Porsche on the use of additive manufacturing
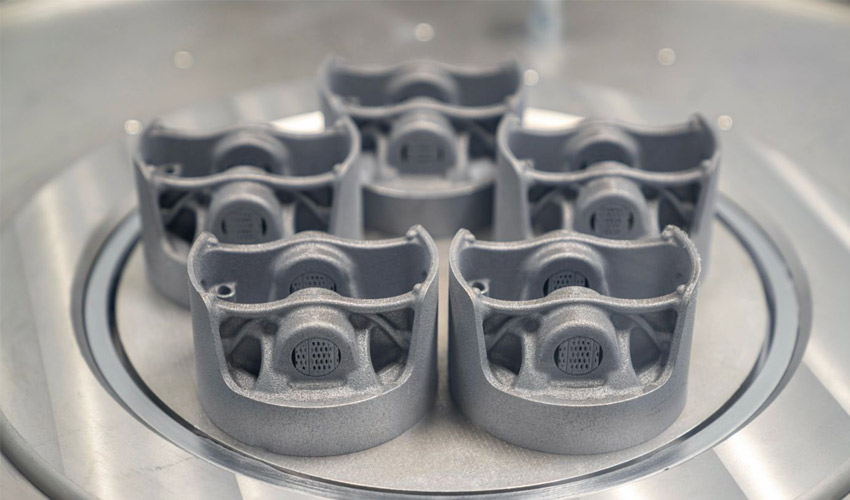
A few weeks ago, the car manufacturer Porsche presented 3D printed pistons for the engine of its famous model 911 GT2 RS. Additive manufacturing allowed Porsche to reduce the overall weight of the part as well as the production lead times and increase the final performance of the car. These are advantages that are highly sought-after in today’s automotive sector, which is increasingly oriented towards 3D printing as it offers significantly higher levels of complexity and innovation than traditional production methods. We wanted to meet with the Porsche team to find out more about how they use additive manufacturing today and what it brings to their daily business. Therefore, we discussed with Frank Ickinger, one of the members of Porsche’s advanced engine development department.
3DN: Can you introduce yourself and your link with additive manufacturing?
My name is Frank Ickinger and I work on the Advanced Powertrain Development part. I am responsible for the conceptual work on powertrains and in charge of all new development methods and technologies for powertrains. We are currently exploring the full potential of additive manufacturing at Porsche, especially for this part of our vehicles.
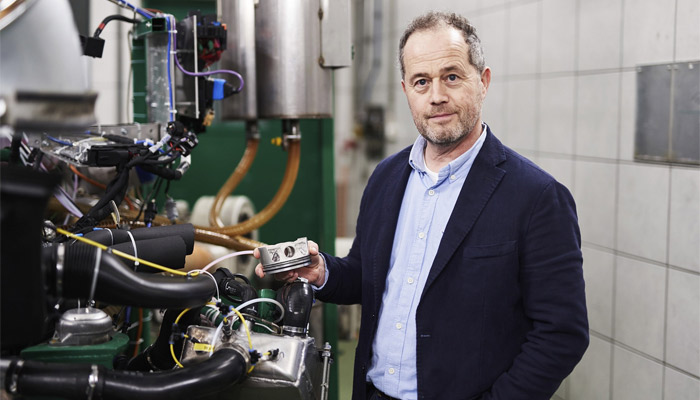
Frank Ickinger holding a 3D printed piston. (Image credits: Porsche)
3DN: Can you remind us how Porsche uses additive manufacturing today?
We have been using additive manufacturing technology since the early 1990s. At that time it was called Rapid Protoyping. Since then, we have been using it for our prototypes in the development process of plastics and metals. Today, it is a technology that is well on the way to being industrialized and we are thus hoping to realize its full potential at Porsche. We have three industry groups: product innovation, process innovation and new business models. Product innovation means that the focus is on the product, such as lightness, functional integration, etc., especially for our small series and special productions such as GT cars. Process innovation means agile development, decentralised production, etc. New business models include, for example, the fact that we print special products for our customers for the cars they have ordered, etc. We use all kinds of technologies and materials because we do not have our own in-house machine park. We simply have a small number of 3D plastic printers for the prototyping department. We follow the news and developments of the various processes on the market very closely.
