Should you adopt 3D printing for plastic end-use parts? The Complete Guide
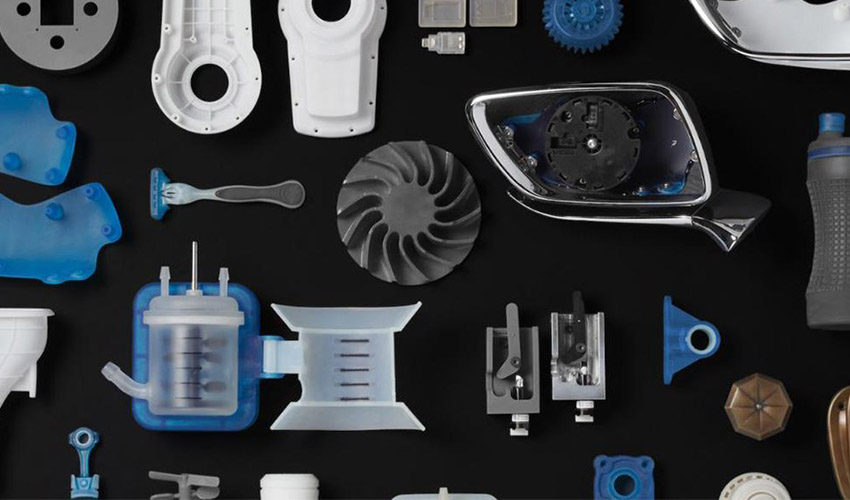
What is a plastic end-use part exactly?
An end-use part is a manufactured good that is either ready to market, part of an assembly of products or ready to be used in the internal operations of a company. A plastic part ready to market could be a plastic cover or medical model, for internal use it could be a customized jig or even a fixture. Finally, an end-use part such as a plastic clamp can be used on an assembly line to hold parts while they are being put together.
In other words, plastic end-use parts are useful for a number of applications and sectors. When looking at 3D printing technologies, we are now aware of the benefits of using these instead of traditional manufacturing methods for many industries. But how much exactly are you benefiting from the adoption of additive manufacturing? In order to answer this question, we spoke to one of the industry’s experts, Hubs. They were able to give us some practical advice and examples by comparing 3D printing technologies (FFF, SLA, DLP, SLS, MFJ) with traditional manufacturing processes for different applications.
1. Fused Filament Fabrication (FFF)
Fused filament fabrication, also known under the trademarked term Fused Deposition Modeling (FDM), starts with a roll of thermoplastic filament. The filament is fed into a heated nozzle, melted, and extruded: creating a three-dimensional object layer by layer. This is the most common additive manufacturing process, also easy to use, and widely available – these three elements make this process economical with quick production times, an important benefit for many companies.
For this technology, the materials that can be used include commodity thermoplastics, engineering thermoplastics (e.g. ULTEM and PEEK), as well as various composites for advanced applications. Our expert at Hubs recommends the FDM process for parts used in internal company operations and for low-volume production, up to around 100 units. Below, you will find 2 examples of uses of this technology for the production of end-use plastic parts.
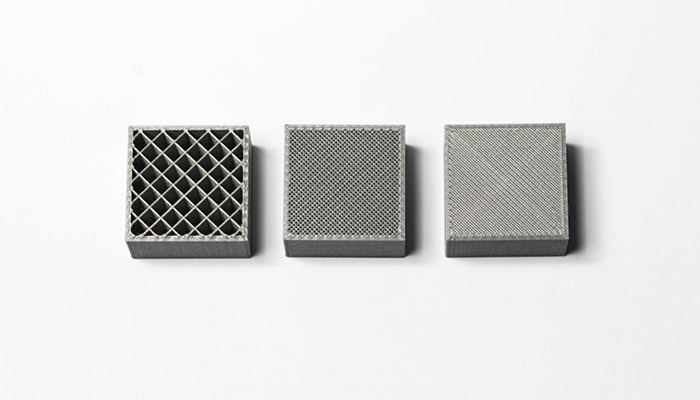
The internal geometry of FDM prints with different infill density | Credits: Hubs
Application: Jigs, Fixtures, and Brackets
Some of the requirements on these plastic end-use parts include: low to medium mechanical strength and durable and thermal resistance. When comparing the technologies that exist to manufacture such parts, the expert at Hubs explains: “The lead time needed is only two to five days. The cost would be about 60 euros for one, down to about 20 euros a piece for quantities up to 50. On a CNC machine, the lead time needed increases to between ten and fifteen days. The cost would be about 120 euros for one, down to around 15 euros a piece for quantities of 100.” Therefore, substantial time and money is saved by adopting the technology.
