Resins vs Powders: Which Material Family Should You Choose for 3D Printing?
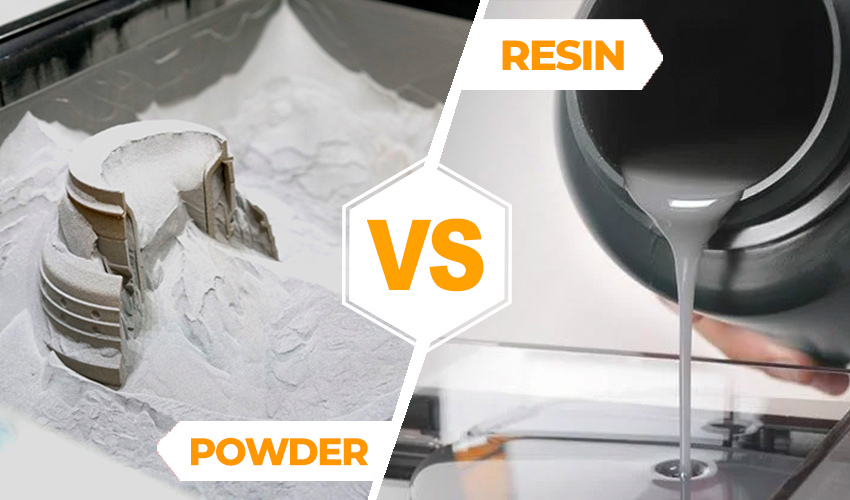
Depending on the intended application and the preferred 3D printing process, different materials can be used, only makes the selection more difficult for the user due to the wide range. Whether plastics, ceramics or even metals, the 3D printing material portfolio can be long and confusing. Therefore, we would like to give a detailed overview that directly compares two families of polymer materials: resins and powders. It should also be noted that although there are a number of powders and resins on the market today, such as metal powders or even ceramic resins, today we will focus only on polymers.
There are two types of 3D printing plastics: thermosets and thermoplastics, with the main difference between these two families being their different behavior when exposed to heat. On the one hand, thermoset plastics decompose when cured and do not reform after cooling. On the other hand, thermoplastics are the most commonly used, and when heated they can assume the desired shape and undergo various melting and solidification processes, with their properties changing slightly each time they are reheated.
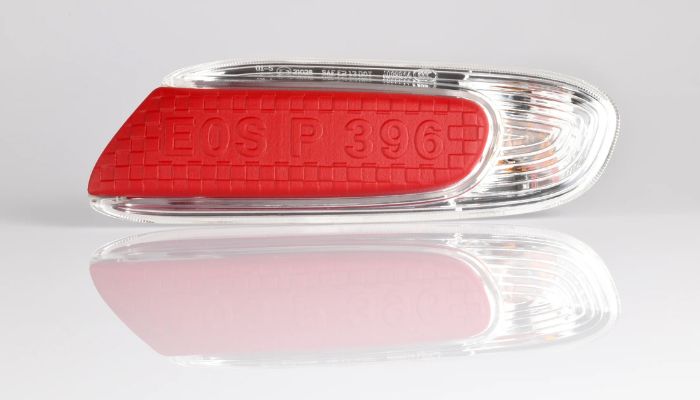
Plastic powders can be used in many areas, e.g. in the automotive industry (photo credits: EOS)
These two families of materials are among the most used in additive manufacturing. For plastic powders, the market is expected to reach $3 billion by 2029 according to the Linker report, and for resins, this value is even estimated to be over $750 billion according to Fortune Business Insights. As you might expect, each family of materials is compatible with different 3D printing processes such as SLS or Multi Jet Fusion for powders, and material jetting or photopolymerization for resins; we’ll go into more detail on these in our article, as well as post-processing, pricing, material characteristics, manufacturers and more!
Features and Properties of Plastic Powders and Resins
3D Printing Polymer Resins
In the current polymer market, there are different resins that, depending on their properties, have different applications in different sectors. The use of resin for 3D printing allows the creation of small objects with great detail. Some of the resins that can be found on the market include:
- Standard resins: These are the cheapest and most wildly used. Additionally, they are easy to find in the market, simple to work with and grind and soft to the touch. However, they are also fragile and can easily break and crack. They are mostly used for rapid prototyping.
- Flexible resins: They are usually used for printing resistant objects that can be bent or compressed. There is also a wide range of flexibilities and the Shore hardness can be individually adapted.
- Water washable resins: As the name suggests, these do not need to be washed off with isopropyl alcohol, but with water, so that finishing is easier. They are low odor and have a dry and less sticky surface.
- Industrial resins: suitable for the manufacture of parts that require a rigid and hard surface. Within the resins we find:
- Temperature resistant resins: capable of withstanding up to 238 ºC. These resins are used for the production of prototypes that require greater detail, precision and high thermal stability.
- Burnout resins are a type of resin that has a high level of detail and a great surface finish, and its curing process is faster than other resins. The main feature is that the process after casting is clean and leaves no residue.
- Dental resins: There are special resins for the dental field which can be colored, transparent, more flexible or more rigid depending on needs. Some applications in dentistry are bridges, crowns, retainers or splints, and therefore these resins must be sterilizable.
