How to Achieve Quality ABS Parts at Scale With Additive Manufacturing?
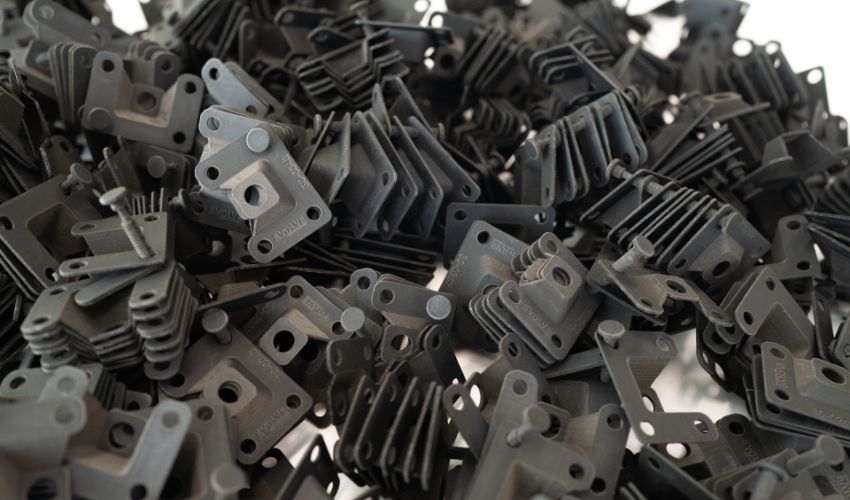
According to a report by MarketsandMarkets, the polymer 3D printing market is growing, with a calculated value of $1.7 billion in 2023 and an estimated $4.4 billion by 2028. Among the most widely used thermoplastics in the manufacturing industry is ABS (Acrylonitrile Butadiene Styrene), best known for its impact resistance, low temperature resistance and light weight. Thanks to these characteristics, it is used in numerous applications: prototypes, appliance parts, car interiors, gears, valves, tools, etc.
The most widely used production method for large-batch ABS parts is injection molding, but additive manufacturing is equally used for prototyping and small runs. A limitation in this field is that encountered by the segment of users who are scaling up their production and therefore need to move quickly from prototyping to volume production. Evolve Additive Solutions’ Selective Thermoplastic Electrophotographic Process (STEP) technology fits into this market segment, offering itself as a viable alternative to injection molding for the production of quality ABS parts at scale. How? Let’s delve deeper.
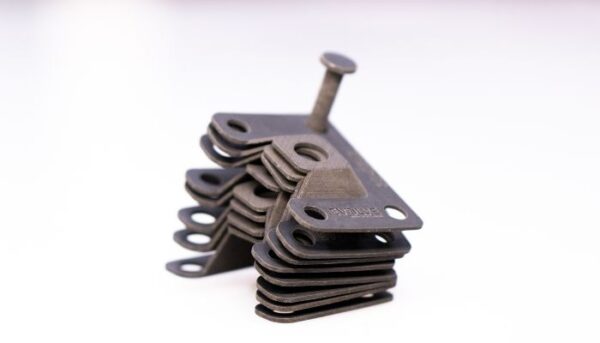
Set of ABS brackets 3D printed using STEP technology.
How Does STEP Work?
Evolve’s STEP technology is part of the additive technology family, but it does not correspond exactly to any of the processes currently outlined in the international standard ISO/ASTM 52900:2021, which describes additive manufacturing processes.
In fact, STEP involves creating parts layer by layer, but the technology’s core is based on high-speed 2D digital printing. It is structured in 3 steps: the first is imaging, in which particles of the part and supporting materials are selectively deposited on a moving belt using electrophotography; the second is alignment, here the images are heated and transferred to the build plate; and finally fusing takes place, i.e., under the effect of heat and pressure, the particles are fused to the build layer and then cooled below glass transition temperature. Fully developed layers of part and support material are deposited one after another, producing the 3D part. “We’ve found a way to micronize engineering thermoplastics so that they behave like toner in a 2D printer,” explained John Lees, vice president of engineering at Evolve Additive.
What is interesting about STEP, and what Evolve says distinguishes this technology from other additive processes, is that it enables the production of fully dense parts. This is because the roller presses the image onto the print layer by exerting pressure, which, combined with heat, ensures optimal adhesion. The machine marketed by Evolve, the SVP™ (Scaled Volume Production), also scans the layer at each pass to identify any variations in height, compensating for them by adjusting deposition in subsequent layers. According to Evolve, compared to other additive processes, STEP thus allows for parts that are highly accurate with superior mechanical properties that are scalable.
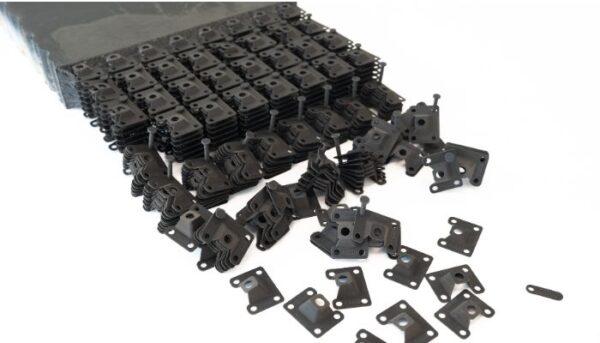
One SVP machine build unit includes 92 sets of brackets for a total of 736 brackets, printed in 6.5 hours.