“With sheet fabrication, the parts would have to be made of metal. The lead time would also be between ten to fifteen days and the cost would be about 100 euros for one and spiraling down to around 10 euros a piece for quantities up to 100.”
Application: Medical Devices
Some of the requirements on the parts for the medical sector include: high mechanical strength, biocompatibility, and heat resistance. When comparing the 3D printing technology to more traditional manufacturing techniques, our expert at Hubs explains: “The lead time for the FFF/FDM 3D printing process would be about three to eight days. If made on a CNC machine, the lead time would be ten to fifteen days. These products can also be made by injection molding, but the lead time increases to between four and six weeks.”
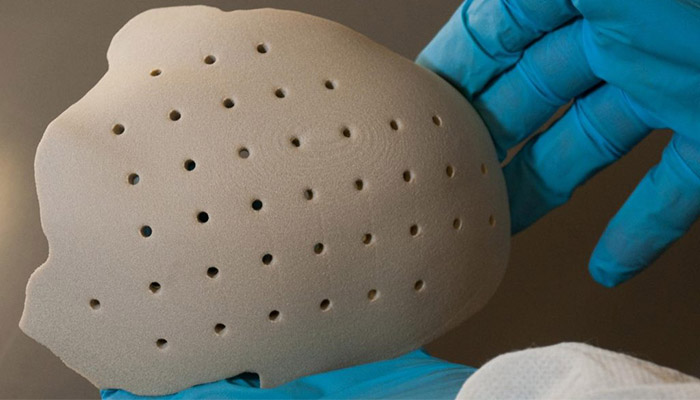
3D printed implant | Credits: Oxford Performance Materials
“The cost per unit with the FFF/FDM process would be 30 to 90 euros for quantities of 1 to 100. On a CNC machine, the cost would be 50 to 300 euros per unit for quantities of 1 to 200. With injection molding, the quantity would have to be greatly increased to be economical. For quantities of 500 to 5,000, the cost would be 20 to 50 euros per piece.”
Materials that can be used in the FFF/FDM process are ULTEM and PEEK, but PEEK would be the only choice for CNC machining and injection molding. PEEK being an expensive product, when produced with CNC and with injection molding, the cost is still quite high when compared to 3D printing, even at high quantities.
2. Stereolithography Apparatus or Digital Light Projector Process
The stereolithography (SLA) process (or 3D printers with a Digital Light Projector, known as DLP) uses an ultraviolet light to solidify a liquid resin in a vat. The SLA/DLP process has several strengths that are well known within the industry. These include smooth surface finish, high accuracy and resolution on the parts. The finish can even be compared to an injection molded part. It is extremely difficult, if not impossible to achieve this quality for FDM 3D printed parts.
On the other hand, a downside to using the SLA/DLP process is that it requires a support structure. Therefore, this process is only economical in small series production runs. Hubs recommends the SLA/DLP manufacturing process for mass customization for smaller volumes, usually up to 50 units. By mass customization, we are talking about products that are all individually different but that have been produced in quantity. An example would be a toothbrush handle of varying circumferences and colors.
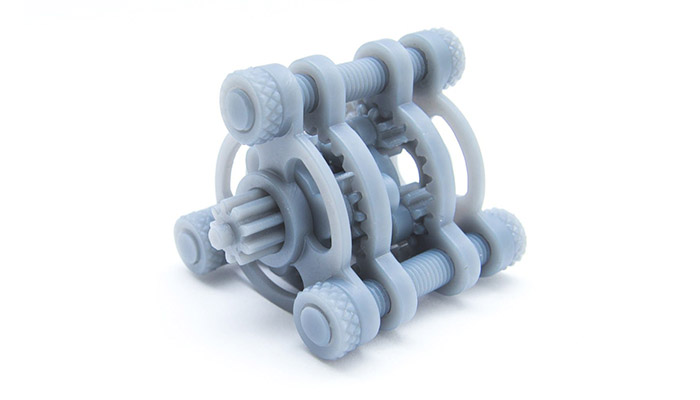
SLA 3D printed piece shows high detail and smooth surface, injection mold-like prototyping | Hubs
For this process, materials that can be used include thermoset resins and engineering grade resins (available both in clear and color). Thermoset resins tend to be more brittle than thermoplastics.
Application: Custom Razor Blade Handle
Our expert at Hubs explains that one real-life project was the making of some custom razor blade handles in a variety of colors: high mechanical strength was not necessary, but they needed it to be lightweight and have a glossy finish, which is why SLA was an appropriate choice.
