Rapid Fusion Talks Using Pellets for Large-Format Additive Manufacturing
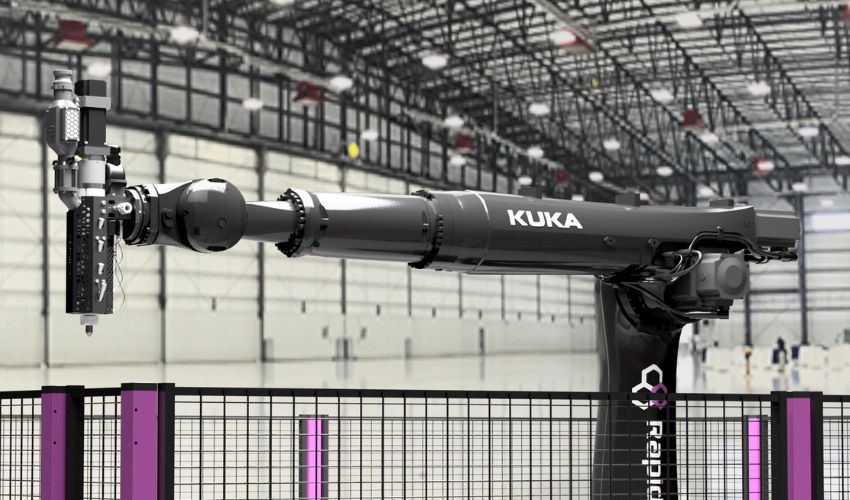
If asked which two trends have been dominating the polymer 3D printing sector, the answer would be obvious: pellets and large-format additive manufacturing (LFAM). In recent years, we have seen machines getting larger for even more applications in sectors like maritime and automotive. At the same time, pellets have become a popular extrusion material choice. This is not just because they are often cheaper and have a wider range of properties than their filament counterparts, but also because they are particularly suited to LFAM. One company that recognizes this more than most is Rapid Fusion, which has developed its own solutions to print large-scale projects with a range that includes everything from extruders all the way to its new all-in-one cell. We spoke with the founder of the company to learn more.
3DN: Could you introduce yourself and your connection to 3D printing?
Hi, my name is Jake Hand, and I am the founder and manager director for Rapid Fusion, an advanced robotic additive manufacturing company based in the UK.

The Rapid Fusion team including Jake Hand (on the far left)
3DN: How did Rapid Fusion come about?
The story of Rapid Fusion begins with Evo3D, the sister company, which we founded in November of 2021. Through that, we specialize in reselling large-format additive products. And it helped us realize that there was a gap in the market for a manufacturer to produce.
More specifically, we wanted to build our own robot 3D printer and develop something that we could sell as a system through Evo3D. But we realized that the technology on the market was actually quite clunky and did not work very well. Plus, the results that you got at the beginning were pretty poor.
This meant that the chance that someone in industry would be able to buy this type of technology and it work straight out of the box would probably be slim. To solve this, we set about designing our own products.
First, we created our own extruder and our own control panel and dialed that into the product that we have now. And so was born our spin-off, Rapid Fusion. The company was formed in the beginning of 2023 about 18 months after we had started Evo3D.
Initially, we launched the PE320 extruder, and we created a fantastic product right away. It was very solid in terms of its capabilities, notably, it is a lot lighter than its competitors while being a lot more powerful, which is beneficial if you are buying a robot. The cost of a robot is a lot higher depending on the weight of what it carries, so something lighter but powerful is the direction to go in.
When we launched the P320, it was well received and won some awards. We then went on to create the ecosystem that would allow you to convert a robot into a 3D printer. This is everything you need, including the robot, pellet extruder, control system, air plus kit, enclosure, accessories, etc. That range then allowed us to create a full cell, which we call Apollo. Apollo is a full, all-in-one solution, and we are already selling it.
Essentially, users have the choice of the individual components that we created or the full system. Furthermore, we have seen that there has been a lot of interest in these products in a wide range of sectors. We can point towards things like furniture but also industrial applications like creative molds, which are a huge sector.
If you think about it, molds are being used in a lot of industries, including demanding ones like maritime and automotive, essentially anywhere where it is necessary to create something large very fast. Our solutions and this specific technology can offer a lot of benefits for that, ultimately helping to cut costs and make the process a lot easier for customers.
3DN: What are the benefits of using pellets specifically for 3D printing?
Firstly, with pellets, you get access to a wider range of polymers. This enables users to create interesting materials by blending different materials together. For example, when you print for the marine sector, there is a material called r-UltraMarathon 3D that has been specifically developed. It is UV-resistant, allowing it to be in the sun, which is clearly very necessary when we are talking about boats. It is also antimicrobial and antifungal, meaning it does not allow the build-up of moss or anything on the bottom of the boat. That has been developed as a blend of polymers, which is possible with pellets.
