Porsche Present 40% Lighter 3D Printed Electric Drive Housing
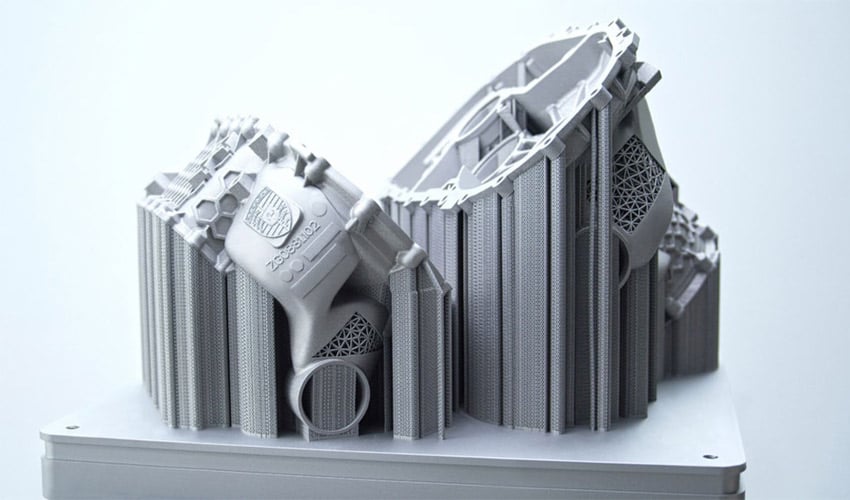
The car manufacturer Porsche has just unveiled its first complete housing for an electric engine thanks to additive metal manufacturing, or more precisely, thanks to SLM Solutions’ new machine, the NXG XII 600. Still in the prototype stage, the part would be lighter than those conventionally manufactured, reducing the total weight of the drive by about 10% and doubling the rigidity in heavily stressed areas. The prototype has passed all the quality and resistance tests successfully, proof that additive manufacturing has a bright future in the automotive sector.
Porsche has been using 3D technologies since the 1980s, first for rapid prototyping, then, with the evolution of the market, to design more and more finished parts. Today, 3D printing for manufacturers can be divided into three areas: product innovation, process innovation and new business models. Having recently introduced 3D-printed pistons for its GT cars: which are now lighter and directly incorporate a cooling duct to reduce temperature, increasing efficiency. It is then unsurprising that their new electrically powered housing was designed using the same approach.
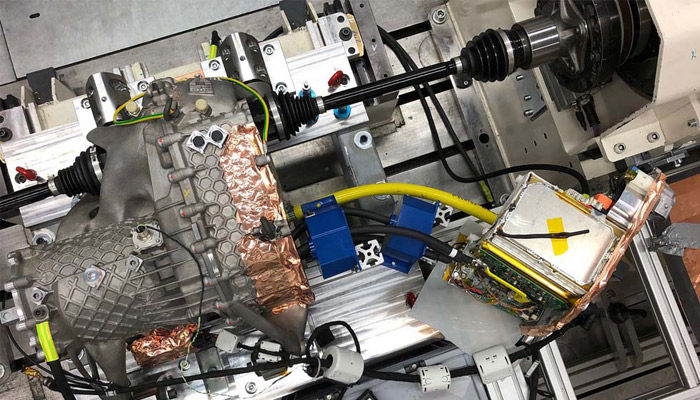
Porsche uses additive manufacturing to accelerate the prototyping phase (photo credit: Porsche AG)
Lighter and more efficient 3D printed electric drive housing
Made with a high-performance metal alloy, the housing would also incorporate the two-speed gearbox, intended to be used on the front axle of a sports car. The goal was to bring together as many features as possible in a single room, reducing the assembly steps. Falk Heilfort, project manager in the Powertrain Advance Development department at the Porsche Development Center in Weissach, explains: “Our goal was to develop an electric drive with the potential for additive manufacturing, at the same time integrating as many functions and parts as possible in the drive housing, saving weight and optimising the structure.”
The project teams explain that they used topological optimization methods to integrate the various components such as bearings, heat exchangers, etc. in the best way possible. The software was then able to calculate the loads and their trajectories to optimize the final part. This resulted in the conception of the honeycomb structures which reduce the weight of the housing by 40% and the total drive by 10%. While their walls are just 1.5 millimetres thick, these honeycomb structures are responsible for increasing the rigidity between electric motor and the gearbox by 100%.
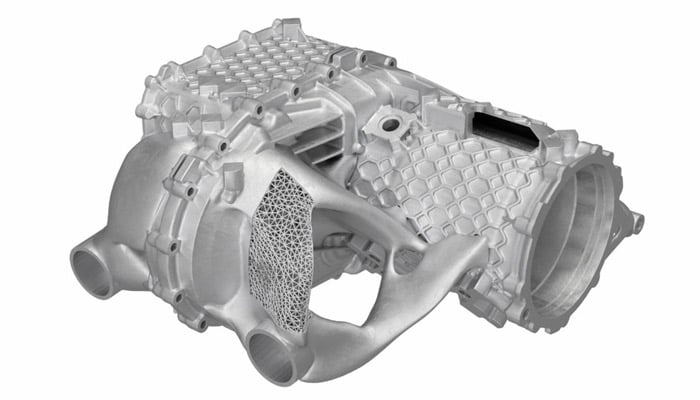
Topological optimization has made it possible to invent lighter lattice structures (photo credit: Porsche AG)
Porsche on a faster industrial machine
Porsche chose to use SLM Solutions’ new machine to make its part. Based on laser powder bed fusion technology, the NXG XII 600 incorporates 12 1,000-watt lasers, greatly increasing printing speed. The carmaker says the machine could reduce manufacturing time by 90%; taking just 21 hours to 3D print the electric drive housing. Assembly would consist of 40 fewer steps, which is equivalent to an approximate reduction in production time of 20 minutes.
Ralf Frohwerk, Commercial Director of SLM Solutions, concludes: “We are glad and proud to cooperate with highly innovate companies like Porsche. The NXG XII 600 achieves unmatched levels of performance and functional improvements of key automotive parts, while delivering cost productivity that enables broad use of Additive Manufacturing technology for true series production. We are thrilled to take this big step towards full industrialisation of metal Additive Manufacturing for Porsche applications.”
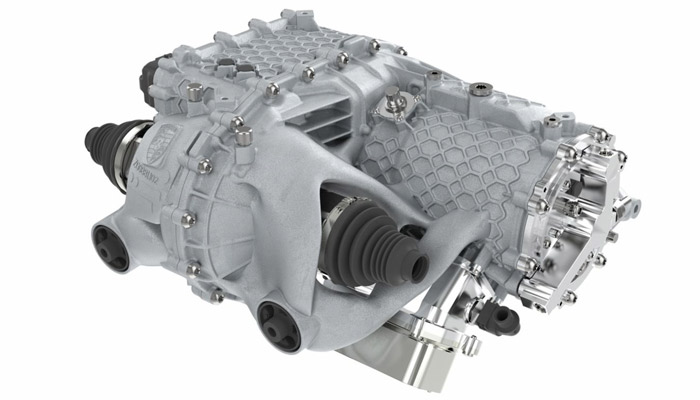
The 3D printed electric drive housing (photo credit: Porsche AG)
It remains to be seen whether Porsche will be able to rely on 3D technologies for mass production, following the direction of most car manufacturers today. Let us know what you think in a comment below or on our Facebook and Twitter pages! Sign up for our free weekly Newsletter here, the latest 3D printing news straight to your inbox!