Producing ABS Parts: Comparing STEP, Other Additive Technologies and Injection Molding
Having given an overview of the technology, let’s get to the heart of why this technology differs from other AM processes and could be a viable alternative to injection molding when it comes to producing scalable ABS parts. First, in terms of materials, STEP uses two types of ABS — one in black and one in light gray. The process also works with a nylon PA-11, which offers greater elongation and a higher softening temperature.
In terms of printing speed, the technology is faster compared to, for example, Powder Bed Fusion additive technologies. This is because these technologies require, with each print, the use of the entire build volume and thus longer times to switch between production runs, which is not necessary with STEP. In fact, the process can be stopped once the part is ready and, once it is extracted, a new one can be started immediately.
If we look at part accuracy and detail, the layer thickness for STEP is 13 microns, with 22μm particles enabling the production of strong, high-resolution parts; surface roughness is 3-6μm. The Kodak NexPress print engine, which the technology uses, has a resolution of 600 dots per inch (DPI), equivalent to a pixel size of 40 microns. Because this is an electrophotographic process, it does not encounter the same thermal challenges as other 3D printing processes, such as power density limits. That is why Evolve with STEP aims to overcome the “historical” limitations of additive manufacturing and especially the relationship between print speed and resolution.
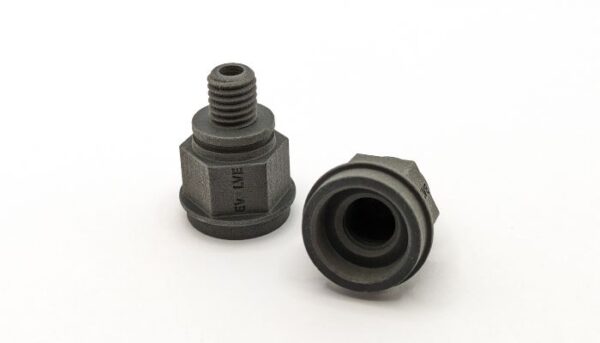
A fully dense ABS part can meet air or fluid handling requirements.
When compared instead with injection molding, while STEP cannot offer the same high-volume production, it provides the same mechanical properties and quality for ABS parts. This, as anticipated, is a plus point for this additive manufacturing process, which could be a good solution for small and medium-sized enterprises (SMEs) looking to scale.
Given the relative speed of STEP, the technology can effectively serve as a bridge between prototyping and volume production. And, in terms of cost, it can be an initial solution for SMEs that want to scale up but cannot afford to invest in injection molding technology.
3D Printing of ABS End-Use Parts for Serial Production
As mentioned, ABS components are used in numerous industries and applications. These include that of irrigation systems and electrical components. Both these sectors, in addition to benefiting from material properties, have the need to produce small, detailed parts in not-too-large production runs in common. This is why injection molding often does not prove to be the wisest choice, even considering the additional cost of molds.
STEP technology in such cases has made it possible, for example, to create sprinkler valves, check valves, and pressure test manifolds for irrigation systems. In these cases, ABS is ideal because it is chemically resistant to aqueous acids, alkalis, and concentrated hydrochloric and phosphoric acids. In addition, the technology was able to provide the essential characteristics required in these parts, namely density, no voids or porosity problems.
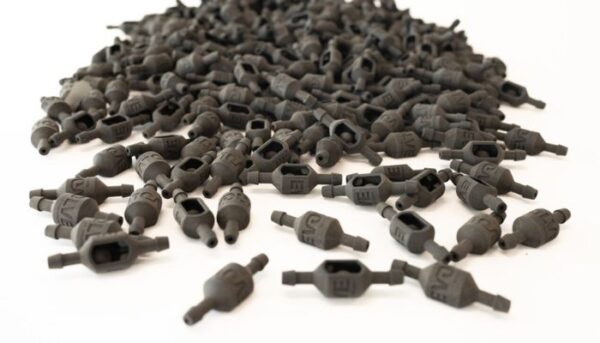
Check-valves with a free-floating ball inside, made by STEP process.
Another use case of STEP technology for the manufacturing of ABS end-use parts is the production of electrical interconnect housings. The use of STEP technology, in this case, was useful because of the ability to combine precision and speed, allowing the end user to create 195 parts in just under two hours. With a standard three-shift rotation, this is an output of more than 300,000 parts per year.
Using STEP technology for these applications, in both prototyping and production, ultimately has enabled users to reduce the risks involved in using multiple production processes. Discover STEP technology for yourself by requesting a free sample part HERE.
What do you think about STEP technology for serial production of ABS end-parts? Let us know in a comment below or on our LinkedIn, Facebook, and Twitter pages! Don’t forget to sign up for our free weekly newsletter here, the latest 3D printing news straight to your inbox! You can also find all our videos on our YouTube channel.
*All Photo Credits: Evolve Additive Solutions