Rigid or Elastic? The Plastic Material that Changes Properties Thanks to 3D Printing
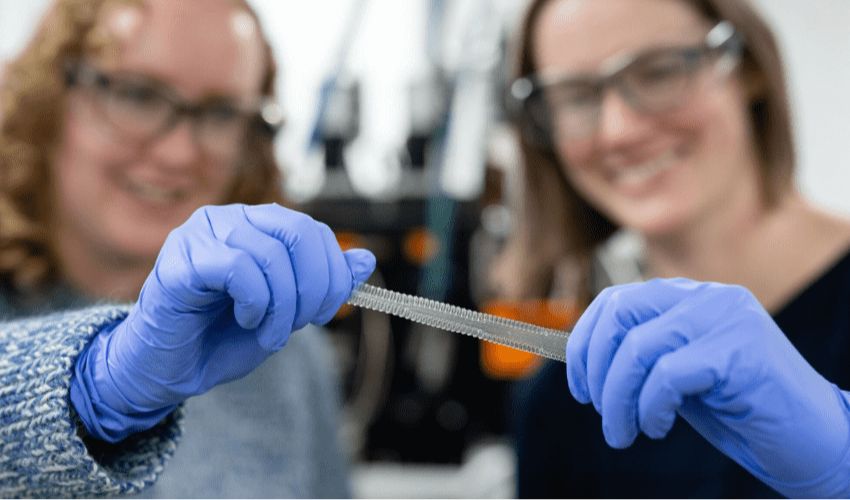
In recent years, many university research projects have been developing multifunctional materials through additive manufacturing. In the medical field, for example, it is important to create fabrics capable of regenerating organs or bone structures and design advanced biomedical devices. At the same time, other sectors are creating new 3D printable materials, offering a wide range of potential applications.
To demonstrate this, Alice Fergerson and a team of engineers from Princeton University, led by Emily Davidson, have developed a plastic material capable of adopting different levels of flexibility. The material, composed of a class of polymers known as TPEs, enables the design and manufacture of flexible 3D-printed structures whose rigidity can be adjusted. Thanks to 3D printing, engineers have been able to control the physical properties of this material, enabling the fabric to stretch and bend repeatedly in one direction while retaining rigidity in another.
The Characteristics of Plastic Material
The thermoplastic elastomer selected by the Princeton University engineering team is a block copolymer that can be molded when molten. As it cools, it solidifies to form an elastic structure. This phenomenon is explained by the behavior of the copolymer’s internal components, composed of homopolymers, which separate like oil and water rather than mixing. The researchers used this characteristic to create a material consisting of rigid cylinders dispersed in an elastic matrix, enabling the material to remain flexible while retaining its internal properties.
The rigid cylindrical structures of this plastic material have a thickness of 5 to 7 nanometers and are embedded in an elastic polymer matrix. For context, a human hair measures around 90,000 nanometers in diameter, while a DNA helix is around 1 nanometer. The researchers also studied how printing speed and controlled material extrusion can modulate the physical properties of the printed material. Thanks to 3D printing, cylinders can be oriented at a nanometer level, creating a material offering localized rigidity while maintaining soft, elastic zones.
Its Self-Repairing Properties
The most interesting aspect of this process lies in the thermal annealing of the plastic material and its self-healing properties. Fergerson explained that thermal annealing significantly improves the material’s properties after printing. This process enables objects printed in the laboratory to be reused several times, and even to repair themselves if damaged. To demonstrate these self-repair properties, the researchers cut a flexible sample of the printed material and repaired it by annealing. According to their observations, the repaired material showed no noticeable difference from the original.
Davidson points out that similar materials used in other contexts are expensive and require complex processing, such as controlled extrusion followed by ultraviolet light treatment. These materials can cost around $2.50 per gram. In contrast, the thermoplastic elastomer used in this project costs only around one cent per gram and can be printed using commercial 3D printers. This makes the material not only economical but also accessible for low-cost printing solutions.
One of the main aims of the project was to develop soft materials with locally adjustable mechanical properties while adopting a cost-effective and easily scalable approach for industry. Davidson believes that this method of designing advanced soft materials could have applications in various fields, such as soft robotics, medical devices, prosthetics and high-performance customized shoe soles. The next step for the research team will be to create new 3D printable architectures, compatible with applications such as wearable electronics and biomedical devices. For more, read Princeton Engineering’s press release here.
What do you think of this plastic material? Let us know in a comment below or on our LinkedIn, Facebook, and Twitter pages! Don’t forget to sign up for our free weekly Newsletter here, the latest 3D printing news straight to your inbox! You can also find all our videos on our YouTube channel.
*All Photo Credits: Princeton Engineering