3DN: You recently printed 3D pistons: why did you turn to additive manufacturing?
We would like to use additive manufacturing initially for our small series with small quantities, such as GT cars. These cars generally offer more performance and efficiency. It is therefore necessary to allow certain parts to perform better. With the GT2 RS pistons project, we wanted to find out whether it was possible to use 3D printing to design powertrain parts that are highly stressed like a piston and to build on all the advantages that the technology can provide. That’s why we made the piston lighter (10% less weight) and incorporated a cooling duct to reduce the temperature, which makes us more efficient.
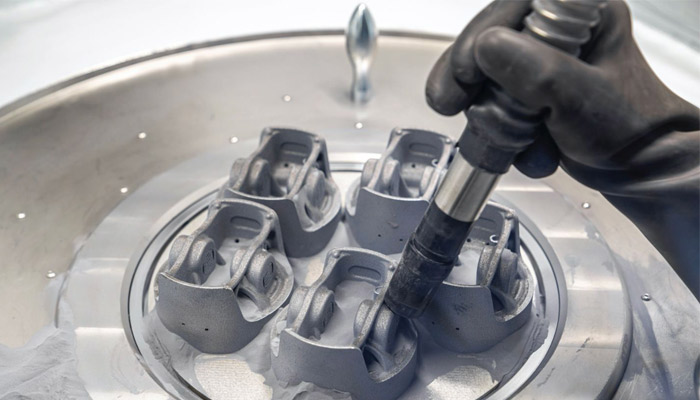
All image credits: Porsche
3DN: What difficulties were encountered?
It was mostly difficulties concerning the parameters of the materials and processes. We used a special aluminium alloy for Mahle’s cast pistons, in order to obtain the best properties for this specific application. We therefore had to develop new parameters for the printing work, which was carried out by our manufacturing partner Trumpf. This was not easy.
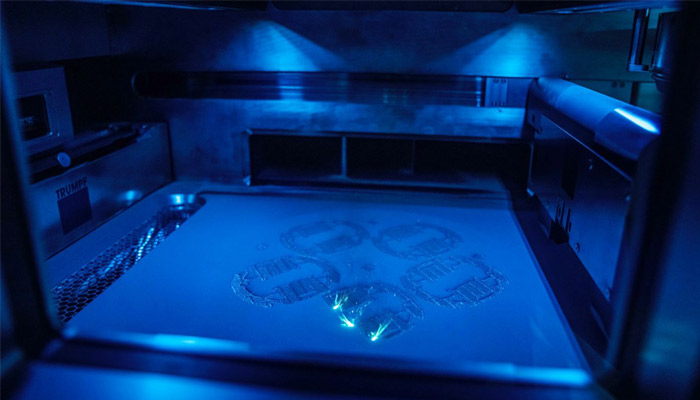
Trumpf’s 3D printers were used to design the pistons.
3DN: What DfAM techniques did you use to design the pistons?
We developed an end-to-end construction method, from CATIA to topological optimization, through STL files, back to CATIA where we do the redesign of the topological optimization, then we go into the 3D printer software to check the support structure. It’s a process that repeats until we get the final geometry. This method works very well.
3DN: In your opinion, what is the future of additive manufacturing in the automotive industry?
I am certain that additive manufacturing will be an integral part of automotive development and production in ten years at the latest. Stay curious, it will surely happen sooner than expected! You can find more information about our 3D printed pistons HERE.
What do you think about Porsche using additive manufacturing in its production? Let us know in a comment below or on our Facebook and Twitter pages! Sign up for our free weekly Newsletter, all the latest news in 3D printing straight to your inbox!