Philipp Aduatz on Using 3D printing to Design Colorful Concrete Furniture
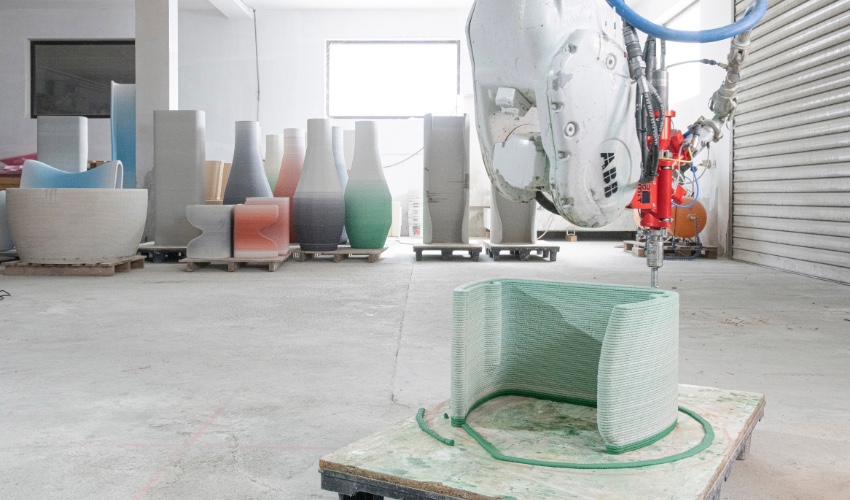
Design freedom is one of the most important strengths of additive manufacturing. This is why various 3D printing processes are also being used more and more frequently in the creative industry. They offer unprecedented possibilities in the design process, meaning that there are fewer and fewer limits to creativity. For example, there is already technology can be used to replicate natural forms (bionics) or to create experimental designs. For Austrian product designer Philipp Aduatz, 3D printing has become an integral part of his design work for years. His designs are a prime example of how to take advantage of additive manufacturing. From creating the first prototype to 3D printing limited edition furniture. Philipp Aduatz spoke with us about the application of additive manufacturing to his business and explains how the technology influences his design process.
3DN: Can you briefly introduce yourself and your work?
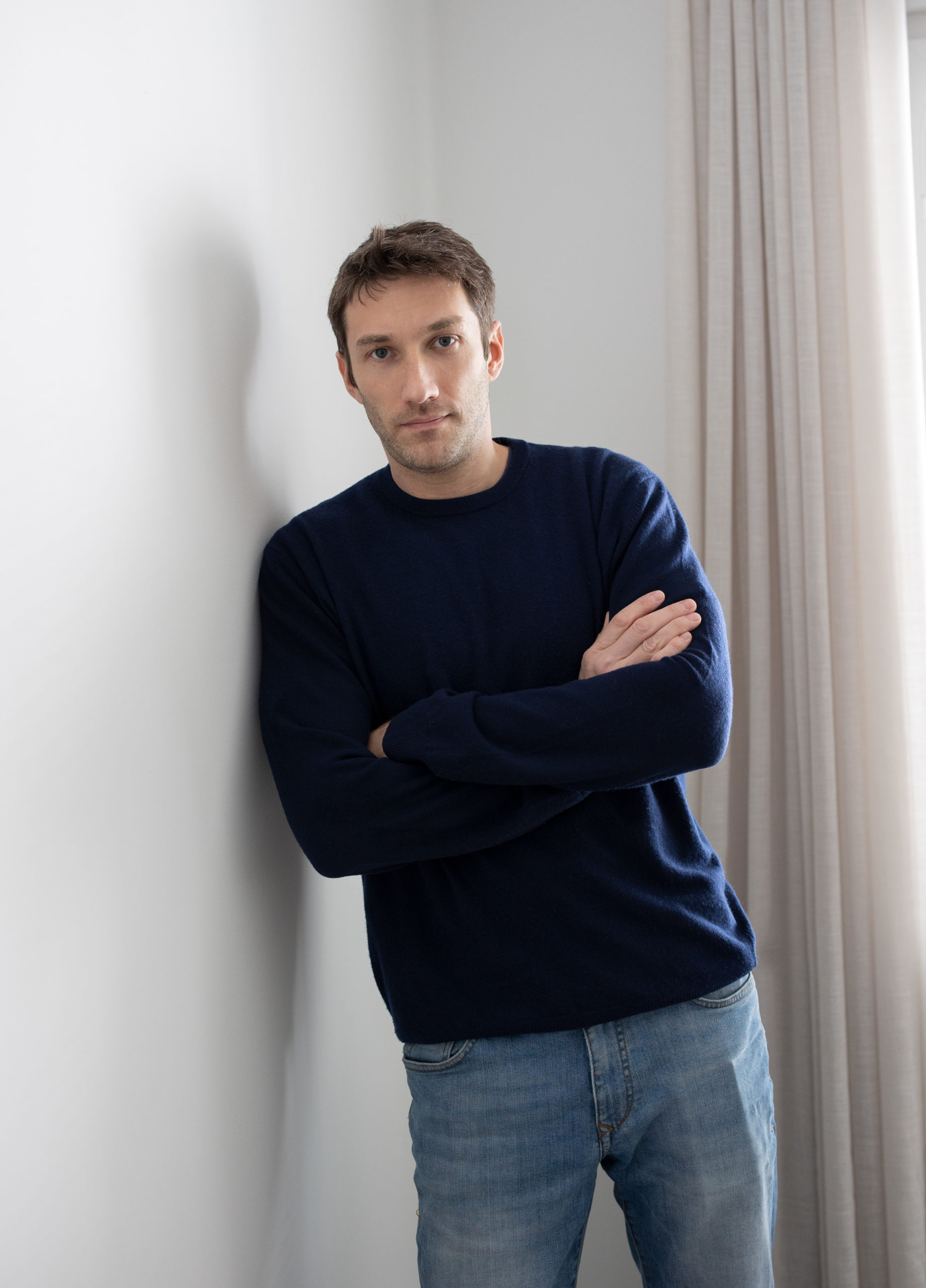
Philipp Aduatz
I am a product designer from Vienna and my work is at the interface of design and art, notably working with technology and material sciences. My process is characterized by both experimental and scientific theoretical features and the result are objects in small limited editions. 3D printing has always played a role in my work. Since 2005, I have used it primarily to quickly produce small working models in the design process. In recent years, however, it is mainly the possible dimensions in 3D printing that have changed and since 2018 I also produce large objects in 1:1 scale.
3DN: What are the advantages of additive manufacturing in the design and manufacturing process of your objects?
For me personally, there are several advantages. The most important one for me is that no complex mold construction is necessary for production. This is primarily an economic advantage. In the past, I always had to incur large financial expenses for the production of models and molds, but this is completely eliminated by using additive manufacturing. Furthermore, minor changes and optimizations can always be made during pilot production. Even in production, adjustments can still be made if necessary. In the past, this was not possible for me; once molds were produced, it was impossible to make any more changes here. And last but not least, new forms of design expression are also a significant advantage of 3D printing; the aesthetic dimension in particular is an interesting aspect for designers.
3DN: Just recently you presented a limited edition furniture series, additively manufactured from concrete. Can you tell us more about that?
Concrete 3D printing is a new and innovative manufacturing process, whereby large and complex structures in design can be printed very quickly. The company incremental3d is currently working on ways to colorize concrete in the 3D printing process as part of a research project. This involves injecting color pastes directly into the nozzle during the printing process, thereby reducing labor, waste and time delays. Thus, the color design can be selected not only globally, but locally point by point. The aim in developing the new series was to combine technology with color design in order to create innovative products in this way.
