Replacing Metals With High-Performance Polymers in Industrial Applications
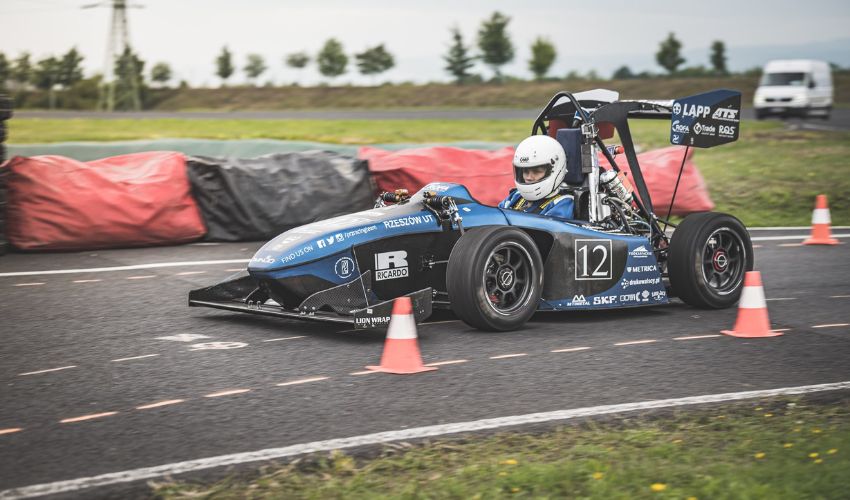
In traditional manufacturing, metal is praised for its strength, corrosion resistance and durability, among other properties. And while that will never change, the rise of the use of additive manufacturing with high-performance polymers has brought about an astonishing development: the ability to replace metal parts with high-performance polymer ones. This can even be done in safety-critical industries like aerospace, automotive and railway.
But what are the advantages of switching metal parts for ones made from high-performance polymers? And more importantly, what tools are needed to ensure that it is done safely? Omni3D, known for its industrial-grade 3D printers, has arisen as one of the leaders in this field and it is actively working to show how it is possible to switch metals for high-performance polymers in different sectors. We took a look at how.
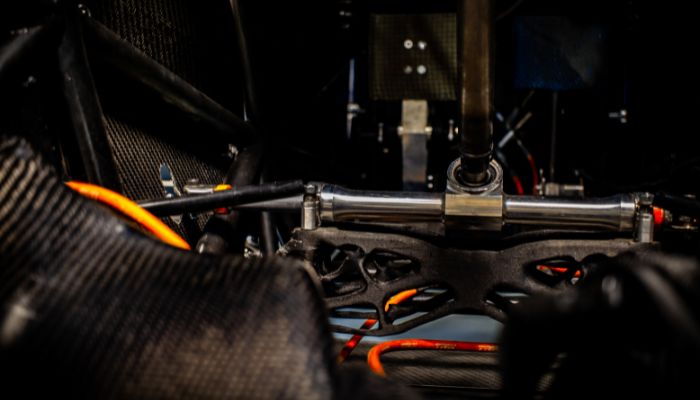
A polymer gear mount made using Omni3D’s large-format 3D printing
What Are the Benefits of Using High-Performance Polymers Over Metals?
First, it is important to note what exactly high-performance polymers are. These thermoplastics are notable for their incredible properties like corrosion resistance, superior strength-to-weight ratio, durability, thermal stability, creep resistance and chemical resistance, among others depending on the material. For additive manufacturing, some of the most used are PEEK, PEKK and ULTEM which offer different advantages.
One of the most significant is the ability to reduce weight. Despite the many benefits of metals, it cannot be denied that they are heavy. High-performance polymers are lighter, and their properties allow them to offer a comparable performance as compared to metals. This lightweighting is critical for industries like aerospace, automotive and railway. That is because weight reduction translates directly to improved fuel efficiency, increased payload capacity and reduced environmental impact.
Not only that, but by combing high-performance polymers with additive manufacturing, the benefits become even greater. That is due to the fact that additive manufacturing allows for the creation of much more geometrically complex parts than in traditional manufacturing, helping break free from legacy constraints. Notably, this can be used to optimize the designs and create even lighter parts.
