PVA vs HIPS: How to Choose the Right 3D Printing Support Material
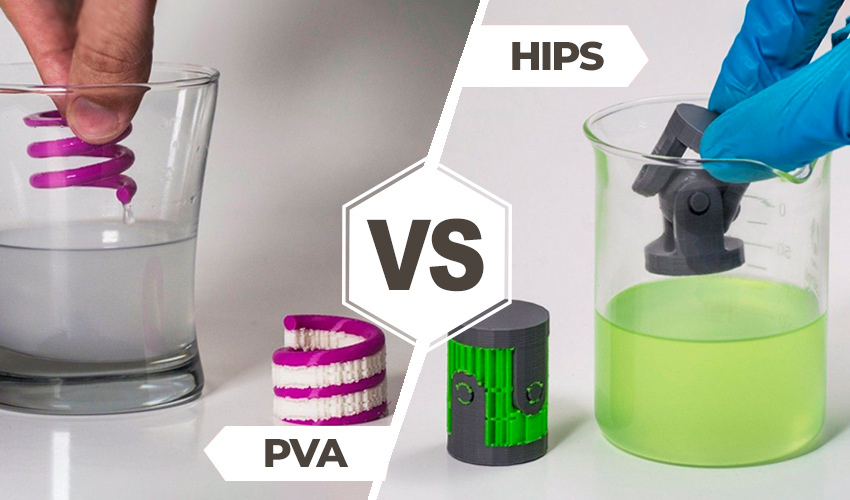
If you want to print objects with complex geometries, steep overhangs, long bridges and cavities, you cannot avoid support structures. With powder-based printing technologies, these are not required, as the powder itself is able to support the printed structure. However, when printing with filaments or resin, it is necessary to include support structures to ensure that the final object survives the print in one piece. Two materials that are frequently used for supports are PVA and HIPS, which we will examine in more detail in this article specifically in their use in FFF printing.
The requirements for support materials are diverse and therefore choosing the right one can be difficult. After all, the supports should be as easy to remove as possible after printing and should not leave any traces on the printed object. Moreoever, in the best case, it will also be a different material to the one used for the printed object itself. Therefore, it is recommended to use an FFF printer with dual extruders, thus reducing the printing time and also the risk that the two materials mix and affect each other unfavorably. Fortunately, in the filament market there are those that are suitable or even specifically designed for printing supports. We took a closer look at two of them, contrasting PVA and HIPS in their characteristics, printing properties and applications. PVA is a material primarily used as a soluble support material in FDM 3D printing, while HIPS is often used both as a support material and as a printing material for stand-alone parts. Though we will focus mainly on its use as a material for support structures.
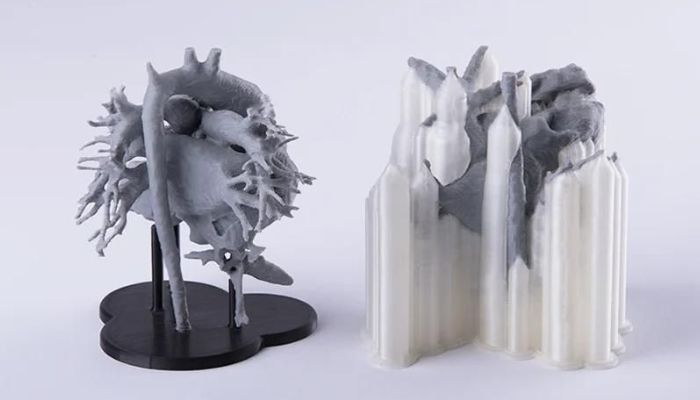
Complex 3D-printed object with supports made of PVA (photo credits: Zortrax)
Properties of PVA and HIPS
Both PVA and HIPS are thermoplastic polymers. PVA stands for polyvinyl alcohol and is formed by the alkaline hydrolysis or saponification of polyvinyl acetate (PVAC) by splitting chemical bonds through a reaction with water. HIPS on the other hand is formed from a mixture of high impact polystyrene and polybutadiene rubber, hence the name High Impact Polystyrene. It is thus a copolymer that combines the elastic properties of rubber with the strength of polystyrene.