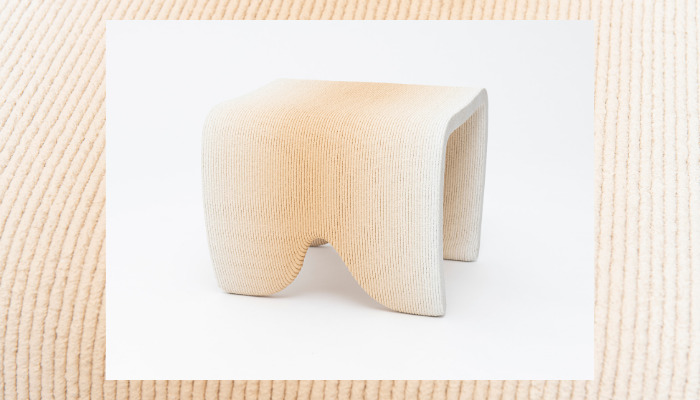
The “Gradient Stool” manufactured using 3D concrete printing. (Images: Philipp Aduatz)
3DN: Can you tell us more about the printers and materials you use?
I am working with the Austrian company incremental3d, which is a spin-off of the University of Innsbruck, on concrete 3D printing. We use a six-axis industrial robot which applies an innovative special cement-based mortar through a nozzle in web widths between 10 and 40 mm and web heights between 5 and 10 mm. An accelerator mixed in during the printing process ensures rapid setting, so that large geometries can be produced in a relatively short time. The high stability and rapid strength build-up enable the printing of 3-dimensional spatial structures (planar, single-curved or double-curved).
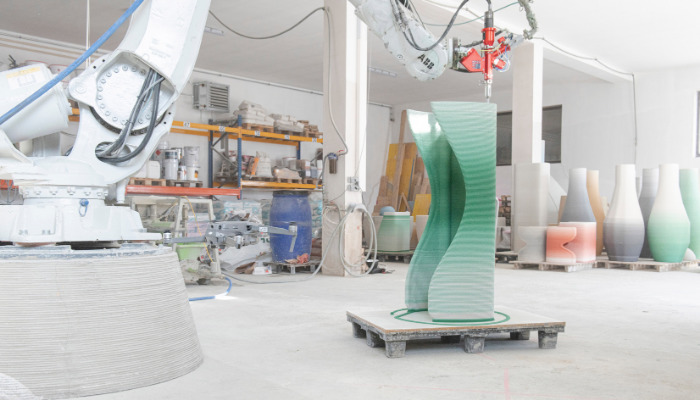
Layer by layer, the concrete objects of the “Gradient Furniture” series are created. (Image: Philipp Aduatz)
3DN: 3D printing is known for its design freedom benefits. To what extent does this influence the creation of new projects? Where do you see creative limits?
Enormous, of course; the freedoms are very great compared to conventional technologies. However, there are also limits. Concrete 3D printing works in a similar way to the already very well-known FFF process with plastic, although no support structures are possible here. Overhangs can thus only be designed to a certain extent; you are always working against gravity. When developing the objects, we always try to go as far as possible to the limits in order to be able to exploit the creative scope to the maximum.
3DN: Do you have any last words for our readers?
By the way, all my new furniture is available for purchase, I offer different colors and on request also custom-made. If you are interested, please contact me at ph*****@***********tz.com
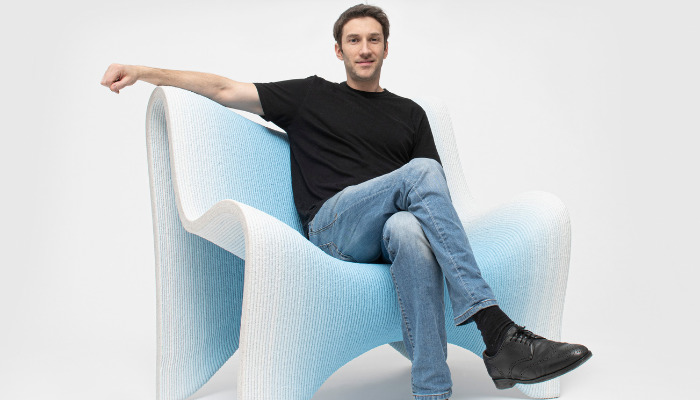
Designer Philipp Aduatz with the Gradient fauteuil. (Photo Credits: Philipp Aduatz)
What do you think of Philipp Aduatz’s Gradient Furniture Collection? Let us know in a comment below or on our Facebook, Twitter and LinkedIn pages! Sign up for our free weekly Newsletter here, the latest 3D printing news straight to your inbox!