Researchers Have Created a New Rotational, Multimaterial 3D Printing Process
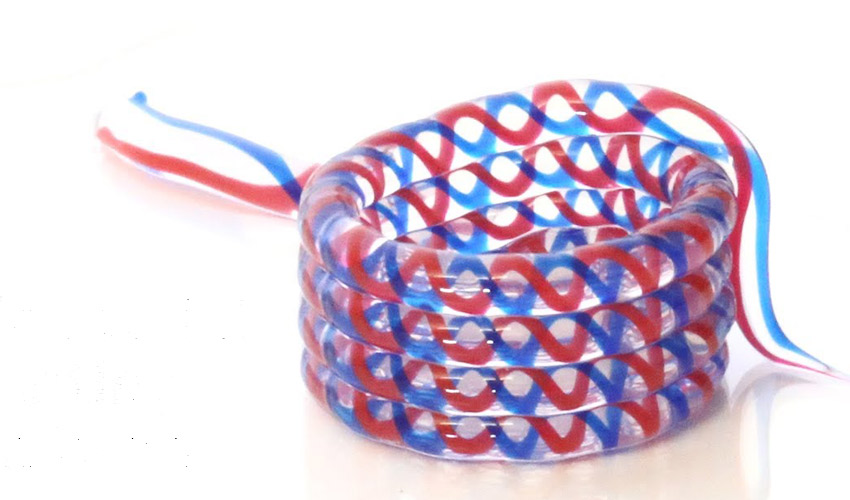
A team of researchers from the Harvard John A. Paulson School of Engineering and Applied Sciences and the Wyss Institute for Biologically Inspired Engineering at Harvard University have taken inspiration from nature to develop a rather surprising 3D printing method. Inspired by the helix-shaped structures found mainly in plants, they have designed a 3D printer that is capable of printing with four different materials wherein a rotating nozzle deposits a helical filament. So far, the team has 3D printed structures of different stiffnesses that could have interesting applications in robotics for example.
This is not the first time that mankind relies on nature’s behavior to innovate: in 3D printing, we often talk about biomimicry and there are many projects imitating the structures that surround us. One example is the lattice structures, like those seen in hives. In this particular project, the idea is to be inspired by the helical shapes found in all biological systems, such as plants and our own muscles. In fact, it is our proteins that assemble themselves and that, by taking this helix shape, trigger their contraction. It would therefore be interesting to be able to design a structure capable of contracting thanks to the properties of the material. This is the track explored by these researchers.
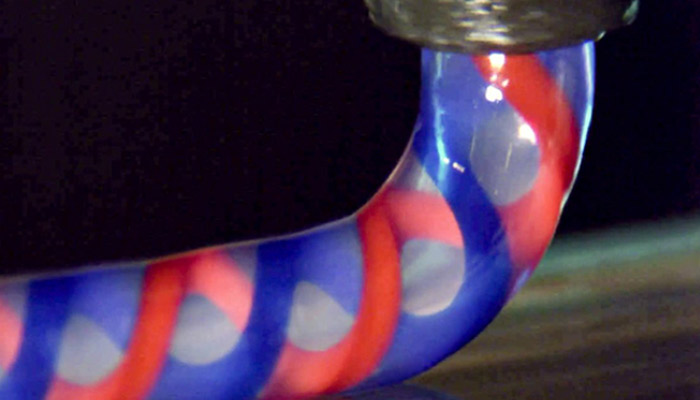
The helical shape is integrated into the deposited filament (photo credits: Harvard John A. Paulson School of Engineering and Applied Sciences)
How Rotational Multimaterial 3D Printing Works
The imagined additive manufacturing solution uses four different ink cartridges – similar to large syringes. They are connected to a complex rotating nozzle that, as it moves, creates a filament with helical properties. Natalie Larson, author of the study, explains, “Rotational multimaterial printing allows us to generate functional helical filaments and structural lattices with precisely controlled architecture and, ultimately, performance.”
As far as applications are concerned, the researchers would be able to print structures capable of contracting when subjected an applied voltage. This contraction would be programmable according to the contractile response of the actuator filaments. They could also play on the rigidity of the 3D printed structures: the base matrix would be flexible and inside, there would be adjustable rigid inks, like a metal spring in a soft mattress. The team explains that this could be useful for creating hinges in soft robots, for example.
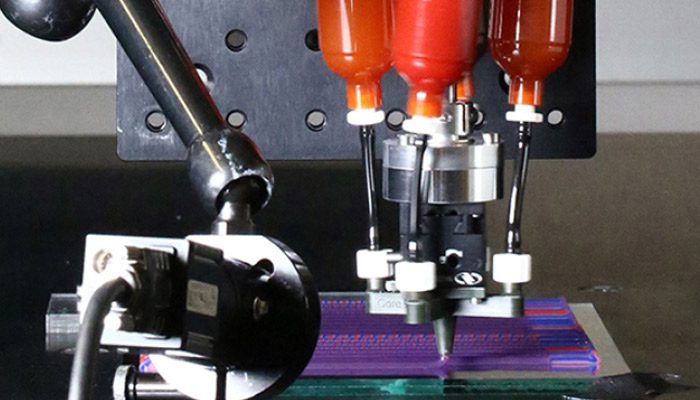
The 3D printing platform includes 4 cartridges (photo credits: Harvard John A. Paulson School of Engineering and Applied Sciences)
And the research is still in its infancy! The field of possibilities is wide and we can’t wait to see what the next developments will be! Natalie Larson concludes, “By designing and building nozzles with more extreme internal features, the resolution, complexity, and performance of these hierarchical bioinspired structures could be further enhanced.” In the meantime, you can find more information HERE.
What do you think of this new rotational multimaterial 3D printing process? Let us know in a comment below or on our LinkedIn, Facebook, and Twitter pages! Don’t forget to sign up for our free weekly Newsletter here for the latest 3D printing news straight to your inbox! You can also find all our videos on our YouTube channel.
*Cover Photo Credits: Harvard John A. Paulson School of Engineering and Applied Sciences