Overall, HIPS is similar to ABS in its properties, but is harder and more impact-resistant. It also is well-known for its impact strength, lightness, resistance and mechanical resilience. Printed objects made with the material tend to have a smooth and scratch-resistant surface and are antibacterial. HIPS is hard, but not brittle.

HIPS as a support structure (photo credits: Zortrax)
This is in complete contrast to PVA, which gains more and more elasticity and flexibility through water. Moisture in general acts like a plasticizer on PVA, which is actually brittle and rather fragile, resulting in PVA dissolving sooner or later, depending on the degree of moisture in the environment. The water solubility depends on the respective PVA composition or on the saponification. Depending on the PVA type, the degree of hydrolysis varies between 70 and 100 mol%. This degree influences the melting point and how fast PVA dissolves. Additionally, if PVA is dissolved in water, it can simply be disposed of making it very environmentally friendly. However, as a printing material for a durable object, PVA is completely unsuitable due to its solubility in water, unlike HIPS, but it is excellent as a support material, since it is precisely these dissolving properties that are relevant.
Adding onto that, PVA should only be used with materials that have a similar melting point to prevent printing errors, such as PLA. The melting point is 230°C for PVA and 220°C for HIPS. Although the melting point of PVA is theoretically 230 degrees, it depends on the type of PVA. For fully hydrolyzed forms, the melting temperature is lower and ranges from 160 to 180 degrees.
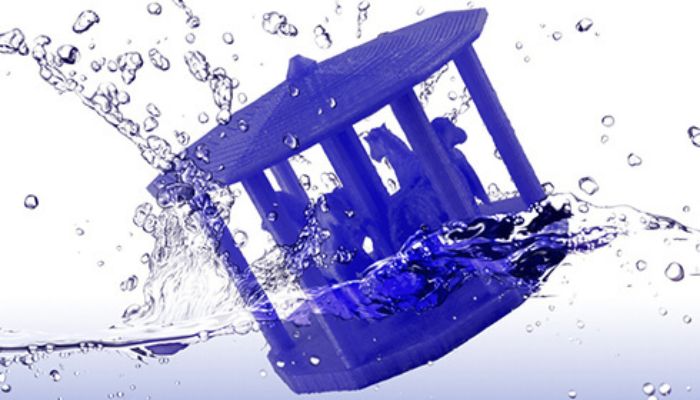
Unlike HIPS, PVA dissolves easily in water (photo credits: XYZ Printing)
Although HIPS cannot be dissolved by water, it can be broken down by certain acids, alkalis, organic solvents and chemicals, which leads to the degradation of the material. Limonene and gasoline cause HIPS to become brittle, discolored and decompose. Therefore, if it is used as a material for support structures, it is necessary in post-processing to treat the object with limonenes, best known as the waste material from citrus peels, so that the supports decompose and come off. However, other plastics also react to alkalis, acids and chemicals with disintegration, so HIPS cannot be used as a support material for a number of other materials. Printing works best in combination with ABS, which is acid-resistant, but not with PLA or PETG. In combination with these materials, it is better to reach for PVA for the support structures.
PVA and HIPS are also similar in terms of tensile strength. They have a low tensile strength of 22MPa and are therefore not very flexible, however PVA does become more elastic when water is added. Both are non-toxic and odorless, but printing with HIPS may produce unpleasant fumes. In terms of color, PVA is naturally transparent to cream-colored, while HIPS is available as a white filament that can be colored if it is not used as a support material. Though in this case the question of coloring is superfluous for PVA because, unlike HIPS, it more often used as a support material or disposable objects.