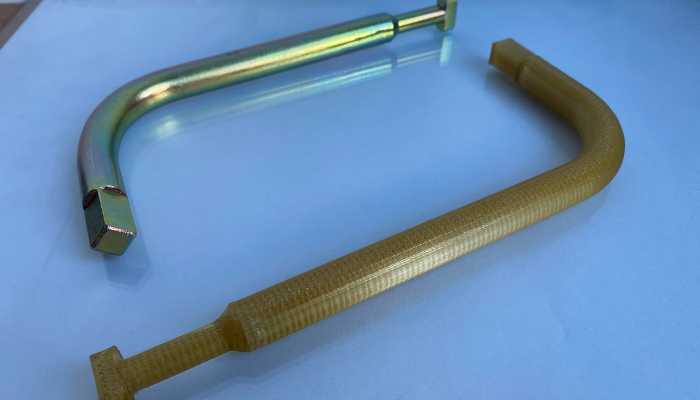
A metal vehicle manhole key (top) that Omni3D replaced with a high-performance polymer version (bottom)
AM is also known for being a game-changer when it comes to improving supply chains thanks to the ability to produce on-demand parts. It is also a viable alternative when it comes to broken or obsolete components, especially ones made of metal. Using high-performance polymers and additive manufacturing, production will be significantly more rapid and thus reduce downtime.
Equipment Needs for High-Performance Polymers
However, there is a reason that high-performance polymers cannot be used for every single part made with 3D printing. And that is because not just any additive manufacturing solution will do. Industrial-grade equipment is necessary in order to truly allow users to take advantage of the benefits of these thermoplastics and handle demands for large-scale production.
One of the most important needs, of course, is material compatibility. If a machine does not have a heated chamber or an extruder that can reach certain temperatures, it will be impossible to print with high-performance polymers. Precise temperature control and uniform heating especially are critical for performance.
Other ideal qualities include a larger build-volume for the production of larger and more complex parts, advanced control systems and precision mechanisms and of course the capacity for continuous operation and minimal downtime. Open material systems are also preferable as a way to allow users to experiment with a wide range of filaments and materials, critical for optimizing part properties and exploring new applications.
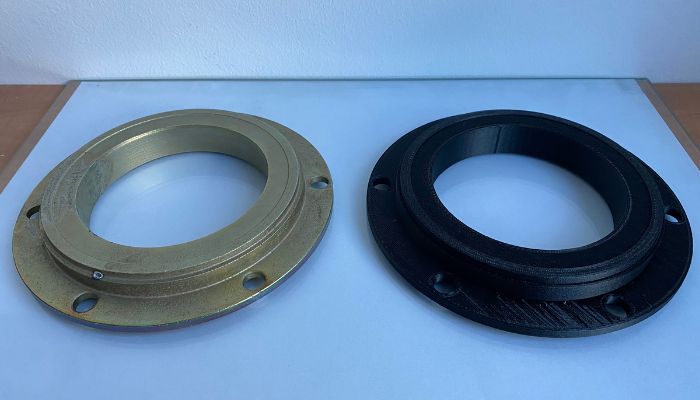
A metal wheel bearing (right) and the high-performance polymer version made by Omni3D for NATO vehicles
A good example of such suitable equipment comes from Omni3D as a leader in industrial 3D printing. The company’s large-format printers are equipped with heated chambers that have been designed for precise temperature control regulation through the build volume as well as consistent temperature disruption for uniform heating and avoidance of cold spots. This helps to ensure optimal material crystallization and minimize warping and other part defects.
These properties mean that they are capable of handling the demanding thermal requirements of materials like PEEK, PEKK and ULTEM. Furthermore, closed-loop control ensures that accurate temperature settings are maintained even for long print jobs. These features are ideal for printing with high-performance polymers. Even if there are still issues that must be overcome.
When these come together, some incredible parts can be made with high-performance polymers. Taking an example from Omni3D in the defense sector, large-format 3D printing with high-performance polymers helped NATO to maintain a fleet of BMP-1 vehicles. These tanks are key assets for NATO military forces, but they can pose a significant logistic challenge as procuring replacement parts for them is both time-consuming and expensive. Long lead times especially can jeopardize operational readiness.
Omni3D was able to show that NATO could produce high-strength, functional parts for the tanks directly on site. By combining this with a digital library of BMP-1 components, NATO military forces were able to bypass supply chain delays and ensure continuous vehicle operation with minimal downtime. Overall, by turning to additive manufacturing, NATO saw a significant improvement in fleet maintenance.
Another example where metal parts were replaced with high-performance polymers using Omni3D’s solutions comes from Luk-Plast. Here, the company had an issue where the brass vacuum pump rotors were wearing out necessary due to exposure to harsh conditions such as aggressive chemicals, water and gas. This, combined with high-speed operation and continuous duty that added mechanical stress, resulted in frequent replacements and increased downtime. This resulted in inefficiencies in railway systems.
