All You Need to Know About PEEK for 3D printing
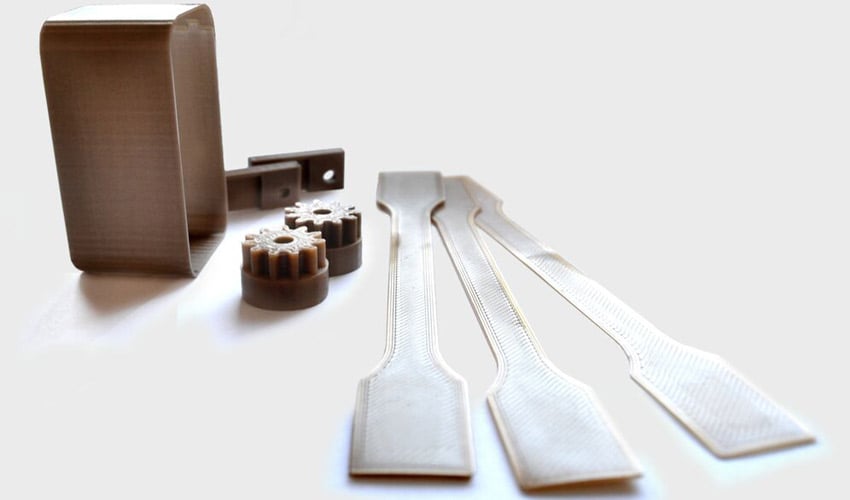
Polyether ether ketone, more commonly known as PEEK, is a semi-crystalline thermoplastic that is well known in the manufacturing industry for its mechanical properties. And for some years now, it has been a popular material in the additive manufacturing sector. Today, it is available in filament form for all FDM/FFF machines, and is slowly becoming available in powder form for SLS processes. Mainly used in the aerospace, medical and automotive industries, PEEK is heat and wear resistant and can even be used as a substitute to some metals due to its strength-to-weight ratio. However, it is also important to note that it is a demanding 3D printing material as it is difficult to print and can only be done so successfully if a number of parameters are met. So what exactly do you need to know about PEEK for 3D printing? We took a closer look in this guide!
Production and Characteristics of PEEK
PEEK is a member of the PAEK (polyaryletherketone) family, which is known for its high thermomechanical properties. If we look at the pyramid of different polymers in the industry, PEEK is at the top of the pyramid, in the category of high-performance polymers. Its molecular structure is composed of a ketone and two ethers, organic compounds of the carbonyl family, with a double bond between a carbon and an oxygen atom. It was first marketed at the end of the 1970s, and quickly adopted by sectors such as aeronautics or electronics because of the performance it can offer. If we look at its structure, note that it is a semi-crystalline polymer, therefore when it melts, its molecules arrange themselves under the effect of heat, creating a certain order until the material solidifies completely. This enables it to maintain its mechanical characteristics when the temperature is increased. While this semi-crystalline structure has many advantages, it should be noted that in additive manufacturing, it involves a more complex printing process: it is a highly technical material that requires experience and the appropriate system.
3D Printing With PEEK
In 3D printing, the crystallization process of PEEK must be controlled as part of the material will crystallize, thus changing the density of the material. Therefore, high temperature levels – extrusion, build plate and chamber – must be maintained and fluctuations in temperature need to be avoided. To print 3D print PEEK, you will therefore need a 3D printer with an extruder that can reach 400°C, a chamber that can be heated to 120°C, and a build plate that can heat to 230°C to ensure proper part release at the ending and prevent warping. In terms of chemical reaction, the material changes density during printing, then contracts as it cools.
Though PEEK is a demanding material, it must also be said that it offers very interesting mechanical and chemical characteristics for different industries. In fact, it is very resistant to heat and wear, has a high chemical resistance, it’s sterilizable and has dielectric properties. PEEK also has a high strength-to-weight ratio and is often used to replace certain metals. Finally, PEEK is flame resistant which makes it an interesting 3D printing material for sectors such as aerospace that have high fire/smoke constraints. If we were to compare it with other high-performance thermoplastics, PEEK outstrips ULTEM in mechanical strength.
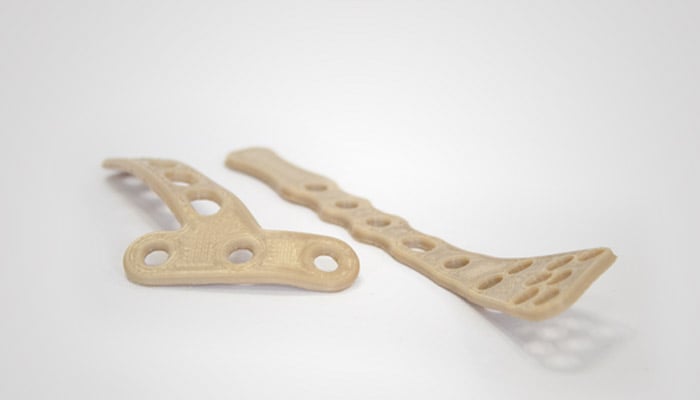
Photo Credits: Apium
Applications
This high-performance material is particularly interesting for the medical sector. Since it’s sterilizable and biocompatible, it can be used for a number of applications including the manufacture of custom-made implants. In fact, PEEK has properties similar to human bone: an implant 3D printed with PEEK could therefore promote the reconstruction of tissues around the implant, accelerating osseointegration. As such, a number of companies have turned to 3D printing of PEEK to design customized medical devices such as FossiLabs.