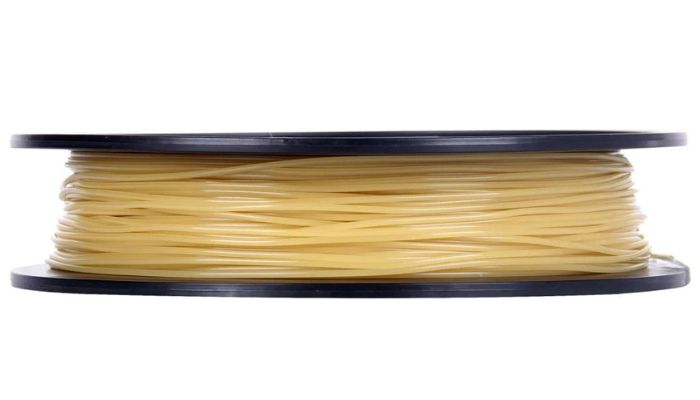
PVA spool from ESUN (photo credits: ESUN)
3D Printing With PVA and HIPS
Storage
For 3D printing with PVA to be most successful, the filament must be stored in a cool place, away from natural or artificial light, dust and moisture. Both HIPS and PVA have limited resistance to UV light. Proper storage is therefore essential to avoid printing problems in advance. For example, the optimum storage temperature for PVA is 15 to 25 °C.
This is because PVA has a tendency to mold and should not be used if it has absorbed moisture, otherwise the finished part may warp or exhibit other anomalies such as holes or bubbles. Therefore, if PVA has absorbed moisture, it must be dried before use. A guideline is about 8 to 12 hours at 50 to 80 °C. To avoid this, it is best for PVA to be stored in an airtight container. HIPS, on the other hand, does not absorb moisture and does not need to be dried before printing.
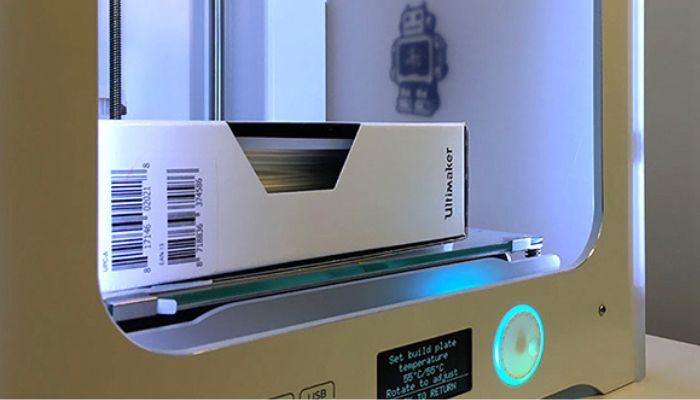
PVA is dried on the print bed (photo credits: IGO3D)
Printing Process
As is generally the case when printing with support materials, you should set the printing configuration so that a distance of 0 layers prevails between the support part and the final part. In this way, the surface of the final part will be optimal, without any segregation or other inconvenience. Since the supports should dissolve after printing anyway, their adhesion to the part during the printing process is of no further relevance.
To achieve good adhesion of HIPS to the print bed, it is recommended to use solutions such as glue or adhesive tape. A slag with a mixture of ABS and acetone can also be used for this purpose. For PVA, painter’s tape is ideal.
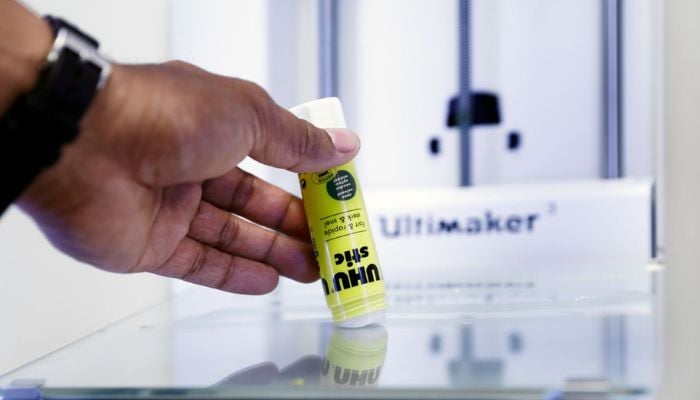
To make HIPS better adhere to the print bed, you can use glue (photo credits: Makerbot)
To achieve a good printing result with PVA, the printing plate must be preheated to 45 to 60 ºC and the extruder must be brought to a temperature of between 185 and 200 ºC. HIPS, on the other hand, requires higher temperatures: between 100 and 115 ºC for the printing plate and 230 and 245 ºC for the extruder.