“With 3D printing, the lead time needed for this project was only two to five days. The cost would be 30 euros for one piece, reduced to 10 euros each for 30 units. If the project coordinators were to choose CNC machining instead, a 5-axis machine would be required and the lead time would jump to between ten and fifteen days. The cost would rise astronomically to 150 euros for one and 50 euros each for an order of 30.”
“Vacuum casting is another option to produce the customized razor handles. The lead time for the production would be high at ten to fifteen days. The cost of the casting process is also high. Vacuum casting would be about 120 euros for one handle, and for 30 handles, they would be about 30 euros each.3D printing using the SLA/DLP process was clearly the best choice for this project.”
3. Selective Laser Sintering and Multi Jet Fusion
Selective Laser Sintering (SLS) and Multi Jet Fusion (MJF) are similar processes that use a heat source to bond plastic powder particles together into a solid structure. Hubs recommends this process for low production runs up to 300 units. Some of the benefits of these two technologies include high strength parts and isotropic properties. Also, SLS and MJF do not require support structures, therefore multiple parts can be produced simultaneously in one batch.
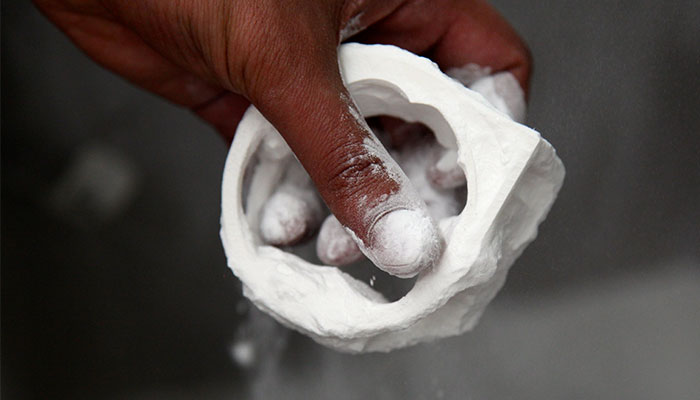
An SLS 3D printed piece
In terms of materials, compatible materials for this technology include nylon (PA 11, PA 12), carbon-filled nylon, which adds strength while being lightweight, glass-filled nylon, which also adds strength and reduces lubricated wear properties. Finally, it is also possible to use TPU (Thermoplastic Polyurethane), which is resistant to abrasion and chemicals. The mechanical strength of parts is usually medium, however they are durable and present a very smooth surface finish.
Application: General
Hubs explains: “A low production run of product using the SLS/MJF 3D printing process will require five to ten days of lead time. Your cost would run between 15 to 35 euros a piece for a 50 to 300-unit production run.
Vacuum casting would also be an option. The lead time for vacuum casting would need to be ten to fifteen days. Since vacuum casting is labor intensive, the cost of this process would be 30 to 40 euros per unit for a 50 to 200-unit production run.
Injection molding could be a cheaper option, but it would take a longer wait time and a higher volume order. The lead time would be 4 to 6 weeks and the cost per piece would range from 3 to 10 euros for orders of 500 to 5,000 units. In other words, it is best to mass manufacture with injection molding and produce spare parts on-demand with SLS/MJF.
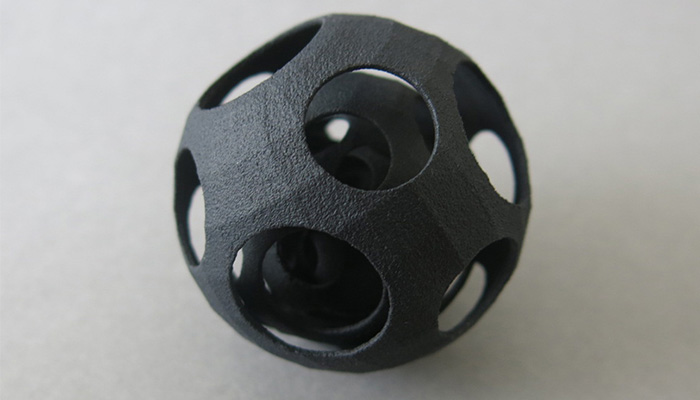
A 3D printed piece using Multi Jet Fusion (MJF) | Credits: Sculpteo
Who is Hubs?
Hubs online 3D printing service is a well-trusted source for on-demand, economical, and quality end-use plastic parts. Their experience and expertise will help you accomplish your projects in a timely and skillful manner.
*Cover Image Credits: Formlabs
Was this guide useful? Let us know in a comment below or on our Facebook and Twitter pages! Don’t forget to sign up for our free weekly Newsletter, with all the latest news in 3D printing delivered straight to your inbox!