued by a laboratory authorized by the French health service, enables the evaluation of the suitability of a material which comes into contact with drinking water through rigorous screening of the formulation.
By using Arkema’s material, Novall was able to design a turbine with high chemical and mechanical performance, capable of withstanding the constraints of its environment over time. For example, it ensures optimum sealing and the glass beads increase ion exchange. Ronald Bosch continues: “This part was made according to a specific process and material, we could not have used this PA11 with traditional manufacturing processes. 3D printing offers many benefits.” Among these is local manufacturing, which reduces the carbon footprint. Additionally, thanks to additive manufacturing, each part is designed as a single block, eliminating assembly constraints, and also facilitating recycling since the part is made of a single material. It should also be noted that Rilsan® PA11 is made from castor oil, a vegetable oil that is more sustainable compared to other materials in the oil industry. Rilsan® PA11 also has interesting refresh rates. In fact, Arkema is one of the 4 founding members of the Pragati project launched in 2016 which was created to enable sustainable castor crop production in India. Since its inception, it has led to a proactive engagement of the castor seed growers and the adoption of better farming practices.
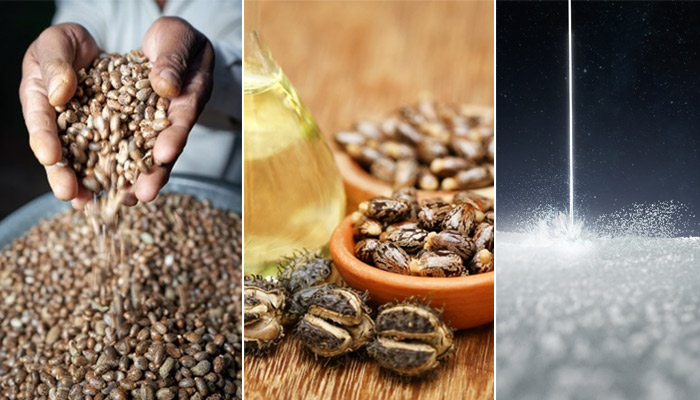
Rilsan® PA11 is made from castor oil, a vegetable oil that is more sustainable compared to other materials in the oil industry
Ronald Bosch concludes: “We were able to develop a manufacturing process with a specific material that meets our application needs in the aquatic field. We have thus obtained ACS certification, a key market advantage that enables our end customers to use our innovative products in complex drinking water systems.” Do you want to know more about Arkema’s Rilsan® PA11? Find more information HERE.
What do you think of Rilsan® PA11’s properties? Let us know in a comment below or on our Facebook and Twitter pages! And remember to sign up for our free weekly Newsletter, to get all the latest news on progress, research and more entrepreneurs in 3D printing sent straight to your inbox!