PLA vs ABS: Which Material Should You Choose?
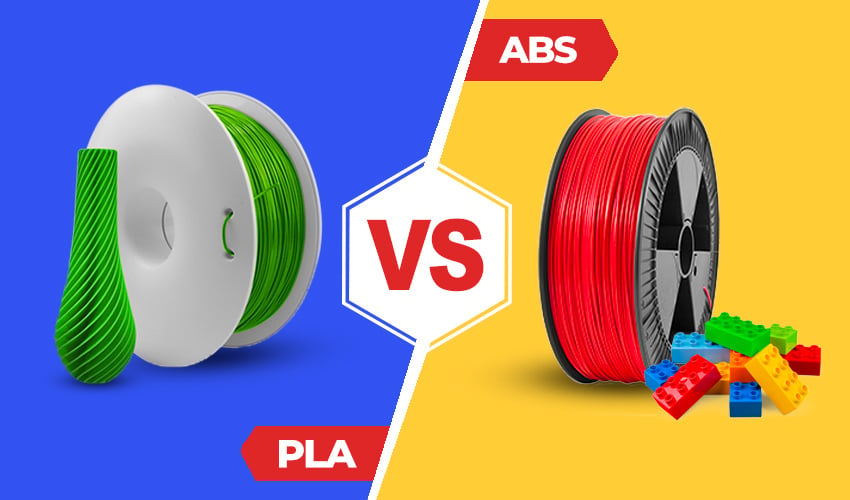
When it comes to 3D printing polymers, it can be hard to decide which one to use. This is the case for pretty much any 3D printing technology, but especially for beginners or hobbyists using FDM/FFF 3D printing for whom it can seem impossible to know which filament is most appropriate. Previously, we have broken down the differences between two 3D printing filaments, PLA and PETG. Now, we want to go even further, comparing two of the most popular and widely used filaments, PLA vs. ABS. From properties to printing requirements and more, we took a closer look at the similarities and differences of PLA and ABS to help you better understand which to use depending on your needs.
Characteristics and Properties of PLA vs ABS
Of course, when talking about the characteristics of PLA vs ABS, the first thing to consider is what they are made of. Though both are what would be considered thermoplastics, polymers that can be softened through heating before cooling and hardening, that is where the similarities end. Famously, PLA is made out of organic sources such as corn or sugar cane, meanwhile ABS, like most standard plastics, is made out from petroleum. More specifically, PLA is made from fermented plant starch from sources like corn, cassava, maize, sugarcane or sugar beet pulp. The sugar from these sources are transformed into lactic acid which is then polymerized into polylactic acid. In contrast, ABS is made up of three monomers: acrylonitrile, butadiene and styrene. Acrylonitrile is a synthetic (man-made) monomer that comes from propylene and ammonia, butadiene is a petroleum hydrocarbon and styrene is made from the dehydrogenation (the removal of hydrogen by chemical reaction) of ethyl benzene. Understandably, the makeup of these materials has an impact in terms of “sustainability” of the materials.
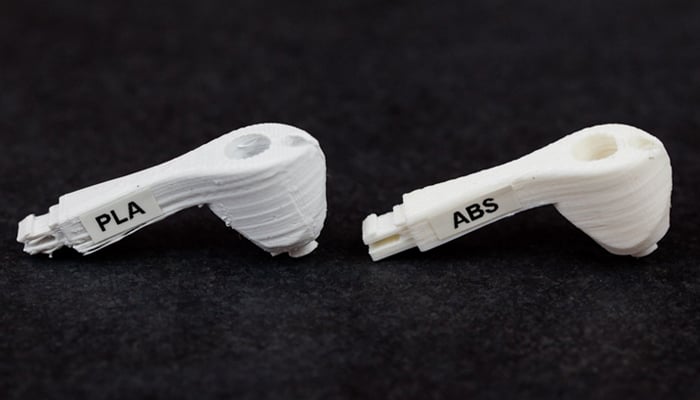
Parts 3D printed with PLA vs ABS have differences in both their appearance and properties, as can be seen above (photo credits: Fictiv).
PLA is often lauded as a more environmentally friendly material because it is in fact biodegradable. However, it is important to note however that it is only truly biodegradable under the right conditions and many towns do not have the right tools to properly degrade the material. This means that though it is possible, in actuality it would only truly be able to be done through industrial composting. Therefore, though PLA is of course more “green” than many materials, especially since it is made out of renewable resources, it is perhaps not as environmentally friendly as it is often purported to be when it comes to disposal.
On the other hand, ABS is not considered to be a sustainable or environmentally friendly material. As previously mentioned, it is made, as are most plastics, from petroleum, meaning its processing is not as sustainable. However, what is a plus is that ABS is recyclable, though it is not widely accepted by recycling centers. Considering that many people do not realize how limited the biodegradability of PLA is, this could even be considered a plus for beginners who could potentially be more sure that the plastic would be appropriately disposed of without creating more waste.