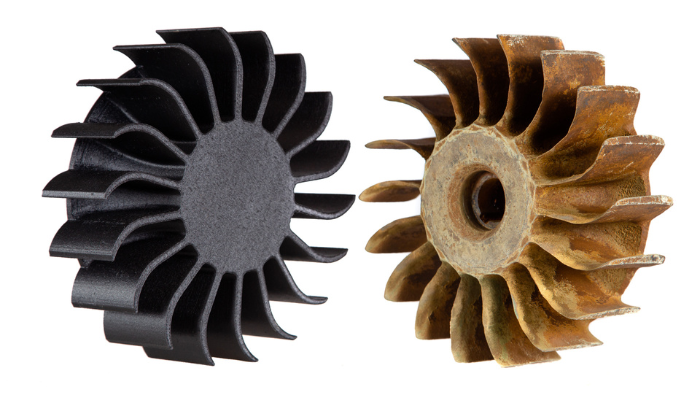
The brass (right) and high-performance polymer (left) vacuum pump rotors
Again, Omni3D was able to address the problem with polymer parts. More specifically, the Omni Pro 3D printer and CF PA-12 were used to create durable parts that could withstand these extreme conditions. The company noted that the precise temperature control in the heated chamber enabled the 3D printed component to retain its strength and stability, even in the face of aggressive chemicals and high mechanical stress. In the end, the 3D printed rotor had a significantly improved lifespan, reducing maintenance intervals and minimizing downtime.
Similarly in the automotive sector, Omni3D was able to replace a metal intake manifold, gear mount and joint cover for the PRz Racing Team using 3D printing, CF PA-12 and TPU-93A. The resulting polymer parts were lightweight, durable and heat resistant. Turning to additive manufacturing enabled design flexibility and fast, cost-effective production as well as lighter parts, the intake manifold’s weight was reduced by 1.5kg compared to the aluminum equivalent.
These examples, among others, show what can be achieved when using engineering and high-performance polymers to replace metal. Especially when done using additive manufacturing. However, that does not mean that there is no room for improvement.
What Is Need for Future Advancement?
There is another factor that is critically important when working with high-performance polymers: the human element. As it stands, engineers and technicians are not always equipped with the knowledge necessary to use AM for industrial applications, especially when it comes to replacing metal parts with high-performance polymer ones. This is another area where leaders in the industry such as Omni3D have an important role to play.
Engineers working with high-performance polymers should be skilled in a wide array of areas. These include the ability to evaluate part designs for printability, know how to use 3D scanning and reverse engineering, be able to create CAD designs that have been optimized for manufacturing, select the most appropriate materials based on the requirements of the part and the used AM process, be able to fine-tune print parameter optimize and understand the necessary post-processing techniques. All these are important to being able to truly use the technologies and bring out their benefits.
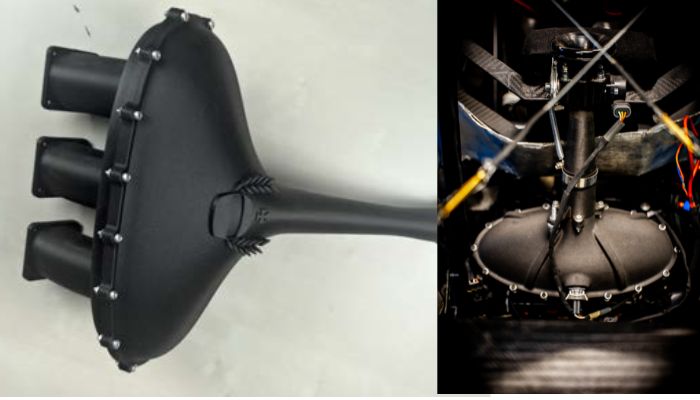
An Intake Manifold made for PRz Racing using Omni3D’s solutions and CF PA-12
But how is this possible? Well one way is to ensure that systems are open. Omni3D for example has always noted that it is important to keep them open in order to future-proof equipment that is used for replacing metal parts with 3D printed substitutes. Open-source platforms and software will help increase adoption as technical teams can use and test AM technologies at their own pace.
An additional aspect is putting more of a priority on both education and support. Both of which Omni3D has committed itself to in recent years. Through hands-on workshops, online resources for self-paced learning, technical support for when there are issues and even customizable training programs, the company hopes to enable organizations to leverage the potential of AM in industry.
This focus on education and support is one of the most important factors that will help to drive the move from metals to high-performance polymers for even safety-critical parts. Combined with the materials themselves as well as the appropriate equipment, it becomes possible to maximize the use of additive manufacturing and drive innovation. You can learn more about how Omni3D does this in the free whitepaper, which you can download HERE.
What do you think about replacing metals with high-performance polymers? Can you think of other industries where this is becoming more common? Let us know in a comment below or on our Facebook and Twitter pages! Don’t forget to sign up for our free weekly Newsletter, with all the latest news in 3D printing delivered straight to your inbox!