HP adds highly reusable polypropylene to its range of materials
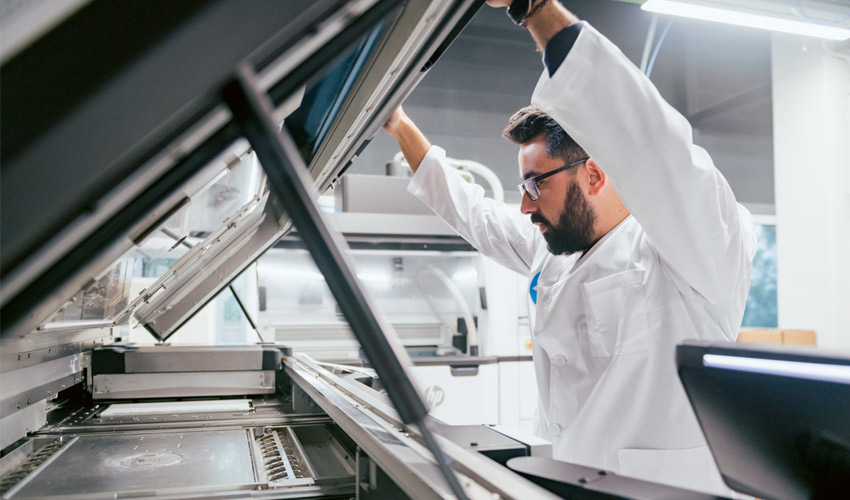
The US additive manufacturing giant, HP has unveiled a new material for its Multi Jet Fusion 3D printing solutions. In collaboration with chemical company BASF, it is developing a powder and highly reusable polypropylene, called 3D High Reusability PP, it is tailored for the 5200 machine range. The material is intended to be versatile, durable, chemically resistant and suitable for industrial applications. This is good news for the additive manufacturing market, given that polypropylene is a very affordable polymer, one of the cheapest in the world. This new powder is the proof that HP is industrializing its technology, and is widening its range of materials as much as possible. The company also took advantage of this announcement to announce two new users of its metal 3D printing technology: the U.S. Army and Cobra Golf.
Highly prized in the injection industry, polypropylene is a semi-crystalline material that presents a number of interesting characteristics for the industry: it is very light, accessible, resistant to chemicals, fatigue, impact and has good insulation properties. Today, it has little presence in the additive manufacturing market because it remains difficult to print with. During extrusion, for example, the user is often confronted with problems of shrinkage and adhesion to the build plate. HP therefore seized the opportunity and entered the powder market – its new PP opens the door to industrial applications for sectors like medical, automotive and consumer goods.
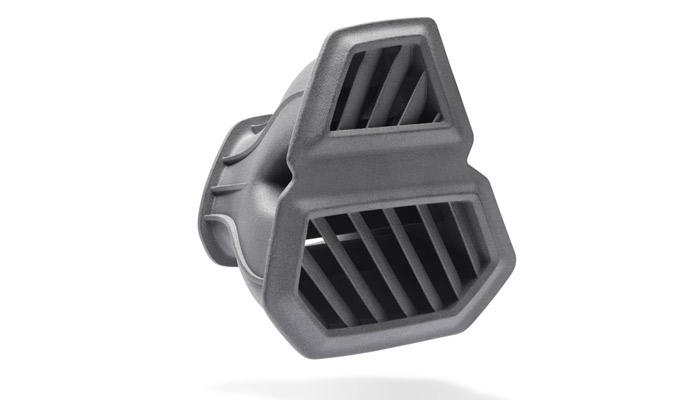
A 3D printed automotive part printed with the highly reusable polypropylene | Credits: HP
Highly reusable polypropylene
Compatible with the HP Jet Fusion 5200 series, 3D High Reusability PP, will offer high productivity while minimizing waste. According to the manufacturer, it is on average 30% less expensive than PA12 – the most commonly used material in HP systems. Additionally, PP offers excellent chemical resistance, low moisture absorption, long-term durability and exceptional welding capabilities with other PP parts. According to HP, the user will be able to reuse up to 100% of the unused powder, given this refresh rate, the goal has been to reduce the waste and the environmental footprint. The manufacturer works hand in hand with partners such as Extol, Henkel, GKN/Forecast 3D, Oechsler and Prototal to test all the characteristics of PP and develop relevant applications.
Ramon Pastor, president of HP 3D Printing and Digital Manufacturing, added: “The response to the COVID-19 crisis is a watershed moment for the industry. HP and its partners have 3D printed more than 2.3 million parts to bridge supply chain gaps, enable local production, and help healthcare professionals on the front lines. As we navigate this new landscape, we continue to execute on our strategy and push innovative new 3D printing materials, solutions, and partnerships forward to help our customers re-open manufacturing and deliver disruptive innovation for the world’s industries.“
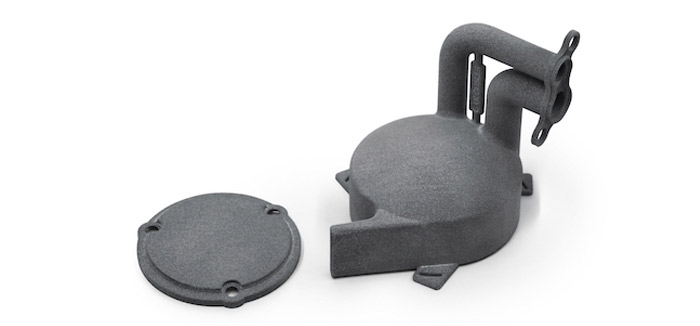
Credits: HP/ Oechsler
Finally, HP is taking advantage of this new development to announce two new users of its Metal Jet technology: the US Marine and Cobra Golf. The Army should use it to produce stainless steel spare parts for its amphibious assault vehicle. As for Cobra, HP technology should be employed to design more efficient golf equipment adapted to the needs of all levels of golfers.
Have you used polypropylene to make parts before? Let us know in a comment below or on our Facebook and Twitter pages! Don’t forget to sign up for our free weekly Newsletter, with all the latest news in 3D printing delivered straight to your inbox!