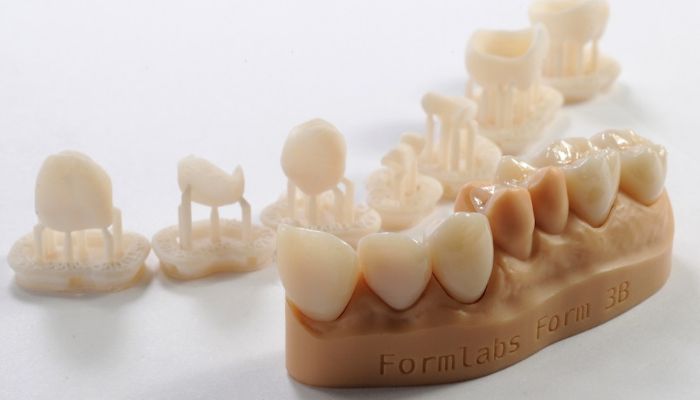
Resins play an important role within the dental industry (photo credits: Formlabs)
3D Printing Polymer Powders
In today’s thermoplastic polymer powder market, there is a wide range of plastics, of which nylon is the most common. It is important to add that powders can also contain beads, such as HP 3D High Reusability PA 12 Glass Beads, which – as the name suggests – is a thermoplastic filled with 40% glass beads.
- Nylon: Also known as polyamide, PA12 and PA11 are the most commonly used. These two types of nylon absorb little moisture and are used, for example, in the automotive industry for their resistance and friction.
- Nylon PA12 is made from petroleum. This material has the ability to withstand drastic temperature changes and is resistant to various chemicals.
- Nylon PA 11 is a bio-based polymer, but this does not automatically mean that it is also biodegradable. As we know, polyamide 11 contains castor oil, has good heat resistance, high elasticity and is more ecological than PA12.
- PEEK: A semi-crystalline thermoplastic that is highly valued in industry for its mechanical properties, heat and wear resistance, and ability to replace certain metals thanks to its weight/strength ratio. However, it is a difficult material to machine, notably in terms of temperature. For this reason, this material is mainly used in the automotive, aerospace and medical industries.
- Composites: Composites consist of a matrix polymer and short or long fibers. The best known are carbon fibers and glass fibers. Carbon fiber is made by mixing a polymer with carbon fibers, resulting in a lighter, stronger and stiffer material. Glass fibers, in which a polymer is mixed with glass fibers, are as strong as carbon fibers, but less stiff and denser.
- Polypropylene: This thermoplastic (PP) is also semi-crystalline and is characterized, among other things, by its resistance to chemical products, its good electrical insulation and its light weight, but it is difficult to print because its thermal treatment must be controlled.
- TPU: Thermoplastic polyurethane is a material characterized by its high durability and flexibility during processing. Also has a high resistance to shocks, abrasion and cuts, although does not tolerate high temperatures, a step that you must take into account in your 3D machine and technology used.
A clearly environmentally friendly aspect of plastic powders is their recyclability. Since the powders used for SLS and MJF are thermoplastics, they can be sieved and mixed with new powder after the sintering process to reuse the excess material and thus avoid waste.
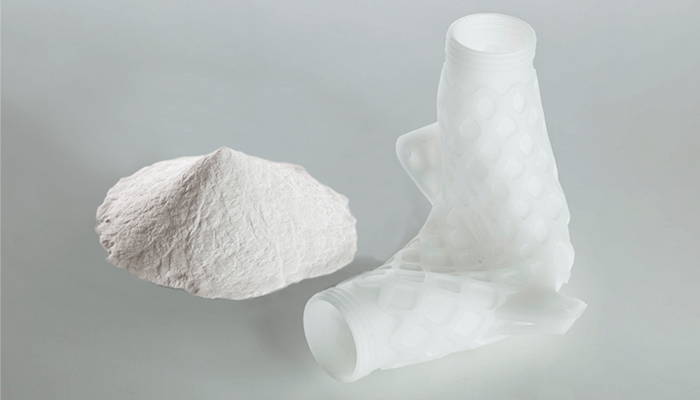
Photo Credits: BASF
The 3D Printing Digital Workflow
Resins
For resin 3D printing, one of the most popular methods used is vat polymerization. This encompasses SLA, DLP and LCD processes and uses an ultraviolet (UV) light to cure the resin; what differs between the processes is the light source used. For 3D printing with plastic resins, as mentioned earlier, there are SLA, DLP and MSLA, which use different light sources. For example, SLA uses a laser to cure the resin point by point, while DLP uses a projector that cures the entire resin tray in a single projection. Another completely different process that is compatible with resins is material jetting, where several resins are used at the same time, including the possibility of using transparent ones.
Turning now to the necessary post-processing, you may have already noticed that after printing, there is often sticky resin residue on the surface, which must be removed by washing in a solvent. Isopropyl alcohol is the most common solvent and gives the best results. You also need to remove any supports added during the design process – depending of course on the geometry of your part. This is best done with pliers. Finally, since not all curing reactions are necessarily completed immediately after printing, parts made from resin must undergo additional heat treatment. There are many methods for this, ranging from simple photopolymerization – for example in sunlight – to the use of curing devices. Note that the curing time varies from part to part. Finally, when finishing, you can smooth the surfaces, reinforce the parts themselves or even create an aesthetic surface.