Since it is preferable to use a support material that has a similar melting temperature to the material of the printed object, PVA and HIPS are not used as supports for the same materials. PVA is used with PLA, TPLA, PETG and CPE, while HIPS is mainly used with ABS. Another reason why HIPS is preferred to be used with ABS is that, as previously mentioned, unlike many other printing materials, ABS is not destroyed by limonic acid (D-limonene), which is used as a solvent to dissolve the HIPS carrier.
For optimal printing of PVA, it is also recommended to use an ooze shield to protect the part and the supports from oozing. This is because if a nozzle is not used but continues to be heated, the filament it contains can seep out and even clog the nozzle. With HIPS, the heated chamber eliminates the need for a ooze shield. Also, with PVA, it is recommended to cool the parts as it helps solidify the plastic faster. Thus, stringing is reduced and the quality of the printed part is improved. For printing HIPS, on the other hand, the use of a cooling fan is not necessary.
When printing HIPS, it is recommended to use a closed enclosure to limit the temperature difference between the printed object and the ambient air, since, as mentioned above, HIPS must be printed at high temperatures. This precaution prevents the material from curling, warping or delaminating due to sudden temperature changes. It is also advisable to have an efficient ventilation system or a HEPA air filter to protect the respiratory tract, since printing HIPS, unlike PVA, can produce unpleasant fumes such as styrene.
The recommended printing speed for PVA is about 30 mm/second, which is lower than for most other materials: this is due to the fragility of PVA. For HIPS, the printing speed can be higher and ranges from 40 to 80 mm/sec. That being said, both filaments are quite easy to print if the printer has been adequately configured beforehand. When HIPS is used, shrinkage occasionally occurs during cooling, which leads to warping of the printed object. However, if HIPS is used for the support structure, this effect is hardly a problem, since the support is removed anyway.
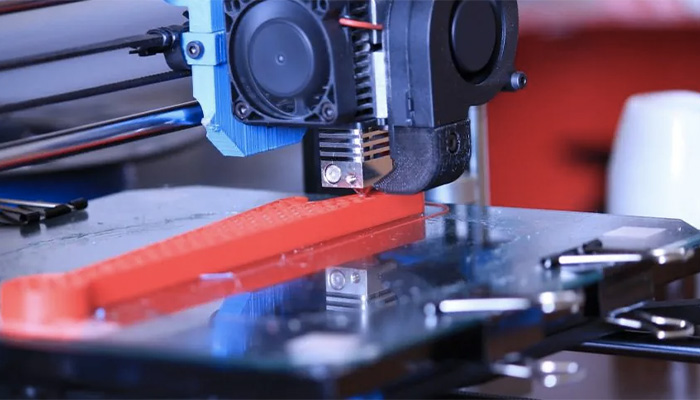
Just like ABS, HIPS tends to curl and warp under pressure (photo credits: Sculpteo)
Post-Processing
A great advantage of PVA is the ease of post-processing. The entire structure is simply placed in a warm water bath and after waiting 1-2 hours, you take out the finished part. The water can be easily disposed of down the drain, since PVA, as already mentioned, is completely biodegradable.
Post-processing with HIPS structures, on the other hand, always involves the use of a chemical, which must be handled with the necessary care and is also relatively expensive. Therefore, it is recommended to always work with a respiratory mask and protective gloves for safety and to break off the large structures by hand to save costs for the chemical solution.