Moving beyond the roots of the material, ABS and PLA also have distinctive properties that cause them to differ from each other. One, which will also be a factor when discussing ease of print, is the heat resistance of each one. Namely, ABS is resistant to heat and has a higher glass transition temperature, whereas PLA melts at much lower temperatures and is thus not considered heat resistant. This of course impacts applications for the materials, which will be covered later on.
Generally speaking, if you are looking for a material that is tougher with better mechanical properties, you will want to choose ABS. Beyond being heat resistant and having a higher heat deflection, it is also impact resistant, more durable and lighter than PLA. That being said, the two materials have similar tensile strength (ABS is slightly lower however) though ABS is often preferred for more industrial applications thanks to properties such as its improved ductility, or the ability of a material to be deformed without fracture, as well as a higher flexural strength and better elongation before breaking. In essence, these mean that ABS is more flexible compared to the more brittle PLA. These together enable ABS to even be used for end-use applications and is one of the reasons it is so popular in industries like injection molding.
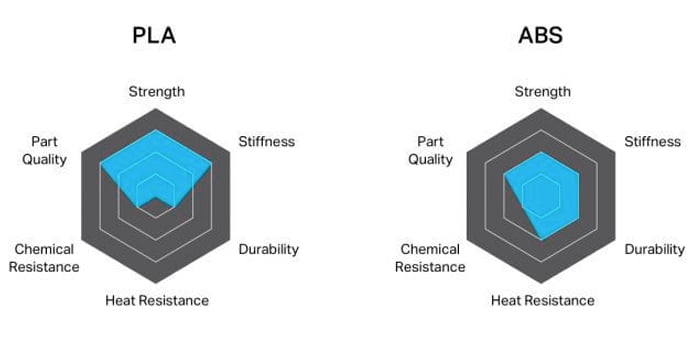
Characteristics of PLA vs ABS
PLA however wins in a few other categories. Notably, it is both stronger and stiffer than ABS. Still, because of its low melting point, it loses these properties above 50 degrees Celsius, making it less useful in any application involving heat. However, even if ABS is significantly more heat resistant than PLA, as both are thermoplastics they do both degrade over time in UV light as well as in heat. For parts that will be outside therefore, different materials would be preferable.
Ease of Print
Now that we have covered the characteristics and properties of PLA vs ABS, next step is to discuss the 3D printing process itself. To begin with, since the glass transition temperature is different between the two thermoplastics, the preparation of the print will vary. This is because the temperature range in which a thermodynamic transition occurs in matter needs to be taken into consideration. In the case of PLA, the glass transition temperature range is between 60 – 100ºC, while ABS is between 105 – 200ºC. This subsequently determines the melting point of the material, or when it will be in a liquid state and thus ready to print. Depending on the parameters set in the slicer, it will take more or less time to heat up the 3D printer and reach the desired temperature.
Related to this, it is essential to correctly set the variables of the manufacturing process, both the bed and the print head. ABS requires a high print bed temperature, around 80-110ºC, as opposed to the 60ºC usually established for PLA. As far as the extruder is concerned, PLA also requires a lower temperature, specifically around 180-230°C vs the 210-250°C needed for ABS.
In terms of ease of use, ABS is known to be more complex to print than PLA. The printing difficulties encountered are also related to the temperature and properties of each material. PLA melts at a lower temperature than ABS, therefore, when the 3D printing process of the part is finished, the thermal change for the layers to solidify is lower. However, since ABS requires higher temperatures to melt, there will be a more abrupt change when cooling the parts. This thermal shrinkage can lead to misshapen parts. In fact, one of the most common problems is warping, in which the ends of the part contract, detach from the tray and deform. To avoid this phenomenon, it is crucial to control the temperature and the printing environment when printing with ABS, and use adhesives if necessary. This is also one of the reasons why it is often strongly recommended to use a 3D printer with an enclosed chamber when printing with ABS.
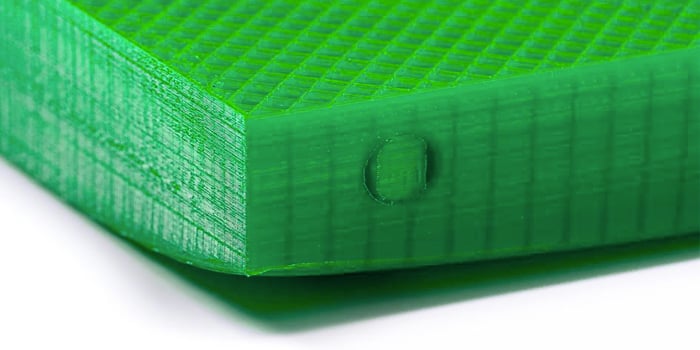
ABS tends to suffer from the warping, a problem related to the shrinkage of the material under sudden temperature changes
Both materials have approximately the same print speed, which is an advantage since there is no need to readjust the parameters in the slicer for the different materials. PLA generally prints at 60 mm/s, although some users have even worked with higher speeds. ABS on the other hand, is usually in the range of 40-60 mm/s, and it would be difficult to reach a higher speed.
