Researchers Develop Multi-Material DLP Method For Plastic-Metal Composites
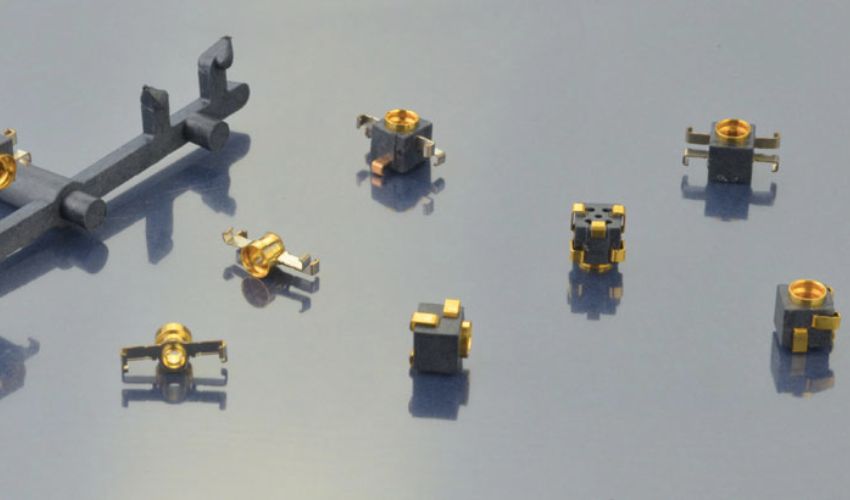
Both plastic and metal are key materials within many 3D printing processes and applications. When combined to make plastic-metal composites, the properties are modified to apply to a number of fields as the final product has metal and plastic integrated within its structure. However, current methods to do this are expensive. Researchers at Waseda University, Japan, and Nanyang Technological University (NTU), have therefore developed a process for the fabrication of these structures, known as multi-material DLP additive manufacturing or MM-DLP3DP.
The researchers performed a multi-step process. To start with, they prepared active precursors: that is, the chemical which was transformed into a different chemical. They used NH4Cl in 50 mL of deionized water, to which 270 mg of PdCl2 was added. Once fully prepared, they mixed this with one of the light-curable resins. The palladium ions allow the metal particles in solution to be deposited in ELP: this essentially means that the metal ions settle onto a pre-existing surface to form the metal pattern. In short, this first step consisted of the creation of modified resins for the ELP process.
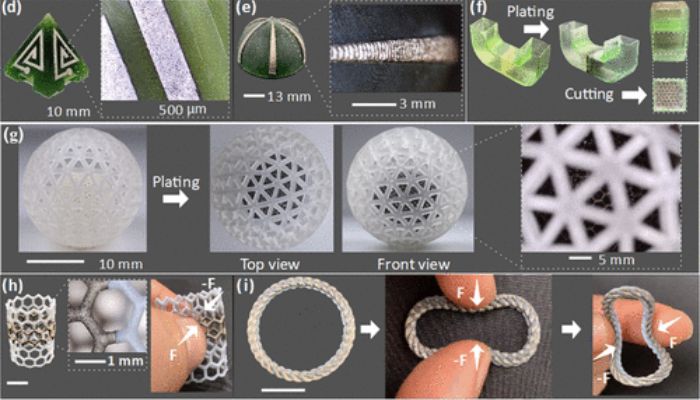
Examples of plated parts made with multi-material DLP 3D printing. (Photo credit: Waseda University)
Next the MM-DLP3DP process was used to make micro-structures of nested regions of the resin or active precursor together. Finally, they plated the materials and added 3D metal patterns with the use of ELP. To demonstrate the usefulness of this technology, they manufactured a 3D circuit with a double-sided structure which was connected by a through-hole, and also a series of sensors which can be integrated with the product being measured (a general example would be a thermometer manufactured with an integrated temperature detector). As they showed, MM-DLP4DP has ‘higher resolution and thus allows the construction of microstructured surfaces with special functions’ when compared to multiple-nozzle printing.
The researchers hope that this method could be applied to electronics, including sensors and robotics and wearable devices, as the integrated manufacturing reduces the risk of errors. Lead authors Professor Shinjiro Umezu and Kewei Song from Waseda University and Professor Hirotaka Sato from NTU Singapore, put it this way: “Robots and IoT devices are evolving at a lightning pace. Thus, the technology to manufacture them must evolve as well.”
Within the field of additive manufacturing, composites are fairly common as a way of improving the properties of a material before the product is fabricated. Common examples include carbon fiber and kevlar. The development of a resin-metal composite, however, is fairly novel. In July of this year, researchers at the Department of Electrical Engineering at the University of South Florida (USF) developed a method to print copper on fabric in order to make wearable fabrics. The potential of these projects is clear, and it is only a matter of time before it is realized on a large-scale. If you would like to learn more, the research paper is available HERE.
What do you think of this multimaterial DLP technology? Let us know in a comment below or on our LinkedIn, Facebook, and Twitter pages! Don’t forget to sign up for our free weekly Newsletter here, the latest 3D printing news straight to your inbox! You can also find all our videos on our YouTube channel.
*Cover Photo Credits: Vogt