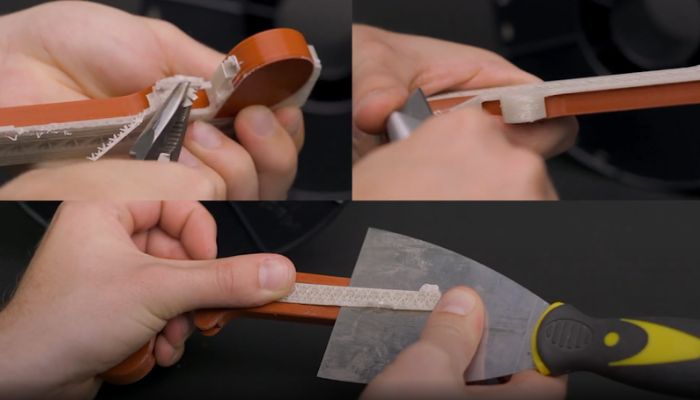
If HIPS is used as a support material, it is beneficial to cut away the larger pieces before machining the part with limonene (photo credits: MatterHackers)
Applications of PVA and HIPs in 3D Printing
As we have already seen, PVA and HIPS are mainly used to make supports in 3D printing with other materials. But that is not all. PVA can also be used to make prototypes and molds. Meanwhile, in the design field, PVA is also used for the production of decorative models.
This is taken even further with HIPS. As already mentioned, HIPS does not dissolve in water like PVA. It is light, very impact resistant and is therefore often used in the production of toys and children’s articles. It is also frequently used in the automotive industry for the production of interior parts such as dashboards or generally in the manufacture of housings for electrical and electronic devices. Another field of application for HIPS is in packaging. Takeaway meal trays are often made of HIPS, as is packaging for cosmetics. However, it should be noted that in 3D printing, both materials primary use is as a support.
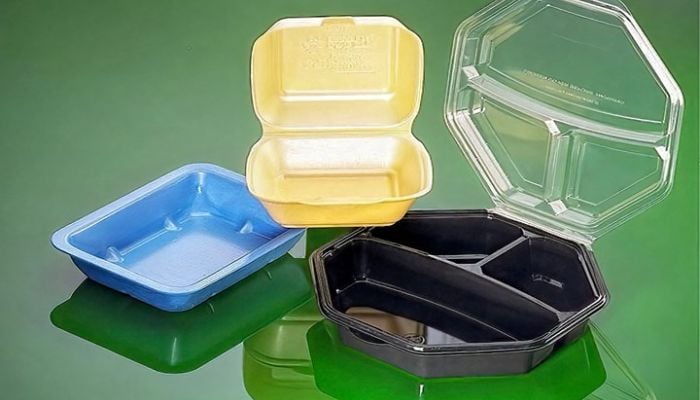
HIPS is used as a stand-alone material for packaging (photo credits: Plastics Technology)
Manufacturers and Price
PVA filament is available on the market in filaments of both 1.75 and 2.85 mm. Before buying the filament, check that the thickness matches the diameter of your 3D printer’s extruder. The price of a 500-gram spool of PVA ranges from $18 to $185, with the average price being around $50. However, prices depend on the manufacturers. Among the manufacturers of PVA filaments are Arianeplast, eSUN, FormFutura, Forward AM (BASF), Infinite Material Solutions, INNOVATEFIL, MatterHackers, Mitsubishi Chemical Corporation, Neofil3D, Polymaker, PrimaCreator, Raise3D, RS PRO, UltiMaker, XYZprinting.
HIPS is much cheaper than PVA. A spool of filament is traded at a price between $13 and 38. Well-known manufacturers are Arianeplast, eSUN, Forward AM (BASF), Intamsys, Kimya, Nanovia, Neofil3D, Raise3D, RS PRO, Smart Materials 3D, MatterHackers and Zortrax. Note that the specific composition of HIPS filaments is not always the same and pay special attention to it. This is because some contain additives that can facilitate the printing process but make it difficult to remove the support after printing.
Do you already use one of the two support materials? Do you have experience with printing PVA or HIPS? Let us know in a comment below or on our LinkedIn, Facebook, and Twitter pages! Don’t forget to sign up for our free weekly Newsletter here, the latest 3D printing news straight to your inbox! You can also find all our videos on our YouTube channel.