Reinforcement of PLA For 3D Printing Using Plant Waste
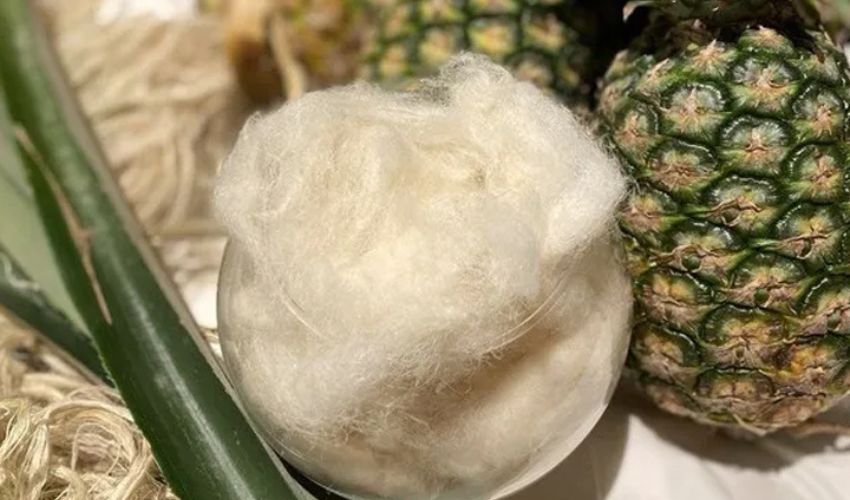
A recent study from an international group of researchers suggests that pineapple leaf fiber (PALF) could be used to reinforce polylactic acid (PLA). They tested two types of PALF (raw, and alkali-treated) combined with PLA, and results showed better ductility for the former, and better tensile strength for the latter. Both were, however, an improvement on the PLA alone. This could have big implications for 3D printing using plant waste. Polylactic acid is a thermoplastic polymer, the most widely used plastic filament material for 3D printing. Its characteristics of partial biodegradability, good thermal stability and ease of processing make it a popular choice for many industries. Therefore, any method to improve its properties is important.
The Research Process
The researchers were an international team, led by scientists Dr. Mansingh of India, Dr. JS Binoj of Malaysia and Associate Professor Eugene Wong of Singapore. To begin their study on plant materials and 3D printing, they took two samples of PALF. One was left untreated, while the other was treated with alkali of various weight percentages. Each was then separately tested by combination with PLA and then extruded in an FDM process. They used the Ultimaker 3 for this step. Several tests were carried out to assess the new properties of the product. These included infrared spectroscopy, microscope viewing to check for impurities, and thermal analysis which checked for thermal stability (how the mass changed over time with change in temperature).
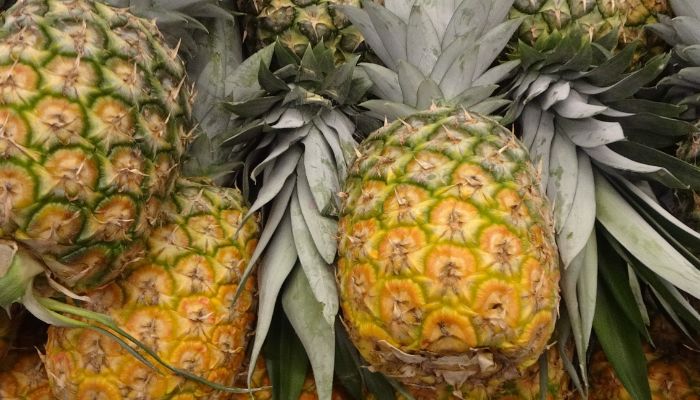
The researchers were seeing if pineapple waste could be combined with PLA to make stronger but still biodegradable filament (photo credits: David Adam Kess, CC BY-SA 4.0, via Wikimedia Commons)
They found that untreated, or raw, PALF had higher elongation at break than alkali-treated, meaning a better ductility. However, alkali-treated PALF reinforcement at 3 wt% exhibited maximum tensile and flexural characteristics, so was considered to be the optimized condition. Both reinforcements were an improved on PLA alone. This suggests that plant waste can in fact be used for 3D printing to improve the properties and function of materials.
If this experiment at first might seem abstract and theoretical, in fact it could have implications for 3D printing in the future. The industry is constantly striving for two things: to optimize materials for better-performing products, and to improve sustainability. Using biodegradable plant materials to improve PLA for 3D printing could be the answer; particularly when the material is as accessible and inexpensive as pineapple fibers. This is not the first time that plant materials have been used for 3D printing. For example, Austrian company Extruder recently created a range of bio-responsible filaments named GreenTec and Biofusion, and Italian company WASP collaborated with Dior for a pop-up store using eco-friendly materials.
To read a write up of the report, you can click HERE. The full report is available on Polymer Composites, a scientific journal.
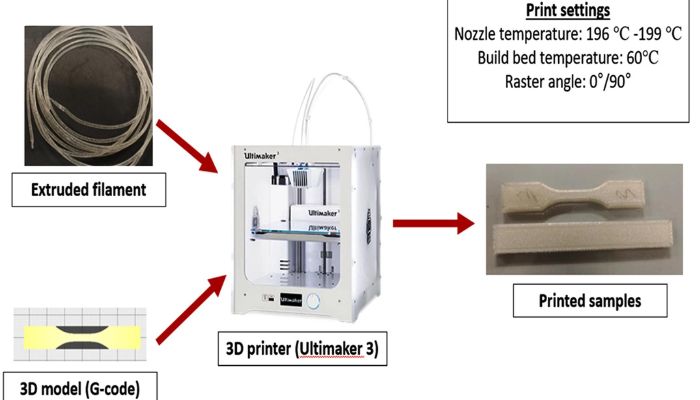
Experiment process to create the products. (Photo credits: Umar Abdul Hanan, Shukur Abu Hassan, Mat Uzir Wahit, Joseph Selvi Binoj, Bright Brailson Mansingh, Kheng Lim Goh, in Polymer Composites).
What do you think of this study? What do you think it could mean for the use of PLA in the future? Let us know in a comment below or on our LinkedIn, Facebook, and Twitter pages! Don’t forget to sign up for our free weekly Newsletter here, the latest 3D printing news straight to your inbox! You can also find all our videos on our YouTube channel.
*Cover photo credit: NextEvo/Sourcing Journal