With pellets, it is also easier to recycle material as they can be used repeatedly. Take plastic bottles, these are made of PETG. PETG can be chopped back up and used as a pellet and reprinted multiple times. Through pellets, it is possible to reach a circular economy with these materials.
And this is quite important. We notice that when we speak to car manufacturers, they have a lot of waste plastic that they are trying to figure out how to reuse and put into cars. Pellet technology allows you to chop that plastic back up and print some parts within the car where, typically, you would need to use what we call virgin material. With this, we can make additive manufacturing better for the planet while creating a better economy for the materials.
Furthermore, we are not limited in terms of properties for pellets. It is possible to add graphite and carbon into a polymer, which gives it extraordinary strength capabilities while keeping the part lightweight. Essentially, it is the best of both worlds. Typically, when you think of something, a structure being strong, it is going to be heavy. Through this, we know this no longer needs to be the case, and, instead, we can turn to these and other engineering-grade polymers.
There are also other polymers available in pellet form that have been created to be fire-resistant while being lightweight. This could be used to build parts that would be used in the maritime industry, for example on a warship, where the weight that is on that ship costs millions to move around in its lifetime. Meaning if you can create even just a fire extinguisher holder out of a polymer instead of metal, the benefits are huge.
There are a number of pros and cons to it. But using polymer pellets means you can blend them quicker. It is easier to create things faster. You can create a material and test it quickly with very limited machinery. It is allowing us to develop these extraordinary materials faster.
3DN: What about for large-format additive manufacturing?
Large format additive is clearly where we can see the market going. We are already seeing it with people who are printing car chassis. I can’t see why you couldn’t print even the hull or the chassis of a train.
The bottom line is that pellets are ideal for large format printing because they allow users to push a lot of material and extrude it quickly. One limitation with filaments is that there is a set size, so it takes a long time to melt that down into something useful. This is not the case for pellets.
This is a big reason why our Apollo solution and our range of products make sense for people in a lot of industries where specific properties or large-format printing are necessary.
3DN: Could you tell us more about how Rapid Fusion has evolved and what is next for the company?
In March of 2023, we received an award from Innovate UK to produce a large machine that combined pellet AM and CNC. That machine is being built at the That has also opened doors because it has allowed us to hire a lot of engineers, building up a team to help us develop new products. That project should be available in early 2025.
What is really incredible is that it is being designed with a group of manufacturers in the UK. Companies like Rolls-Royce, GKN, Baker Hughes and some real big names are guiding us on their needed industrial applications on that machine. And of course, that has helped put our name out there. It is safe to say now that we have managed to build up a credible business and pipeline of customers that want to buy our technology.
This has also enabled us to mix in new circles and enter new markets. We also have developed a network where we have signed resellers in different countries including CNC World in the UK, Hyperion in Australia, Maptec in Dubai and ACCUFACTURE in the USA. Through this, we have been able to open up into these other territories.
We are fortunate that we have grown quite quickly through our experience in launching high-quality, solid products all while understanding how marketing is done and how to build stuff that the industry wants. At the end of the day, it is a good tech team of designers and product engineers coupled with a strong sales and marketing team. Now we aim to grow and find our way into other regions across the world.
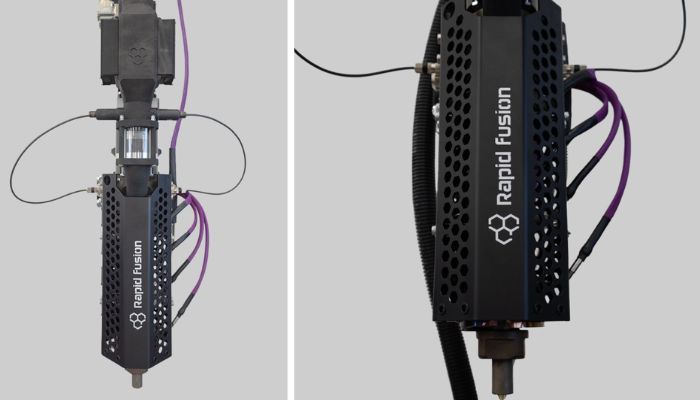
Rapid Fusion started with the PE320 extruder and has extended to Apollo, the full cell
3DN: Any last words for our readers?
If you are looking at exploring large format additive manufacturing or have a process currently where you are producing large parts, and it is not going to scale effectively: we have a team of people here that are allowing you to test the technology and understand how the solution works.
You are welcome to visit our facility in Exeter where we can demo the equipment, discuss your projects, and work out how we can help assist you make that leap into using AM for these applications. We look forward to hearing from you, you can find out more HERE.
What do you think of Rapid Fusion and its solutions? Do you use pellets for additive manufacturing? Let us know in a comment below or on our LinkedIn, Facebook, and Twitter pages! Don’t forget to sign up for our free weekly newsletter here for the latest 3D printing news straight to your inbox! You can also find all our videos on our YouTube channel.