All You Need to Know About PLA for 3D Printing
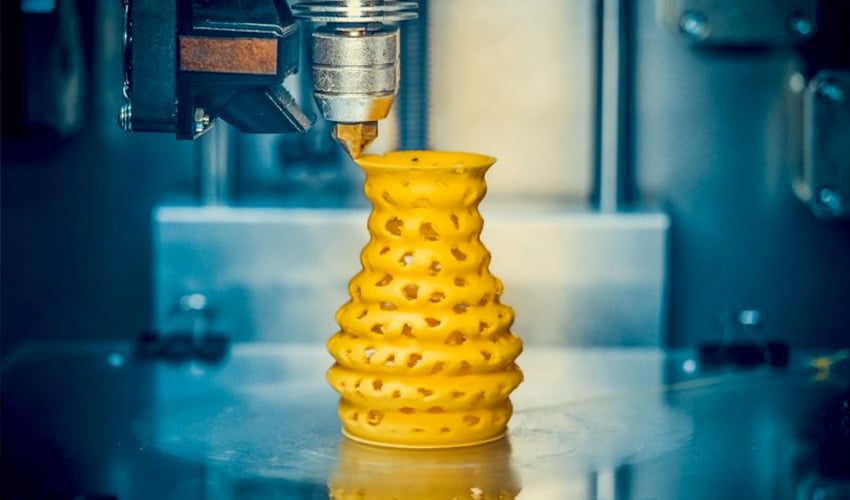
PLA (polylactic acid) is one of the most widely used plastics in the additive manufacturing sector. Invented in 1930 by chemist Wallace Carothers, also the developer of nylon and neoprene, this material can be used in filament or pellet form for desktop 3D printers or more industrial solutions. Unlike many other material options available on the market, PLA is often considered to be a more sustainable thermoplastic since it does not come from finite resources, as is the case with petroleum, but is sourced from natural and renewable resources. Due to its somewhat more eco-friendly origins, this material has been popular since its inception in the field of 3D printing. In fact, its use has spread to a wide variety of industries and applications. In this guide we will learn all about this material, including its characteristics, ease of printing, some applications as well as the main manufacturers in the market.
Production and Characteristics of PLA
As mentioned, PLA is made from organic and renewable resources such as corn starch, tapioca roots or sugar cane. Indeed, the production of the polymer is possible thanks to the fermentation of one of these carbohydrate sources. More specifically, the natural product is ground to separate the starch from the corn, mixing it with acid or lactic monomers. With this mixture the starch is broken into dextrose (D-glucose) or corn sugar. Finally, glucose fermentation produces L-lactic acid, the basic component of PLA. This results in an environmentally friendly and renewable material that, depending on temperature and humidity conditions, can become biodegradable.
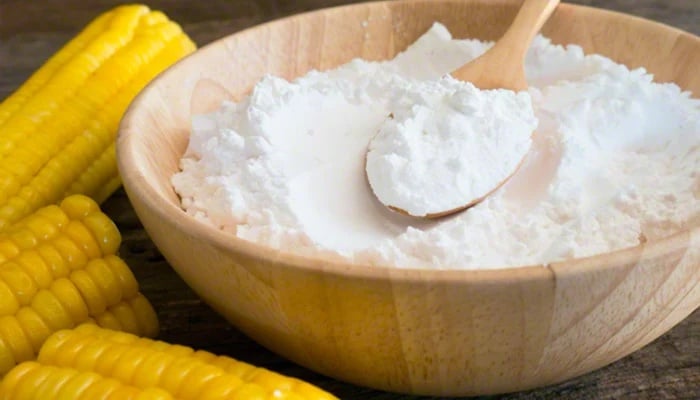
PLA is manufactured from renewable materials such as corn starch
Whether or not it can truly be considered biodegradable however has been at the center of great debate in recent years. With the sustainability of the material and its environmental impact being questioned. The truth is that answering the question PLA’s biodegradability is not as simple as it seems. Although the plastic is obtained from renewable resources, its ability to be decomposed by living organisms depends on decomposition under certain aerobic conditions. Thus, PLA can degrade rapidly when subjected to industrial composting processes. Otherwise, it can take up to 80 years to decompose in the open, becoming just another plastic pollutant.
An additional property of this material is that it is considered a non-Newtonian pseudoplastic fluid. This means that its viscosity (resistance to flow) will change depending on the stress to which it is subjected. Therefore, it does not have a defined and constant viscosity value, but varies according to the manufacturing conditions. More specifically, PLA is a thin shear material, which means that the viscosity decreases with applied stress. To learn more about it, let’s take a look below at its ease of use and its behavior when used as a 3D printing material.
PLA in 3D Printing
PLA is one of the most widely used materials in FFF 3D printing, especially by those who are just beginning in the 3D industry, as it is very easy to print with it. It can generally be found in filament form, but also in pellet or granule form. And although the material feed source and the melting system will change depending on the PLA format (through an extruder for filaments, or a hopper for pellets), the characteristics of the material and the final parts will not vary from one type to another. Still, in this article we will focus more on PLA in filament form, as this is the most common form in which this thermoplastic is usually found.