Finally, in terms of the toxicity of the resin, it is important to know that it can often cause severe irritation and allergies when in contact with the skin, especially when exposed to the sun’s UV rays. Also beware of inhaling vapors when handling the resin. These can cause dizziness in users due to their high toxicity, hence why it is important to wear adequate protection.
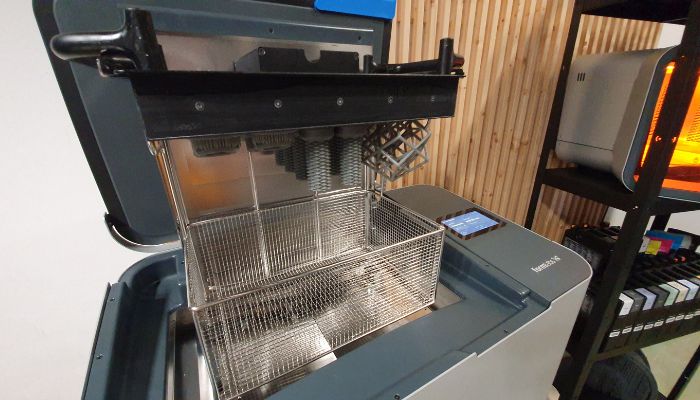
Post-processing of resins requires all the steps, such as washing off here (photo credits: Formlabs)
Powders
For 3D printing with plastic powders, a distinction is made between SLS, MJF and Stratasys’ SAF – binder jetting could also be included, which uses plastic powder in some cases. In SLS technology, after depositing a thin layer of powder on the build plate, a laser is used to selectively sinter the powder and solidify the selected area. There is also HP’s Multi Jet Fusion process, which, after the powder layer is applied, deposits a fusing agent selectively on the areas where the particles are to be fused together. At the same time, a detailing agent is applied and reduces the fusion on the edges of the part, resulting in clean and smooth edges. In the case of SAF – Selective Absorption Fusion – the main difference is that this technology uses a high-energy absorption fluid that, once deposited, absorbs the energy, fusing the polymer powder into the desired 3D pattern.
If you want to print with polymer powder, you need to know that, unlike using resin, you do not need supports. In fact, the 3D printed part is in the so-called “powder cake” during printing and is therefore supported. Continuing on post-processing, the first step is to remove the parts from the powder cake. This involves a cooling process that can take up to 10 hours depending on the parts. Then comes the removal of the powder. This can be done manually or automatically with a machine. Special protective equipment must be worn, as the inhalation of the powder to be removed can cause health risks. There are a number of other finishing steps for plastic parts, such as galvanizing, painting or sanding, but these are optional.
The Price Range of Plastic Powders and Resins
The price of the two materials depends heavily on their respective properties and applications. However, it can be said that the price of 500g of resin starts at around $25 for a standard black resin and goes up to over $400 for one liter. Plastic powders are in a very different price range than resins. PA 11, for example, costs between $75 and $320 per kilogram. Keep in mind, however, that when printing with plastic powder, it can be reused to a certain percentage, usually from 50%, which is therefore also reflected in the price.
What Manufacturers Are on the Market?
The best-known manufacturers of these families of materials are the chemical groups, which are responsible for producing the raw materials, and the 3D companies, which then use them or sometimes even develop them in collaboration with the chemical groups. In the case of raw materials for resins, this includes the chemical groups Loctite Henkel and Covestro Additive Manufacturing, but also, for example, BASF and Arkema, which collaborate with 3D printer manufacturers and often develop their own materials. Zortrax, Formlabs and also EnvisionTEC are examples. For plastic powders, it is also the chemical companies, and we can mention here Arkema, BASF, Evonik which works in collaboration with HP but also EOS for example. We should also not forget the manufacturers of 3D printing powders such as AM Polymers or Fabulous.
You should also keep in mind that there are currently a lot more proprietary resins, as some resin machines are still closed, i.e. they are only compatible with the materials developed by the manufacturer itself.
Applications for Resins and Powders
When we talk about resins, the suitable applications are often those that require a certain level of detail and precision. For example, small detailed parts, but also more colored components for sectors like entertainment or jewelry. Resins are also very popular in the medical field, especially in the dental field particularly for the creation of surgical guides, crowns or implants.
As far as possible applications of plastic powders are concerned, they are also found in the health sector. Nylon is biocompatible and is therefore ideal for the manufacture of prostheses, as it can be in direct contact with the skin. The manufacturing industry also appreciates this family of materials, as it uses them for functional prototypes, small and medium series. For example, it can be used to make gears or even hinges.
Have you already used either resins or plastic powder in 3D printing? Let us know in a comment below or on our LinkedIn, Facebook, and Twitter pages! Don’t forget to sign up for our free weekly Newsletter here, the latest 3D printing news straight to your inbox! You can also find all our videos on our YouTube channel.