Phoenix, The New 3D Printed Concrete Bridge
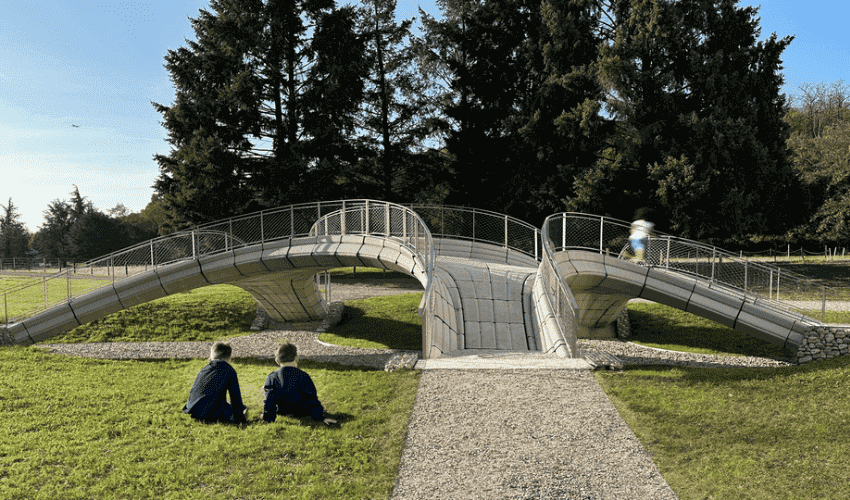
Additive manufacturing is transforming and revolutionizing construction methods, opening up new possibilities in terms of efficiency, customization and sustainability in a constantly evolving industry. Holcim, a company specializing in concrete 3D printing, has recently completed the construction of the “Phoenix” bridge. This 3D printed concrete bridge is the result of a fruitful collaboration with renowned partners such as the Block Research Group of ETH Zurich, the Computation and Design Group of Zaha Hadid Architects, and Incremental3D. This collaboration has played a crucial role in the search for sustainable infrastructure solutions for the Phoenix project.
The creation of the Phoenix Bridge benefited in part from the recycling of aggregates from the original Striatus blocks, the first of the reinforcement-free 3D printed concrete bridges to be unveiled at the Venice Architecture Biennale in 2021. Made from 10 tons of recycled materials, the bridge was molded using a mixture specially designed by Holcim, modifying its composition to reduce its carbon impact by 40%. This improvement translates into a 25% reduction in the structure’s total carbon footprint. Edelio Bermejo, head of research and development at Holcim, underlines the ecological importance of the project, stating that Phoenix “[is] demonstrating that essential infrastructure can be designed and built in a way that is circular and low-carbon today.”
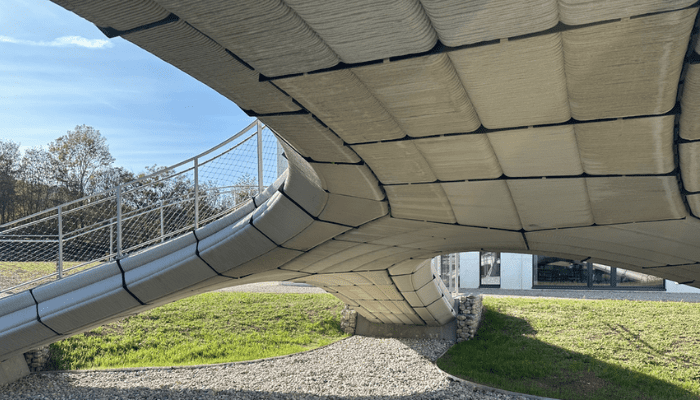
Circular construction methods, including 3D printing, can reduce the use of materials by 50%.
This bridge highlights the benefits of a more environmentally friendly infrastructure, characterized by the fact that Holcim has developed a special mix for the concrete of the Phoenix bridge using its circular ECOCycle® technology. The special concrete mixture incorporates recycled materials from building demolitions with fully recycled ECOPlanet cement. Thanks to circular construction, which combines computer-aided design and 3D printing, it is possible to reduce the use of materials by up to 50% without compromising performance.
Philippe Block, co-director of the Block Research Group at ETH Zurich, explains: “Concrete is an artificial stone, and like stone, it does not want to be a straight beam, it wants to be a masonry arch. Following these historical principles allows us to keep materials separated for easy recycling and to dry-assemble the structure for easy deconstruction and reuse. 3D concrete printing allows us to use material only and exactly where needed. The result is a sustainable and truly circular approach to concrete construction.” Johannes Megens, co-founder of incremental3D also notes, “Now, after two years and in its second iteration, Phoenix adds a largely reduced carbon footprint and permanence according to building codes along with many other further improvements.”
By using Holcim’s circular ECOCycle® technology, the company and its partners are now exploring opportunities to extend the impact of Phoenix into a wider deployment of sustainable infrastructure solutions. To learn more about the Phoenix bridge, you can visit Holcim’s website HERE.
What do you think about the Phoenix Bridge? Let us know in a comment below or on our LinkedIn, Facebook, and Twitter pages! Don’t forget to sign up for our free weekly Newsletter here, the latest 3D printing news straight to your inbox! You can also find all our videos on our YouTube channel.
*All photo credits: Block Research Group