Phillips on Their Hybrid AM Solution and Work with Meltio
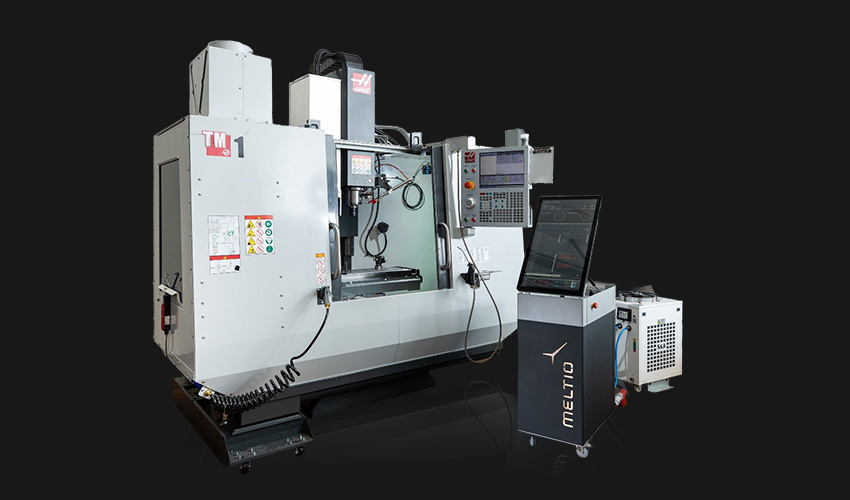
More and more, we are seeing industries adopting additive manufacturing. In these new sectors, one of the common ways to integrate AM technologies is through some kind of hybrid solution. In other words, a solution that has both subtractive (or traditional methods like CNC machining) and additive manufacturing components. The most recent company to adopt a hybrid approach is Philips, a leading solutions provider for manufacturing technology products and services to both commercial markets and federal governments. In particular, the new hybrid machine is a combination of Haas Automation’s subtractive CNC machine tool technology with an additive laser head from Meltio. We sat down with John Harrison, the Director of Additive Manufacturing for Phillips Corporation to learn more the machine and its applications, such as in those in the maritime sector, as well as about why they chose to move more into the additive manufacturing market and about their partnership with Meltio.
3DN: Can you introduce yourself and your connection to 3D printing?
I am John Harrison, Director of Additive Manufacturing for Phillips Corporation. Phillips has been in the 3D printing industry for 16 years. One of my first experiences with the technology was at Walter Reid Hospital, where doctors were helping soldiers with traumatic head injuries. The doctors would take 3D scans of the damaged area of a soldier’s head, then print a plate to be implanted to repair the skull.
As the technology has matured, new opportunities in production, human adaptation (knee implants, dental repair, hearing aids), and supply chain support have emerged. Our company is focused on getting additive technology and know-how in the hands of the innovators that will change the world.
3DN: Tell us a little bit more about the new hybrid AM solution? Why has Phillips decided to start using AM?
Phillips was brought into the hybrid AM space by our customers 8 years ago. As a partner with Haas Automation, a world leader in CNC manufacturing solutions, a customer asked us to integrate a wire arc additive head into a CNC mill. This was our first hybrid. Over the years, we have experimented with a few different technologies to integrate into a mill.
A few years back, we started discussions with the Department of Defense about an expeditionary hybrid solution. Shortly after, an OEM approached us, looking to integrate additive onto a Haas UMC-1000. These inquiries were the catalyst for the development of the Phillips Hybrid team.
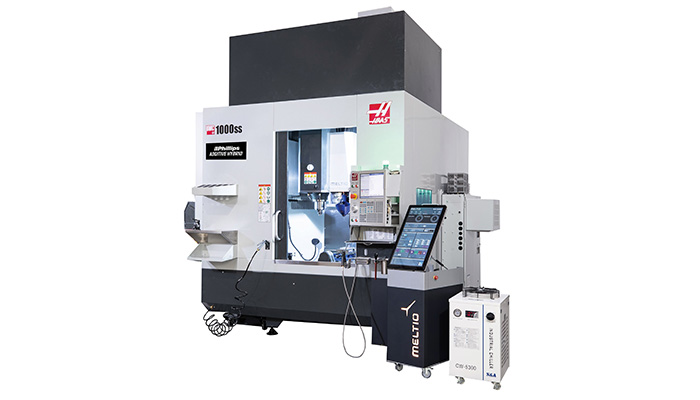
The new hybrid machine from Phillips and Meltio (photo credits: Phillips)
3DN: In order to create the solution, you have adopted Meltio’s direct energy deposition (DED) technology. What drew Phillips to Meltio and why DED over other AM technologies?
We had some experience with several technologies and experimented with wire arc, and powder blown solutions. We stumbled upon Meltio and think we have a good fit. Melito had developed the M450, a wire-fed DED solution using multiple lasers. The design used multiple, low-power lasers that made the solution affordable. The head was designed to introduce power from multiple sides, which allows the machine to produce additive layers in any direction. The use of lasers minimizes the heat added to the work area and the amount of Argon assist gas.
Meltio was already integrating their print engines on robotic arms, which gave us a head start in the development of the process to integrate the technology onto a Haas machine. We started on a 3-axis machine, the Haas TM-1, to demonstrate the capability for use in expeditionary environments. The word got out that we were working on this project, and an OEM asked us to build a hybrid unit based on the Haas UMC-1000.
The Meltio team has been supportive in the process and continues to improve on an already robust print engine. We are happy with the interest from our customers in the product.
3DN: What are the advantages of using both subtractive and additive manufacturing in one machine? Why not just one or the other?
The hybrid machine can be used for new parts and repair parts. The advantages in new parts are apparent in an expeditionary environment. If you do not have feedstock, you can “grow a part” and then use the cnc to finish it. Other new part applications include parts that are cast or would require a large amount of material removal.
If a component is damaged or worn, the hybrid offers a predictable repair. The worn area can be repeatably removed, the laser DED head can precisely add material into the void, then the cnc can re-finish to original tolerances. In addition to expeditionary repair, manufacturing lines and mold-making shops could benefit from the hybrid solution.
3DN: What are the applications for this solution? What industries, in particular, do you believe will benefit?
Whenever I think about the usage case for expeditionary, I think of the show on Discovery Channel called “Deadliest Catch.” It follows crab fishermen as they harvest seafood in the Bearing Sea. On most episodes, a boat experiences a breakdown of a vital component. They usually do not have a spare part and need to decide how to come up with a fix or face a return to port. The value of having the ability to create or repair a part at point of need is evident. Think about the needs of large Naval vessels at sea or a soldier supporting equipment in remote environments. The application is evident. Relative to manufacturing facilities, the repair of components that experience regular wear is emerging as a great application.
3DN: Any last words for our readers?
We are excited to be a part of bringing the Meltio technology to the Haas platform. We believe that the affordability and serviceability of the Phillips Hybrid will allow many shops to unlock the potential of this game changer. You can find out more on Phillips’ website HERE.
What do you think of Phillips’ use of AM? Let us know in a comment below or on our Facebook and Twitter pages. Don’t forget to sign up for our free weekly newsletter, with all the latest news in 3D printing delivered straight to your inbox!