Aerospace and automotive are also markets where PEEK 3D printing is common. Additive manufacturing allows for the creation of high-performance, lightweight, custom and on-demand parts: coupled with the use of a high-performance material, it is even more attractive. PEEK will offer greater wear and temperature resistance, while optimizing weight – a key factor in such areas. It is so capable in fact that parts from PEEK have already been sent to space, further proof that this material can meet the needs of even the most demanding sectors.
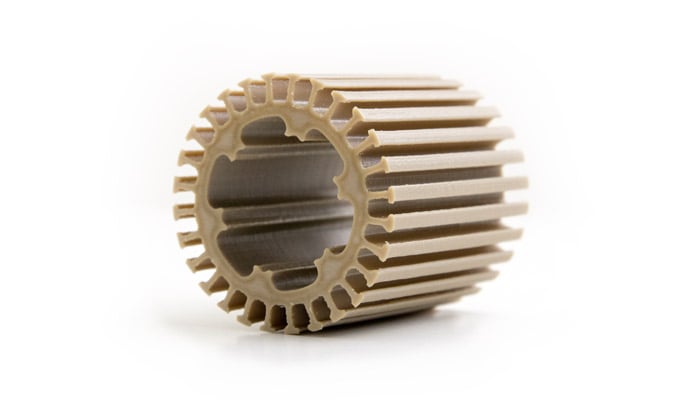
Photo Credits: Apium
The Main Manufacturers and Price
Currently, the majority of PEEK in 3D printing is available in filament form and therefore compatible with FFF 3D printers. Carbon fiber filled PEEK is also available on the market. Chemical companies such as Victrex, Solvay and Evonik are the main producers of the material. On the filament side, most machine manufacturers today produce their spools such as Intamsys or Apium. The Spanish company Innovatefil, a subsidiary of Smart Materials 3D, also offers it. If we now look at the price, PEEK is a very expensive material: count between €350 and 700 for 1 kg. By comparison, PEKK, another high-performance thermoplastic, costs between €400 and €500 per kg. Finally, for SLS processes, EOS was the first – and only – manufacturer to offer PEEK HP3, a material for powder sintering. However, the Belgian company Aerosint is working on the design of an SLS machine capable of combining several materials. PEEK could be one of them.
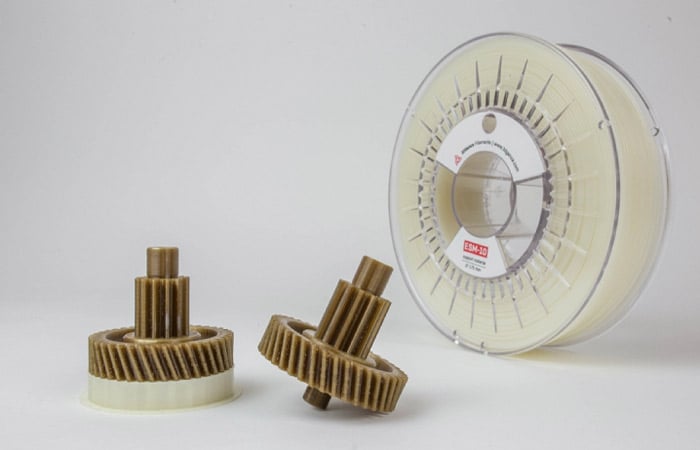
It is most widely available in filament form (photo credits: 3DGence)
*Cover Image Credits: Indmatec
Do you have any more questions about PEEK? Let us know in a comment below or on our Facebook and Twitter pages! Don’t forget to sign up for our free weekly Newsletter, with all the latest news in 3D printing delivered straight to your inbox!
If you like to learn more about Evonik’s VESTAKEEP® filaments for medical applications – the world’s first PEEK filament in implant-grade quality for 3D printing – please visit our website:
https://3d-printing.evonik.com/product/additive-manufacturing/en/materials/biomaterials-medical-applications/peek-filaments/
3D4MAKERS produces a wide range of PEEK filaments. For the L&V types no heated chamber is required. Materials are specially engineered for 3D Printing
I would like to receive more PEEK medical-implant-standard filaments material informations.
I intend to mix peek with UHMWPE to design a dumbbell shape, but I don’t know how to regulate the temperature of PEEK so that I can be able to mix appropriately and print both at a temperature that is less than 400.
please Advice