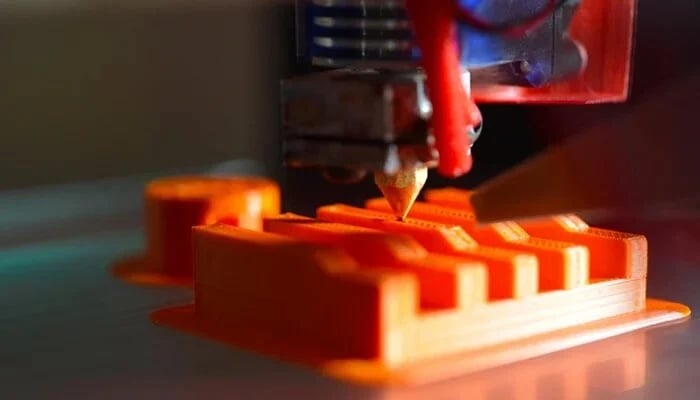
PLA is one of the most widely used thermoplastics in 3D printing (photo credits: BMI Lab)
PLA is considered a semi-crystalline polymer with a melting temperature of between 170-180°C, which is relatively low compared to ABS filament which melts at a temperature between 200 260°C. This avoids the need to use a heated tray and an enclosed printing chamber. At the same time, the filament offers good performance by combining high printing speed with fairly sharp edges, provided the material is properly cooled. Also, the resulting parts tend to have a very low deformability. That being said, it should be noted that PLA has a higher viscosity than other standard thermoplastics, which can lead to clogging if care is not taken. Additionally, the filaments have a shelf life of at least 1 year if stored at 15 to 25°C. If we compare PLA with ABS, another of the most commonly used thermoplastics in FDM 3D printing, we observe that, in general, the former does not have the same strength and flexibility as the latter though it is also less susceptible to warping. Even so, it is always recommended to use PLA in parts that do not have high mechanical complexity, as working with it is much simpler.
In terms of post-processing, PLA generally does not require complex steps. When removing parts, problems with the adhesion of the first print layer may be encountered. It is therefore recommended to use special adhesives on the printing plate to facilitate the removal of the parts. To improve the surface condition of the parts, the user can sand them and treat them with acetone if necessary. Supports, if used, can be easily removed with tweezers, or dissolved if soluble support structures have been used.
Applications of PLA in 3D Printing
As outlined above, PLA is a relatively accessible plastic that is easy to use in 3D printing, especially among makers. But that is not to say it only has advantages. Its properties result in fragile printed parts that are not very strong as well as sensitive to sunlight and high temperatures. This is why it is used primarily by beginners, especially for creating decorative elements, gadgets and toys.
However, PLA is not limited to the world of makers. Many industries also use this thermoplastic for prototyping, for example. This saves companies a lot of money, instead of going through the process of creating molds. Also, although it’s not the first option people turn to, industries such as automotive can also benefit from PLA filament. In this case, it can be useful for creating accessories for cars or even for certain elements of the dashboard.
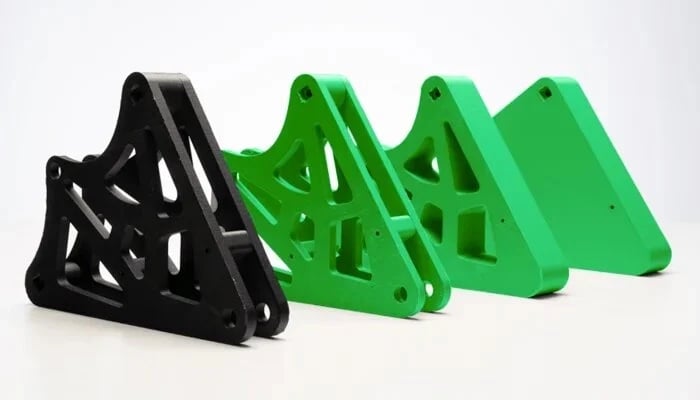
PLA is popular with makers as well as for rapid prototyping (photo credits: Markforged)
However, it is important to note that PLA has a low glass transition temperature, making it unsuitable for applications requiring higher temperature resistance. Industries such as the food industry should not use this thermoplastic to, for example, create cups containing hot liquids. Still it is food contact safe, which is why it is widely used in packaging.
Main Manufacturers and Price
As it is one of the most widely used thermoplastics in FDM/FFF printing, almost all material manufacturers offer PLA filaments or pellets in their product range. These include Polymaker, Recreus, Smart Materials or BASF through its Forward AM brand. It is also worth noting that FDM 3D printer manufacturers often offer their own filaments. There are many PLA manufacturers, such as UltiMaker, Stratasys, Prusa or Zortrax, among others.
As for the price of PLA filament, it can currently vary depending on the colors and characteristics sought. Hybrid filaments such as wood filament or fiber reinforced filaments increase the price considerably. Nevertheless, the price of a standard filament is generally between 20 and 70 euros per kilogram. Finally, as mentioned above, there are also 3D printers that can print from pellets, a form of material that is more affordable than filament, especially because it has not been processed.
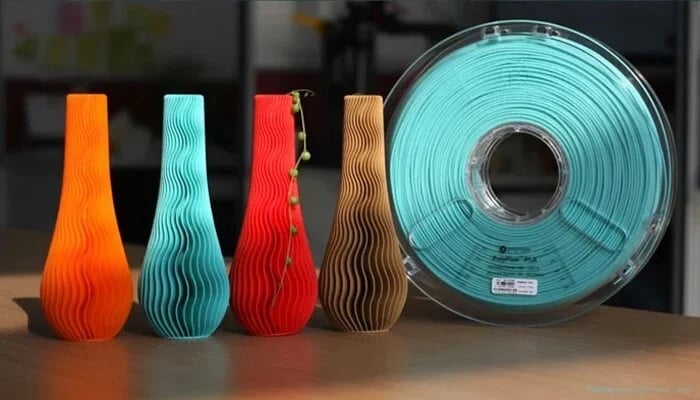
Photo Credits: Polymaker
Did you learn something about PLA for 3D printing?Let us know in a comment below or on our LinkedIn, Facebook, and Twitter pages! Don’t forget to sign up for our free weekly Newsletter here, the latest 3D printing news straight to your inbox! You can also find all our videos on our YouTube channel.