Another point to keep in mind during the manufacturing process is the emissions that are generated during manufacturing. Like almost every thermoplastic filament, noxious odors and gases are generated during printing, although some are more harmful than others. When the material is heated, it releases substances containing particles that are harmful to health. In the case of PLA, as it comes from natural, plant-based sources, it does not give off a strong odor and is therefore not something to be concerned about. However, ABS is known to emit toxic gases and an unpleasant odor. In fact, this is another reason why it is strongly recommended when using ABS is to have an enclosed print enclosure as well as an air filter to prevent fumes from being released into the workspace. And even then, it is advisable to ventilate the room continuously to ensure that the fumes do not reach our lungs. This is related to the presence of styrene in ABS, a material that is toxic to human beings when inhaled.
Finally, to learn first-hand about the properties and printability of both filaments, we spoke with industry professionals. Luke Taylor, Marketing Manager at Polymaker, explained: “PLA is a weaker material but the advantage is that it is very easy to work with, it prints very easily. You do not need a heated bed, you do not need high temperatures, it has very low shrinkage rates, whereas ABS has a very high shrinkage rate. And it makes sense, generally speaking we see that the better the mechanical properties, the harder it is to work with. Though we can also add things to PLA to make it stronger without changing the printability“.

Figures 3D printed with PLA filament from Polymaker (photo credits: Polymaker)
Post-Processing
When thinking about PLA vs ABS, it is safe to say that similar post-processing techniques can be used for both thermoplastics. Though there are a few noticeable differences, one of which is in the finish of the part after printing. PLA parts are shinier immediately after removal whereas ABS tends to have a more matte finish. Both materials can also be painted for decoration after printing.
However, ABS is generally easier to post-process than PLA. This is for a number of reasons. First, though both can be sanded, the process is easier with ABS thanks to its durability. PLA can be harder to sand as well because it melts easier due to its low heat resistance. Machining is also possible with both, but again users must be more delicate with PLA.
ABS meanwhile is not only easier to post-process with these basic methods, but if you want a truly shiny finish, parts made with ABS can be smoothed with acetone vapor. Acetone is a colorless liquid often used as a solvent for plastics. Though it cannot be used with PLA, those with ABS parts can use acetone for much faster post-processing as well as a glossy finish. It is possible nevertheless to do a similar process with PLA. THF, or Tetrahydrofuran, can be used for hand polishing if you wish to do a vapor smoothing process with parts made out of PLA filament.
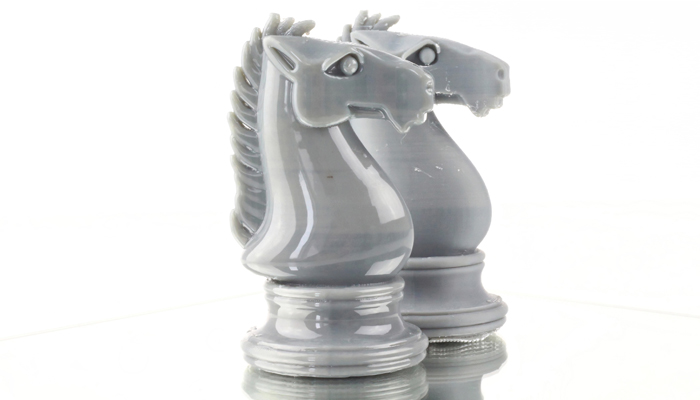
These finished parts have a glossy finish thanks to acetone smoothing (photo credits: Zortrax)
Applications for PLA vs ABS
Another major difference that we can find when discussing PLA vs ABS concerns which applications are used for each material. Depending on the purpose of the proposed part, we can choose one or the other. PLA is the most used material in FDM 3D printing, and it is mostly used in a maker environment. This is mainly due to its ease of printing, as well as its mechanical properties that make the parts fragile, weak and sensitive to the sun and high temperatures. For this reason, it is often widely used by novice users or for the creation of decorative elements and toys.
On the other hand, ABS is a more industrial material that offers advanced properties and, although it is more difficult to print, the parts have better qualities. It is therefore often used in the development of prototypes, gears or tooling. In short, it is usually implemented in situations where parts can be subjected to physical stresses and where high mechanical and thermal resistance is required. Therefore, before starting the additive manufacturing process, assess the differences between both materials to create parts according to their use.
