Are powders a barrier to the development of metal additive manufacturing?
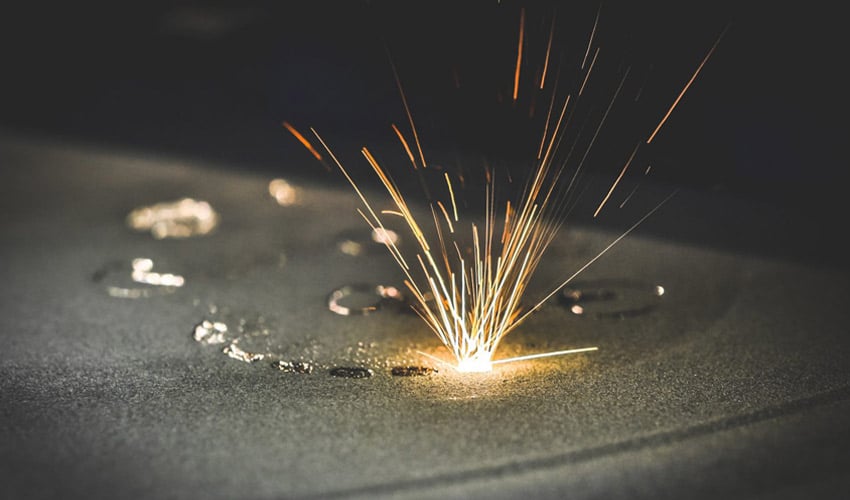
Equispheres is a Canadian company that specialises in the development of metal powders, particularly for additive manufacturing technologies such as laser powder bed fusion or cold spray. Drawing on its experience on the market, Equispheres recently conducted a study investigating the main problems confronting metal 3D printing and printers and more particularly the powder bed fusion process. According to the company, the choice of metal powder can result in more or less significant problems such as irregular mechanical properties for the final part, a reduced production speed and therefore reduced efficiency, etc. For Equispheres, this technology needs metal powders designed specifically for additive manufacturing, taking a number of factors into account. If raw material does not meet specific criteria, then laser powder bed fusion processes will not be satisfactory: this is where the main problem in 3D metal printing lies.
Much has been said about the growth of metal 3D printing in recent years, with studies highlighting the increased number of manufacturers on the market. The Wohlers 2018 report indicated around thirty players, offering more than 125 machines geared towards increased productivity to reduce a production cost that is still too expensive. In the end, the real issue is not the printers, but rather the lack of developments of adapted and innovative materials: while the polymer market sees new solutions appearing every day – many specially designed for additive manufacturing – the metal materials market is stagnant. Currently, the metal powders used in 3D printing are mainly made using gas atomization, a method not suitable for the production of materials with properties that are sufficiently constant from one production to another.
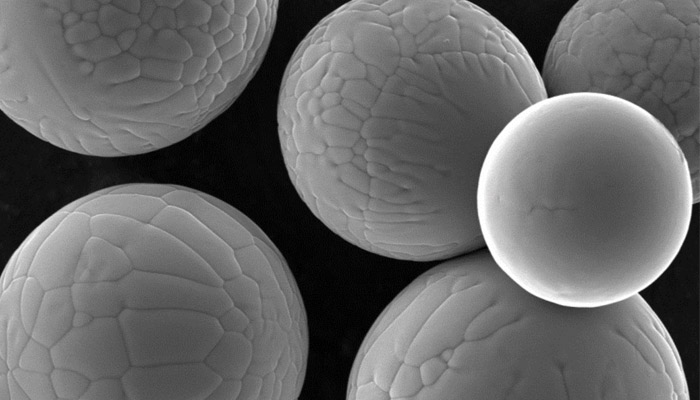
Powder is one of the principle obstacles to the development of metal additive manufacturing
Metal powders’ properties, Metal AM’s problem
Equispheres notes in its study that metal additive manufacturing often faces issues with process reliability and productivity, both challenges directly related to the material itself. According to the company, metal powders must possess 4 essential qualities : high fluidity, high distribution density, low moisture absorption and high chemical stability for when the laser heats up.
The company go on to explain that these qualities directly influence the mechanical properties of the final part. Inconsistent powder properties result in uneven energy absorption and material flow during printing, resulting in voids and irregular material properties in the final part. Despite the control systems put in place by machine manufacturers, these point-to-point inconsistencies cannot be corrected in the printing chamber. Unfortunately, even the best powder made using traditional spraying methods cannot meet these requirements, which significantly compromises build speed and the consistency of the final part.
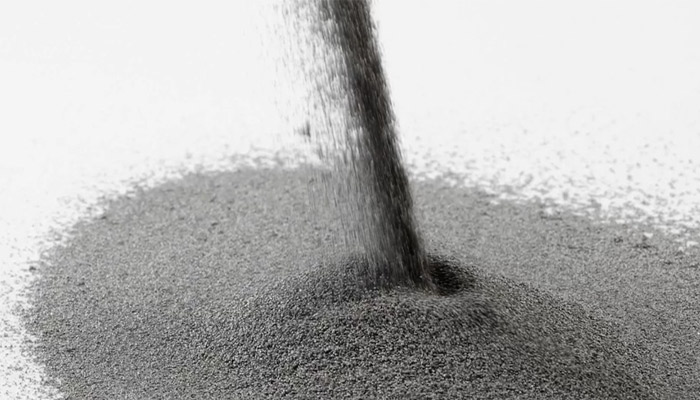
The powder must have 4 essential qualities (photo credits: Nanosteel)
It is for this reason that the metal additive manufacturing market must produce its own specialised powders. In order for a powder to produce the previously mentioned qualities, the granules that make it up must have certain key physical properties: they must be spherical, smooth, equally sized, very fine, and have a low oxygen content . These 5 characteristics form an ideal raw material for metal 3D printing. The study shows that parts 3D printed from powder conforming to these specifications have better mechanical properties, are more homogeneous and can be printed up to 50% more quickly.
The study thus acknowledges each physical property of the powder, demonstrating how each can reduce printing defects and guarantee stable and regulated final mechanical properties. You can download the whole study HERE to find out more.
Do you think powder is the main obstacle to the development of metal 3D printing? Let us know in a comment below or on our Facebook and Twitter pages! Sign up for our free weekly Newsletter here, the latest 3D printing news straight to your inbox!