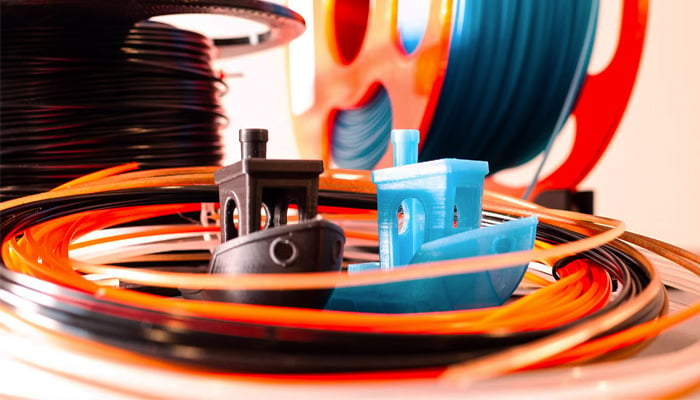
PLA is typically used for more maker applications, decorative elements and toys. On the other hand, ABS can be used for applications where higher mechanical and thermal resistance is required.
Price
In terms of price, there is functionally no difference between PLA and ABS. Price instead differs by factors such as manufacturer. Manufacturers especially play a role when it comes to 3D printers that have a closed system. This means that the only filaments that can be used with said printers are ones made or approved by the manufacturer in question. This decision is often made as a way to ensure quality control, however it can impact price. Though again, in a closed system, the prices of ABS and PLA filament will still be similar if not the same.
Generally, we found that 1kg of PLA and ABS filament starts at around $18, though on average the price for a basic filament roll seems to be around $20. Of course, if you want higher quality filaments or special features like multicolor or professional grade, the price will go much higher. Nevertheless, it should be noted that since PLA is probably the most popular 3D printed filament, as previously mentioned, there tends to be a wider array of colors and options available for PLA filaments and you will find it sold by most material or 3D printer manufacturers.
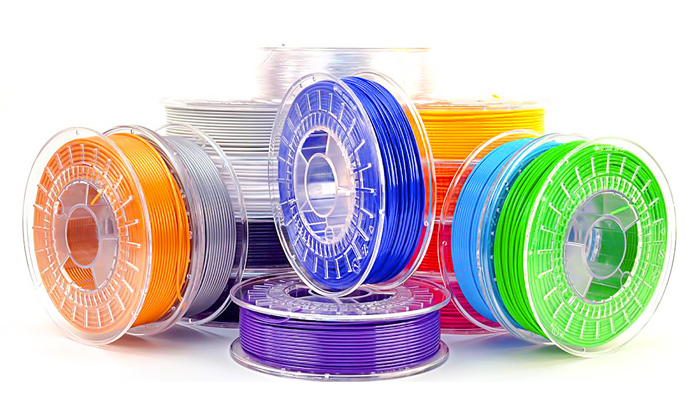
Photo Credits: ColorFabb
Though occasionally ABS filaments are more expensive than PLA filaments, due to less availability, this is actually reversed in raw form. As one of the most popular industrial plastics, used for example by manufacturers such as LEGO, ABS is actually less expensive as a raw material, that is to say before being processed into a shape such as a filament. Though this does not have much of an impact for FDM printers, for those using pellets, this could also be a factor as in this case ABS would likely be cheaper than PLA.
Manufacturers of the Materials
In the additive manufacturing market, the number of companies dedicated to materials development is truly extensive. Since FDM 3D printing is the most widely used technology, whether by beginners or industrial companies, most manufacturers develop thermoplastic polymer filaments. Because PLA is more popular than ABS and more democratized, the offer is much larger. There are now hundreds of different brands, colors and blends, and although ABS filament is also available in several brands and colors, the supply is smaller than PLA. As for manufacturers of PLA materials, we can find companies specifically dedicated to the development of filaments, such as Polymaker, ColorFabb, Filamentum, MatterHackers, etc.
If we focus on ABS, we can see that, in general, companies that develop this type of filaments, probably also manufacture PLA. In this sense we can also find Polymaker, Hatchbox or Filamentum, among many others. Nor can we forget the machine manufacturers who, although it is not their main activity, also devote part of their time to develop 3D printing materials. In this case it is worth mentioning companies such as Ultimaker, Zortrax or Flashforge.

A comparison between PLA and ABS (image credits: 3Dnatives)
What do you think of the comparison of PLA vs ABS? Do you have a preferred material? Let us know in a comment below or on our LinkedIn, Facebook, and Twitter pages! Don’t forget to sign up for our free weekly Newsletter here, the latest 3D printing news straight to your inbox! You can also find all our videos on our YouTube channel.